Stainless steel casting is revolutionizing the industrial machinery sector with its superior quality and dimensional accuracy. In European industries, stainless steel investment casting, especially SS 316 castings, plays a crucial role, offering precision, corrosion resistance, strength, durability, versatility, and sustainability. Its properties and applications make it highly significant in aerospace, healthcare, automotive, and architectural sectors.
Key Takeaways:
- Stainless steel casting offers precision, corrosion resistance, strength, durability, versatility, and sustainability.
- SS 316 castings are highly significant in aerospace, healthcare, automotive, and architectural sectors.
- Precision casting techniques and innovations contribute to the excellence of stainless steel castings.
- Quality assurance, compliance with industry standards, and reliability are vital in stainless steel casting.
- The integration of CNC technologies with traditional casting methods drives advancements in stainless steel casting.
The Advantages of Stainless Steel Casting
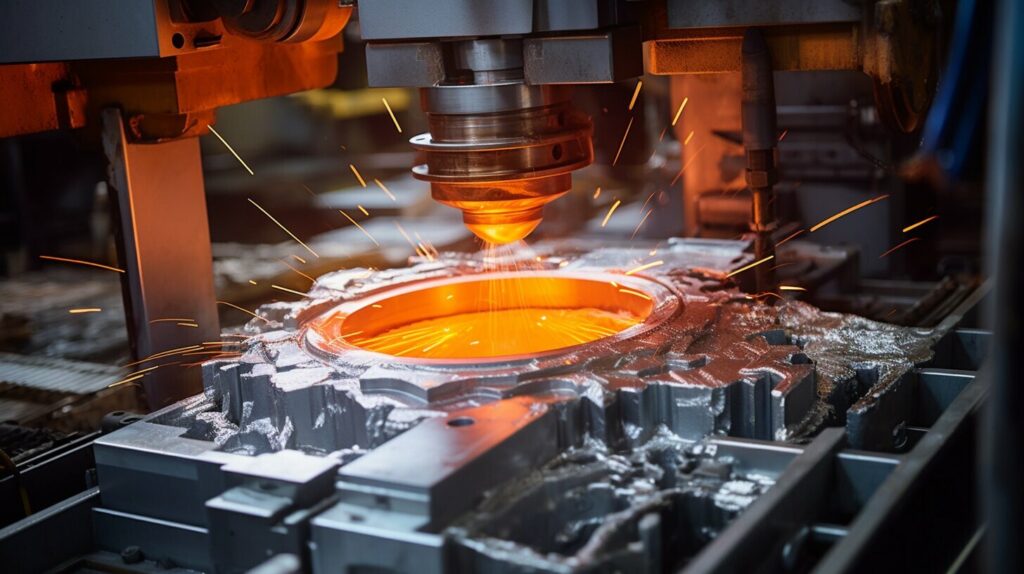
Stainless steel casting offers numerous advantages, including exceptional corrosion resistance, robust mechanical properties, and a flawless surface finish. These qualities make it a preferred choice in various industries, ranging from aerospace and healthcare to automotive and architectural sectors. The corrosion resistance of stainless steel casting ensures that components can withstand harsh environments and maintain their structural integrity over time. This is particularly crucial in industries where exposure to corrosive substances or high temperatures is common.
In addition to corrosion resistance, stainless steel casting exhibits excellent mechanical properties, such as high strength and durability. This makes it suitable for applications that require components to withstand heavy loads or intense mechanical stress. Moreover, stainless steel castings can be engineered to meet specific requirements, allowing for the production of complex shapes and intricate designs with precision.
Another notable advantage of stainless steel casting is the flawless surface finish it offers. The smooth texture and seamless appearance of cast stainless steel components contribute to improved aesthetics and functionality. This is especially important in industries like architecture and automotive, where the visual appeal of the final product is paramount.
Advantages of Stainless Steel Casting |
---|
Exceptional corrosion resistance |
Robust mechanical properties |
Flawless surface finish |
We believe that stainless steel casting is a game-changer in the industrial machinery sector. Its ability to deliver precision, corrosion resistance, and durability has revolutionized manufacturing processes in various industries. The advantages of stainless steel casting, such as exceptional corrosion resistance, robust mechanical properties, and a flawless surface finish, have made it an indispensable choice for engineers and designers. As we continue to explore new techniques and integrate advanced technologies, the future of stainless steel casting looks promising, opening up even greater possibilities for innovation and advancement in the industrial machinery sector.
The Stainless Steel Casting Process
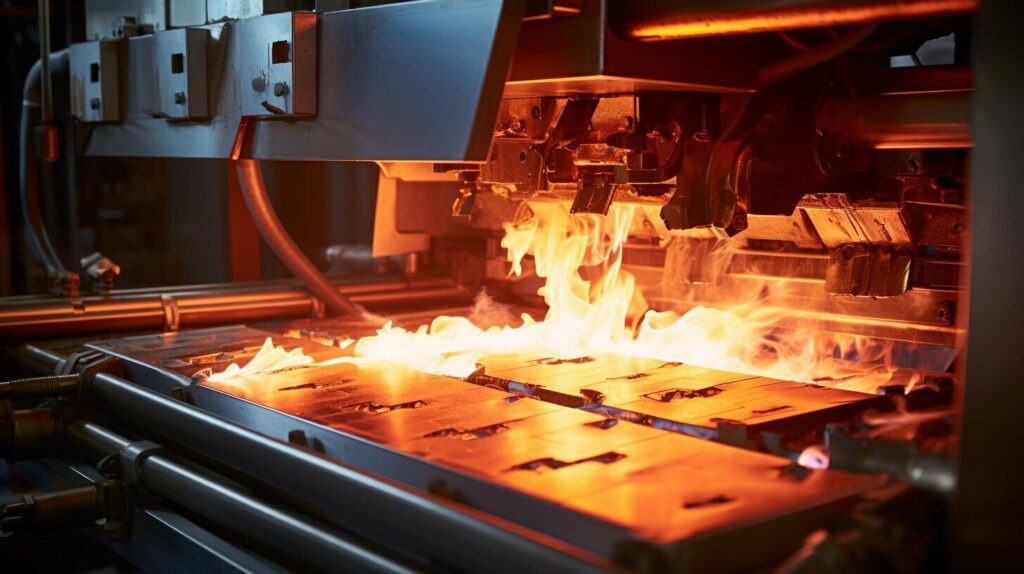
The stainless steel casting process, particularly the investment casting technique, involves the use of ceramic shells and wax patterns to achieve intricate and accurate stainless steel components. This process is widely used in various industries due to its ability to produce parts with excellent dimensional accuracy and surface finish.
Investment casting, also known as lost-wax casting, begins with the creation of a wax pattern that is an exact replica of the desired stainless steel component. This wax pattern is then coated with a ceramic shell, which is created through a series of dipping and drying stages. The ceramic shell is then heated to remove the wax, leaving behind a hollow mold.
Molten stainless steel is poured into the ceramic shell mold, filling the cavity and taking the shape of the wax pattern. After solidification, the ceramic shell is broken away, revealing the stainless steel casting. The casting is then cleaned, finished, and undergoes various post-processing treatments such as heat treatment and surface finishing.
This investment casting process provides numerous benefits, including the ability to create complex geometries with intricate details, tight tolerances, and excellent surface quality. It is also cost-effective for small to medium-sized production runs and offers a wide range of stainless steel alloys to choose from, each with its own unique mechanical properties and corrosion resistance.
Advantages of Stainless Steel Investment Casting: |
---|
1. Intricate and accurate components |
2. Excellent dimensional accuracy and surface finish |
3. Ability to create complex geometries |
4. Cost-effective for small to medium-sized production runs |
5. Wide range of stainless steel alloys available |
The Transformation of Stainless Steel Investment Casting
In recent years, the stainless steel casting process has undergone a transformation with the integration of CNC machining and rapid prototyping technologies. This fusion has resulted in enhanced precision, efficiency, and material utilization in the production of stainless steel components.
- CNC machining allows for the precise shaping and finishing of stainless steel castings, reducing the need for extensive manual labor and improving consistency.
- Rapid prototyping enables the quick production of prototypes, allowing for faster iterations and reduced time-to-market.
- The integration of CAD-CAM systems optimizes pattern design and machining processes, leading to improved accuracy and efficiency.
These advancements in the stainless steel casting process have paved the way for greater innovation and advancement in the industrial machinery sector. With the ability to produce intricate and accurate components, stainless steel casting continues to play a crucial role in driving excellence in European industries.
Stainless Steel Alloys in Casting
Stainless steel casting utilizes a wide range of stainless steel alloys, each offering unique mechanical properties and corrosion resistance. This variety of alloys allows for the customization and optimization of cast components based on specific industry requirements. Let’s explore some of the commonly used stainless steel alloys in the casting process:
- Stainless Steel 316: Known for its excellent corrosion resistance and high strength, SS 316 is widely used in industries such as aerospace, healthcare, automotive, and architecture. Its superior mechanical properties make it suitable for stringent applications that require durability and reliability.
- Stainless Steel 304: This alloy is widely recognized for its versatility and is commonly used in various industries. It offers good corrosion resistance, high-temperature strength, and is easily machinable, making it a popular choice for many casting applications.
- Duplex Stainless Steel: Duplex stainless steel alloys, such as 2205 and 2507, exhibit a combination of high strength and excellent corrosion resistance. These alloys are commonly used in applications where resistance to stress corrosion cracking and pitting is crucial, such as offshore oil and gas exploration and production.
The selection of the appropriate stainless steel alloy depends on factors such as the intended application, environmental conditions, mechanical requirements, and desired surface finish. By carefully choosing the alloy, manufacturers can ensure that cast components meet the specific demands of their industry.
Table: Stainless Steel Alloys Used in Casting
Stainless Steel Alloy | Mechanical Properties | Corrosion Resistance |
---|---|---|
Stainless Steel 316 | High strength, excellent corrosion resistance | Superior resistance to corrosion |
Stainless Steel 304 | Versatile, easily machinable | Good corrosion resistance |
Duplex Stainless Steel | High strength, resistance to stress corrosion cracking | Excellent resistance to pitting |
The use of the appropriate stainless steel alloy in casting ensures that the final components possess the desired mechanical properties and can withstand the harsh operating conditions they may encounter. The corrosion resistance of these alloys contributes to the longevity and reliability of the cast components, making them suitable for various industrial applications.
Precision and Efficiency in Stainless Steel Casting
Stainless steel casting ensures exceptional precision and efficiency by maintaining dimensional accuracy and tight tolerances, utilizing various casting methods. This level of precision is crucial in industries where even the smallest deviation can have significant consequences. With advancements in technology and casting techniques, manufacturers can now achieve intricate designs and complex shapes with utmost precision, meeting the stringent requirements of modern industrial machinery.
The casting methods employed in stainless steel casting play a pivotal role in achieving the desired precision and efficiency. Investment casting, also known as the lost-wax casting method, is widely utilized for its ability to produce detailed and intricate stainless steel components with high dimensional accuracy. By creating wax patterns and encasing them in ceramic shells, manufacturers can achieve tight tolerances and consistent results during the casting process.
Furthermore, other casting methods such as sand casting and centrifugal casting offer their own unique advantages in terms of production efficiency and cost-effectiveness. Sand casting allows for the production of larger stainless steel components while maintaining dimensional accuracy, while centrifugal casting enables the creation of cylindrical and symmetrical parts with exceptional precision.
Table: Casting Methods and Their Advantages
Casting Method | Advantages |
---|---|
Investment Casting | – High dimensional accuracy – Ability to create intricate designs – Consistent results |
Sand Casting | – Suitable for larger components – Cost-effective – Maintains dimensional accuracy |
Centrifugal Casting | – Ideal for cylindrical and symmetrical parts – Excellent precision and repeatability |
By utilizing these different casting methods, manufacturers can achieve the desired precision and efficiency in stainless steel casting. This ensures that the resulting components meet the strict quality standards and functional requirements of industrial machinery, contributing to their reliable and high-performance operation.
Stainless Steel Casting in Various Industries
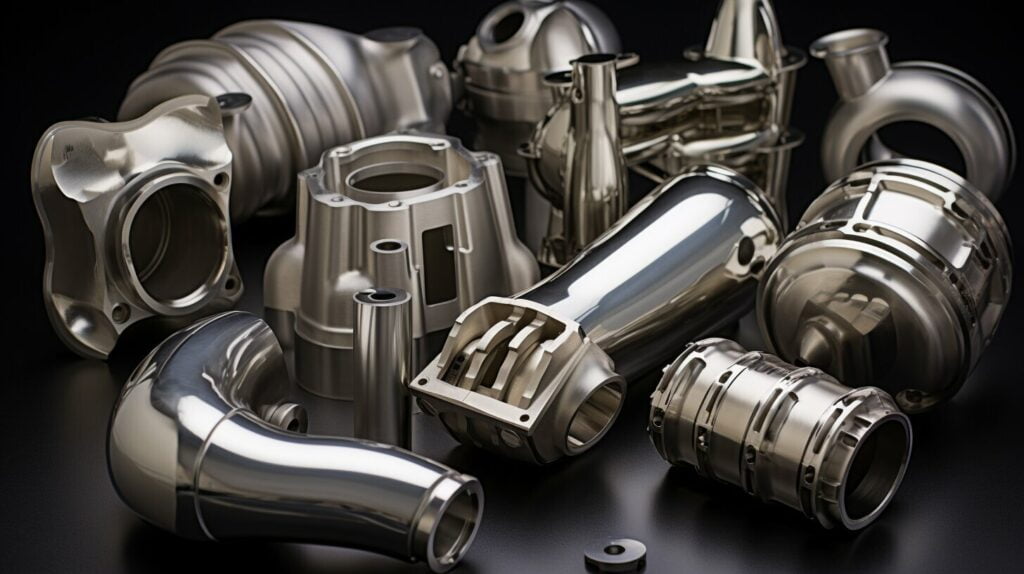
Stainless steel casting finds application in a multitude of industries, empowering the manufacturing process and creating components with intricate designs. From aerospace to healthcare, automotive to architecture, the versatility of stainless steel components enables the production of high-quality, durable, and corrosion-resistant parts that meet the rigorous demands of these sectors.
In the aerospace industry, stainless steel castings play a critical role in the construction of aircraft engines, where precision, strength, and heat resistance are paramount. These components are subjected to extreme conditions and must maintain their performance and integrity. Stainless steel casting ensures dimensional accuracy and the ability to withstand high temperatures, making it an ideal choice for this critical application.
In the healthcare sector, stainless steel castings are utilized in medical devices and equipment. The corrosion resistance and biocompatibility of stainless steel make it suitable for surgical instruments, implants, and diagnostic equipment. These components require a high level of precision to ensure optimal functionality and patient safety.
The automotive industry also benefits from stainless steel casting, where components like engine parts, exhaust systems, and suspension components are produced with intricate designs and precision. The durability and corrosion resistance of stainless steel ensure the longevity and performance of these automotive parts, even in harsh environments.
Industry | Application |
---|---|
Aerospace | Aircraft engines |
Healthcare | Medical devices and equipment |
Automotive | Engine parts, exhaust systems, suspension components |
Architecture | Structural components, decorative elements |
Case Study: Niagara Investment Castings
An exemplary company in the stainless steel casting industry is Niagara Investment Castings. They have developed a reputation for providing comprehensive services to their clients across various industries. With a commitment to quality and collaboration, Niagara Investment Castings has successfully delivered high-quality stainless steel components that meet the stringent requirements of their clients.
By leveraging their expertise and advanced casting techniques, Niagara Investment Castings has demonstrated their ability to produce complex parts with tight tolerances and precise dimensional accuracy. Their attention to detail and adherence to industry standards have earned them the trust of their clients and positioned them as a leader in the stainless steel casting sector.
As stainless steel casting continues to evolve, the future holds even greater possibilities for its application in various industries. Ongoing advancements in CNC machining and rapid prototyping techniques, coupled with the integration of CAD-CAM systems, will further enhance the precision, efficiency, and customization options of stainless steel castings. This will result in improved material efficiency and cost-effectiveness, driving excellence in the manufacturing process and enabling the creation of even more intricate and high-performance components.
Company | Services |
---|---|
Niagara Investment Castings | Comprehensive services, commitment to quality, collaboration with clients |
Quality Assurance in Stainless Steel Casting
Quality assurance plays a pivotal role in stainless steel casting, employing non-destructive testing techniques to ensure dimensional accuracy and identify surface defects and inclusions. By utilizing advanced inspection methods, such as X-ray, ultrasound, and magnetic particle testing, manufacturers can maintain the highest standards of quality and reliability in the production of stainless steel castings.
One of the key aspects of quality assurance is dimensional accuracy. Precise measurements and tight tolerances are crucial in the manufacturing process to ensure that stainless steel components meet the required specifications. Through non-destructive testing, any deviations or variations in the dimensions of the castings can be identified and rectified, guaranteeing that the final products meet the exact requirements of the customers.
In addition to dimensional accuracy, surface defects and inclusions are also carefully examined during the quality assurance process. Surface defects, such as cracks, porosity, or uneven surfaces, can compromise the integrity and functionality of the stainless steel castings. By conducting thorough inspections, manufacturers can detect and address these issues, ensuring that only flawless components are delivered to the customers.
Non-Destructive Testing Techniques | Advantages |
---|---|
X-ray | Effective in detecting internal defects such as porosity or inclusions. |
Ultrasound | Can identify cracks, voids, and other internal flaws. |
Magnetic Particle Testing | Highly sensitive to surface defects like cracks and discontinuities. |
Ensuring Quality and Reliability
By prioritizing quality assurance, stainless steel casting manufacturers can establish a reputation for delivering reliable and high-performing products. The use of non-destructive testing techniques guarantees that the dimensional accuracy is maintained, minimizing the risk of product failure or malfunction. Surface defects and inclusions, which may compromise the structural integrity of the castings, are meticulously identified and eliminated, ensuring that the final components possess the necessary strength and durability.
Furthermore, the implementation of comprehensive quality control processes ensures compliance with industry standards and regulations. By adhering to stringent guidelines, manufacturers can ensure that their stainless steel castings meet the necessary requirements for various applications and industries.
“Quality assurance is not just a step in the production process; it is the foundation of our commitment to excellence and customer satisfaction.”
At our company, we recognize the importance of quality assurance in stainless steel casting. Our commitment to excellence extends beyond the production floor. We actively collaborate with our clients, ensuring that their specific requirements are met and exceeded. Through continuous improvement initiatives and relentless dedication to quality, we strive to deliver stainless steel castings that not only meet the highest industry standards but also drive excellence in European industries.
In conclusion, quality assurance is an essential component of stainless steel casting, ensuring that dimensional accuracy is maintained and surface defects are identified and eliminated. By employing non-destructive testing techniques and adhering to rigorous quality control processes, manufacturers can guarantee the reliability, performance, and longevity of stainless steel castings. This commitment to excellence is what sets industry leaders apart and propels the stainless steel casting industry towards a future of innovation and advancement in the industrial machinery sector.
Dimensional Accuracy | Surface Defects | Reliability |
---|---|---|
Ensures precise measurements and tight tolerances. | Detects and eliminates surface defects. | Guarantees the performance and longevity of castings. |
The Future of Stainless Steel Casting
The future of stainless steel casting lies in the integration of CNC machining, rapid prototyping, and a focus on material efficiency for sustainable and groundbreaking innovations. As technology continues to advance, the manufacturing industry is embracing new methods and techniques to enhance the capabilities of stainless steel casting. CNC machining offers precise and automated machining processes, ensuring dimensional accuracy and consistency in the production of complex stainless steel components. Rapid prototyping, on the other hand, allows for quick and cost-effective production of prototypes, enabling manufacturers to test and refine designs before full-scale production.
One of the key aspects that will shape the future of stainless steel casting is material efficiency. With environmental concerns becoming increasingly important, manufacturers are seeking ways to reduce waste and optimize resource utilization. By utilizing advanced techniques such as CAD-CAM integration, designers and engineers can optimize patterns and machining processes, minimizing material waste and improving overall efficiency. This focus on material efficiency is not only beneficial for the environment but also helps to reduce costs and enhance the sustainability of stainless steel casting processes.
The integration of CNC machining and rapid prototyping with stainless steel casting opens up endless possibilities for innovation and advancement. Manufacturers can create intricate and complex stainless steel components that were once considered challenging or even impossible to produce. This level of precision and customization allows for the design and production of highly specialized equipment and machinery, catering to the unique needs of various industries. From aerospace to automotive, healthcare to architecture, stainless steel casting is set to revolutionize the manufacturing landscape.
Advantages of Integrated Stainless Steel Casting: |
---|
1. Precision and dimensional accuracy in complex component manufacturing. |
2. Cost-effectiveness through reduced material waste and optimized production processes. |
3. Customization and flexibility in design, allowing for the creation of unique components. |
4. Enhanced sustainability through improved material efficiency and reduced environmental impact. |
In conclusion, the future of stainless steel casting looks promising, with CNC machining, rapid prototyping, and a focus on material efficiency driving innovation and excellence in the industrial machinery sector. As technology continues to advance, manufacturers will continue to explore new possibilities and further enhance the capabilities of stainless steel casting. With its exceptional properties and versatility, stainless steel casting will undoubtedly remain an integral part of various industries, contributing to the development of advanced and sustainable manufacturing processes.
Mechanical Properties and Corrosion Resistance
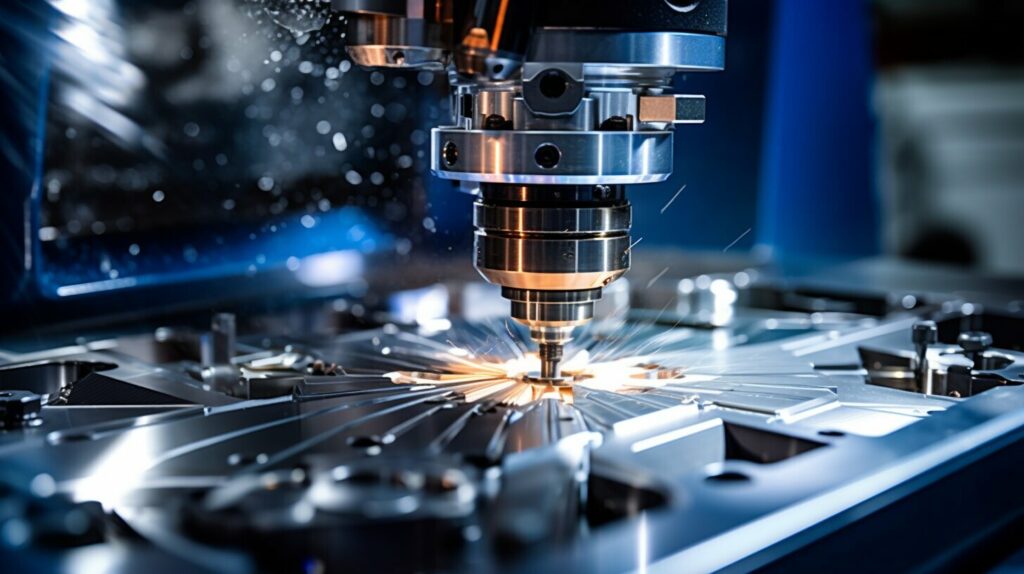
The 304L alloy steel pipes are good for bending and cold forming and have good weldability with or without the addition of filler metal. The austenitic structure also gives these grades excellent toughness, even down to cryogenic temperatures. These grades have good corrosion resistance in a wide range of environments, including those with high temperatures. This high level of corrosion resistance is due to the 18% chromium and 8% nickel content. The 304L alloy is also known for being one of the most ductile and weldable of the austenitic grades of stainless steel.
The 300 series of stainless steels are the most widely used of all stainless steels. The austenitic steels, which are essentially alloys of iron and chromium, contain between 16 and 26 percent chromium. The chromium provides corrosion resistance and the iron imparts strength. As implied by their name, the main difference between the 300 and 400 series of stainless steels is the inclusion of molybdenum in the 400 series. Molybdenum is a alloying element that provides increased corrosion resistance over the 300 series.
The main types of austenitic stainless steels are the 304 and 316 grades. The 304 grade is the most widely used, accounting for more than half of austenitic stainless steel production. It is an economical and versatile choice for a wide range of applications. The main difference between the 304 and 316 grades is the higher molybdenum content of the 316, which provides it with improved corrosion resistance in certain aggressive environments.
There are also duplex stainless steels, which are a combination of austenitic and ferritic stainless steels. These steels have a two-phase microstructure consisting of grains of austenitic stainless steel embedded in a matrix of ferritic stainless steel. This microstructure gives duplex steels a combination of increased strength and corrosion resistance compared to austenitic and ferritic stainless steels.
The most common grades of duplex stainless steels are the 2205 (22% chromium, 5% nickel) and the 2507 (25% chromium, 7% nickel). These steels are resistant to chloride stress corrosion cracking, a type of corrosion that can occur in aggressive environments such as marine applications.
Super austenitic stainless steels are a newer class of stainless steels that contain higher levels of chromium, nickel, and molybdenum. The higher alloy content gives these steels improved corrosion resistance in aggressive environments. These steels are also known for their higher strength and resistance to pitting and crevice corrosion.
The most common grade of super austenitic stainless steel is the 904L (24% chromium, 23% nickel, 4.5% molybdenum). This steel is used in marine applications due to its high levels of corrosion resistance.
The final category of stainless steels is precipitation hardening stainless steels. These steels are a combination of austenitic and martensitic steels. The addition of elements such as chromium, nickel, and copper give these steels increased strength and hardness. The most common grade of precipitation hardening stainless steel is the 17-4PH (17% chromium, 4% nickel). This steel is used in applications that require high strength and corrosion resistance, such as aerospace components.
Stainless steels are a family of iron-based alloys that contain a minimum of 10.5% chromium. Chromium produces a thin layer of oxide on the surface of the steel that acts as a barrier to further corrosion. The addition of other elements, such as nickel, molybdenum, and copper, increases the corrosion resistance of the steel.
There are over 150 grades of stainless steel, each with unique physical and mechanical properties and corrosion resistance profiles. The most common grades of stainless steel are the austenitic 300 series and the duplex 2205.
The 304 grade is the most widely used, accounting for more than half of austenitic stainless steel production. It is an economical and versatile choice for a wide range of applications. The main difference between the 304 and 316 grades is the higher molybdenum content of the 316, which provides it with improved corrosion resistance in certain aggressive environments.
The 2205 duplex stainless steel is the most common grade of duplex stainless steel. It contains 22% chromium, 5% nickel, and 3% molybdenum. This steel is resistant to chloride stress corrosion cracking, a type of corrosion that can occur in aggressive environments such as marine applications.
Super austenitic stainless steels are a newer class of stainless steels that contain higher levels of chromium, nickel, and molybdenum. The higher alloy content gives these steels improved corrosion resistance in aggressive environments. These steels are also known for their higher strength and resistance to pitting and crevice corrosion.
Precipitation hardening stainless steels are a combination of austenitic and martensitic steels. The addition of elements such as chromium, nickel, and copper give these steels increased strength and hardness. The most common grade of precipitation hardening stainless steel is the 17-4PH (17% chromium, 4% nickel). This steel is used in applications that require high strength and corrosion resistance, such as aerospace components.
The different grades of stainless steel are classified by their microstructure. The microstructure is the structure of the steel at the atomic level. The three main types of microstructure in stainless steel are austenitic, ferritic, and martensitic.
Austenitic steels are non-magnetic and have a high degree of corrosion resistance. This microstructure is produced by heat treatment at high temperatures followed by rapid cooling. Austenitic steels make up more than 70% of all stainless steel production.
Ferritic steels are magnetic and have a lower chromium content than austenitic steels. They are typically used in applications where corrosion resistance is not as important as strength or where cost is a factor. Ferritic steels make up about 20% of stainless steel production.
Martensitic steels are magnetic and have a high carbon content. They can be heat treated to increase their strength and hardness. Martensitic steels are used in applications where high strength and wear resistance are required. They make up about 5% of stainless steel production.
The microstructure of the steel affects its physical and mechanical properties as well as its corrosion resistance. The austenitic steels are non-magnetic, have good ductility and weldability, and excellent corrosion resistance. The ferritic steels are magnetic, have good ductility, but are not as weldable as austenitic steels. They have good corrosion resistance in some environments but not others. The martensitic steels are magnetic, have good wear resistance, but are not as weldable as austenitic steels. Their corrosion resistance is also variable depending on the environment.
The main factors that affect the corrosion resistance of stainless steel are chromium content, molybdenum content, and microstructure.
The chromium content is the main factor that determines the ability of the steel to resist rusting. The higher the chromium content, the better the corrosion resistance. The molybdenum content increases the resistance to pitting and crevice corrosion. The microstructure affects the overall corrosion resistance of the steel. Austenitic steels have the best corrosion resistance due to their high chromium and molybdenum content and their non-magnetic microstructure.
Stainless steel is an alloy that contains at least 10.5% chromium. The chromium forms a thin oxide layer on the surface of the steel that acts as a barrier to further corrosion. The addition of other elements such as nickel, molybdenum, and copper increases the corrosion resistance of the steel.
Stainless steel can be divided into five main families: austenitic, ferritic, martensitic, precipitation hardening, and duplex.
The austenitic family contains the most common grades of stainless steel, such as 304 and 316. These grades have good weldability and formability but are not as strong as martensitic or ferritic grades. The main difference between 304 and 316 is the higher molybdenum content of 316, which gives it better corrosion resistance in aggressive environments.
The ferritic family contains grades such as 430 and 434. These grades are less weldable than austenitic grades but have better ductility. They are typically used in applications where cost is a factor or where weldability is not as important as other properties such as strength or corrosion resistance.
The martensitic family contains grades such as 410 and 420. These grades can be heat treated to increase their strength and hardness but are not as weldable as austenitic grades. They are often used in applications where high strength and wear resistance are required such as knives and surgical instruments.
The precipitation hardening family contains grades such as 17-4PH and 15-5PH. These grades are a combination of austenitic and martensitic steels that can be heat treated to increase their strength and hardness. They are often used in aerospace applications where high strength and corrosion resistance are required.
The duplex family contains grades such as 2205 and 2507. These grades contain a mix of austenitic and fer
Collaboration for Success
Collaboration is at the heart of Niagara Investment Castings’ approach. They work closely with clients to understand their requirements and develop customized solutions that meet their specific needs. Their team of experts collaborates throughout the entire casting process, ensuring effective communication and seamless integration of ideas. This collaborative approach allows for efficient problem-solving, quicker turnaround times, and ultimately, the delivery of superior stainless steel castings.
Achieving Excellence in Stainless Steel Casting
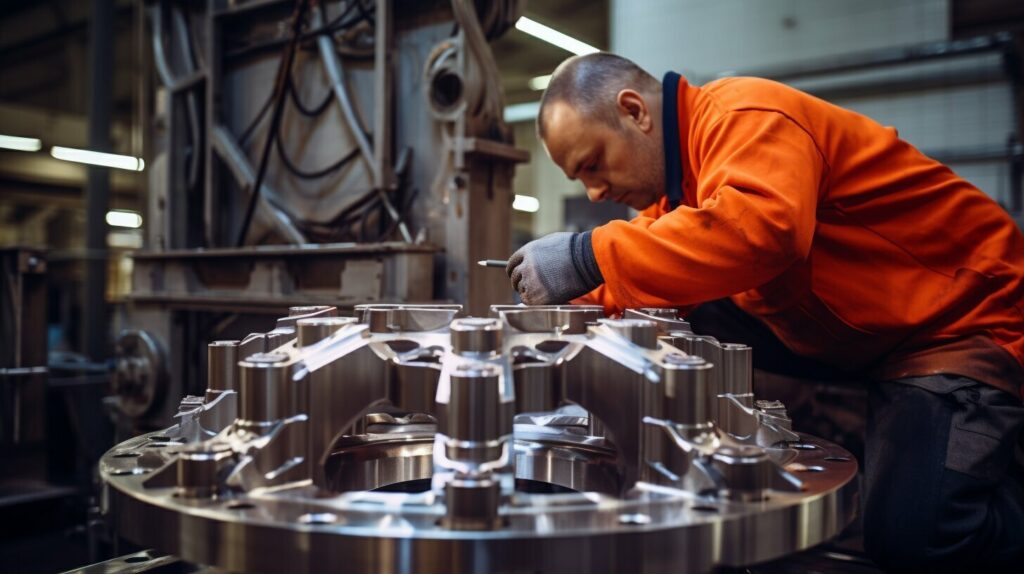
Niagara Investment Castings is dedicated to achieving excellence in stainless steel casting. By constantly staying updated with the latest advancements in technology and techniques, they are able to offer innovative solutions to their clients. Their state-of-the-art facilities and skilled workforce enable them to produce complex and intricately detailed stainless steel components with precision and accuracy.
Their commitment to sustainability is another aspect that sets them apart. Niagara Investment Castings follows environmentally friendly practices throughout their operations, ensuring minimal waste generation and efficient use of resources. By prioritizing sustainability, they contribute to a greener future while delivering exceptional stainless steel castings to their clients.
Key Services: | Design and pattern making | Casting | Finishing and assembly |
---|---|---|---|
Advantages: | Comprehensive range of services | Unwavering commitment to quality | Successful collaboration with clients |
Conclusion
In conclusion, stainless steel casting plays a crucial role in industrial machinery, offering precision, corrosion resistance, strength, durability, versatility, and sustainability, while paving the way for even greater possibilities in the future. The use of stainless steel alloys, such as SS 316 castings, has proven to be highly significant in various sectors, including aerospace, healthcare, automotive, and architecture. Its excellent mechanical properties and resistance to corrosion make it an ideal choice for manufacturing processes.
Throughout this guide, we have explored the advantages of stainless steel casting, including its dimensional accuracy, tight tolerances, and superior surface finish. We have delved into the stainless steel casting process, focusing on the investment casting technique, which utilizes ceramic shells and wax patterns to create precise components. Additionally, we have discussed the different types of stainless steel alloys used in casting, highlighting their specific mechanical properties and corrosion resistance.
The importance of precision and efficiency in stainless steel casting cannot be overstated. Achieving dimensional accuracy and tight tolerances is essential in the manufacturing process, and various casting methods contribute to these qualities. Furthermore, stainless steel casting is widely embraced across various industries due to its ability to produce components with intricate designs and high strength.
Quality assurance is paramount in stainless steel casting, and non-destructive testing techniques play a vital role in ensuring dimensional accuracy, detecting surface defects, and identifying any inclusions. By prioritizing quality, stainless steel casting manufacturers can deliver reliable and high-performing components to their clients.
Looking to the future, stainless steel casting holds even greater promise. The integration of CNC machining, rapid prototyping, and material efficiency will continue to drive innovation in the industry. Additionally, the selection of the right stainless steel alloy, tailoring material properties, and the integration of CAD-CAM technology will optimize patterns and machining processes, further enhancing the capabilities of stainless steel casting.
One successful case study in the stainless steel casting industry is Niagara Investment Castings, known for its comprehensive services, commitment to quality, and successful collaboration with clients. Their expertise and dedication have contributed to the advancement of stainless steel casting and its widespread use across industries.
In conclusion, stainless steel casting is not only a fundamental component in industrial machinery, but it also offers numerous advantages that contribute to the excellence of manufacturing processes. With its precision, corrosion resistance, strength, durability, versatility, and sustainability, stainless steel casting has a bright future ahead, driving innovation and advancement in the industrial machinery sector.
FAQ
What are the advantages of stainless steel casting?
Stainless steel casting offers corrosion resistance, excellent mechanical properties, and a superior surface finish. These properties make it an ideal choice for various industries.
How does the stainless steel casting process work?
The stainless steel casting process, specifically the investment casting technique, involves creating precise components using ceramic shells and wax patterns.
Which stainless steel alloys are used in casting?
Different types of stainless steel alloys are used in casting, each with specific mechanical properties and corrosion resistance. This versatility allows for customized solutions.
How does stainless steel casting achieve precision and efficiency?
Stainless steel casting achieves precision and efficiency through dimensional accuracy and tight tolerances. Various casting methods contribute to these qualities.
In which industries is stainless steel casting used?
Stainless steel casting is widely used in various industries, particularly in industrial machinery. It plays a crucial role in the manufacturing process and the creation of components with intricate designs.
How is quality assurance ensured in stainless steel casting?
Quality assurance in stainless steel casting is ensured through non-destructive testing techniques, which help detect surface defects, inclusions, and ensure dimensional accuracy.
What does the future hold for stainless steel casting?
The future of stainless steel casting involves the integration of CNC machining, rapid prototyping, and a focus on material efficiency. This promises even greater innovation and advancement in the industry.
Can you provide a case study of a reputable stainless steel casting company?
KT-Foundry Castings is a reputable company in the stainless steel casting industry. They are known for their comprehensive services, commitment to quality, and successful collaboration with clients.