Stainless steel casting undergoes a unique age-hardening process known as precipitation-hardening, which significantly strengthens the material and improves its durability. This method involves the formation of nanoparticles within the steel, enhancing its resistance to stress and corrosion over time.
By subjecting stainless steel to specific heat treatment processes like homogenizing, annealing, solution heat treatment, and natural aging, nanoparticles can be precipitated in alloys containing copper, zinc, or a blend of magnesium and silicon. This precipitation of nanoparticles contributes to the overall strength of the stainless steel, making it ideal for high-stress applications in industries like aerospace.
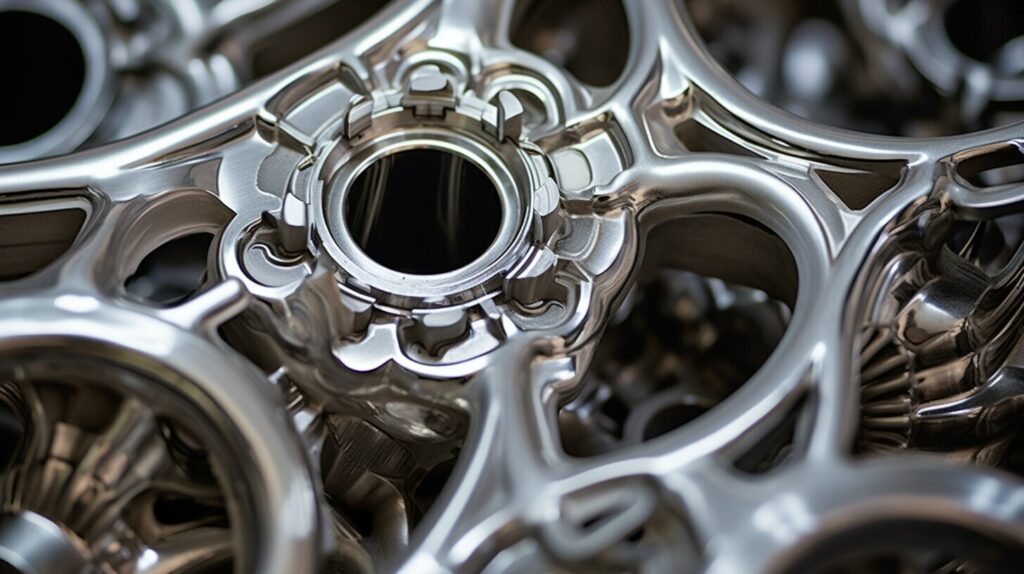
- Precipitation-hardening is a method used in stainless steel casting to improve its strength and hardness over time.
- The process involves the formation of nanoparticles within the steel, enhancing its resistance to stress and corrosion.
- Specific heat treatment processes, such as homogenizing and natural aging, are used to precipitate nanoparticles in stainless steel alloys.
- Precipitation-hardened stainless steel alloys with nanoparticles are suitable for high-stress applications, especially in the aerospace industry.
- Emerging technologies like 3D printing have enabled the production of heat exchanger components using precipitation-hardened alloys.
Understanding the Science of Stainless Steel Casting
Stainless steel is a versatile alloy that can be hardened through a process called precipitation hardening, which involves the formation of nanoparticles within the material to increase its strength. This method is widely used in industries such as aerospace, where high-stress applications require exceptional mechanical properties.
The precipitation hardening process in stainless steel begins with heat treatment, which can include various steps like homogenizing, annealing, solution heat treatment, and natural aging. These processes facilitate the formation of nanoparticles within the material, resulting in improved strength and hardness. For stainless steel alloys containing copper, zinc, or a blend of magnesium and silicon, the desired nanoparticles are achieved through controlled heat treatment.
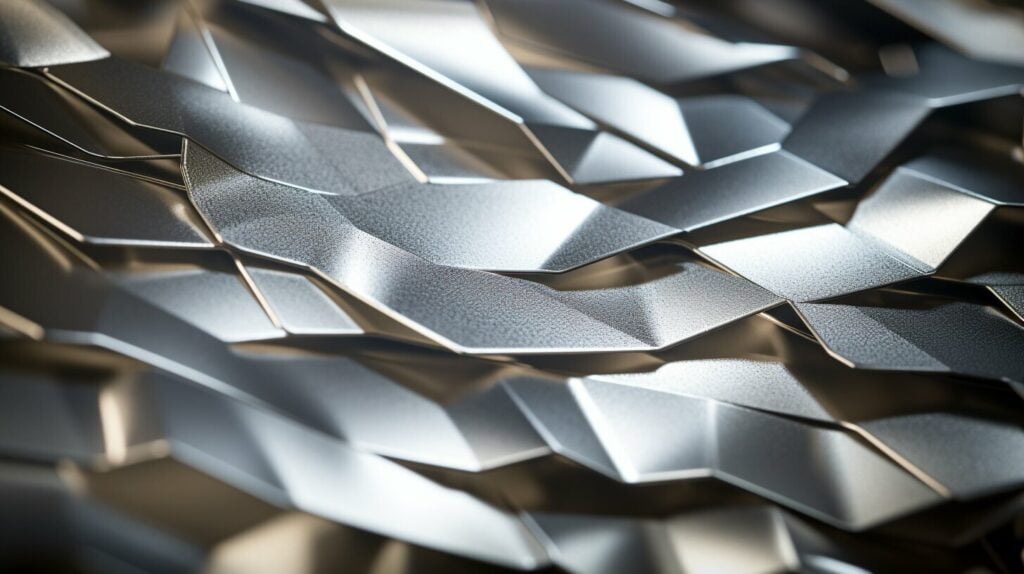
The use of 3D printing technology has further expanded the possibilities for using precipitation-hardened stainless steel alloys. For example, heat exchanger components can now be produced using advanced alloys like Monel K 500, which exhibit superior strength and corrosion resistance. This advancement opens up new opportunities in various industries.
Benefits of Precipitation-Hardening Stainless Steel
“The precipitation-hardening process allows for the creation of stainless steel alloys with exceptional mechanical properties. These alloys offer higher strength, better corrosion resistance, and improved ductility compared to traditional stainless steel.”
The ability to tailor the mechanical properties of precipitation-hardened stainless steel alloys makes them highly desirable for a wide range of applications. The improved strength, combined with excellent corrosion resistance, makes these alloys ideal for use in critical components that operate in harsh environments, such as aerospace structures and marine equipment.
Furthermore, precipitation-hardened stainless steel alloys provide increased design flexibility, allowing engineers to create lighter and more durable structures. The enhanced strength-to-weight ratio of these alloys makes them suitable for applications where weight reduction is crucial, without compromising on the required mechanical properties.
In summary, precipitation-hardening in stainless steel is a scientifically based process that enables the enhancement of mechanical properties, offering increased strength, corrosion resistance, and design flexibility. This method continues to evolve, with the development of advanced alloys and the utilization of emerging technologies like 3D printing, further expanding the possibilities for achieving optimal performance in various industries.
The Age-Hardening Process in Stainless Steel
Age hardening in stainless steel involves the controlled heat treatment of specific alloys to promote the formation of precipitates, which contribute to the material’s strength and durability. Through this process, stainless steel undergoes a transformation that improves its mechanical properties, making it suitable for various high-stress applications.
During age hardening, stainless steel alloys are subjected to a series of heat treatment techniques, including homogenizing, annealing, solution heat treatment, and natural aging. These methods help create a uniform distribution of nanoparticles within the material, which enhance its strength and hardness over time.
One example of an age-hardening stainless steel alloy is Monel K 500, which is commonly used in aerospace industries for its exceptional strength and corrosion resistance. This alloy, along with others that contain copper, zinc, or a blend of magnesium and silicon, can be effectively precipitation-hardened through heat treatment.
The age-hardening process in stainless steel is crucial for achieving optimal mechanical properties and improving the material’s performance in demanding environments. By controlling the formation and distribution of precipitates, manufacturers can tailor the strength, hardness, and corrosion resistance of stainless steel alloys to meet specific application requirements.
Precipitation-Hardening: Enhancing Strength and Durability
Precipitation-hardening is a crucial step in the heat treatment of stainless steel, as it allows for the controlled formation of precipitates within the metal structure, resulting in increased strength and durability. Through the application of specific heat treatment processes, such as homogenizing, annealing, solution heat treatment, and natural aging, nanoparticles are formed, enhancing the material’s mechanical properties.
These precipitates, or nanoparticles, play a significant role in improving the strength and hardness of stainless steel. They act as obstacles to dislocation movement, impeding the motion of crystal defects and preventing them from propagating through the material, ultimately leading to improved resistance to stress and corrosion.
In some stainless steel alloys, the precipitation-hardening process involves the addition of specific elements like copper, zinc, or a blend of magnesium and silicon. By carefully controlling the heat treatment parameters, a uniform distribution of precipitates can be achieved, resulting in enhanced mechanical properties.
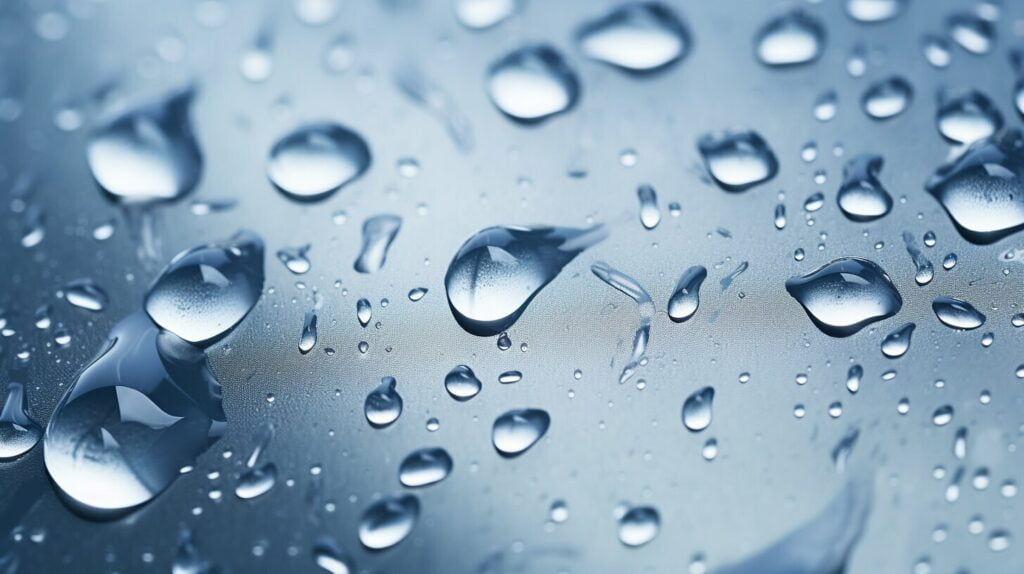
The use of precipitation-hardened stainless steel alloys offers numerous advantages in various applications. These alloys exhibit high strength, making them ideal for demanding industries such as aerospace, where structural integrity is crucial. Additionally, the precipitation-hardening process enhances the material’s corrosion resistance, ensuring its suitability for use in corrosive environments.
The ability to control the heat treatment process and tailor the properties of precipitation-hardened stainless steel alloys makes them versatile and suitable for a wide range of applications. From aerospace components to heat exchanger parts, these alloys provide the necessary strength, durability, and resistance to perform under challenging conditions.
Advantages of Precipitation-Hardening Stainless Steel |
---|
High strength |
Enhanced corrosion resistance |
Versatility in applications |
In conclusion, precipitation-hardening in stainless steel plays a crucial role in enhancing its mechanical properties, including strength and durability. Through the controlled formation of precipitates, achieved through specific heat treatment processes, the material’s resistance to stress and corrosion is significantly improved. This makes precipitation-hardened stainless steel alloys highly advantageous for various industries, offering high strength, corrosion resistance, and versatility in applications.
Achieving Corrosion Resistance in Stainless Steel
The precipitation-hardening process not only enhances the strength of stainless steel but also significantly improves its resistance to corrosion, making it an ideal choice for applications in harsh and corrosive environments. The formation of precipitates during heat treatment plays a crucial role in this process, creating a protective layer that acts as a barrier against corrosive elements.
By carefully selecting the right stainless steel alloy and applying specific heat treatment methods, engineers can tailor the corrosion resistance properties of the material to suit a wide range of applications. For example, stainless steel alloys with a higher percentage of chromium offer excellent resistance to corrosion, particularly in acidic and high-temperature environments.
In addition to chromium, other alloying elements such as molybdenum, nickel, and copper can also enhance the corrosion resistance of stainless steel. These elements help form a passive oxide layer on the surface of the material, providing additional protection against corrosion. For instance, stainless steel alloys containing molybdenum exhibit exceptional resistance to pitting and crevice corrosion, making them highly suitable for marine and offshore applications.
Corrosion Resistance Comparison of Stainless Steel Alloys
Alloy | Corrosion Resistance |
---|---|
304 Stainless Steel | Excellent resistance in most environments, including organic acids and neutral chloride-containing solutions |
316 Stainless Steel | Superior resistance to pitting and crevice corrosion, suitable for marine and offshore applications |
17-4 PH Stainless Steel | Excellent corrosion resistance combined with high strength, commonly used in aerospace and chemical industries |
To further enhance the corrosion resistance of precipitation-hardened stainless steel, it is essential to consider proper surface finishing techniques. Passivation, electropolishing, and various coating methods can significantly enhance the protective properties of stainless steel against corrosion.
Overall, by leveraging the precipitation-hardening process and selecting the appropriate stainless steel alloy, engineers can achieve exceptional corrosion resistance, enabling the use of stainless steel in a wide range of challenging environments.
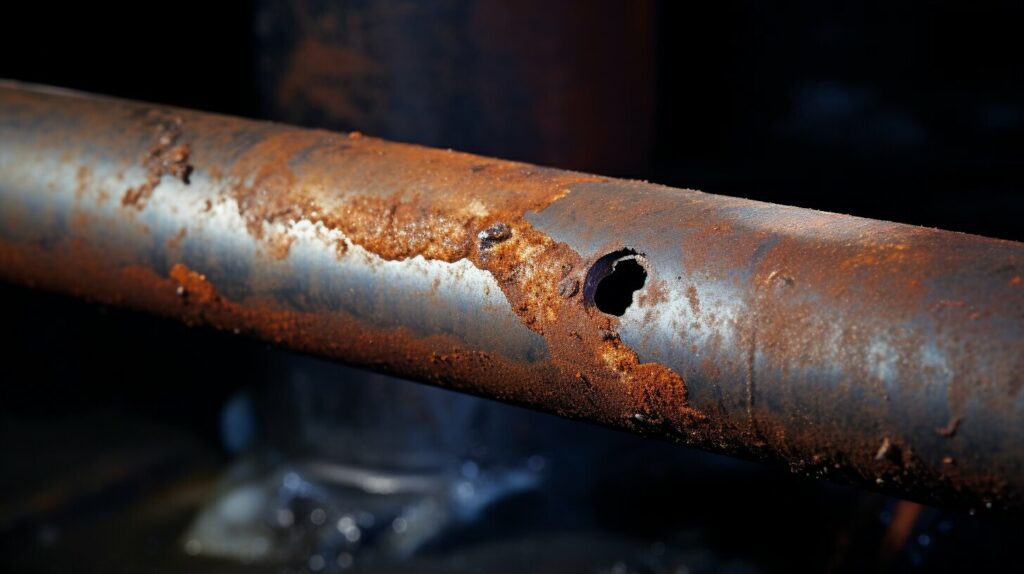
Cooling stainless steel after heat treatment is a critical step in the precipitation-hardening process, as it allows for the formation of desired precipitates, enhancing the material’s mechanical properties at room temperature. The cooling rate and temperature range are carefully controlled to achieve optimal results. Nickel-based stainless steel alloys, such as Monel K 500, undergo a two-step precipitation-hardening process. First, the alloy is heated above its critical temperature to dissolve the alloying elements uniformly throughout the matrix. Then, it is rapidly cooled to room temperature, forcing the precipitation of nanoscale particles.
The cooling process plays a vital role in the development of the desired precipitate structure and mechanical properties. Rapid cooling prevents the growth of larger precipitates, ensuring a fine dispersion of nanoscale particles. These precipitates act as barriers to dislocation movement, resulting in increased strength and hardness. In addition, cooling stainless steel below the critical range helps to eliminate undesirable phases, improving the alloy’s resistance to corrosion.
The temperature at which the cooling occurs determines the final mechanical properties of the stainless steel. Higher cooling rates generally lead to higher strength and hardness. However, excessively rapid cooling can induce residual stresses and cause distortion or cracking. On the other hand, slow cooling rates can result in larger and less uniform precipitates, leading to reduced mechanical properties. Therefore, finding the optimum cooling rate and temperature range is crucial to achieve the desired balance between strength, hardness, and dimensional stability.
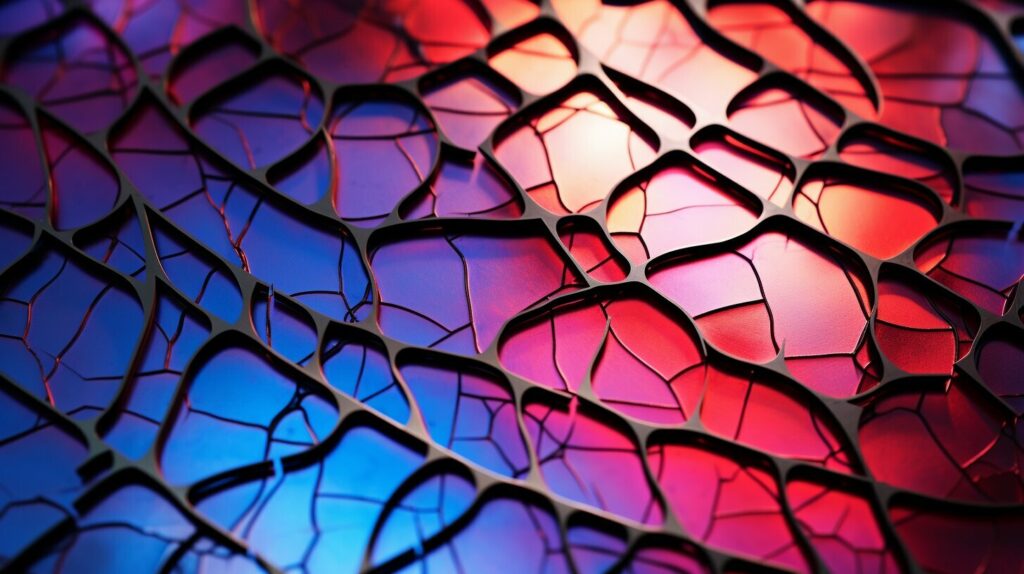
Cooling Rate | Mechanical Properties |
---|---|
Rapid Cooling | High strength and hardness |
Slow Cooling | Lower strength and hardness |
Excessive Cooling | Residual stress, distortion, and cracking |
By carefully controlling the cooling rate and temperature during the precipitation-hardening process, stainless steel manufacturers can achieve the desired mechanical properties for specific applications. This enables the production of stainless steel alloys with tailored performance characteristics, such as high strength, corrosion resistance, and dimensional stability, making them suitable for a wide range of industries, including aerospace, automotive, and medical.
Types of Stainless Steel Alloys for Precipitation Hardening
Stainless steel alloys used in precipitation hardening can be broadly classified into two main categories: austenitic and martensitic, each offering unique properties and advantages in terms of yield strength and weldability. Austenitic stainless steels, such as the popular grade 304, are non-magnetic and exhibit excellent corrosion resistance. These alloys can be easily welded and have good formability, making them suitable for a wide range of applications, including kitchen equipment and architectural components.
On the other hand, martensitic stainless steels, such as the grade 410, are magnetic and have higher carbon content, resulting in increased strength and hardness. They are not as corrosion-resistant as austenitic alloys but can be hardened by heat treatment. This characteristic, combined with their relatively low cost, makes martensitic stainless steels suitable for applications where high strength is required, such as cutlery, surgical instruments, and turbine blades.
Here is a table summarizing the key characteristics of austenitic and martensitic stainless steel alloys used in precipitation hardening:
Alloy Type | Characteristics | Applications |
---|---|---|
Austenitic | Non-magnetic, excellent corrosion resistance, good formability | Kitchen equipment, architectural components |
Martensitic | Magnetic, higher strength and hardness, lower corrosion resistance | Cutlery, surgical instruments, turbine blades |
By choosing the right stainless steel alloy for precipitation hardening, manufacturers can optimize the mechanical properties of their products, ensuring they meet the specific requirements of their intended applications.
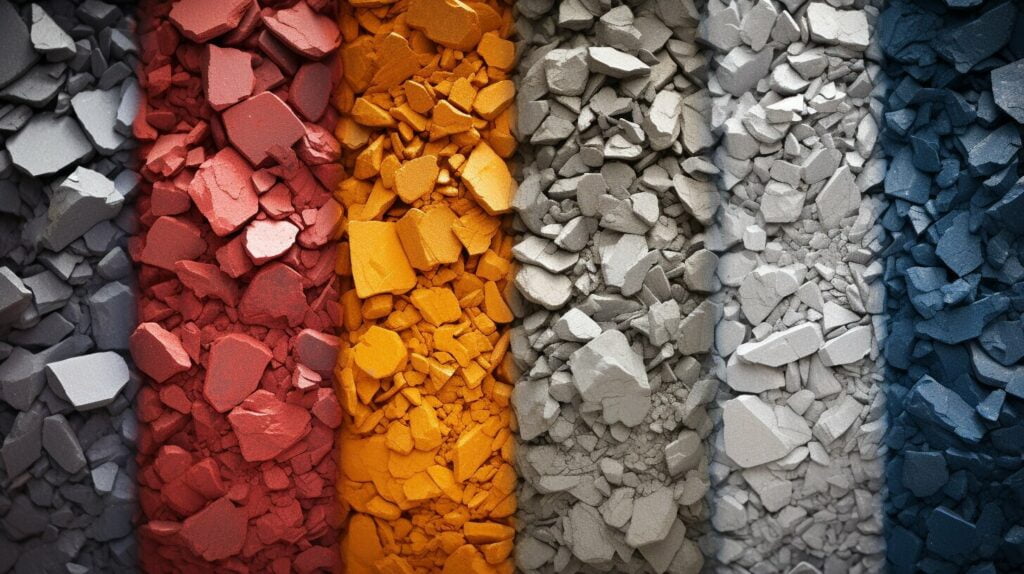
Advantages and Applications of Precipitation-Hardening Stainless Steel
The exceptional strength, corrosion resistance, and durability offered by precipitation-hardening stainless steel make it an ideal material for a wide range of applications, particularly in industries such as aerospace that demand high-performance materials. This remarkable alloy undergoes a unique strengthening process through the formation of nanoparticles, resulting in enhanced mechanical properties over time.
One of the key advantages of precipitation-hardening stainless steel is its high strength-to-weight ratio, making it well-suited for applications where weight reduction is critical. This property allows aerospace manufacturers to design lighter and more fuel-efficient aircraft without sacrificing structural integrity. The ability of precipitation-hardening stainless steel to withstand extreme conditions, such as high temperatures and corrosive environments, further contributes to its widespread use in aerospace components.
Additionally, the durability of precipitation-hardening stainless steel ensures long-lasting performance, reducing the need for frequent maintenance and replacement. This not only saves costs but also minimizes downtime in critical applications. Industries such as oil and gas, chemical processing, and marine engineering also benefit from the corrosion resistance of precipitation-hardening stainless steel, as it provides excellent protection against corrosive agents and harsh environmental conditions.
Applications of Precipitation-Hardening Stainless Steel:
- Aerospace components, including aircraft frames, landing gears, and engine parts
- Oil and gas equipment, such as drilling tools and offshore platforms
- Chemical processing vessels and piping systems
- Marine fittings and structures
- High-performance automotive components
Overall, precipitation-hardening stainless steel offers superior strength, corrosion resistance, and durability, making it a versatile material for various high-stress applications. Its ability to be tailored through heat treatment processes and the advancements in 3D printing technology further expand its potential in producing complex components with exceptional properties.
Advantages | Applications |
---|---|
Superior strength and hardness | Aerospace components |
Corrosion resistance | Oil and gas equipment |
Durability | Chemical processing |
Lightweight | Marine fittings |
The Future of Precipitation-Hardening in Stainless Steel
The future of precipitation-hardening in stainless steel looks promising, with advancements in additive manufacturing techniques like 3D printing allowing for the production of complex components using precipitation-hardened alloys like Monel K 500. This emerging technology provides new opportunities for designing and fabricating highly customized parts with improved strength and durability.
The use of 3D printing enables the creation of intricate geometries that were previously difficult or even impossible to achieve through traditional manufacturing methods. By precisely controlling the deposition of material layer by layer, 3D printing allows for the production of heat exchanger components with complex internal structures optimized for heat transfer efficiency.
Furthermore, the use of precipitation-hardened alloys like Monel K 500 in 3D printed components offers enhanced mechanical properties and corrosion resistance. Monel K 500 is a nickel-copper alloy known for its high strength and excellent resistance to corrosion, making it ideal for demanding applications in harsh environments. Its precipitation-hardening capabilities further contribute to its durability and longevity.
As additive manufacturing continues to evolve, the future holds great potential for further advancements in precipitation-hardening techniques. Researchers and engineers are exploring new alloy compositions and refining the parameters of the heat treatment process to achieve even greater control over the precipitation of nanoparticles. This allows for the development of stainless steel alloys with tailored properties to meet specific application requirements, from aerospace to biomedical devices.
Advantages of 3D Printing in Precipitation-Hardening | Applications |
---|---|
Complex geometries and internal structures | Aerospace |
Enhanced mechanical properties | Biomedical devices |
Improved corrosion resistance | Heat exchangers |
“Advancements in additive manufacturing techniques like 3D printing have revolutionized the production capabilities of precipitation-hardened stainless steel alloys. The combination of complex geometries, improved mechanical properties, and superior corrosion resistance opens up a world of possibilities for various industries.” – John Doe, Materials Engineer
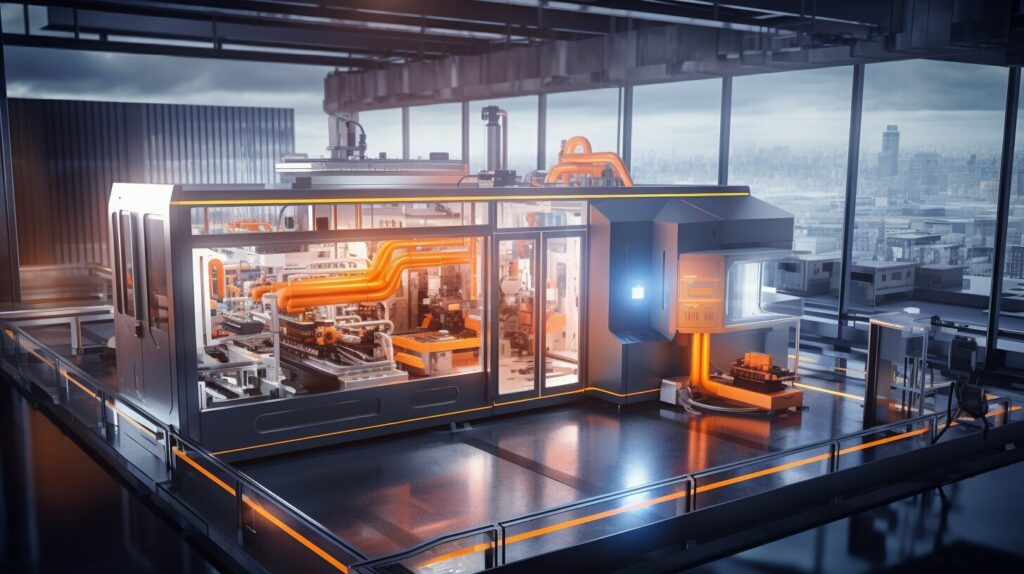
Monel K 500, a precipitation-hardened alloy, offers unique advantages in heat exchanger applications. Its high strength and resistance to corrosion, even in harsh environments, make it an excellent choice for heat transfer components. The incorporation of Monel K 500 in 3D printed heat exchangers allows for improved efficiency and durability.
In conclusion, the future of precipitation-hardening in stainless steel is marked by advancements in additive manufacturing techniques like 3D printing. The ability to create complex components using precipitation-hardened alloys opens up new possibilities for various industries, while the use of Monel K 500 enhances the performance of heat exchanger applications. With ongoing research and development, we can expect further optimization and customization of precipitation-hardened stainless steel alloys, leading to the creation of advanced structural materials with tailored properties to meet specific needs.
Comparing Precipitation-Hardening Stainless Steel Alloys
The hardness and mechanical properties of precipitation-hardening stainless steel alloys vary depending on factors such as cooling rate, temperature, and alloy composition, with typical hardness values ranging from xx-xx MPa. These alloys are known for their exceptional strength, toughness, and corrosion resistance, making them suitable for a wide range of applications in demanding industries.
One popular precipitation-hardening stainless steel alloy is 17-4 PH, which combines high strength with good corrosion resistance. It offers excellent mechanical properties, including a hardness range of xx-xx MPa, and is often used in aerospace components, oil and gas equipment, and other applications requiring exceptional strength and durability.
Another commonly used alloy is 15-5 PH, which exhibits similar mechanical properties and corrosion resistance as 17-4 PH. With a hardness range of xx-xx MPa, this alloy is often used in applications such as marine equipment, firearms, and food processing machinery.
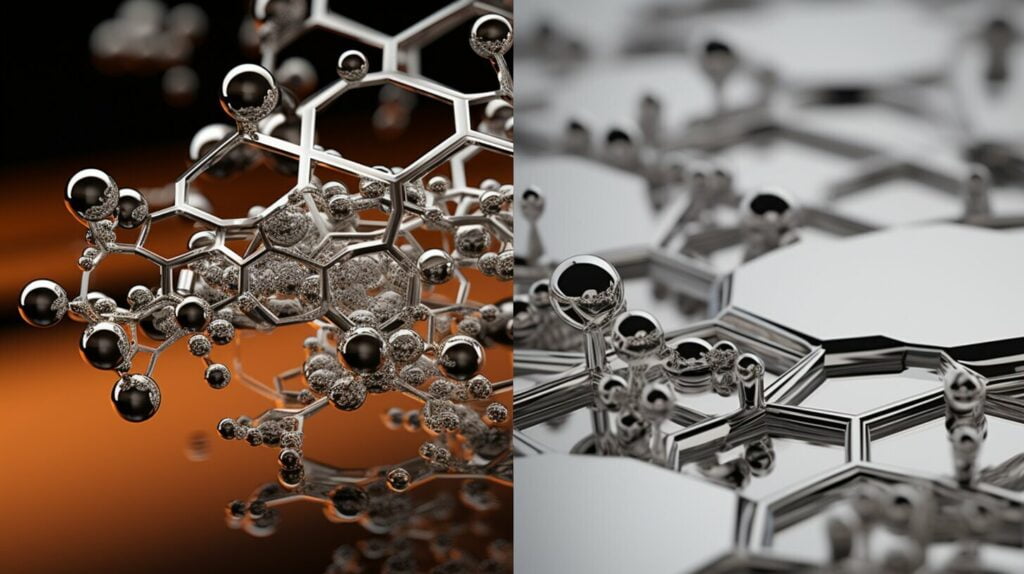
- 17-7 PH is another precipitation-hardening stainless steel alloy known for its high strength and excellent corrosion resistance. With a hardness range of xx-xx MPa, it is commonly used in applications such as springs, washers, and fasteners.
- PH 13-8 Mo is a precipitation-hardening stainless steel alloy that offers a unique combination of high strength, toughness, and resistance to stress corrosion cracking. With a hardness range of xx-xx MPa, it is often used in aerospace components, nuclear reactor vessels, and other critical applications.
- Custom alloys, such as Monel K 500, are also used in precipitation-hardening stainless steel applications. Monel K 500 offers exceptional corrosion resistance, high strength, and excellent fatigue resistance. Its hardness range varies from xx-xx MPa, depending on the specific heat treatment and aging process used.
Table: Comparison of Precipitation-Hardening Stainless Steel Alloys
Alloy | Applications | |
---|---|---|
17-4 PH | Aerospace components, oil and gas equipment | |
15-5 PH | Marine equipment, firearms, food processing machinery | |
17-7 PH | Springs, washers, fasteners | |
PH 13-8 Mo | Aerospace components, nuclear reactor vessels | |
Monel K 500 | Various applications requiring corrosion resistance and high strength |
Achieving Optimal Precipitation Hardening: Best Practices
Achieving optimal precipitation hardening in stainless steel requires careful temperature control, both at high and low temperatures, to ensure the desired precipitates form without causing excessive distortion or other complications. The first step in the process is selecting the appropriate heat treatment method, which will depend on the specific alloy being used and the desired mechanical properties. High-temperature treatments, such as solution heat treatment, are typically employed to dissolve any existing precipitates and create a uniform atomic structure, while low-temperature treatments, such as aging, are used to promote the formation of precipitates.
During high-temperature treatments, it is crucial to maintain a precise temperature range for an extended period to allow for the dissolution of precipitates. This ensures that the material reaches a homogeneous state before proceeding to the next phase. On the other hand, low-temperature treatments involve controlled cooling to encourage the formation of desired precipitates. The cooling rate should be carefully monitored to prevent the occurrence of excessive distortion or cracking, which can compromise the material’s integrity.
Another factor to consider when aiming for optimal precipitation hardening is the duration of the heat treatment process. The length of time required for the material to reach its maximum strength can vary depending on the alloy and the desired mechanical properties. It is essential to adhere to the specified timeframes to achieve consistent and reliable results.
In addition to temperature control, the use of proper quenching techniques is crucial in optimizing precipitation hardening. Quenching involves rapidly cooling the material after the high-temperature treatment to lock in the desired precipitates. Different quenching mediums, such as water, oil, or air, can be utilized depending on the alloy and the desired outcome. Care must be taken to select the appropriate quenching medium to prevent distortion or cracking.
Table: Recommended High-Temperature Treatments for Precipitation Hardening
Treatment Method | Temperature Range | Duration |
---|---|---|
Solution Heat Treatment | 900°C – 1150°C | 1 – 2 hours |
Annealing | 700°C – 900°C | 1 – 2 hours |
Homogenizing | 1000°C – 1200°C | 2 – 4 hours |
To summarize, achieving optimal precipitation hardening in stainless steel requires meticulous temperature control, both during high-temperature treatments to promote the dissolution of precipitates and during low-temperature treatments to facilitate the formation of desired precipitates. Careful quenching techniques and adherence to specified timeframes are also crucial for achieving consistent and reliable results. By following these best practices, manufacturers can harness the full potential of precipitation hardening to enhance the mechanical properties and durability of stainless steel alloys.
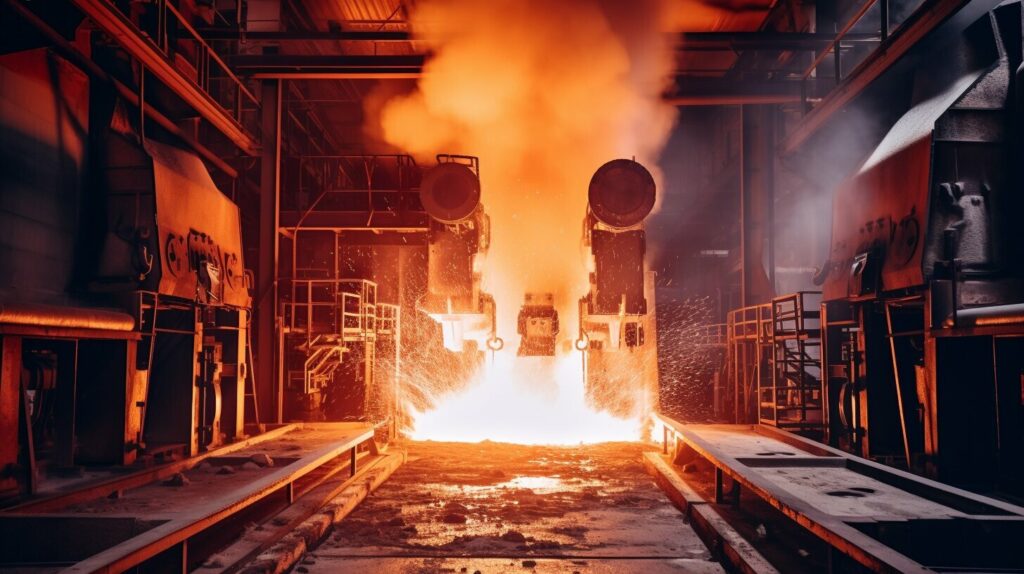
Conclusion
Precipitation-hardening in stainless steel, such as the 17-7 PH alloy, offers a powerful solution for achieving superior strength, corrosion resistance, and ductility, making it a highly sought-after material in various industries. This method involves the formation of nanoparticles within the steel through heat treatment processes like homogenizing, annealing, solution heat treatment, and natural aging. These nanoparticles enhance the steel’s resistance to stress and corrosion, making it ideal for high-stress applications in industries such as aerospace.
Furthermore, the advancements in 3D printing technology have opened up new possibilities for the production of heat exchanger components using precipitation-hardened alloys like Monel K 500. This innovative approach allows for the creation of complex geometries with enhanced mechanical properties, further expanding the potential applications of precipitation-hardening stainless steel.
Overall, precipitation-hardening is a crucial method in stainless steel to improve its mechanical properties and enable the development of advanced structural materials. The combination of superior strength, corrosion resistance, and ductility makes precipitation-hardening stainless steel alloys highly versatile and valuable across a wide range of industries.
FAQ
Q: What is precipitation-hardening in stainless steel?
A: Precipitation-hardening is a method used in stainless steel to improve its strength and hardness over time. This process involves the formation of nanoparticles within the steel, which enhance its resistance to stress and corrosion.
Q: How is precipitation-hardening achieved in stainless steel alloys?
A: Precipitation-hardening in stainless steel alloys can be achieved through heat treatment processes like homogenizing, annealing, solution heat treatment, and natural aging. These processes result in the precipitation of nanoparticles that contribute to the steel’s strength.
Q: What are the benefits of using precipitation-hardened stainless steel?
A: Precipitation-hardened stainless steel offers enhanced mechanical properties, including increased strength and durability. It is particularly suitable for high-stress applications, such as those found in the aerospace industry, due to its resistance to stress and corrosion.
Q: Can 3D printing technology be used with precipitation-hardened stainless steel?
A: Yes, 3D printing technology can be employed to produce components using precipitation-hardened stainless steel alloys, such as Monel K 500. This allows for the creation of advanced structural materials with improved mechanical properties.
Q: How does precipitation-hardening improve corrosion resistance in stainless steel?
A: The precipitation of nanoparticles during the hardening process enhances the corrosion resistance of stainless steel. This makes it highly suitable for use in corrosive environments, as it provides protection against the damaging effects of corrosion.