Cast aluminum is a widely used material in manufacturing various products, including automotive parts, household items, and construction materials. Cast aluminum is produced by melting aluminum and pouring it into a mold to create a desired shape.
The chemical composition makes it a highly durable and corrosion-resistant material. Its contact with air forms a thin aluminum oxide layer that adds an extra protection from further corrosion.
Corrosion can take many forms, including pitting, cracking, and flaking, and can reduce the aluminum’s thickness, unlike rust.
Factors That Contribute to Aluminum Corrosion
Aluminum corrosion can be accelerated in areas with high humidity or wet environments, such as coastal areas or where products are exposed to rain or snow.
The process of aluminum oxidation can be accelerated by exposure to moisture or acidic or alkaline environments. It may come in the form of pitting or scaling, weakening the aluminum and compromising its durability.
Its manufacturing process can also contribute to corrosion. Improper cleaning, handling, or storage can lead to the formation of contaminants on the surface of the aluminum, which can accelerate corrosion.
Salt is highly corrosive and can quickly degrade the protective oxide layer on the aluminum. Products used in marine or coastal environments corrode faster compared to regular environments.
Types of Corrosion That Affect Cast Aluminum
The most common type of corrosion that affects aluminum is uniform corrosion. Corroded aluminum covers the metal caused by exposure to moisture or salt.
A galvanic corrosion happens on two different metals. In the case of aluminum, it can undergo galvanic corrosion when it comes into contact with copper or steel, which is more reactive than aluminum.
Pitting corrosion comes from the metal’s exposure to chlorides or other corrosive substances. It comes in the form of small pits or holes in the aluminum’s surface. This type weakens the structural integrity of the metal, which leads to rapid material loss.
Intergranular corrosion is another type of corrosion that can affect aluminum. This type of corrosion occurs when the aluminum corrodes along its grain boundaries, which can cause the metal to become brittle and prone to cracking. Intergranular corrosion can be caused by exposure to high temperatures, like in cast aluminum patio furniture.
Effects of Aluminum Rust Stains on Cast Aluminum
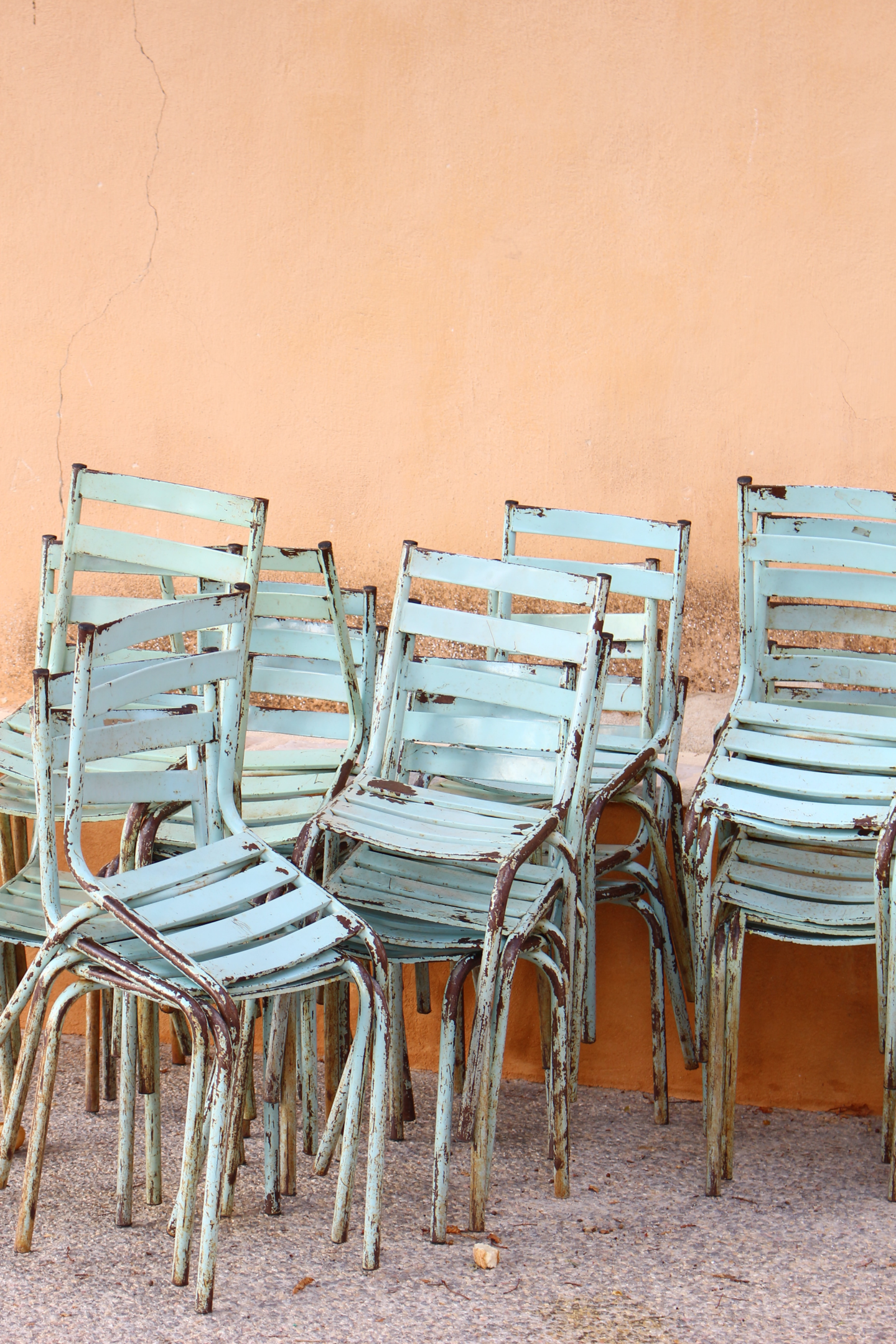
Appearance
Aluminum is a widely used material in various industries due to its many desirable properties, mainly when used as outdoor furniture. However, even aluminum is susceptible to corrosion over time, which can lead to rusting on the surface of the metal furniture. These stains not only detract from the appearance of the outdoor decor but can also indicate deeper corrosion problems.
Rusting can make the aluminum look old, worn, and dirty, which can be especially problematic for cast aluminum patio furniture meant to have a sleek and modern appearance.
Structural Integrity
In addition to their negative impact on appearance, aluminum rust stains can also indicate deeper corrosion problems that can compromise the structural integrity of the metal. When corrosion happens, it can weaken the aluminum, which can be dangerous in specific applications.
For example, if an aluminum structure supporting heavy loads begins to rust, it could eventually collapse, causing damage and injury.
Longevity
Rust can significantly impact aluminum’s longevity, affecting its structural integrity and overall performance. For example, aluminum is a fantastic choice for structures such as bridges, building facades, and roofing systems in the construction industry. However, rust can compromise the structural integrity of these structures, making them unsafe and potentially causing them to fail.
Preventing Aluminum Rust
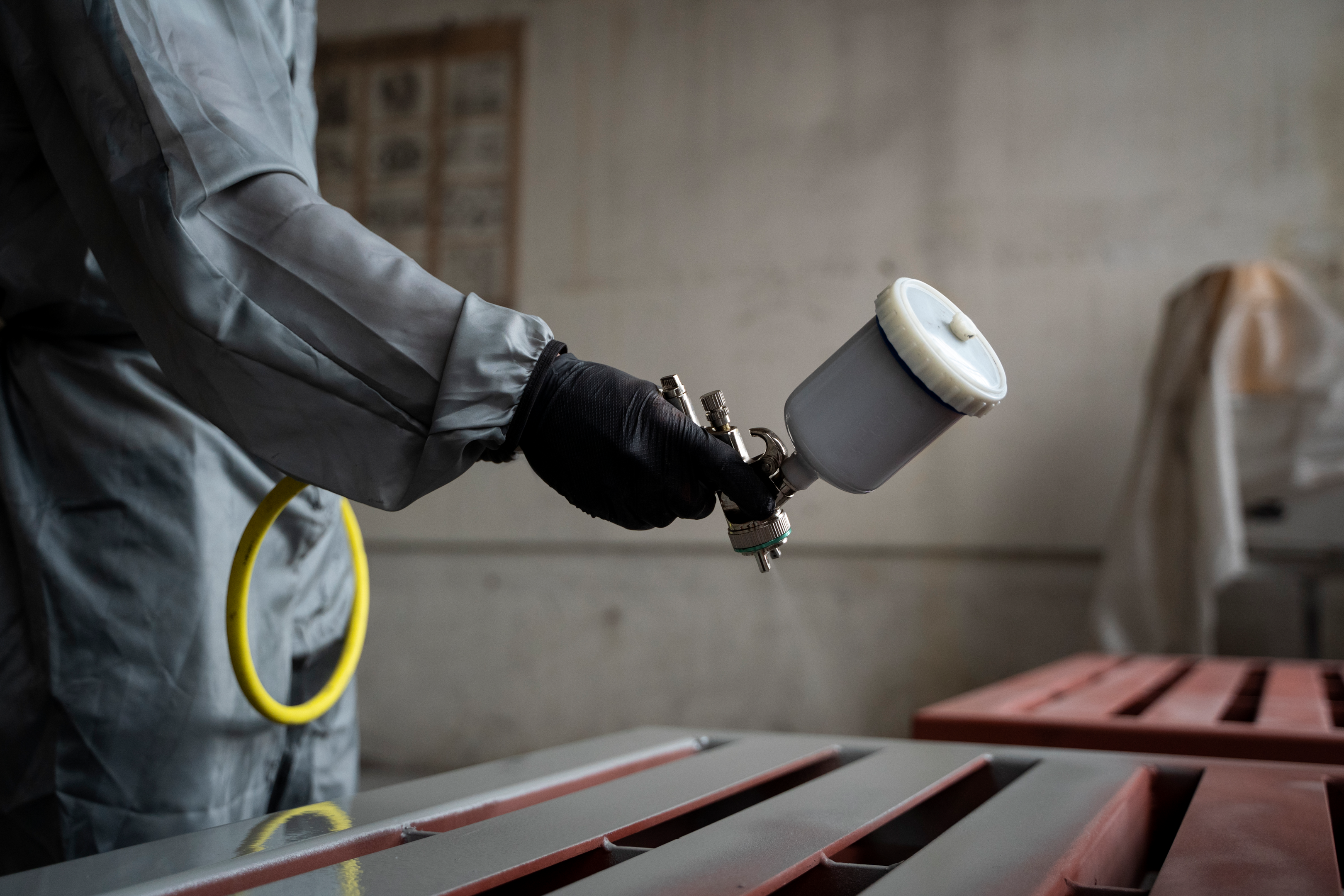
Aluminum Surface Treatment
Anodizing is an electrochemical process that adds a layer of protection on aluminum. The process involves immersing the product in an electrolyte solution and passing a current through it, which creates an oxide layer tightly bonded to the surface of the metal.
Protective Paint and Powder Coating Process
Powder coating is a dry powder-based coating that is applied electrostatically to the surface of the aluminum. The powder is then cured by heating, which causes it to melt and form a hard, durable coating on the surface of the metal. Powder coating is highly resistant to corrosion, abrasion, and fading, making it an excellent weather-resistant option for outdoor applications.
Painting is a commonly used method of protecting the aluminum from corrosion. A high-quality paint can be a barrier between the aluminum surface and effects of the environment.
Cleaning and Maintenance
Wipe down the aluminum with a damp cloth to remove dirt and grime. Chemicals like bleach or acidic cleaners can affect and eventually damage the oxide layer on the aluminum.
The aluminum should be wiped to dry, especially if used for food services. Moisture easily accumulates on its surface and lead to corrosion.