Welcome to our comprehensive analysis of the expenses involved in aluminum die casting. In this article, we will delve into the intricate details of cost analysis, providing invaluable insights to help businesses optimize their production costs efficiently. By examining various factors such as material cost, production cost, and tooling cost, we aim to equip you with the knowledge necessary to streamline your operations and achieve cost optimization.
Key Takeaways:
- Understanding the expenses in aluminum die casting is vital for cost optimization.
- Factors such as material cost, production cost, and tooling cost should be carefully analyzed.
- Implementing strategies to reduce custom die casting costs can lead to significant savings.
- Analyzing the impact of material and production costs helps in identifying areas for improvement.
- Tooling cost considerations, such as die set, machining, and part geometry, play a crucial role in cost management.
Understanding Investment Casting Cost Components
Investment casting cost can be divided into direct cost and period cost. Direct manufacturing costs include direct materials, direct labor, fuel and power, and manufacturing costs. On the other hand, period costs such as management expenses are the fixed costs of an enterprise. It is important to analyze the cost according to the manufacturing process, taking into account factors such as wax mold manufacturing, shell making, melting and pouring, and post-treatment. The cost structure varies based on the weight of the casting and the process yield.
Direct Cost Components
The direct cost components of investment casting include:
- Direct Materials: These are the raw materials used in the casting process, such as metal alloys, refractories, and consumables.
- Direct Labor: This includes the cost of skilled labor involved in the casting process, including operators, technicians, and quality control personnel.
- Fuel and Power: The cost of energy sources used for heating, melting, and other process requirements.
- Manufacturing Costs: This includes the cost of equipment maintenance, tooling, and other direct manufacturing expenses.
Period Cost Components
The period cost components of investment casting include:
- Management Expenses: These are the fixed costs associated with running the enterprise, such as salaries, administrative costs, and overhead expenses.
- Selling and Distribution Expenses: These are the costs associated with marketing, advertising, and delivering finished castings to customers.
- Research and Development Expenses: The cost of conducting research and developing new casting techniques or materials.
By understanding the different components of investment casting costs, businesses can identify areas for optimization and cost reduction. Analyzing the cost breakdown according to direct and period cost components allows for a more comprehensive evaluation of the overall expenses involved in investment casting. This knowledge can help businesses make informed decisions to improve cost efficiency and maximize profitability.
Strategies for Reducing Custom Die Casting Costs
When it comes to custom die casting, finding ways to reduce costs without compromising quality is a top priority for businesses. Implementing design strategies and leveraging die casting capabilities can result in significant cost savings. Let’s explore some effective strategies to help lower custom die casting costs:
1. Upfront Design Preplanning
One of the key strategies for reducing costs in custom die casting is upfront design preplanning. By thoroughly examining the design requirements and considering factors such as part complexity, material usage, and manufacturing feasibility, potential cost-saving opportunities can be identified early in the design process. This allows for adjustments to be made before production, minimizing the risk of costly redesigns and rework.
2. Part Consolidations
Another effective strategy is part consolidation, which involves consolidating multiple components into a single die-cast part. By reducing the number of individual parts needed and combining their functionalities, material usage and manufacturing processes can be optimized, resulting in cost reductions. Part consolidation also simplifies assembly processes, leading to further efficiency gains.
3. Minimizing Unnecessary Overdesign
Overdesigning, or adding excessive material or features to a part, can significantly drive up costs in custom die casting. By engaging in thorough design analysis and optimizing part geometry, it is possible to minimize unnecessary overdesign. This not only reduces material usage but also enhances the overall efficiency of the manufacturing process, resulting in cost savings.
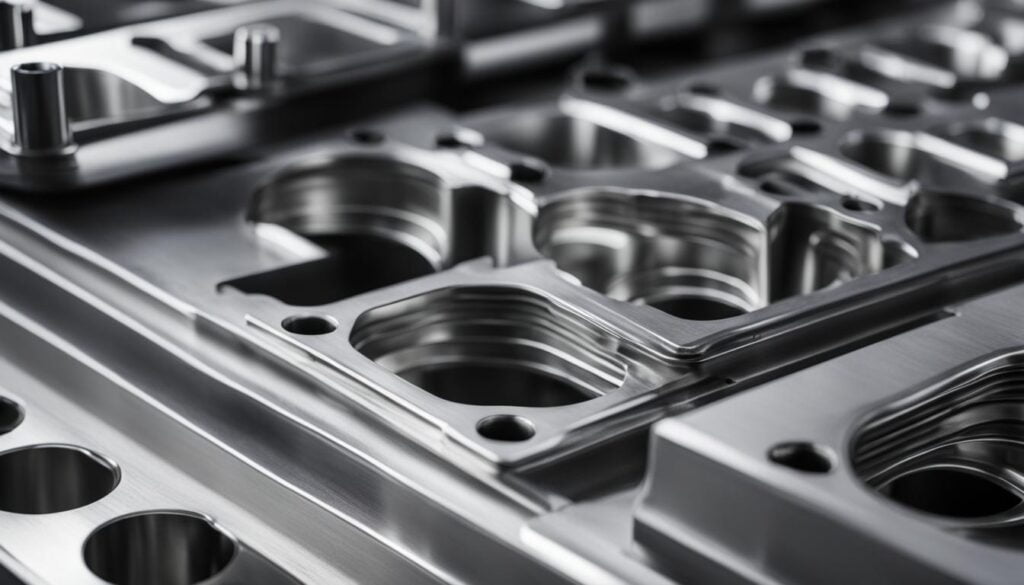
By implementing these strategies for reducing custom die casting costs, businesses can achieve significant cost savings without compromising on quality. It is important to leverage the expertise of experienced die casters who can provide valuable insights and guidance throughout the design and manufacturing process. Taking a proactive approach to cost optimization ensures a competitive edge in the highly competitive custom die casting industry.
Analyzing the Impact of Material and Production Costs
When it comes to aluminum die casting, understanding the impact of material and production costs is essential for optimizing cost efficiency. Material cost is determined by the weight of material required and the unit price of that material. Thinner walls in die casting typically lower the material cost, despite the larger channels needed to ensure proper filling. On the other hand, production cost is primarily calculated based on the hourly rate and cycle time.
The size of the die casting machine, clamping force, and injection time all play a significant role in determining production cost. For instance, a larger die casting machine may have a higher hourly rate, but it can produce more parts per cycle, reducing the overall production cost. Additionally, different cycle times can influence the cost, as longer cycle times result in higher production costs.
It is important to consider various factors when analyzing material and production costs. Cooling time, resetting time, and the use of hot chamber machines also impact the overall cost optimization. By carefully evaluating these factors, businesses can make informed decisions to minimize expenses and maximize production efficiency.
Table: Material and Production Cost Factors
Factors | Impact on Cost |
---|---|
Material Weight | Influences material cost |
Thin Walls | Reduces material cost |
Die Casting Machine Size | Affects production cost |
Clamping Force | Directly impacts production cost |
Injection Time | Determines production cost |
Cooling Time | Impacts overall cost optimization |
Resetting Time | Affects cost efficiency |
Hot Chamber Machines | Influences cost optimization |
By carefully analyzing the impact of material and production costs, businesses can identify opportunities for cost optimization. Making informed decisions based on factors such as material weight, wall thickness, die casting machine size, and cycle time can result in significant savings. It is crucial to strike a balance between cost considerations and design and manufacturing realities to achieve optimal results in aluminum die casting.
Examining the Factors Affecting Tooling Cost
When it comes to aluminum die casting, tooling cost is a significant factor that businesses need to consider. Tooling refers to the various molds, dies, and equipment required to produce high-quality castings. The cost of tooling can vary based on several factors, including the size and complexity of the part, the machining required, and the overall volume of production. By understanding and analyzing these factors, businesses can make informed decisions to optimize tooling cost and improve production efficiency.
One key factor that affects tooling cost is the die set. The die set includes the various components and parts that are used to create the mold for casting. The size of the part’s envelope, including its overall dimensions and weight, plays a significant role in determining the cost of the die set. Larger, more complex parts require larger and more intricate dies, which can drive up the tooling cost.
Another factor that affects tooling cost is the machining required for the casting. Machining refers to the process of shaping and finishing the casting to achieve the desired specifications. Factors such as cavity size, depth, feature count, tolerance, and surface roughness can all impact the machining requirements and, consequently, the overall tooling cost.
Additionally, the volume and geometry of the part can also impact tooling cost. Higher volumes of production generally allow for economies of scale, resulting in lower tooling costs per part. Similarly, parts with simpler geometries are typically easier and less expensive to produce, leading to lower tooling costs. Businesses should carefully analyze these factors and consider how they can optimize part volume and geometry to reduce tooling expenses.
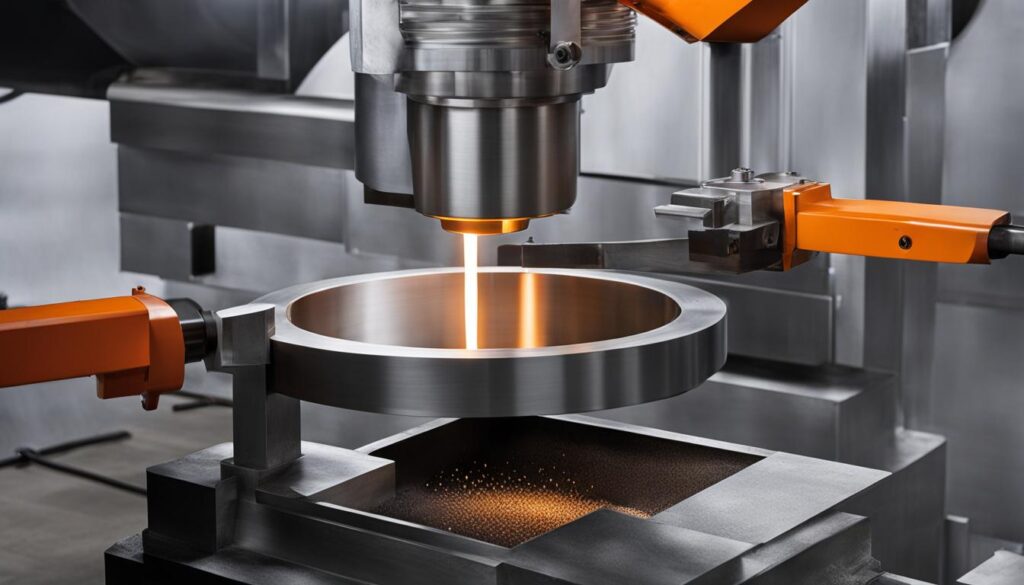
Factors Affecting Tooling Cost | Impact on Tooling Cost |
---|---|
Die Set | Size of the part’s envelope |
Machining | Cavity size, depth, feature count, tolerance, surface roughness |
Part Volume | Higher volumes allow for economies of scale |
Part Geometry | Complex geometries can increase tooling cost |
Leveraging Prototyping and Lowering Die Costs
In the aluminum die casting process, prototyping plays a crucial role in understanding the intricacies of die design and final production requirements. By leveraging in-house prototyping capabilities, businesses gain valuable insights into potential design improvements, ensuring optimal part quality while also contributing to cost savings. Through prototyping, engineers can identify potential issues early on, refining the design to eliminate costly errors and minimizing the need for costly rework during the production stage.
Partnering with a die caster who has an established relationship with an offshore die maker is another effective strategy for lowering die costs. Offshore manufacturing can offer cost advantages due to lower labor and material expenses, allowing businesses to access high-quality dies at a more competitive price. This collaboration also provides the opportunity to tap into the expertise of offshore die makers, who often possess specialized knowledge and techniques that can further optimize the die casting process.
Another avenue for reducing die costs is the utilization of multi-cavity dies. By incorporating multiple cavities within a single die, businesses can significantly increase production efficiency and reduce costs per part. Multi-cavity dies enable the simultaneous casting of multiple parts with each cycle, effectively reducing cycle time and maximizing the utilization of the die. This approach is particularly beneficial for high-volume production runs, where economies of scale can be achieved through the increased output per cycle.
Comparing Offshore and Onshore Die Costs | |
---|---|
Factors | Offshore Die Costs |
Labor and Material Expenses | Lower due to lower costs in offshore manufacturing |
Expertise and Specialized Techniques | Access to the knowledge and techniques of experienced offshore die makers |
Collaboration and Communication | Close partnership between the die caster and offshore die maker |
In summary, prototyping and exploring options for lowering die costs through offshore manufacturing and multi-cavity dies are effective strategies for optimizing production costs in aluminum die casting. By leveraging prototyping capabilities, businesses can refine their designs, reduce errors, and enhance part quality, resulting in cost savings in the long run. Collaborating with offshore die makers and utilizing multi-cavity dies offer opportunities to reduce tooling costs and increase production efficiency. When combined with other cost reduction strategies discussed in this article, these approaches can help businesses achieve optimal results in aluminum die casting.
Conclusion
In conclusion, optimizing production costs in the aluminum die casting process is vital for businesses seeking efficient operations. By analyzing investment casting cost components, implementing strategies to reduce custom die casting costs, evaluating material and production costs, considering tooling cost factors, leveraging prototyping, and exploring options for lower die costs, businesses can make informed decisions to improve cost optimization and production efficiency.
Understanding the various cost components involved in aluminum die casting is essential. By carefully examining direct manufacturing costs and period costs, businesses can identify areas where cost savings are possible. Utilizing design strategies, such as upfront design preplanning and part consolidations, can significantly reduce custom die casting costs. Additionally, partnering with a die caster that offers in-house prototyping can lead to improved part quality and cost savings.
By assessing material costs, production costs, and tooling costs, businesses can make informed decisions to optimize their production processes. Factors such as thinner walls, cycle time, and the size of the die casting machine can all impact costs. Furthermore, considering the size of the part’s envelope, machining requirements, and part volume can help in determining tooling costs. Exploring options such as offshore manufacturing and multi-cavity dies can also lead to substantial cost reductions.
In order to achieve cost optimization and production efficiency in aluminum die casting, businesses must strike a balance between cost considerations and design and manufacturing realities. By implementing the strategies and insights discussed in this article, businesses can streamline their operations and maximize their cost efficiency in the aluminum die casting process.
FAQ
What factors contribute to the cost of investment casting?
Investment casting costs include direct manufacturing costs such as materials, labor, fuel, and power, as well as period costs like management expenses.
How can businesses reduce costs in custom die casting?
Design strategies such as upfront planning, part consolidation, and avoiding unnecessary overdesign can help achieve cost savings. Leveraging die casting capabilities and considering wall thickness variations can also lead to cost reductions.
What are the main components of material and production costs in die casting?
Material cost is determined by the weight of material required and its unit price, while production cost is calculated based on the hourly rate and cycle time. Die casting machine size, clamping force, injection time, cooling time, and resetting time all affect production cost.
What factors impact the cost of tooling in die casting?
Tooling cost is influenced by factors such as part size, cavity machining, cavity size, depth, feature count, tolerance, surface roughness, quantity of parts, material used, and the number of side-action directions.
How can prototyping and die cost optimization help in reducing expenses?
In-house prototyping helps in understanding die design and final production requirements, while working with an offshore die maker can reduce tooling costs. Considering multi-cavity and family dies and exploring options like unit die production can also result in cost savings.