Lost wax casting technique involves creating and melting wax patterns. A ceramic shell molded from the wax-like material is then utilized to cast the final metal piece using the molten metal.
With the emergence of 3D-printed lost wax castings, the entire process reduces the costs whem creating a mold. Because of this, it became a preferred method for cost-efficient production.
It eliminates the costs of injection molding, making it a good option for cost-efficient production.
How 3D Printing is Done for Lost Wax Casting or Investment Casting
Designing The 3D Wax Model
The first step in 3D printed lost wax casting is to design the 3D model. This is typically done using computer-aided design software.
The designer can create highly detailed and accurate models that undergo a wax printing process, which will be used as the pattern for the ceramic mold.
Wax Printing and Post Processing of The 3D Model
It involves a process known as “slicing,” which consists of breaking the model down into thin layers that can be printed individually. The slicing software creates a digital map of the model that tells the printer how to build the physical object.
The pattern is printed using a wax 3D printer with a heated nozzle to melt and deposit the castable wax or wax-like resin layer by layer. The wax pattern is removed from the printer and cleaned to remove any supports or excess wax filament.
Once the wax pattern is printed, it must be cleaned and finished. This involves removing any support structures used during printing and polishing the model to create a smooth, even surface.
After the wax pattern has been finished and smoothed, it needs to be polished to create a smooth and even surface. This is done using a polishing wheel or by hand using a polishing compound. The goal is to create a surface free from imperfections and ready for casting.
Casting Process
Once the ceramic mold is finished, it is heated to extremely high temperatures in a furnace. This removes the wax pattern from the ceramic mold and leaves a hollow in the mold in the precise shape of the final product, where it is filled with liquid metal.
The ceramic shell is chipped away when the metal has cooled and hardened.
Benefits of 3D Printing in Lost Wax Casting Process
Traditional lost wax casting process can be time-consuming, expensive, and limited in terms of design complexity. Here are some benefits of 3D printing in the lost wax casting process and how it can help manufacturers increase efficiency, reduce costs, and improve product quality.
Accurate and Precision Casting Design
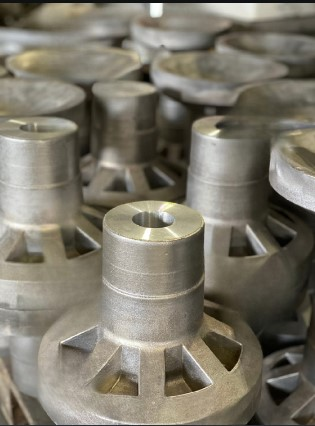
3D printing allows for greater accuracy and precision in creating wax patterns, resulting in a more precise final product.
Additionally, its fast-design revision advantage gives designers and engineers greater flexibility. They can explore new design possibilities, no matter how complex they are.
Faster and More Efficient Lost Wax Casting Technique
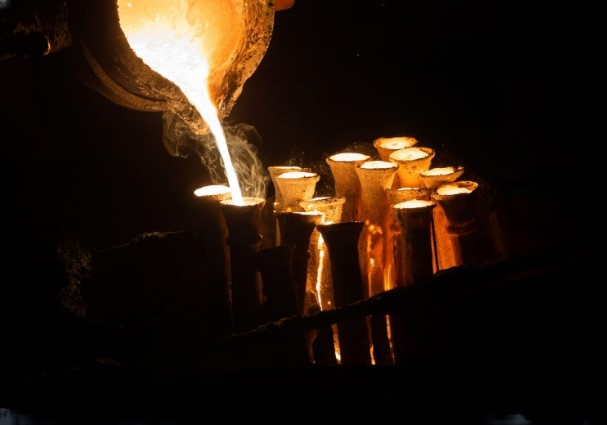
Rapid prototyping is a significant advantage of using 3D printing in lost wax casting. Rapid prototyping using 3D printing saves both time and money by eliminating the need for physical models.
Complex patterns and complicated forms is not a problem because of the capabilities of 3D printing. This increased flexibility can result in more innovative and unique products.
Reduced Material Waste of The Wax Pattern
The use of 3D printing in lost wax casting can help to reduce waste and improve environmental sustainability. With traditional wax carving techniques, a significant amount of wax is wasted in the production process. 3D printing allows more efficient use of materials and significantly reduces waste.
Some 3D printers can use easily recyclable materials, such as PLA or ABS plastics. Any unused material or failed prints can be recycled and used again, reducing waste.
3D printing can reduce waste in lost wax casting by reducing material consumption. Traditional casting methods often require more material than necessary, resulting in wasted material. With 3D printing, only the exact amount of material needed is used to create the pattern, reducing waste.
With 3D printing, precise patterns can be created, resulting in fewer errors and less wasted material.
Applications of Lost Wax 3d Printing
Lost wax 3D printing is a technology that combines the benefits of both 3D printings and lost wax casting. Because of its adaptability and precision in manufacturing complicated metal components, this technique has found widespread use across a number of sectors.
Jewelry Making
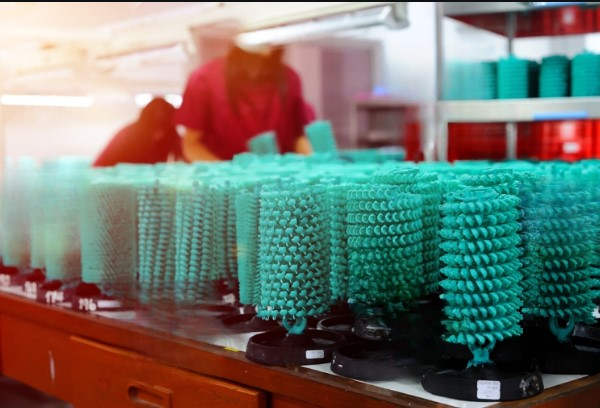
The lost wax 3D printing technology allows for the creation of highly detailed and intricate designs previously impossible to achieve. Second, it reduces the time and labor required to make jewelry, resulting in a more cost-effective process. The 3D printing with lost wax enables the designing of different types of jewelry.
The ability to readily produce elaborate and sophisticated patterns has been made much simpler thanks to these new options that have been opened up for jewelry designers as a result.
Some examples include delicate filigree designs, sculptural pieces with intricate details, and jewelry featuring unique gemstone settings. The possibilities are endless with lost wax 3D printing.
Industrial and Mechanical Metal Parts
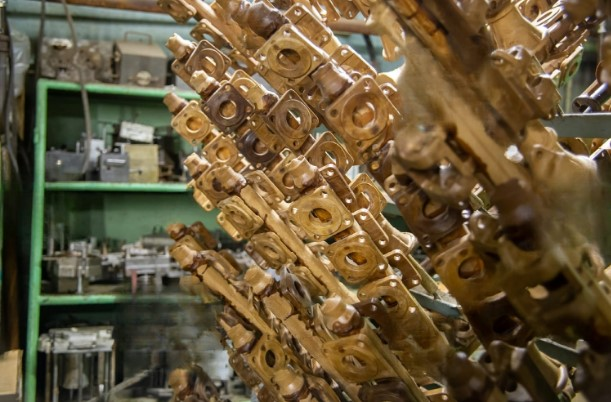
Lost wax 3D printing offers several benefits in producing industrial and mechanical metal parts.
This can result in parts with improved functionality and performance. Lost wax 3D printing also cuts down on the amount of time and effort needed to make parts, resulting in a method that is more efficient and cost-effective.
Lost wax 3D printing has been used to create various industrial and mechanical metal parts, from aerospace components to medical devices. Examples include turbine blades, impellers, gears, and customized orthopedic implants.