At KT-Foundry, we know that choosing the right material for your project is essential. That’s why we want to introduce you to the world of die cast aluminum alloys, a versatile material with a wide range of benefits and applications.
Die cast aluminum alloys are lightweight, strong, and durable, making them a popular choice across various industries. They’re also highly corrosion-resistant, able to withstand high temperatures, and offer excellent dimensional stability.
In this article, we’ll explore the composition and properties of die cast aluminum alloys, the die casting process for these alloys, their advantages and applications, different types of die cast aluminum alloys, surface treatment and finishing techniques, challenges and solutions in die casting aluminum alloys, manufacturing process and operations, benefits in the automotive industry, and future trends and innovations.
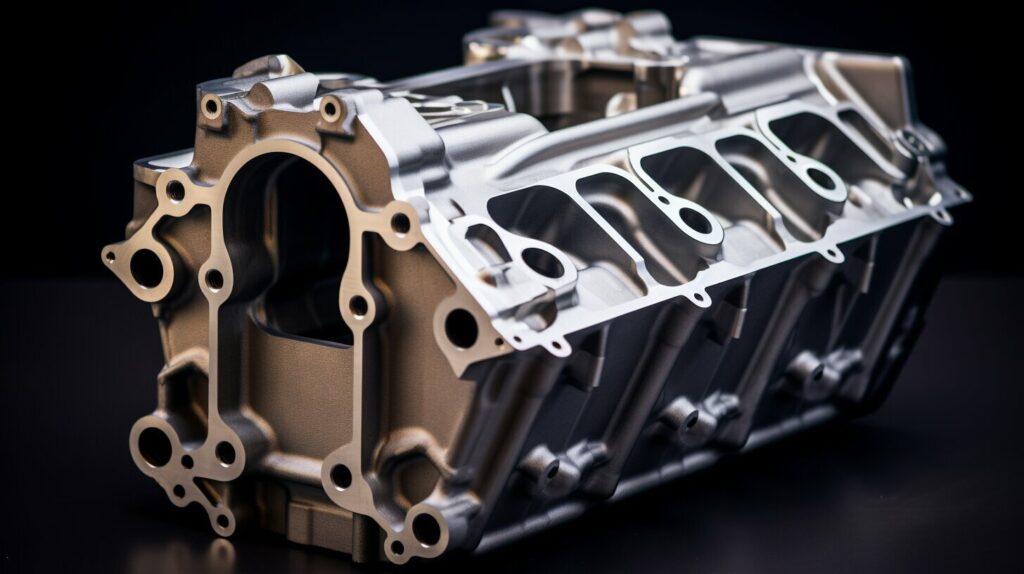
Key Takeaways:
- Die cast aluminum alloys are versatile materials with a wide range of benefits and applications.
- They are lightweight, strong, and durable, with high corrosion resistance, dimensional stability, and ability to withstand high temperatures.
- Die cast aluminum alloys are commonly used in various industries, including aerospace, automotive, and power tools.
- There are different types of die cast aluminum alloys, each with specific properties and applications.
- Surface treatment and finishing techniques enhance the corrosion resistance and overall quality of die cast aluminum alloys.
- The die casting process for aluminum alloys presents challenges such as casting defects and high-temperature requirements, but there are solutions to overcome them.
- Die cast aluminum alloys provide many benefits in the automotive industry, such as pressure tightness, lightweight construction, and high-quality engine blocks.
- The future of die cast aluminum alloys includes emerging technologies and innovations that may impact the industry in the coming years.
What are Die Cast Aluminum Alloys?
As we delve deeper into the world of die cast aluminum alloys, it’s important to first understand what exactly they are. In simple terms, die cast aluminum alloys are a type of aluminum alloy that is created through the die casting process, which involves injecting liquid metal into a mold cavity under high pressure. This results in a high-precision, accurate casting that can be used for a variety of applications.
Die cast aluminum alloys are different from other types of alloys in several ways. For example, they tend to have a higher level of fluidity, which allows for more intricate casting designs. They also have excellent corrosion resistance and can withstand high temperatures, making them ideal for use in various industries.
The composition of die cast aluminum alloys can vary depending on the specific application, but they typically contain a combination of aluminum, copper, zinc, and other metals. The properties of die cast aluminum alloys are also influenced by the manufacturing process, such as the temperature and pressure used during casting.
Overall, die cast aluminum alloys are a versatile and high-quality option for many applications. In the following sections, we will explore the benefits, applications, and manufacturing processes of these alloys in greater detail.
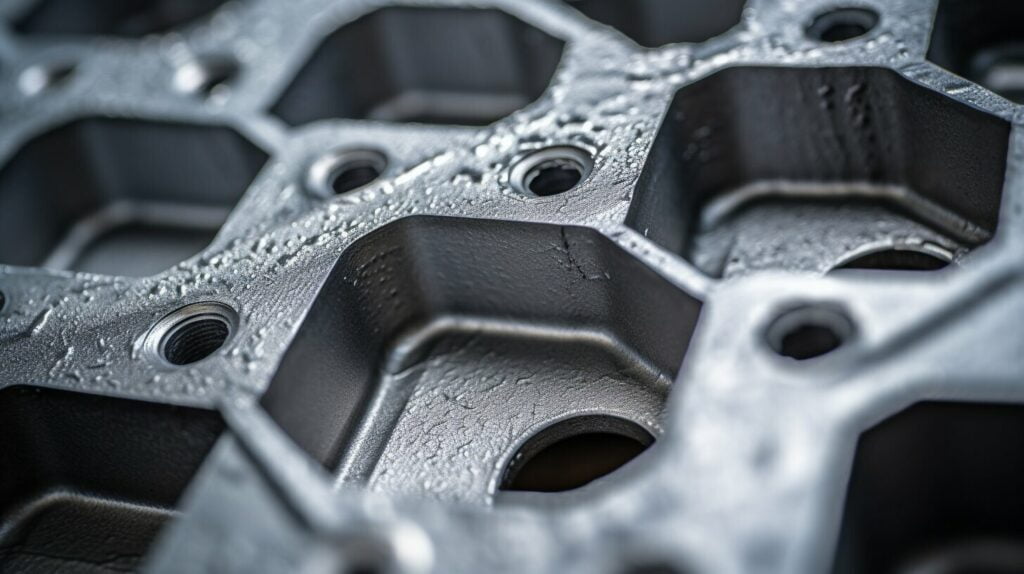
The Die Casting Process for Aluminum Alloys
At the heart of creating die cast aluminum alloys is the process of die casting. Die casting injects molten metal, or alloy, into a reusable steel mold, or die, to create complex shapes with precision and accuracy.
The die casting process for aluminum alloys involves several steps. First, the alloy is heated until it reaches its melting point, which ranges from 660 to 1220 degrees Fahrenheit, depending on the specific aluminum alloy being used. The liquid aluminum is then injected into the die at high pressure, between 1500 and 2500 pounds per square inch, to fill the mold cavity. The alloy is then rapidly cooled, which solidifies the metal and allows it to retain its shape.
One of the key benefits of the die casting process is its ability to create complex shapes with high dimensional accuracy and consistency. This makes it an ideal process for producing aluminum parts with intricate geometries and precise tolerances.
Aluminum die casting services are critical for creating high-quality die cast aluminum alloys. These services ensure that the finished parts are free of defects and meet all necessary quality standards. Aluminum alloys are particularly well-suited for die casting due to their high strength, low density, and excellent corrosion resistance.
Overall, the die casting process plays a crucial role in the production of die cast aluminum alloys. Its ability to create intricate parts with high dimensional accuracy and consistency makes it a popular choice in industries ranging from aerospace and automotive to consumer electronics and medical devices.
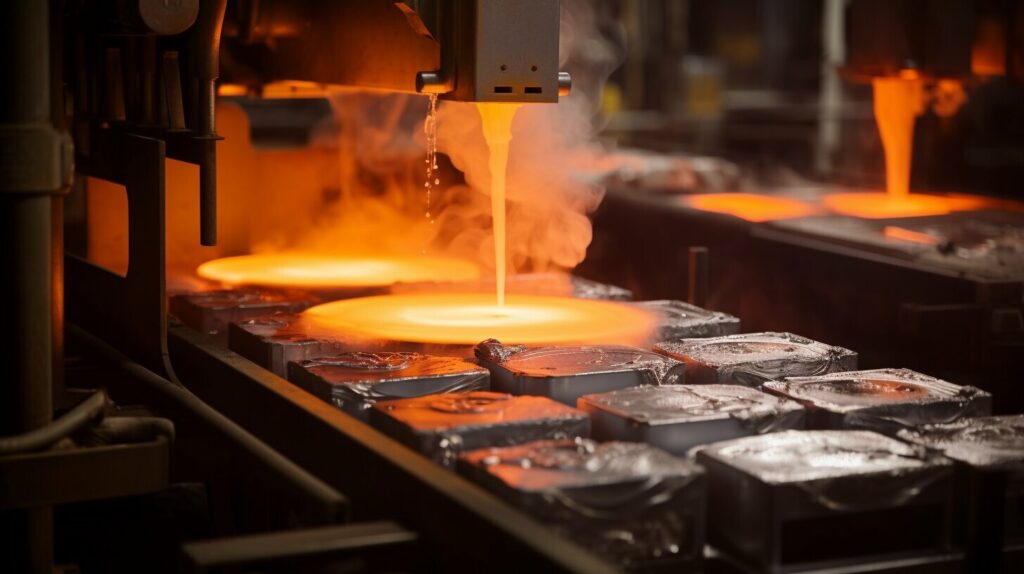
Advantages of Die Cast Aluminum Alloys
Die cast aluminum alloys offer a range of advantages that make them a popular choice for manufacturing various products. Below are some of the main benefits of using die cast aluminum alloys:
Advantage | Description |
---|---|
Corrosion resistance | Die cast aluminum alloys have excellent corrosion resistance, making them suitable for use in harsh environments. The alloy’s oxide layer acts as a barrier against corrosion and enhances durability. |
Dimensional stability | Die cast aluminum alloys have high dimensional stability, which means they retain their shape and size even under extreme physical and environmental conditions. This property makes them ideal for precise parts and products with tight tolerances. |
Ability to withstand high temperatures | Die cast aluminum alloys have a high melting point and can withstand high temperatures, making them suitable for use in high heat environments. The alloy’s thermal conductivity also helps in dissipating heat, which enhances its thermal stability. |
The die casting process that is used to manufacture aluminum die castings further enhances the above properties of the alloys. The high-pressure die casting process produces parts that have a smooth surface finish and excellent dimensional accuracy. It also makes the alloys more uniform, which results in consistent quality and reliability in the final product.
In summary, die cast aluminum alloys offer high corrosion resistance, dimensional stability, and the ability to withstand high temperatures. These advantages, coupled with the exceptional manufacturing capabilities of the die casting process, make die cast aluminum alloys an ideal choice for a wide range of applications.
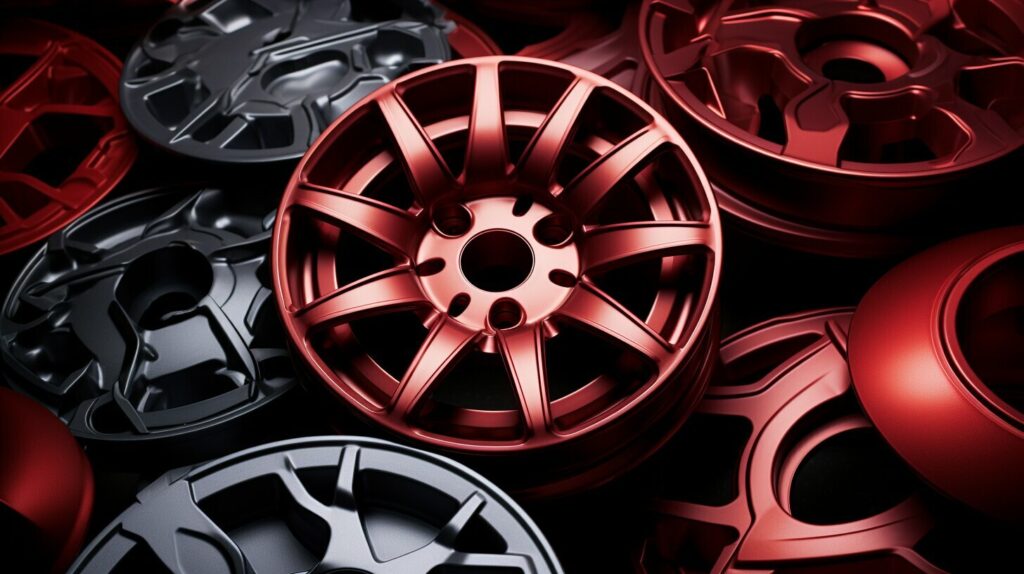
Applications of Die Cast Aluminum Alloys
The versatility and durability of die cast aluminum alloys make them highly popular in a wide range of industries. Let’s take a closer look at some of the most common applications:
Industry | Application |
---|---|
Aerospace | Aircraft hardware fittings |
Automotive | Engine blocks, transmission housings, suspension components, and wheels |
Telecommunications | Satellite and radar equipment, waveguides, and heat sinks |
Computer hardware | Cooling components such as heat sinks and CPU casings |
Construction | Lighting fixtures, door handles, and locks |
Tools and machinery | Power tools, pumps, and gears |
As you can see, die cast aluminum alloys are used in a variety of products and applications due to their excellent mechanical and physical properties.
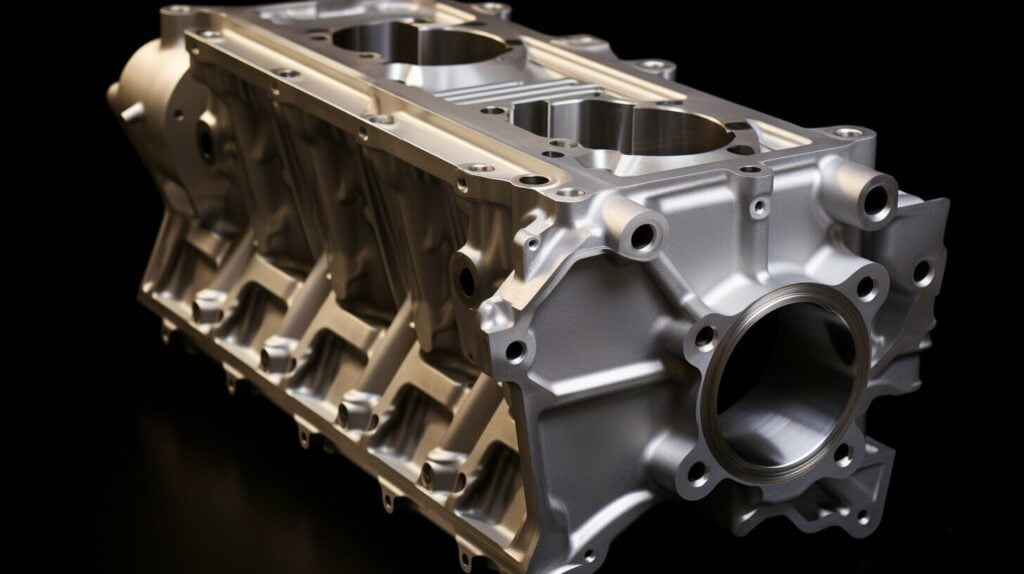
According to a report by MarketsandMarkets, the die casting market for aluminum alloys is projected to reach $49.2 billion by 2025, with the automotive industry accounting for the largest share of this growth.
With their lightweight construction, high-pressure tightness, and excellent corrosion resistance, it’s no wonder die cast aluminum alloys are in such high demand. From aerospace to telecommunications, these alloys are an essential component of modern manufacturing and continue to revolutionize the way we approach product design.
Different Types of Die Cast Aluminum Alloys
Die cast aluminum alloys come in a variety of compositions, each with its unique set of properties and advantages. The most commonly used alloy is the A380 aluminum alloy, which is known for its excellent strength, corrosion resistance, and thermal conductivity. It is widely used in industries such as automotive, aerospace, and consumer electronics.
Other popular die cast alloys include:
Alloy | Composition | Properties/Advantages |
---|---|---|
A360 | Aluminum, silicon, magnesium | High strength, good corrosion resistance, excellent pressure tightness |
A413 | Aluminum, silicon, copper | Good machining properties, excellent pressure tightness, high strength |
A384 | Aluminum, silicon, magnesium | Excellent corrosion resistance, good pressure tightness, high strength |
A413.1 | Aluminum, silicon, magnesium | Good fluidity, high corrosion resistance, excellent pressure tightness |
Each type of die cast aluminum alloy has its own set of applications and benefits. For example, the A360 alloy is commonly used in automotive parts due to its high strength and pressure tightness, while the A384 alloy is frequently used in marine applications because of its excellent corrosion resistance.
As we can see, the use of different die cast aluminum alloys allows manufacturers to choose the alloy that best suits their specific application needs. This diversity of alloys ensures that customers receive high-quality, reliable products that meet their requirements.
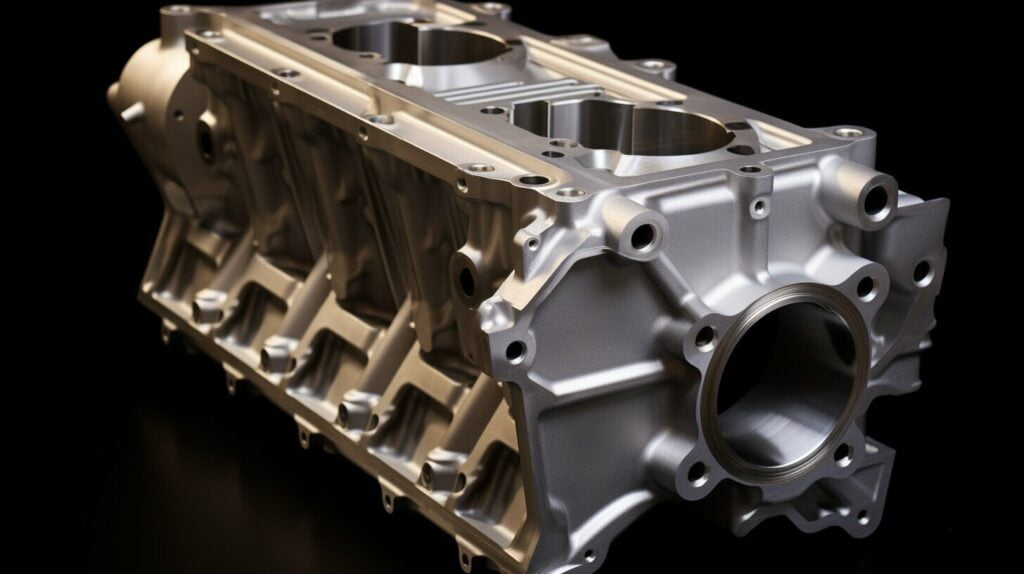
Surface Treatment and Finishing of Die Cast Aluminum Alloys
Surface treatment and finishing are critical steps in the manufacturing process of die cast aluminum alloys. By applying appropriate surface treatments, we can enhance the corrosion resistance, durability and overall quality of the castings.
Die cast aluminum alloys are known for their excellent corrosion resistance, which is further enhanced by surface treatment. Heat treatment is a popular method used to refine the microstructure of castings, improve their mechanical properties, and increase their resistance to corrosion.
Another popular surface treatment technique for die cast aluminum alloys is powder coating. Powder coating provides an attractive finish and protects against corrosion and wear. This technique involves applying a dry, powdered, electrostatically charged material to the surface of the casting, which is then melted and fused to form a uniform coating.
We also use other surface finishing techniques such as anodizing, painting, and plating. Anodizing creates a durable, corrosion-resistant oxide layer on the surface of the castings. Painting and plating provide additional protection against corrosion and wear, as well as improved aesthetics.
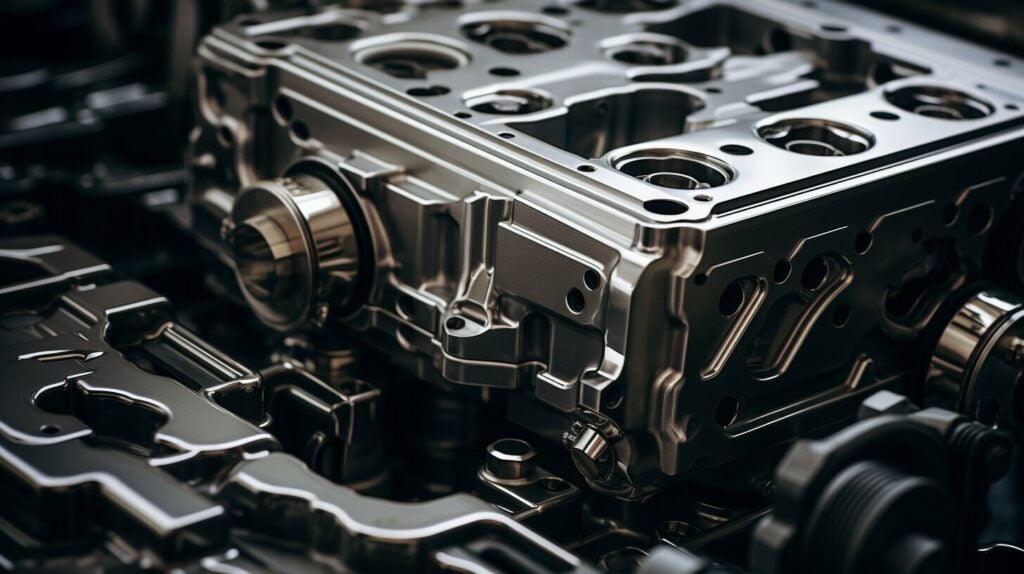
“By applying appropriate surface treatments, we can enhance the corrosion resistance, durability and overall quality of the castings.”
Thanks to these various surface treatment and finishing techniques, die cast aluminum alloys can withstand harsh environments and provide reliable performance for a range of applications.
Challenges and Solutions in Die Casting Aluminum Alloys
While die cast aluminum alloys offer many benefits, they also come with their own set of challenges during the casting process. One of the primary issues is the potential for casting defects, which can result in structural weaknesses, surface blemishes, or other flaws in the finished product. To address this challenge, we use advanced techniques such as simulation modeling and process optimization to identify and eliminate defects before they occur.
Another challenge of die casting aluminum alloys is the need to withstand very high temperatures during the process. This requires special equipment and materials that can handle the heat, as well as careful monitoring and control of the casting conditions. We utilize state-of-the-art equipment and technology to ensure precise temperature control and minimal heat loss, resulting in high-quality castings that meet the most demanding specifications.
Overall, the challenges of die casting aluminum alloys can be overcome through careful planning, advanced technology, and expert knowledge of the casting process. By staying up-to-date with the latest developments and innovations in the industry, we are able to deliver superior quality castings that meet the needs of our customers.
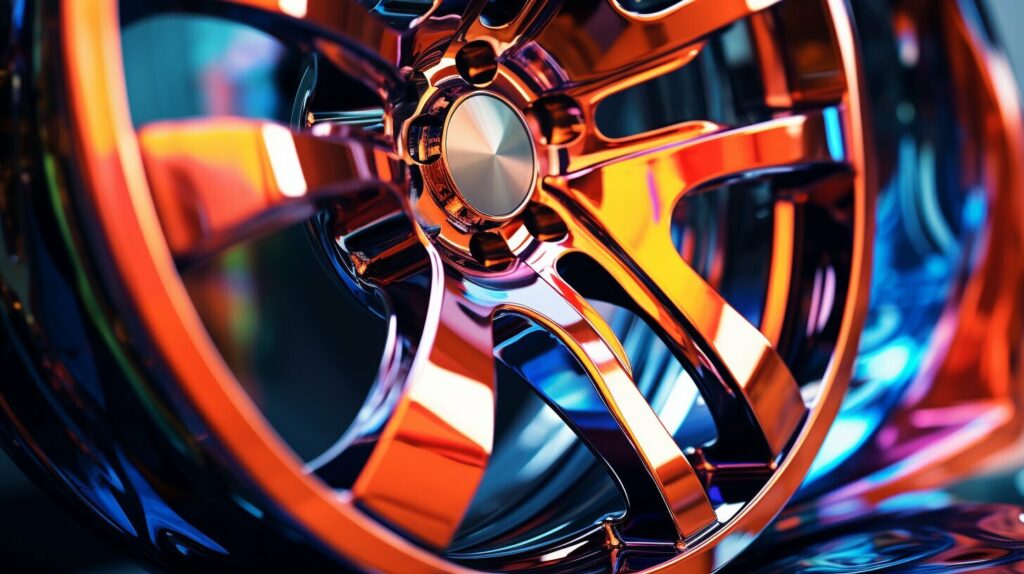
Manufacturing Process and Operations for Die Cast Aluminum Alloys
Producing die cast aluminum alloys involves several manufacturing processes and operations. The process begins with the melting of the aluminum alloy in a furnace, which is then injected into a die casting machine. The machine applies high pressure to the molten metal, forcing it to fill the mold and take on the desired shape.
The die casting machine then quickly cools the casting to solidify it. Once the casting is removed from the mold, it undergoes finishing processes to remove any excess materials or imperfections.
It is essential to note that the liquid aluminum used in the die casting process must be kept in a controlled environment to prevent contamination and ensure consistency in the final product. Maintaining the appropriate temperature and pressure during the manufacturing process is critical for creating high-quality die castings.
Manufacturing Process Steps | Description |
---|---|
Aluminum alloy melting | The aluminum alloy is melted in a furnace. |
Casting injection | The molten metal is injected into a die casting machine and pushed into the mold. |
Cooling and solidification | The casting is cooled and allowed to solidify. |
Removal of the casting | The casting is removed from the mold and undergoes finishing processes. |
Overall, the manufacturing process and operations involved in producing die cast aluminum alloys require a high level of precision and attention to detail to ensure consistent and quality results.
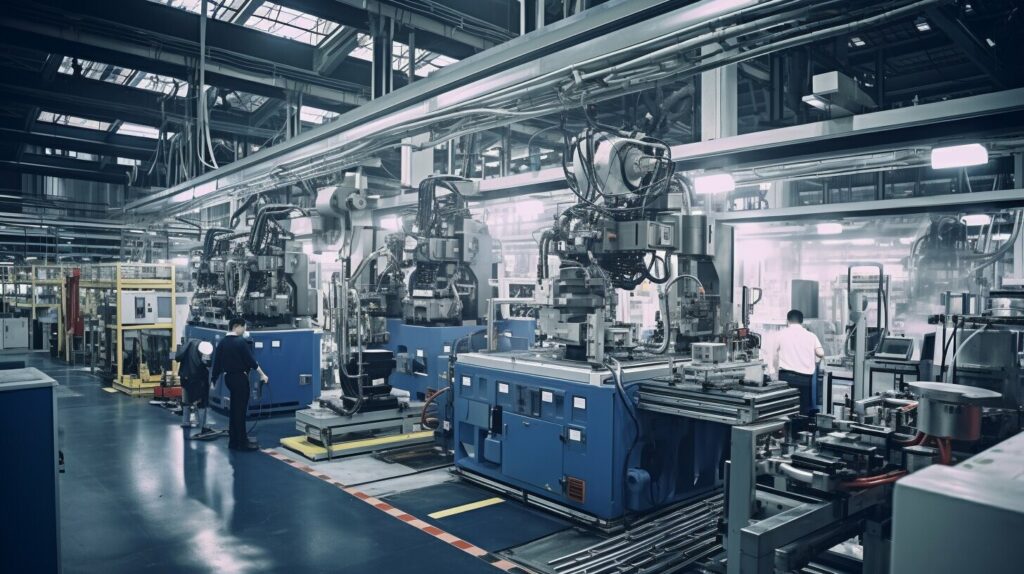
Benefits of Die Cast Aluminum Alloys in the Automotive Industry
When it comes to the automotive industry, die cast aluminum alloys offer various benefits that make them a popular choice for manufacturers. One of the primary advantages is their ability to provide pressure tightness, which is essential in automotive applications.
The lightweight construction of die cast aluminum alloys also makes them ideal for use in the automotive industry. By reducing the weight of vehicle components, manufacturers can improve fuel efficiency and reduce emissions. This is especially important as the industry continues to focus on sustainability and reducing its environmental impact.
Another significant benefit of die cast aluminum alloys in the automotive industry is their ability to produce high-quality engine blocks. The use of aluminum reduces the overall weight of the engine, which can improve performance and handling. It also helps reduce the vibration and noise associated with traditional engine designs.
Overall, the use of die cast aluminum alloys in the automotive industry is a testament to their versatility and durability. As manufacturing techniques continue to evolve, we can expect to see even more innovations and benefits from the use of aluminum in automotive applications.
Future Trends and Innovations in Die Cast Aluminum Alloys
As technology advances and industries continue to evolve, so do the materials that are used to create innovative products. Die cast aluminum alloys are no exception, with new trends and innovations on the horizon.
One emerging trend in die cast aluminum alloys is the development of new high-performance alloys. These alloys offer enhanced strength, durability, and heat resistance, making them ideal for use in high-stress applications. In addition, these alloys are also more environmentally friendly, reducing the carbon footprint of the manufacturing process.
Another trend in the die casting industry is the increasing use of automation and robotics. This allows for faster and more precise production, reducing the risk of defects and improving overall quality. With the use of AI and machine learning, these systems can learn from past production runs and adjust to optimize the process even further.
Advancements in 3D printing technology are also impacting the die casting industry. 3D printing allows for the creation of complex geometries and customized components, opening up new possibilities for design and innovation. This technology is also being used to create tooling for the die casting process, reducing the cost and time required to create molds.
As the demand for sustainable materials and practices continues to grow, the use of recycled aluminum in die casting is also becoming more prevalent. Recycled aluminum offers the same properties and performance as virgin aluminum, but with a smaller environmental footprint. This trend is expected to continue as industries adopt more sustainable practices.
Overall, the future of die cast aluminum alloys looks bright, with new developments and innovations regularly being introduced. As we continue to push the boundaries of what is possible, we can expect to see these alloys being used in even more applications across various industries.
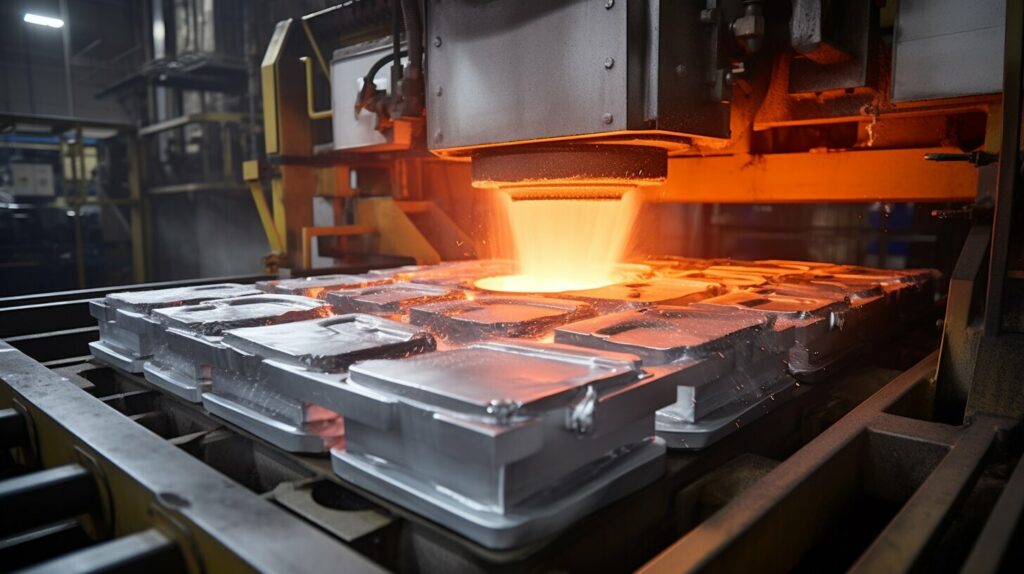
Conclusion
Die cast aluminum alloys offer an array of benefits and applications across various industries. From their high corrosion resistance and dimensional stability to their ability to withstand high temperatures, die cast aluminum alloys offer versatility and durability in many applications.
The die casting process plays a vital role in enhancing the properties of aluminum alloys, making them suitable for a wider range of applications. Surface treatment and finishing techniques, such as heat treatment and powder coating, further enhance the corrosion resistance and quality of the castings.
Despite the challenges associated with die casting aluminum alloys, such as casting defects and the need to withstand very high temperatures during the process, there are various approaches and technological innovations to overcome them.
Looking forward, innovations and emerging technologies in die cast aluminum alloys are likely to increase their use and provide new opportunities across different industries.
Overall, the benefits and applications of die cast aluminum alloys make them an essential material in many industries. As we continue to see advancements in technology and manufacturing processes, the use of die cast aluminum alloys is likely to remain a staple in the production of high-quality components and products.
KT-Foundry’s extensive experience in aluminum die-casting manufacturing has garnered recognition and approval from its clients.
FAQ
Q: What are die cast aluminum alloys?
A: Die cast aluminum alloys are alloys made primarily from aluminum, with the addition of other elements such as copper, magnesium, and silicon. These alloys are specifically designed to be used in the die casting process, which involves injecting molten metal into a mold cavity to create complex shapes with high dimensional accuracy.
Q: What is the die casting process for aluminum alloys?
A: The die casting process for aluminum alloys involves several steps. First, the mold is prepared and lubricated. Then, molten aluminum is injected into the mold at high pressure, filling the cavity and creating the desired shape. After solidification, the casting is removed from the mold and any excess material is trimmed off. The resulting aluminum alloy casting is then ready for further processing or finishing.
Q: What are the advantages of die cast aluminum alloys?
A: Die cast aluminum alloys offer several advantages. They have high corrosion resistance, making them suitable for applications in harsh environments. They also exhibit excellent dimensional stability and can withstand high temperatures, making them ideal for use in automotive and aerospace industries. Additionally, the die casting process enhances the overall mechanical properties of the alloys, resulting in strong and durable castings.
Q: What are the applications of die cast aluminum alloys?
A: Die cast aluminum alloys have a wide range of applications across various industries. They are commonly used in the automotive industry for engine blocks, transmission cases, and other structural components. They are also used in the aerospace industry for aircraft hardware fittings. Additionally, die cast aluminum alloys find applications in consumer electronics, power tools, and many other sectors that require lightweight and durable components.
Q: What are the different types of die cast aluminum alloys?
A: There are several different types of die cast aluminum alloys, with the A380 aluminum alloy being one of the most popular choices. Other common die cast alloys include A360, A413, and ADC12. Each alloy has its own specific properties and applications, with variations in strength, corrosion resistance, and thermal conductivity.
Q: How are die cast aluminum alloys treated and finished?
A: Die cast aluminum alloys can undergo various surface treatments and finishing processes to enhance their properties. These include heat treatment, which improves strength and hardness, and powder coating, which provides a protective layer against corrosion. Other surface finishing techniques such as polishing and anodizing can also be used to improve the appearance and durability of the castings.
Q: What are the challenges in die casting aluminum alloys?
A: Die casting aluminum alloys present certain challenges, such as the potential for casting defects and the need to withstand very high temperatures during the casting process. However, these challenges can be addressed through careful design, process control, and the use of advanced techniques such as vacuum-assisted die casting.
Q: What is the manufacturing process for die cast aluminum alloys?
A: The manufacturing process for die cast aluminum alloys involves several operations. It starts with the melting of aluminum in a furnace, followed by the preparation of the mold. The molten aluminum is then injected into the mold under high pressure, allowing it to fill the cavity and solidify into the desired shape. After the casting is removed from the mold, it may undergo further machining, welding, or other operations to achieve the final product.
Q: What are the benefits of die cast aluminum alloys in the automotive industry?
A: Die cast aluminum alloys offer significant benefits in the automotive industry. They provide pressure tightness, ensuring the integrity of critical components such as engine blocks. They also contribute to lightweight construction, improving fuel efficiency. Additionally, die cast aluminum alloys offer high-quality finishes and excellent heat dissipation properties, making them ideal for use in automotive applications.
Q: What are the future trends and innovations in die cast aluminum alloys?
A: The future of die cast aluminum alloys is characterized by ongoing advancements and innovations. These include the development of new aluminum alloys with improved mechanical properties and enhanced corrosion resistance. Additionally, emerging technologies such as 3D printing and additive manufacturing are being explored for producing complex aluminum castings with greater efficiency and design flexibility.