Casting is a process that has been in use for many years. Cast steel and cast iron are two of the most common materials used in the casting process. Both metals offer good casting properties and potential performance benefits, but which material is best for a particular casting application?
In this article, we’ll explore the differences between cast iron and cast steel and which material has better performance.
What You Need to Know About Cast Steel
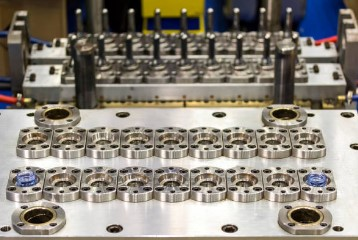
Cast steel is a type of alloy steel that has been treated by a process known as casting. The cast steel process allows for a variety of different alloys to be used to create the desired result. The alloy chosen will depend on the desired strength, corrosion resistance, and other characteristics.
Its molds can be made to achieve a wide range of shapes, sizes, and strengths. This makes it possible to create components to exact specifications.
One of the most significant advantages of cast steel is its strength and durability. This type of steel is resistant to corrosion, mechanical wear, and high temperature. Additionally, it has a high tensile strength and can maintain its strength even after being exposed to extreme temperatures.
Its own advantages make it ideal for components that need to operate in harsh environments.
Manufacturing Process of Cast Steel
The first step of the process is melting. Raw steel is melted in an electric arc furnace or a ladle furnace, depending on the type of steel being used. The molten steel is then poured into a mold.
Once the steel has cooled, the metal is ready to be further processed. This process may involve machining, grinding, or polishing the cast steel to achieve the desired look and feel. In some cases, it may also be treated with a chemical composition to improve its corrosion resistance, hardness, or other characteristics.
It is also important to note that the process can be adjusted and adapted depending on the desired final product.
Low Alloy Steel
Low alloy steel is a type of metal alloy that includes small amounts of other elements, typically less than 5%. It is made by combining various metals.
These metals are typically low in carbon content, with the majority of them being iron. Other metals that may be used include chromium, manganese, nickel, and molybdenum.
High Alloy Steel
The components of high alloy steels can be classified according to the type of alloying elements present. The most common alloying elements are chromium, molybdenum, nickel, manganese, and vanadium.
These steels have higher levels of other alloying elements, which give the steel its superior properties compared to ordinary steels. High alloy steels are an important type of steel that can be used in a variety of applications due to their superior properties.
Treatments for Steel Castings
There are several treatments that can be used to protect steel castings. The most common outer layer treatments include painting, galvanizing, and powder coating.
Other treatments are designed to improve the strength and durability of steel castings. Heat treatment is one such treatment that is used to increase the strength and provide high hardness of the steel. This process involves heating the steel to a high temperature and then cooling it quickly, which allows the steel to develop a stronger, more durable structure.
Quenching is another treatment that is used to improve the steel’s strength and hardness. This process involves heating the steel and then cooling it slowly, which also promotes a stronger and more durable structure.
Why You Should Choose Cast Steel Rather Than Cast Iron
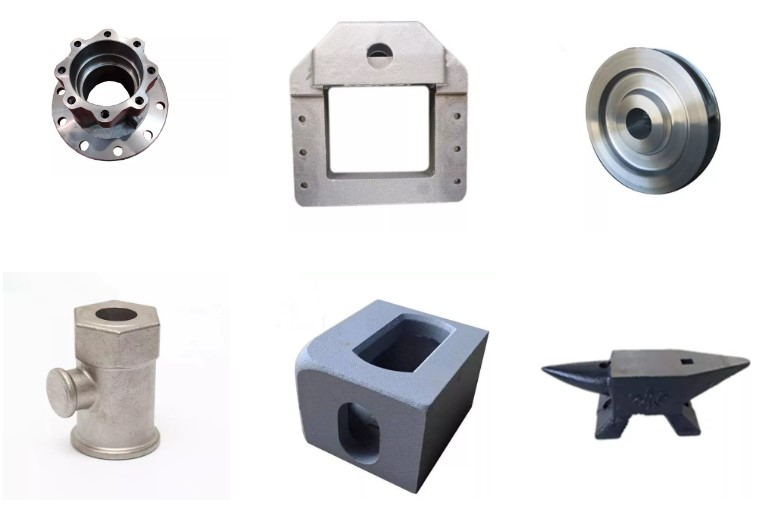
Cast steel is extremely durable, and it can withstand extreme temperatures and a variety of weather conditions.
It is incredibly strong, and it is often used to make products that need to withstand heavy loads and impact resistance. It also features good wear resistance for items that will be used frequently.
Cast steel is extremely versatile, and it can be used to make a variety of products–from metal parts to medical instruments.
What You Need to Know About Cast Iron
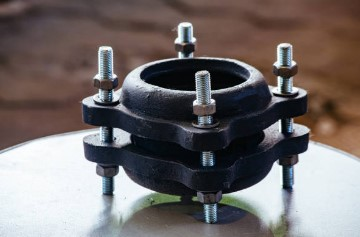
Carbon steel or cast iron generally contains iron and carbon. Iron is the main component, making up 98% of the alloy, while the carbon content makes up the remaining 2%.
In order to create a strong and durable material, the ratio of iron to carbon must be carefully balanced during the production process. If there is too much carbon, the casting will be brittle and won’t be able to withstand extreme temperatures. On the other hand, if there is too little carbon content, the iron casting can be a brittle material.
The other components of cast iron include manganese, phosphorus, sulfur, and silicon. Manganese helps to improve the strength and hardness of cast iron, while phosphorus and sulfur help to improve the steel’s machinability. Silicon helps to reduce the amount of carbon in the casting, which improves its weldability.
Manufacturing Process of Cast Iron
The process of creating cast iron begins with the selection of suitable iron ore and other raw materials. These are melted down in a furnace and the molten iron is poured into a mold. The mold is usually made of sand, clay, or ceramic.
The cast iron then solidifies and takes the shape of the mold. The liquid metal may be further treated by adding various alloys to it. The alloys can be used to create different types of cast iron, such as grey iron, ductile iron, white iron, or malleable iron.
Grey Cast Iron
Grey cast iron is a type of cast iron that is made up of carbon content and graphite flakes surrounded by a metallic matrix. Aside from graphite, gray iron may also include other elements such as silicon, manganese, and phosphorus. These elements are added in order to improve the strength and hardness of the grey cast iron.
Its graphite content is one of the main factors that determine the properties of gray iron. Its other components also play an important role in its overall characteristics.
Ductile Iron
Ductile iron, also known as ductile cast iron, nodular cast iron, spheroidal graphite cast iron, or SG iron, is a type of cast iron with high strength, ductility, and shock resistance.
The carbon content in ductile iron is in the form of small spheroidal graphite particles, which give the metal its strength and ductility. This makes it much more resistant to cracking and breaking than traditional cast iron.
Ductile iron is produced using a process known as “spheroidizing,” which involves melting the metal, adding graphite to create the spheroidal particles, and then cooling it quickly.
White Cast Iron
White cast iron is a type of cast iron that is produced by adding chromium, nickel, and molybdenum to the standard cast iron. The addition of these elements to the cast iron creates a material that is harder and more wear-resistance cast iron.
During the cooling process, the additional elements combine with the iron to create a white iron.
White cast iron is more expensive than other types of cast iron due to its high alloy content. It is also more difficult to machine and shape than other types of cast iron. However, its superior wear resistance makes it a popular choice for many applications.
Malleable Cast Iron
Malleable cast iron is created by annealing cast iron. Like the other types, the malleable iron is added with other elements to increase its mechanical properties. The carbon and silicon give it malleability and better corrosion resistance. The carbon content ranges from 2.5-3.5%, while the silicon content ranges from 1.5-3%.
Manganese also helps to reduce the brittleness of malleable iron and improves its ability to withstand extreme temperatures.
Applications of Cast Iron
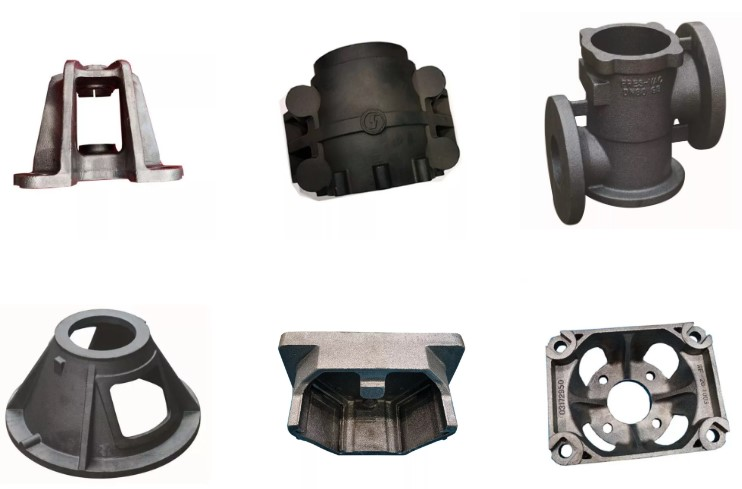
Cast iron is the material of choice for many types of cookware, such as oil pan, skillets, Dutch ovens, and griddles. This is due to its ability to evenly distribute heat, as well as its durability and heat resistance.
It is also used to make components for engines, such as pistons, motor blocks, and cylinder blocks. Its impact resistance and compressive strength is also popular choice for many types of machine parts, such as gears, pulleys, and cams.
Why You Should Choose Cast Iron Rather Than Cast Steel
When used as cookware, cast iron is great for retaining heat. This is because iron is a great conductor of heat. This is great for slow cooking and making sure that your food is cooked through evenly.
It is also one of the most affordable materials, making it great for budget-conscious projects. It is also easy to find and relatively easy to work with, so you won’t have to spend a lot of money on specialized tools and equipment.
Cast iron is also very strong, and has a high compressive strength, making it ideal for high-load-bearing applications.
Comparison of Cast Steel vs Cast Iron
Cast iron and steel both have good physical and mechanical properties. However, to know which is the ideal metal for your project, you need to consider the difference between cast iron and cast steel.
Mechanical Properties of Cast iron and Steel
When comparing the two materials, the mechanical properties of cast iron and cast steel vary significantly. Cast iron has higher tensile strength but is more brittle than cast steel. It also has a low melting point and is more easily cast into complex shapes.
On the other hand, cast steel has higher tensile strength and hardness, as well as a higher melting point and wear resistance.
Cost
When it comes to cost, cast iron generally has lower material costs than cast steel. This is because iron is more abundant in nature than steel, making it easier and cheaper to produce.
However, in terms of strength and durability, cast steel is superior to cast iron. Cast steel is much stronger and more resistant to wear and tear. This means you can expect longer use in cast steel.
Identification
You can identify cast iron apart from cast steel by using an abrasive wheel. The spark test when grinding can be a great indicator of the material’s composition.
Cast iron sparks will be short and fluttery, while those from cast steel will be longer, brighter, and more uniform. The sparks from cast iron are also often more orange in color compared to the white sparks of cast steel.
Another way to identify cast iron and steel is by chemical analysis. Cast iron has a lower carbon content than cast steel and generally appears darker in color. It is slightly more brittle and can contain flakes of graphite that can be seen with the naked eye.