As its name suggests, grey cast iron is a form of cast iron that has a distinct gray color when it is in its raw form. This is created through a process of filling the molds with molten iron and solidifying them through rapid cooling.
Grey iron is one of the most widely used alloys with intermediate carbon content, making it both strong and malleable. It is also known as gray iron or flake graphite iron and may contain pig iron.
How Gray Iron Castings are Made
Gray iron is a type of cast iron that is created by adding graphite to the molten iron during casting production. It is one of the most commonly used metals in the manufacturing industry, due to its high strength and low cost. The process of creating iron castings is relatively simple but requires careful attention to detail to ensure high-quality results.
The first step of creating grey cast irons is to melt down the raw iron. The molten iron is then poured into the appropriate casting molds. A small amount of graphite is then added and mixed into the molten iron and creating spheroidal graphite.
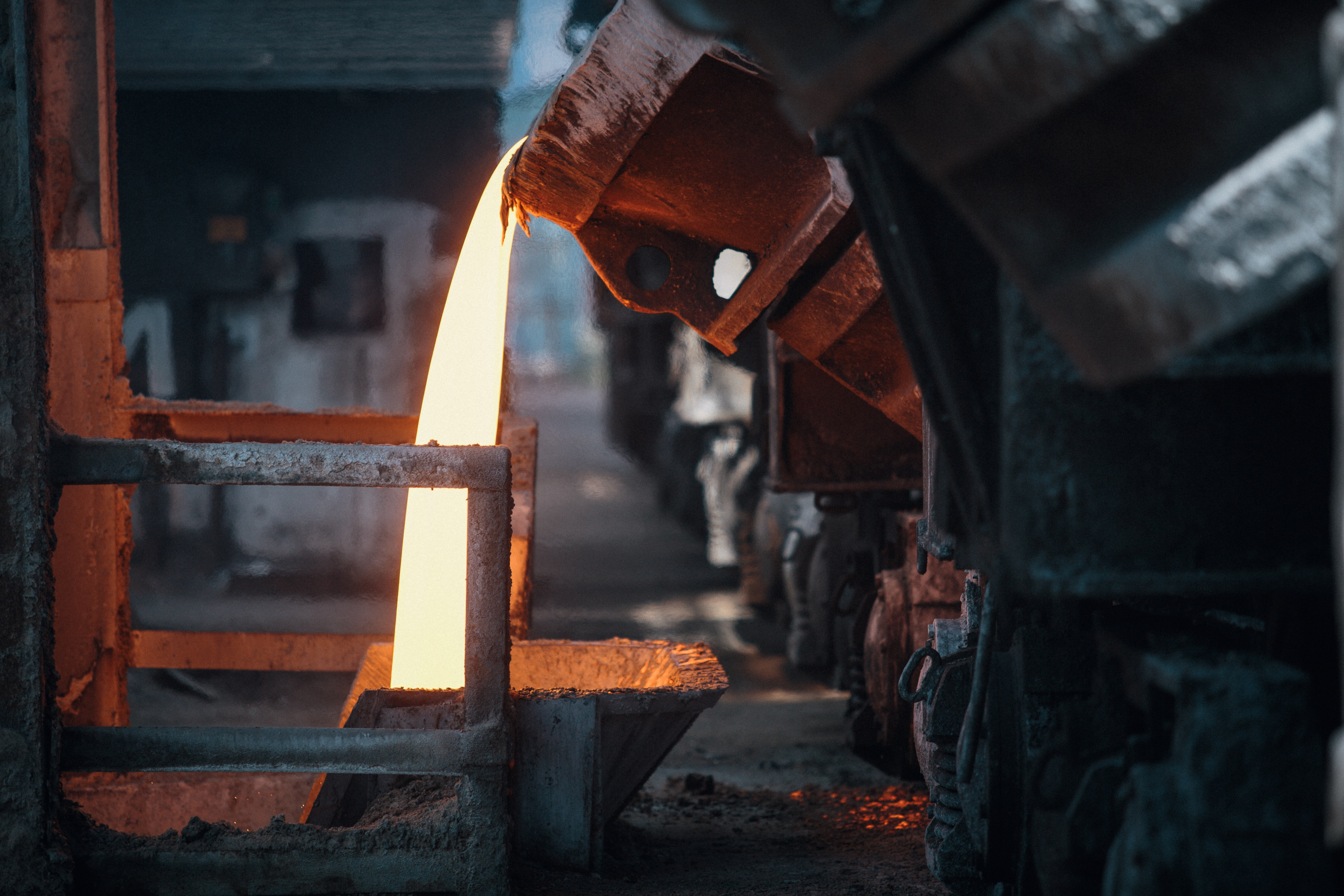
Once the graphite has been added, the molten iron and graphite mixture is poured into the casting molds. After cooling, the cast iron parts are then removed from the molds.
The cast iron parts can then be machined and finished as needed, depending on the specific application. Its excellent properties are used to shape and refine the parts, as well as to create any holes or threads that may be needed. The finishing process is used to create a smooth surface and to protect cast iron from corrosion.
Gray Iron and Other Cast Irons
White iron is a type of iron alloy that is created by adding silicon to the molten metal. This results in much harder iron alloys that are capable of withstanding higher temperatures.
It is commonly used in applications involving high wear, such as the production of machine parts.
White iron is the hardest form of cast iron and has a very low melting point. It is often used in the production of cutting tools, such as blades and dies, due to its high wear resistance.
Ductile iron is stronger and more resilient than gray iron and is often used in the production of brake drums, engine blocks, pump bodies, cylinder heads, and cylinder liners. It is also often used for piston rings, gears, bearings, and other automotive components.
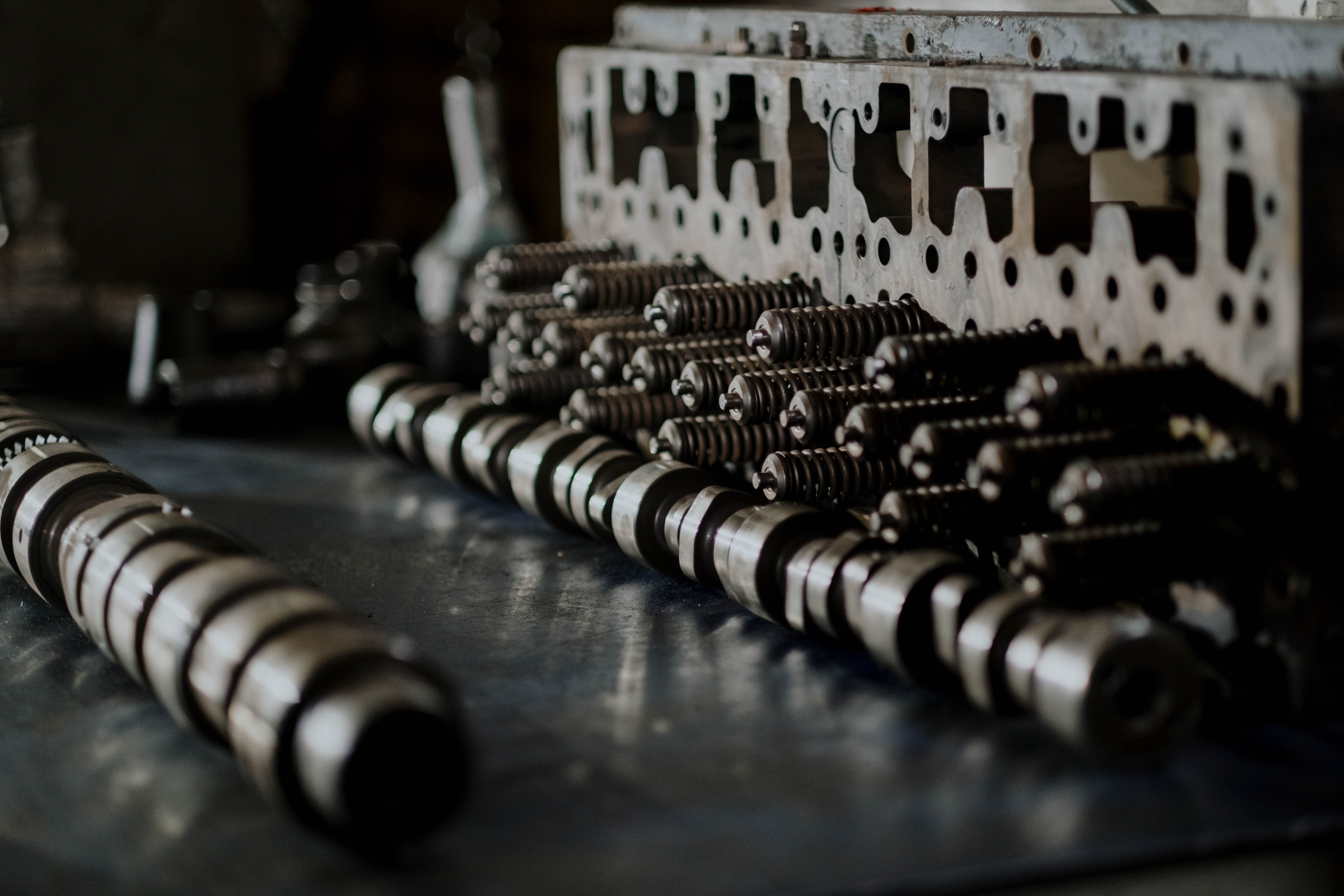
Malleable iron is softer and more ductile. It is used for applications that require high levels of flexibility. It is often used for the production of springs and other automotive components.
High-grade iron is the highest class of cast iron and is often used for applications that require the highest levels of strength and hardness. It is often used in the production of tools, dies, and other components that require extreme durability.
Gray iron has a relatively low melting point and is composed of a combination of carbon and silicon, which gives it superior strength and wear resistance. In addition, it also has a relatively high thermal conductivity.
High Compressive Strength of Gray Cast Iron
This strong material is made up primarily of a mixture of iron and carbon, as well as other elements. It is well known for its ability to handle high amounts of pressure without cracking or breaking.
Tensile Strength
The minimum tensile strength of gray cast iron is typically around 20-25 thousand pounds per square inch (KSI), according to ASTM standards. This is a measure of the material’s ability to resist being pulled apart.
This is because carbon forms a network of carbides throughout the iron, which increases the strength of the metal. Silicon also plays a role, as it helps to form a network of graphite flakes in the metal, which helps to absorb shock and increases the strength of the metal.
In general, a slower cooling rate will result in higher tensile strength. This is because slow cooling allows for the formation of larger graphite networks, increasing the strength of the metal. The higher the carbon content of the grey iron, the higher the tensile strength.
Yield Strength
Knowing the yield strength of a material is important for determining the right material for an application and calculating the necessary dimensions for the component.
Gray cast iron is a type of ferrous alloy composed mostly of iron, carbon, and silicon along with small amounts of manganese and sulfur. It is produced by adding specific amounts of these elements to molten iron, which is then poured into molds and allowed to cool.
Grey cast iron is known for its high strength, but also for being a brittle material. It can crack or shatter under excessive stress.
Hardness
The hardness of gray cast iron is measured using the Brinell hardness test. The test measures the amount of force required to indent a sample of the material with a steel ball. The results are expressed in Brinell hardness numbers (BHN), which range from 10 (very soft) to 600 (very hard).
Its hardness makes it suitable for a variety of applications, ranging from engine blocks to camshafts. Its BHN of 150-250 makes it relatively soft compared to other metals, but much harder than most other cast iron materials.
Gray Iron Properties
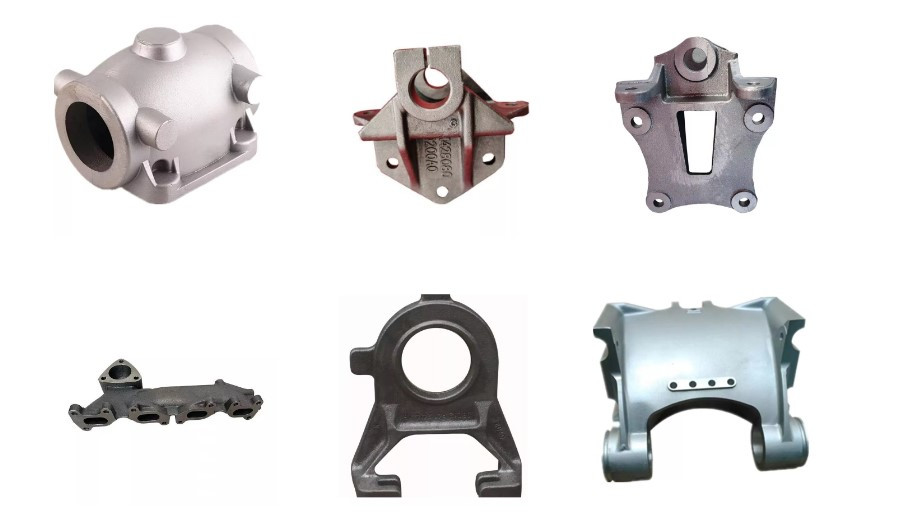
Ductility is its ability to undergo deformation in response to an applied force. It is an important material property that is widely used for many applications.
Gray cast iron has a relatively high ductility, which makes it suitable for components that require bending, shaping, and forming. Various grades of grey iron have different levels of mechanical properties.
The ductility of gray cast iron is due to its graphitic microstructure. Gray cast iron consists of a metal matrix of graphite flakes embedded in a solid ferrite matrix. The graphite structure acts as a stress absorber.
Impact Resistance
Gray cast iron is one of the most commonly used materials in a variety of industries, from machining to construction, due to its excellent durability and impact resistance. The graphite flakes in grey iron help to absorb shock and vibrations, which helps to protect the parts from damage.
The graphite acts give gray iron its superior strength and impact resistance.
Fatigue Strength
Fatigue strength is the maximum stress a cast iron can withstand before it fails due to fatigue. It is an important property for components that are subject to cyclic loadings, such as engine components, gearboxes, and bearings.
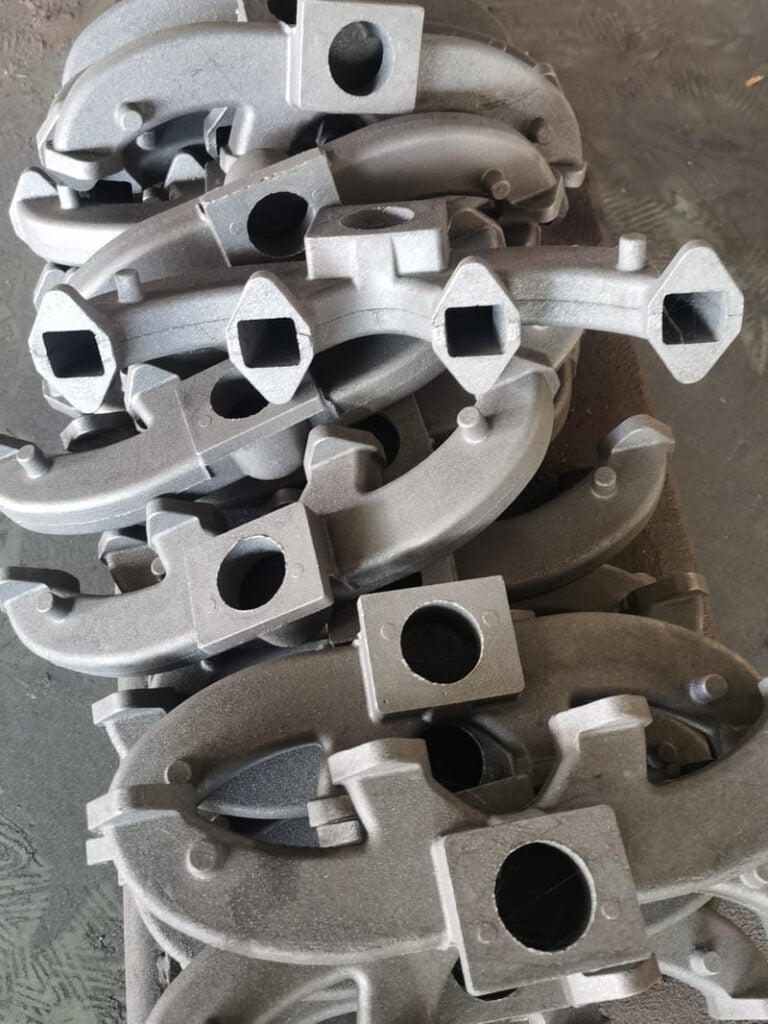
In order to ensure that components made from gray iron can withstand the cyclic stresses of their intended application. It is important to understand the fatigue strength of the metal castings.
Similarly, gray iron that has been cast using chill-casting, will usually have higher fatigue strength than gray cast iron that has been cast using a less advanced process, such as sand casting.
Malleability
One of the most notable characteristics of gray cast iron is its malleability. This property makes it ideal for forming intricate shapes and sizes without sacrificing strength or durability.
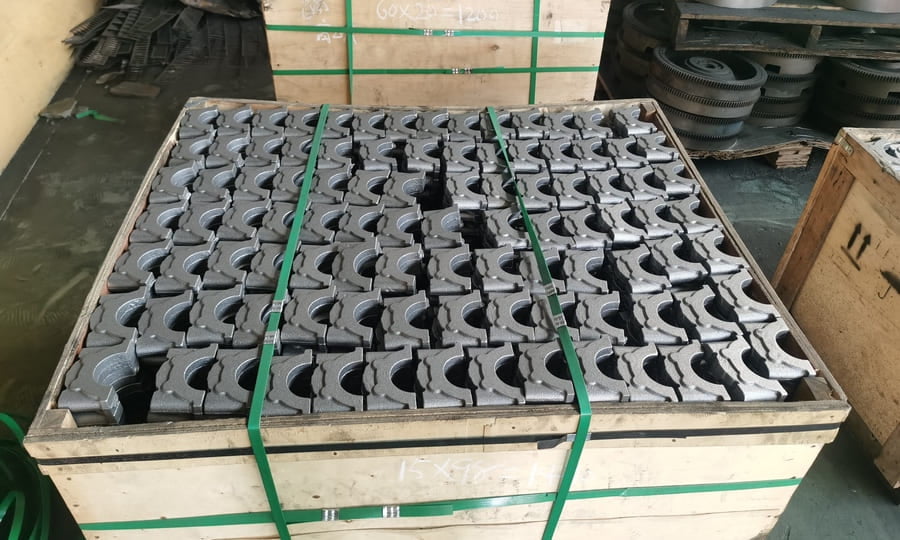
As such, gray cast iron is frequently used in the manufacture of parts that require precision and accuracy, such as engine blocks, automobile frames, brake drums, and machine components. Gray iron is easily machined and can be finished with a variety of surface treatments, such as painting, plating, and anodizing.
Excellent Machinability
The high graphite content in gray iron makes it easier to machine than other materials, as the graphite flakes act as lubricants to reduce the friction between the cutting tool and the castings.
This allows the cutting tool to move more easily through the material, resulting in a smoother finish and reduced tool wear. It also results in faster machining speeds, as the graphite helps to keep the castings cool while it is being cut.
Good Wear Resistance of Gray Iron Castings
Gray iron is well-known for its excellent wear resistance. This is due to its high carbon content, which helps to create a hard and wear-resistant surface. The metal also has a high hardness, and its wear resistance is further enhanced by the presence of graphite flakes, which act as lubricants and protect the metal from wear.
Abrasion Resistance
Abrasion resistance is the ability of castings to withstand mechanical wear due to contact with other castings. Gray cast iron has been used in a number of industries for many years due to its abrasion resistance.
Gray cast iron has a unique combination of properties that make it an ideal material for structure applications where abrasion resistance is important. It has a relatively low melting point and good casting properties, making it easy to cast into complex shapes. It also has a good balance of strength, hardness, and wear resistance, making it well-suited for applications where it will be exposed to wear and tear.
Corrosion Resistance
Grey cast iron has excellent resistance to most acids, alkalis, and salt solutions, and is highly resistant to oxidation and chemical attack. However, it is not as resistant to organic acids and alkalis and can be susceptible to pitting and crevice corrosion.
Gray Cast Iron is a type of cast iron that is highly resistant to corrosion, making it one of the most popular materials for industrial applications. The corrosion resistance of gray cast iron is due to its high carbon content and the formation of an oxide film on the surface of the material.
This oxide film acts like a barrier, preventing the corrosive materials from reaching the underlying metal and causing damage.