The shift towards electric vehicles in the automotive industry is creating new opportunities for aluminum die casting. This innovation in car manufacturing methods, coupled with a change in materials used, is driving the demand for aluminum die castings in the automotive sector. Despite the current chip shortage, the automotive industry is showing significant interest in die casting solutions, which is encouraging for the industry as a whole. Aluminum die castings are particularly beneficial for bodywork, as they can replace multiple steel components, reduce assembly processes, and decrease factory footprint.
Key Takeaways:
- The shift towards electric vehicles is fueling the demand for aluminum die castings in the automotive industry.
- Aluminum die castings offer numerous benefits, including component consolidation and improved production efficiency.
- Collaboration between die casting companies and automotive manufacturers is crucial for success in the industry.
- Digitalization is playing a key role in optimizing production processes and reducing environmental impact.
- The global aluminum die casting market is projected to experience substantial growth in the coming years.
Aluminum Die Casting in the Automotive Sector
The automotive sector plays a crucial role in driving innovation and growth in the aluminum die casting industry. With the increasing demand for larger body parts, such as rear or front underbodies, aluminum die castings have emerged as a viable alternative to traditional steel components in the automotive sector. This shift towards larger aluminum castings offers several advantages, including reduced assembly processes, decreased reliance on robots, and optimized utilization of factory space. Collaborating with the automotive industry is essential for die casting companies to provide comprehensive solutions and support for integrated manufacturing processes.
In the automotive sector, aluminum die casting projects and concept studies have witnessed a surge in demand. As automotive manufacturers explore the potential of producing large aluminum castings, they often require new layouts, different robots, and revised part handling processes in foundries. Close collaboration between die casting companies and automotive manufacturers is therefore crucial in delivering customized solutions and providing operator training. By offering support in process optimization, mold design, and production improvement, die casting companies can help the automotive sector successfully adopt aluminum die castings.
Digitization is another key driver of aluminum die casting in the automotive sector. By embracing digital technologies, foundries can enhance efficiency, reduce waste, and operate round the clock. Digitization enables greater connectivity and automation, leading to significant cost savings and more sustainable production practices. Additionally, the focus on environmental impact has prompted the automotive sector to prioritize the use of recycled or primary aluminum extracted with renewable energy, making aluminum die castings carbon neutral and aligned with sustainability goals.
Table: Benefits of Aluminum Die Casting in the Automotive Sector
Benefits | Description |
---|---|
Lightweight Design | Aluminum die castings provide lightweight solutions, contributing to fuel efficiency and reducing emissions in the automotive sector. |
Complex Shapes | Aluminum die castings can be molded into intricate and complex shapes, allowing for the production of highly functional automotive components. |
Cost Effectiveness | Die casting offers cost advantages through reduced material usage, simplified assembly processes, and decreased factory footprint. |
Enhanced Performance | Aluminum die castings offer excellent mechanical properties, including high strength, corrosion resistance, and thermal conductivity, enhancing overall performance in automotive applications. |
As the automotive industry continues to embrace aluminum die casting, the demand for lightweight and high-performance components is expected to grow. The collaboration between die casting companies and automotive manufacturers, along with the adoption of digital technologies, will drive the evolution and success of aluminum die casting in the automotive sector.
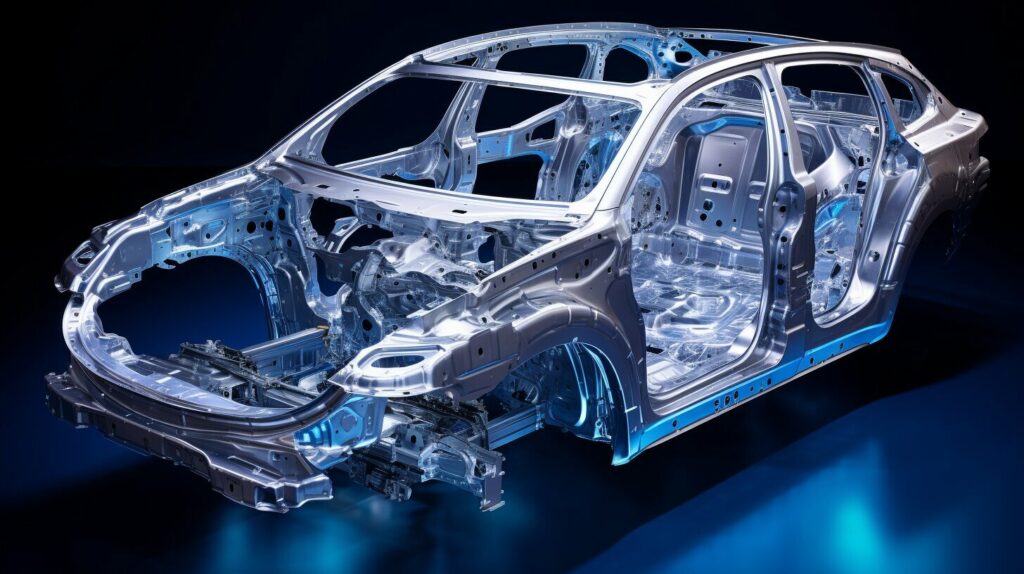
Surge in Aluminum Die Casting Projects
The automotive sector is experiencing a surge in requests for aluminum die casting projects and concept studies. As the industry explores the potential of producing large aluminum castings, there is a need for new layouts, different robots, and revised part handling processes in foundries. Close collaboration between die casting companies and automotive manufacturers is crucial to deliver customized solutions and provide operator training.
Automotive manufacturers are increasingly interested in aluminum die castings due to their numerous benefits. These castings can replace multiple steel components, reducing assembly processes and decreasing the factory footprint. Additionally, aluminum die castings are particularly beneficial for bodywork, making them a preferred choice in the automotive sector.
Die casting companies play a vital role in supporting the automotive sector’s adoption of aluminum die castings. By offering expertise in process optimization, mold design, and production improvement, these companies can help manufacturers successfully integrate aluminum castings into their manufacturing processes. Collaborative efforts between die casting companies and automotive manufacturers are essential for delivering customized solutions that meet the specific requirements of the automotive industry.
Benefits of Aluminum Die Castings in the Automotive Sector
Aluminum die castings offer several advantages that make them increasingly popular in the automotive sector. These benefits include:
- Lightweight: Aluminum castings are significantly lighter than steel components, contributing to improved fuel efficiency and reduced emissions in vehicles.
- Strength and Durability: Despite their lightweight nature, aluminum castings offer excellent strength and durability, ensuring the integrity and safety of automotive components.
- Design Flexibility: Aluminum die castings can be molded into complex shapes, allowing for innovative designs and improved functionality in automotive parts.
- Heat Dissipation: Aluminum has excellent thermal properties, making it an ideal choice for components that require efficient heat dissipation, such as engine parts and heat exchangers.
- Corrosion Resistance: Aluminum castings have inherent corrosion resistance, prolonging the lifespan of automotive components and reducing maintenance costs.
Benefits of Aluminum Die Castings in the Automotive Sector | |
---|---|
Lightweight | Improved fuel efficiency and reduced emissions |
Strength and Durability | Ensures the integrity and safety of automotive components |
Design Flexibility | Allows for innovative designs and improved functionality in automotive parts |
Heat Dissipation | Efficient heat dissipation in engine parts and heat exchangers |
Corrosion Resistance | Prolongs the lifespan of automotive components and reduces maintenance costs |
The surge in aluminum die casting projects in the automotive sector highlights the industry’s recognition of the benefits and potential of this manufacturing method. As automotive manufacturers continue to explore the use of aluminum castings, close collaboration with die casting companies will be crucial for successful implementation and customization of solutions. By harnessing the advantages of aluminum die castings, the automotive sector can drive innovation, improve performance, and meet the demands of an evolving market.
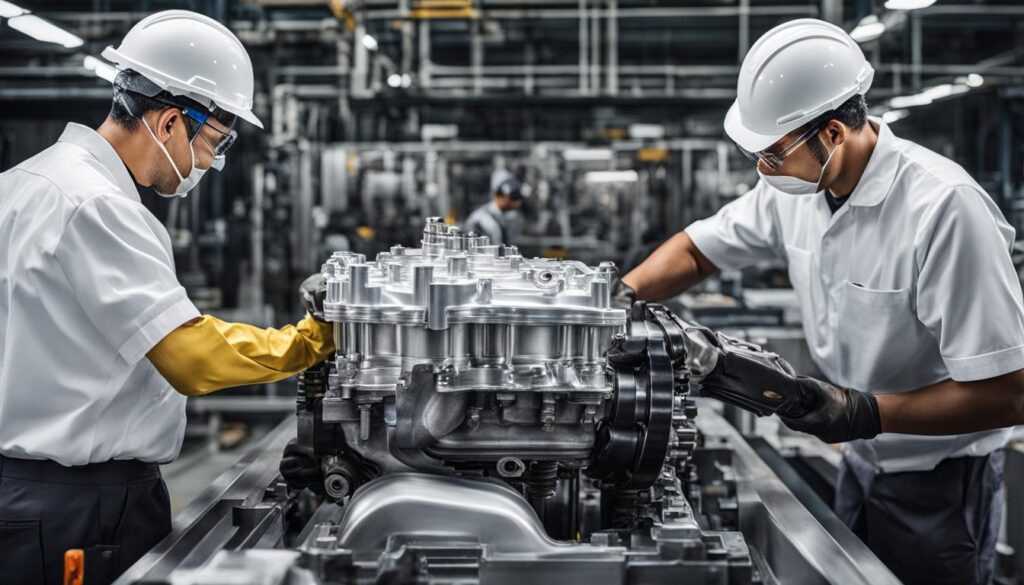
Digitization Driving Aluminum Die Casting in the Automotive Sector
The automotive sector is embracing digitization to drive efficiency and sustainability in aluminum die casting. By leveraging digital technologies, foundries can optimize their operations, reduce waste, and operate round-the-clock. This shift towards digitization is enabling greater connectivity and automation, resulting in significant cost savings and more sustainable production practices.
Digitalization also plays a pivotal role in enhancing the environmental impact of aluminum die castings in the automotive sector. The industry is focused on using recycled or primary aluminum extracted with renewable energy, making the castings carbon neutral. This commitment to sustainability aligns with the broader goals of reducing emissions and promoting eco-friendly manufacturing processes.
In addition to environmental benefits, digitalization enables foundries to enhance their overall efficiency. By streamlining processes and reducing cycle time, manufacturers can meet the growing demand for aluminum die castings in the automotive sector. Furthermore, digitization opens up opportunities for real-time monitoring, predictive maintenance, and data-driven decision-making, leading to improved quality control and customer satisfaction.
Digital Transformation in Automotive Die Casting: Key Aspects
- Implementation of Industrial Internet of Things (IIoT) technologies for enhanced connectivity and data exchange.
- Adoption of advanced simulation and virtual prototyping tools for improved design and process optimization.
- Integration of artificial intelligence (AI) and machine learning (ML) algorithms to enable predictive analytics and production optimization.
- Utilization of cloud computing for seamless data management, collaboration, and remote monitoring.
By embracing digitization, the automotive sector is revolutionizing the aluminum die casting industry, paving the way for more efficient, sustainable, and technologically advanced manufacturing processes. As the industry continues to evolve, collaboration between die casting companies, automotive manufacturers, and technology providers will be crucial in driving innovation and meeting the evolving demands of the market.
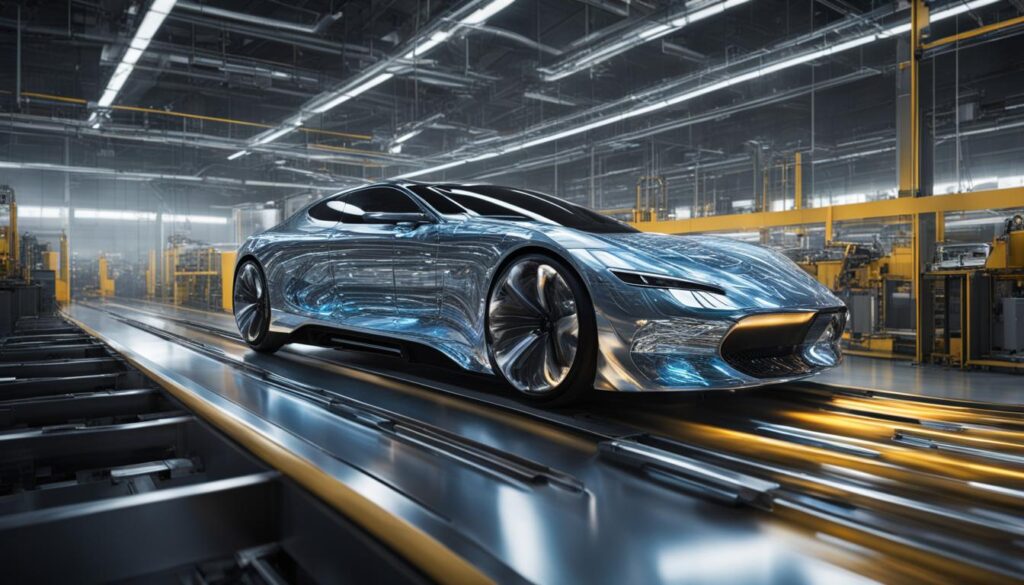
Growth Opportunities in the Aluminum Die Casting Market
The global aluminum die casting market is experiencing significant growth, presenting numerous opportunities for industry players. With a projected CAGR of 5.88% during the forecast period, the market is expected to reach USD 17,254.67 million by 2031. This growth is driven by the increasing demand from various sectors such as transportation, construction equipment, and building and construction.
Key players in the aluminum die casting market, including LTH Castings, Ryobi, Ahresty, and Handtmann, are actively participating in this growth and driving innovation. By developing advanced casting solutions and expanding their market presence, these companies are well-positioned to capitalize on the opportunities offered by the market.
Application Segments in the Aluminum Die Casting Market
The transportation sector, in particular, holds a significant share of the market. The demand for lightweight components in automobiles and aerospace applications is driving the need for aluminum die castings. Additionally, the construction equipment and building and construction sectors are also significant contributors to the market, as they require durable and complex aluminum castings.
Application Segments in the Aluminum Die Casting Market
The aluminum die casting market offers a wide range of applications across various industries. The demand for lightweight and durable components has led to the adoption of aluminum die castings in the automotive, transportation, construction equipment, and building and construction sectors. These segments require complex and precision parts that can be efficiently produced through die casting processes.
In the transportation sector, aluminum die castings find extensive use in automobiles and aerospace applications. The need for lightweight components to improve fuel efficiency and performance drives the demand for aluminum castings in this sector. The construction equipment industry also relies on aluminum die castings for durable and complex parts that can withstand harsh operating conditions. Similarly, the building and construction sector benefits from the versatility and strength of aluminum castings for structural components and architectural designs.
By catering to these diverse application segments, the aluminum die casting market demonstrates its adaptability and versatility. The industry continues to innovate and develop solutions that meet the evolving needs of these sectors, contributing to the overall growth and expansion of the market.
Table: Application Segments of Aluminum Die Casting Market
Application | Description |
---|---|
Transportation | Includes automobiles, aerospace applications |
Construction Equipment | Used in heavy machinery, such as excavators and cranes |
Building and Construction | For structural components and architectural designs |
Others | Various industries requiring durable and complex parts |
The diverse application segments of the aluminum die casting market provide ample opportunities for growth and innovation. As industries continue to seek lightweight, durable, and efficient solutions, aluminum die castings offer a reliable and cost-effective option. With ongoing advancements in die casting technology and increased collaboration between die casting companies and end-users, the market is poised for further expansion in the coming years.
Types of Aluminum Die Casting Processes
Aluminum die casting offers various processes to meet different casting needs in the automotive industry. These processes include high-pressure die casting, low-pressure die casting, and permanent mold casting.
High-Pressure Die Casting
High-pressure die casting is a widely used process for producing complex and precise aluminum castings. In this process, molten aluminum is injected into a steel mold at high pressure. The high pressure ensures that the molten metal fills the mold cavity completely, resulting in intricate and accurate castings. High-pressure die casting is suitable for producing lightweight and thin-walled components with excellent dimensional accuracy and surface finish.
Low-Pressure Die Casting
Low-pressure die casting is another process employed in the aluminum die casting industry. This process is suitable for producing larger and thicker-walled castings. In low-pressure die casting, the molten aluminum is poured into a permanent mold from a furnace located above the mold. The molten metal is drawn into the mold cavity using low pressure, allowing for the production of larger and more robust castings. Low-pressure die casting offers excellent dimensional stability and is often used for producing critical components in the automotive sector.
Permanent Mold Casting
The permanent mold casting process involves pouring the molten aluminum into a reusable mold made of steel or iron. Unlike other die casting processes, the mold used in permanent mold casting can be used multiple times. This process is suitable for producing medium to large aluminum castings with good dimensional accuracy and surface finish. Permanent mold casting offers cost savings and is commonly used in the automotive industry for producing parts such as engine blocks, transmission cases, and wheel hubs.
Process | Description | Applications |
---|---|---|
High-Pressure Die Casting | Injecting molten aluminum into a steel mold at high pressure to produce complex and precise castings | Automotive body parts, engine components, electronic housings |
Low-Pressure Die Casting | Pouring molten aluminum into a permanent mold from a furnace above the mold using low pressure | Large and thick-walled castings, structural components |
Permanent Mold Casting | Pouring molten aluminum into a reusable mold made of steel or iron | Engine blocks, transmission cases, wheel hubs |
These different types of aluminum die casting processes offer versatility and flexibility to meet the diverse requirements of the automotive sector. Manufacturers can choose the most suitable process based on the complexity of the casting, desired properties, and production volume. By leveraging these processes effectively, the automotive industry can continue to benefit from lightweight and durable aluminum castings.
Global Market Research Insights for the Aluminum Die Casting Market
In order to understand the current landscape and future prospects of the aluminum die casting market, comprehensive global market research has been conducted. The insights gained from this research provide valuable information regarding market dynamics, competitive trends, business opportunities, and consumer preferences.
The market research analysis indicates that the aluminum die casting market is projected to witness significant growth in regions such as North America, Europe, Asia Pacific, and the rest of the world. This growth is attributed to the increasing demand for lightweight components in various industries, including transportation, construction equipment, and building and construction.
Key Market Insights | Market Trends | Growth Opportunities | Challenges |
---|---|---|---|
Increasing demand for lightweight components | Adoption of digital technologies | Expansion into emerging regions | Supply chain disruptions |
Collaborative efforts between die casting companies and automotive manufacturers | Incorporation of recycled and renewable materials | Technological advancements | Economic uncertainty |
Focus on sustainability and carbon neutrality | Shift towards electric vehicles | Innovation in casting processes | Regional conflicts |
Overall, the global market research provides valuable insights into the aluminum die casting market, highlighting its growth potential, challenges, and opportunities. This information can guide businesses in making informed decisions, developing effective strategies, and capitalizing on the evolving market trends.
“The insights gained from global market research are invaluable for businesses operating in the aluminum die casting industry. Understanding market dynamics, competitive trends, and consumer preferences is crucial for strategic decision-making and sustainable growth.” – Aluminum Die Casting Industry Analyst
SWOT Analysis of the Aluminum Die Casting Market
The aluminum die casting market can be analyzed using a SWOT (Strengths, Weaknesses, Opportunities, Threats) analysis to gain insights into its competitive landscape and identify key factors influencing its growth. This analysis helps us understand the market dynamics, evaluate industry rankings, assess market share, and identify potential opportunities for growth and expansion. Let’s take a closer look at the SWOT analysis of the aluminum die casting market:
Strengths:
- High demand from industries such as automotive, aerospace, and construction, driving market growth.
- Ability to produce complex and precise aluminum castings for lightweight applications, offering a competitive advantage.
- Established expertise in aluminum die casting technology, infrastructure, and global supply chain.
- Strong collaboration between die casting companies and end-users, ensuring customized solutions and support.
Weaknesses:
- Reliance on the availability and cost of raw materials, particularly primary and recycled aluminum.
- Challenges associated with energy consumption and carbon emissions during the die casting process.
- Need for continuous investments in research and development to stay ahead of technological advancements.
Opportunities:
- Growing demand for lightweight components in the automotive and aerospace sectors, creating opportunities for aluminum die castings.
- Collaboration with automotive manufacturers to provide integrated manufacturing solutions and support.
- Increasing emphasis on sustainable production practices, driving the adoption of aluminum castings.
- Expansion into emerging regions with untapped market potential.
Threats:
- Fluctuations in raw material prices and supply chain disruptions, impacting production costs and delivery timelines.
- Intense competition within the aluminum die casting market, requiring companies to differentiate and innovate to maintain market share.
- Regulatory changes and environmental policies affecting the use of raw materials and energy consumption.
- Potential risks and uncertainties associated with geopolitical tensions and global economic conditions.
By analyzing the strengths, weaknesses, opportunities, and threats of the aluminum die casting market, stakeholders can make informed decisions and develop strategies to navigate challenges, capitalize on opportunities, and drive growth in this dynamic industry.
PESTLE Analysis of the Aluminum Die Casting Market
When assessing the factors that impact the aluminum die casting market, conducting a PESTLE analysis is essential. This analysis examines the political, economic, social, technological, legal, and environmental factors that shape the industry’s landscape and influence its growth prospects.
Political: Government policies and regulations play a significant role in shaping the aluminum die casting market. Policies promoting environmental sustainability, such as carbon emissions reduction targets and support for renewable energy sources, drive the demand for aluminum die castings in industries striving for greener solutions. Additionally, trade policies and international relations impact market dynamics, as tariffs and trade restrictions can affect the global supply chain.
Economic: Economic factors, including GDP growth, inflation rates, and consumer spending, have a direct impact on the aluminum die casting market. The industry’s performance is closely linked to sectors such as automotive, aerospace, and construction, which are influenced by economic conditions. Fluctuations in commodity prices, exchange rates, and labor costs can also impact the overall cost of production and profitability within the market.
Social: Social factors, such as consumer preferences and societal trends, influence the demand for aluminum die castings. The shift towards electric vehicles and the increasing focus on sustainability drive the demand for lightweight and energy-efficient components, which are often produced through die casting processes. Changing demographics, such as an aging population or urbanization, can also shape market demand for specific applications in industries such as healthcare or infrastructure development.
Technological: Technological advancements in materials, manufacturing processes, and automation have a profound impact on the aluminum die casting market. The industry is constantly evolving to adopt new technologies that enhance product quality, increase production efficiency, and reduce costs. Innovations in additive manufacturing, simulation software, and digitalization tools enable the industry to optimize designs, improve casting integrity, and streamline production.
Legal: Legal factors, such as health and safety regulations, intellectual property rights, and product quality standards, define the operating environment for the aluminum die casting market. Compliance with industry-specific regulations ensures the production of high-quality castings that meet safety standards and customer requirements. Additionally, legal frameworks related to labor practices, environmental protection, and international trade agreements can impact market dynamics and operating costs.
Environmental: Environmental factors play an increasingly important role in the aluminum die casting market. The industry’s focus on sustainability and reducing its carbon footprint drives the adoption of recycled materials, energy-efficient production processes, and waste reduction initiatives. Environmental regulations related to emissions and waste management influence the industry’s practices and market demand for greener solutions.
Regional Insights for the Aluminum Die Casting Market
When analyzing the aluminum die casting market, it is crucial to consider regional dynamics and variations in demand. Understanding the regional context provides valuable insights into market growth, opportunities, and challenges. In this section, we explore the regional landscape of the aluminum die casting market, with a focus on key regions and their contributions to the industry.
North America
North America is a significant player in the aluminum die casting market, driven by the growth of the automotive and aerospace industries. The region has a strong presence of key market players and advanced manufacturing capabilities. In recent years, there has been a shift towards lightweight materials in the automotive sector, leading to increased demand for aluminum die castings. Additionally, the aerospace industry’s emphasis on fuel efficiency and performance has further boosted the demand for lightweight aluminum components.
Europe
Europe is another prominent region in the aluminum die casting market, with countries like Germany, Italy, France, and the United Kingdom being major contributors. The automotive industry plays a significant role in driving the demand for aluminum die castings in Europe. The region is known for its well-established automotive manufacturers and a focus on sustainable and energy-efficient solutions. Furthermore, the construction sector in Europe also relies on high-quality aluminum castings for its infrastructure projects.
Asia Pacific
The Asia Pacific region, particularly China, is expected to witness substantial growth in the aluminum die casting market. The rapid industrialization, population growth, and increasing disposable income in the region have fueled the demand for automotive and construction equipment. As a result, there is a growing need for lightweight and durable aluminum components, driving the adoption of die casting solutions. The Asia Pacific region is also home to several die casting companies, making it a key manufacturing hub for the industry.
Other regions, such as South America and the Middle East and Africa, also contribute to the aluminum die casting market, albeit to a lesser extent. However, with the increasing focus on sustainable development and the adoption of lightweight materials in various industries, these regions are expected to witness growth opportunities in the future.
Region | Key Factors |
---|---|
North America | Strong presence of automotive and aerospace industries |
Europe | Well-established automotive manufacturers, emphasis on sustainability |
Asia Pacific | Rapid industrialization, growing automotive and construction sectors |
South America | Potential for growth, increasing demand for lightweight components |
Middle East and Africa | Emerging opportunities, focus on sustainable development |
Impact of COVID-19 and Regional Conflicts on the Aluminum Die Casting Market
The aluminum die casting market has not been immune to the impact of global events such as the COVID-19 pandemic and regional conflicts. These external factors have disrupted supply chains, reduced demand, and created uncertainties for the industry. It is important to analyze and understand the implications of these events on the aluminum die casting market to navigate through the challenges and identify potential opportunities.
The COVID-19 pandemic has led to significant disruptions in the global economy, including the automotive industry, which is a key consumer of aluminum die castings. Lockdowns, travel restrictions, and reduced consumer spending have resulted in a decline in automobile sales and production. This has directly affected the demand for aluminum die castings in the automotive sector, leading to a slowdown in the market. However, as the world gradually recovers from the pandemic and the automotive industry adapts to the new normal, the demand for aluminum die castings is expected to rebound.
In addition to the pandemic, regional conflicts such as the Russia-Ukraine war have also impacted the aluminum die casting market. These conflicts introduce geopolitical risks and uncertainties, which can disrupt supply chains and create trade barriers. The fluctuating political and economic landscapes in affected regions can lead to reduced market accessibility and hinder business operations. It is crucial for industry players to carefully monitor these conflicts and their potential implications on the aluminum die casting market.
Table: Impact of COVID-19 and Regional Conflicts on the Aluminum Die Casting Market
Factors | Impact |
---|---|
COVID-19 | – Disrupted supply chains – Reduced demand from the automotive sector – Slowdown in market growth |
Regional Conflicts | – Geopolitical risks and uncertainties – Disrupted supply chains – Trade barriers – Reduced market accessibility |
Despite these challenges, the aluminum die casting market has shown resilience and adaptability in the face of adversity. The industry has been actively implementing measures to mitigate the impact of these events, such as diversifying supply chains, exploring new markets, and optimizing manufacturing processes. As the global economy stabilizes and regional conflicts are resolved, the aluminum die casting market is expected to regain its momentum and continue its growth trajectory.
It is important for industry stakeholders to stay informed about the latest developments and trends in the aluminum die casting market, especially in relation to the impact of COVID-19 and regional conflicts. By closely monitoring these factors and proactively adjusting strategies, businesses can position themselves for success and capitalize on emerging opportunities in the market.
Conclusion
In conclusion, the aluminum die casting industry is experiencing significant growth prospects, particularly in the automotive sector. The shift towards electric vehicles and the demand for lightweight components have created new opportunities for aluminum die castings. The ability of aluminum castings to replace multiple steel components and reduce assembly processes makes them beneficial for bodywork applications. Collaborative efforts between die casting companies and automotive manufacturers are crucial to provide complete solutions and support for integrated manufacturing processes.
Digitization plays a pivotal role in driving the aluminum die casting industry forward. By embracing digital technologies, foundries can achieve zero waste, reduce cycle time, and operate in a more sustainable manner. Additionally, the focus on using recycled or primary aluminum extracted with renewable energy is making aluminum die castings more environmentally friendly. These advancements contribute to the industry’s growth and evolution, ensuring sustainable practices for the future.
The global aluminum die casting market offers numerous opportunities for innovation, technological advancements, and expansion into emerging regions. With a projected CAGR of 5.88% by 2031, the market is driven by increasing demand from various industries such as transportation, construction equipment, and building and construction. Key players in the market are actively developing innovative casting solutions and expanding their market presence to cater to the diverse needs of different sectors.
In conclusion, the aluminum die casting industry is primed for growth, driven by the demand for lightweight components, collaborative efforts with the automotive sector, digitization initiatives, and expanding market opportunities. With a focus on sustainability and technological advancements, the industry is well-positioned to meet the evolving needs of different sectors and thrive in the future.
Disclaimer
The information provided in this article is based on factual data and research findings from various sources. While efforts have been made to ensure accuracy, the article is for informational purposes only and should not be considered as professional advice. Readers should conduct their own research and consult industry experts for specific guidance related to the aluminum die casting industry.
FAQ
What is driving the demand for aluminum die castings in the automotive sector?
The shift towards electric vehicles and the need for lightweight components are driving the demand for aluminum die castings in the automotive sector.
How are aluminum die castings beneficial for bodywork in automobiles?
Aluminum die castings can replace multiple steel components, reduce assembly processes, and decrease factory footprint in bodywork applications.
What role does digitization play in improving efficiency and sustainability in aluminum die casting?
Digitization allows for greater connectivity and automation, leading to cost savings and more sustainable production practices in aluminum die casting.
What are the key application segments in the aluminum die casting market?
The key application segments in the aluminum die casting market include transportation, construction equipment, building and construction, and others.
What are the different processes used in aluminum die casting?
Aluminum die casting can be performed using high-pressure die casting, low-pressure die casting, and permanent mold casting processes.
Who are the key players in the aluminum die casting market?
Key players in the aluminum die casting market include Aluminum Corporation of China, Rockman Industries Ltd., Alcoa Corporation, Nemak S.A.B. de C.V., and more.
How has the COVID-19 pandemic affected the aluminum die casting market?
The COVID-19 pandemic has disrupted supply chains, reduced demand, and created economic uncertainties in the aluminum die casting market.
What are the growth prospects for the aluminum die casting industry?
The aluminum die casting industry is poised for growth due to the increasing demand for lightweight components and the shift towards electric vehicles.
What should readers consider when interpreting the information provided in this article?
The information provided is based on factual data and research, but readers should conduct their own research and consult industry experts for specific guidance.