Carbon steel and alloy steel are the main components of some of the materials found in different industries. Usually, these are seen in automotive components, mining, construction, aerospace, and many others.
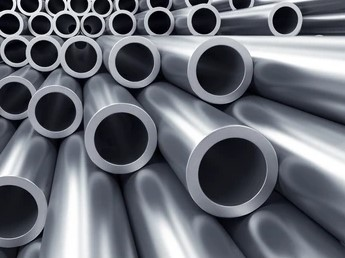
An alloy steel has better strength. However, both metals provide their own benefit for a specific material and industry. Identifying which one is suited for your project will make the metal castings function to their intended purpose.
Carbon Steels and Alloy Steels: Identifications
The high percentage of iron and carbon makes it a popular type of steel used for various applications due to its desirable properties.
On the other hand, alloy steel has common elements. Depending on the use of the metal parts, it may include chromium, cobalt, nickel, molybdenum, and tungsten. These are manufactured by combining two or more base metals, such as iron and carbon, along with other elements. High carbon steels are used in applications with higher requirements.
Such elements are added to create a material with the desired set of properties. The exact combination of the elements will depend on the intended application and the desired physical characteristics.
Features Found on a Carbon Metal
Carbon steel is incredibly strong and durable, making it suitable for many applications that require strength and durability. It is also very hard, making it less likely to deform or break under pressure.
Another property of carbon steel is its hardness. Using it on applications that require machining and designing is not recommended. Its resistance to deterioration makes it a great choice for parts that need to be durable and long-lasting.
Carbon steel also has excellent resistance to corrosion. Its resistant properties make it a great choice for parts that need to be resistant to corrosion. It is also non-magnetic and will not rust easily, making it perfect for parts that need to be kept dry.
0.05% to 0.25% Carbon
Low carbon steel is also known for being economical and easy to work with because of its ductility. It is not as strong as normal steel, but it is still capable of providing good strength and durability.
This type of carbon steel can be easily cut, bent, and welded into the desired shape and size. It is also relatively easy to machine and is often used for making custom pieces.
0.3 to 0.6% Carbon
Medium carbon steel is a popular choice among metalworkers due to its strength and malleability. Its carbon content provides good wear resistance.
The process of making this type of carbon steel begins with selecting a type of iron ore. The iron ore is then melted at a high temperature and mixed with carbon. Other elements can be added to the mixture, depending on the desired property outcome.
1.5% and more Carbon
Its higher carbon content makes it more difficult to work with, as it is more prone to cracking and chipping when machined. Outputs that have excellent strength and durability are usually made from high carbon steels. Its versatility makes it a great choice for many industrial and consumer applications. Very high carbon steel is used for special purposes for industrial works.
Advantages of Using Carbon Steel
Carbon steel is recyclable, so it can be reused and repurposed. It is also easy to modify, making it a great choice for custom projects–from structural supports to auto parts. However, it has low melting points, making it unsuitable for welding.
In addition to that, It is also relatively easy to work with, which helps keep costs down. Its strength, durability, cost-effectiveness, and versatility make it an ideal material for industrial and commercial use.
Properties of Alloy Steel
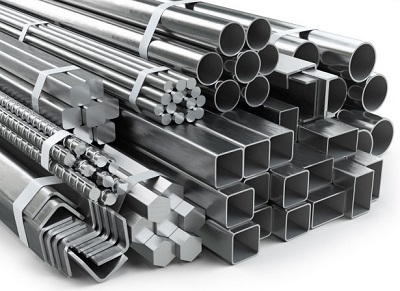
Alloy steels offer a wide range of properties that make them ideal for a variety of applications. With their increased hardness, excellent ductility and toughness, and better resistance to corrosion. Alloy steels are a great choice for any engineering project.
By adding elements such as carbon, chromium, and manganese to the steel, the hardness of the steel can be increased significantly. This allows the steel to be used in applications that require a material with high wear resistance and strength. Alloy steels have an excellent level of strength. Applications that have heavy loads are tolerable without breaking or deforming.
The steel can be formed into a variety of shapes without cracking or breaking. This makes them useful in applications where material needs to be able to absorb shock and vibration without breaking. Adding other elements may also increase corrosion resistance.
Low Alloy Steel
With a small percentage of alloying elements, it features good formability because of its high melting points. These properties make them easily welded, machined, and shaped into complex structures.
These are used to manufacture parts and components that need to be resistant to high temperatures, pressure, and corrosive environments. Low alloy steels are incredibly versatile materials, and their uses are virtually limitless.
High Alloy Steel
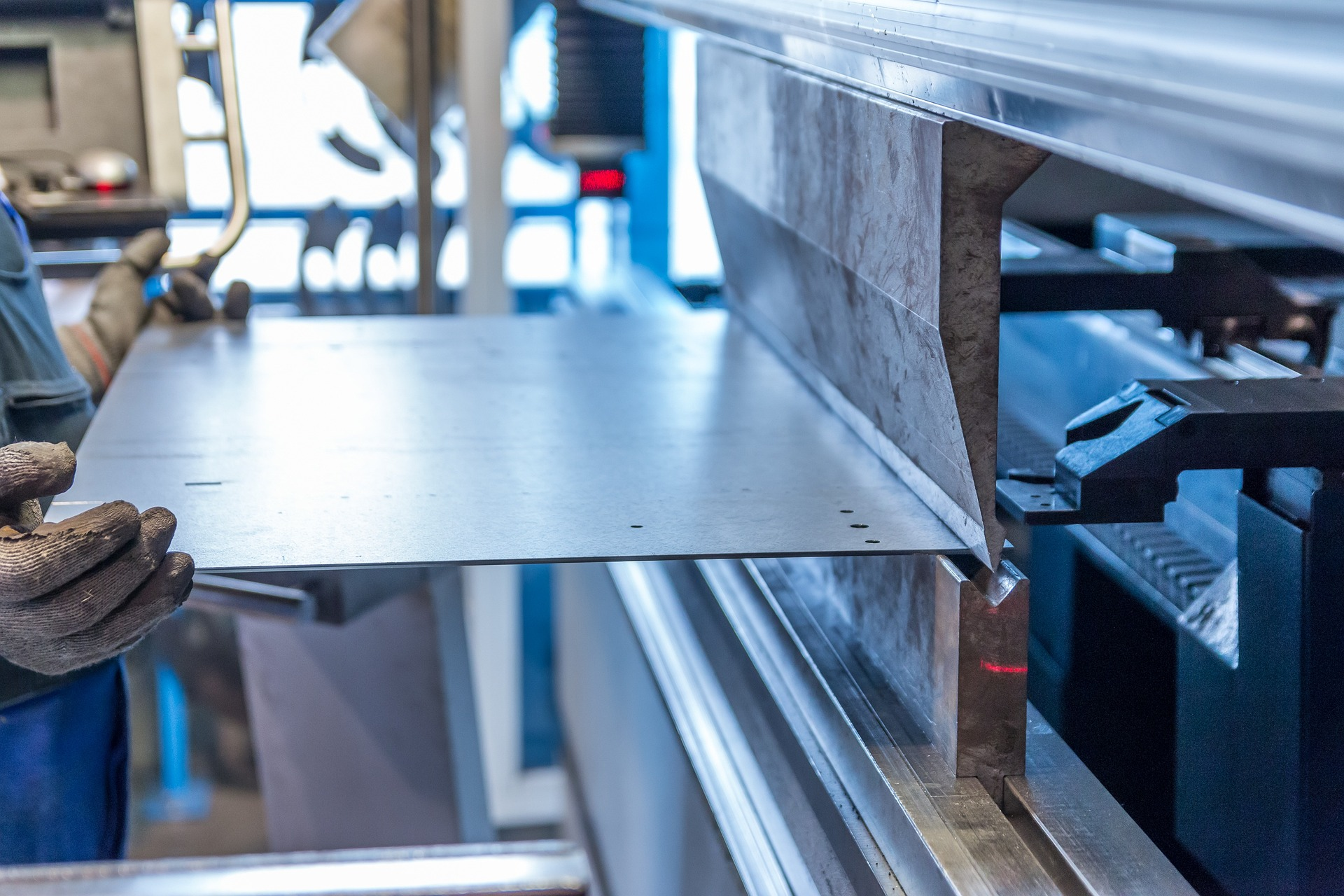
High alloy steels offer many advantages over other materials.
They are often used in the production of stainless steel products in order to protect them from corrosion. They are also often used in the production of pipes and other components that are exposed to corrosive environments, such as in seawater or in the presence of chemicals.
It is also used in manufacturing austenitic stainless steel used in food processing.
Advantages of Using Alloy Steel
High alloy steels are also much more malleable than standard steels. This makes them ideal for components that require intricate designs.
In addition, these steels are often more resistant to fatigue, which can be beneficial for high-stress applications where components need to be replaced less often.
Comparison of Alloy Steel vs Carbon Steel
Strength
The alloying elements give alloy steel greater strength and toughness than plain carbon steel, with around 80,000 psi.
On the other hand, carbon steel is much less strong than alloy steel, with a tensile strength of only around 44,000 psi.
In this case, the alloy steel features better strength.
Anti-Corrosive Property
Alloy steel contains more elements. Its contents are adjusted depending on the intended output. This makes the alloy steel less corrosive.
Carbon steel produces rust over time. When carbon steel is exposed to moisture or acids, it may have a chemical reaction that creates rusts.
Temperature Requirements
Both metals can undergo heat treatment. This process is done to improve the metal’s properties.
For example, quenching to a very low temperature is often used to improve the strength and hardness of the steel.
Carbon steel typically requires fewer heat treatments. Quenching and tempering are also used for carbon steel, but it may not be necessary to perform multiple treatments. In some cases, annealing or normalizing may be adequate. The steel is slowly cooled under room temperature air.
Where These Metals are Used
It includes vehicle frames, axles, shafts, and bolts. It is also often used in structural components and civil works. Structural components such as support beams, columns, and frames often use alloy steel due to its ability to handle high loads.
Mining equipment such as buckets, loaders, and excavators also use alloy steel for its wear resistance and strength. This steel is ideal for applications that require high strength, toughness, and wear resistance.
Aircraft engine components and landing gear components use alloy steel as well due to its strength-to-weight ratio. Other common applications for alloy steel in the aerospace industry include airframes, wings, fuselages, and tail sections.
High carbon steel is often used in knives, tools, masonry nails, and swords due to its ability to maintain a sharp edge. This is because the high carbon content allows it to be heat-treated and hardened and still remain flexible.
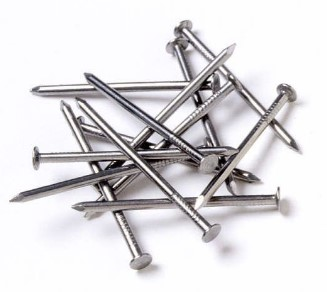
Low carbon steel is a popular choice for medical instruments and other equipment. It is used to make medical implants such as hip and knee replacements. It is also one of the best metals to use in cook wear.
The oil and gas industry is another major user of carbon steel. Carbon steel is used to make pipelines, tanks, and other components used in the production of fuel. Carbon steel is also used in the production of valves, flanges, and other parts used in oil and gas production.