When it comes to aluminum die cast, making the right choice between cold chamber and hot chamber die casting methods is crucial for successful casting production. The process of die casting involves injecting molten metal into a mold cavity under high pressure. Depending on the metal material being used, either a hot chamber or cold chamber die casting machine may be used.
Cold chamber die casting is typically used for metals with high melting points, such as aluminum and copper. This method involves melting the metal in a separate furnace and then transferring it to the machine’s chamber. Cold chamber die casting allows for better control over the temperature and quality of the molten metal, making it suitable for larger and more complex parts that require higher precision and strength.
On the other hand, hot chamber die casting is suitable for metals with low melting points, such as zinc and lead. This method has a built-in furnace that keeps the metal molten at all times, allowing for faster production cycles. However, the types of metal that can be used are limited compared to cold chamber die casting.
Key Takeaways:
- The choice between cold chamber and hot chamber die casting depends on various factors, including the type of metal, part complexity, production speed, and cost.
- Cold chamber die casting is suitable for metals with high melting points, while hot chamber die casting is suitable for metals with low melting points.
- Cold chamber die casting allows for better control over the temperature and quality of the molten metal, making it suitable for larger and more complex parts.
- Hot chamber die casting has faster production cycles but is limited in the types of metal that can be used.
- Consider the specific requirements of your casting process when choosing between cold chamber and hot chamber die casting.
Understanding Die Casting
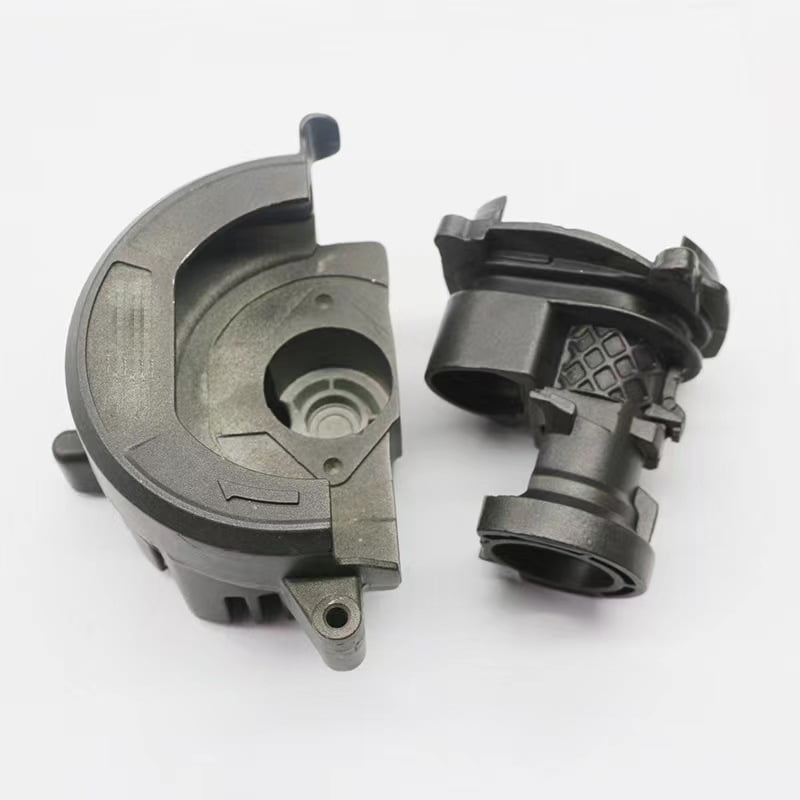
Die casting is a manufacturing process that involves melting metal alloys and injecting the molten metal into a die cavity under high pressure. This process allows for the production of complex and precise parts with excellent surface finishes. Die casting is widely used in various industries, including automotive, aerospace, and electronics, due to its versatility and efficiency.
The first step in die casting is choosing the appropriate alloy for the desired part. Common alloys used in die casting include aluminum, zinc, and magnesium, each offering unique properties and advantages. Once the alloy is selected, it is melted in a furnace and then injected into the die cavity using a casting machine. The high pressure ensures that the molten metal fills the mold cavity completely, resulting in a detailed and accurate part.
One of the key advantages of die casting is the ability to produce large quantities of parts with consistent quality. Since the molten metal is injected under high pressure, it fills every intricate detail of the die cavity, resulting in parts with tight tolerances and minimal porosity. This makes die casting an ideal choice for creating complex shapes and thin-walled components.
In summary, die casting is a highly efficient and precise manufacturing process that allows for the production of complex parts with excellent surface finishes. By melting metal alloys and injecting them into a die cavity under high pressure, die casting offers a cost-effective solution for various industries. With the ability to produce large quantities of parts with consistent quality, die casting continues to be a go-to method for many manufacturers.
Cold Chamber Die Casting
Cold chamber die casting is a method commonly used for metals with high melting points, such as aluminum and copper. This process involves melting the metal in a separate furnace and then transferring it to the machine’s chamber. The molten metal is then injected into a die cavity under high pressure, allowing for the production of intricate and precise parts.
One of the key advantages of cold chamber die casting is the ability to maintain better control over the temperature and quality of the molten metal. By separating the melting process from the casting process, manufacturers can ensure that the metal is at the optimal temperature and free from impurities before it is injected into the die cavity. This results in higher quality and more consistent parts.
Cold chamber die casting is also well-suited for producing larger and more complex parts that require higher precision and strength. The high-pressure nature of the process allows for excellent material flow and fill, ensuring that the molten metal reaches all areas of the die cavity. This results in parts with tight tolerances and superior mechanical properties.
Advantages of Cold Chamber Die Casting:
- Precise and intricate parts can be produced
- Better control over the temperature and quality of the molten metal
- Ideal for metals with high melting points, such as aluminum and copper
- High strength and excellent material flow
Despite its advantages, cold chamber die casting also has some limitations. The process is generally slower compared to hot chamber die casting due to the additional steps involved in melting the metal. Additionally, the initial setup and equipment costs for cold chamber die casting can be higher compared to hot chamber die casting.
Advantages | Disadvantages |
---|---|
Precise and intricate parts | Slower production compared to hot chamber die casting |
Better control over temperature and quality of molten metal | Higher setup and equipment costs |
Ideal for metals with high melting points | |
High strength and excellent material flow |
Despite its limitations, cold chamber die casting is a versatile and widely used method for producing high-quality and complex parts. By carefully considering the specific requirements of the casting process, manufacturers can choose the right type of die casting – cold chamber or hot chamber – to achieve optimal results in terms of quality, precision, and production efficiency.
Hot Chamber Die Casting
Hot chamber die casting is ideal for metals with low melting points, such as zinc and lead. In this process, the die casting machine has a built-in furnace that keeps the metal molten at all times, allowing for faster production cycles. The molten metal is injected directly into the die cavity under high pressure, resulting in the formation of the desired part.
One of the main advantages of hot chamber die casting is its efficiency in producing small and relatively simple parts. The continuous cycle of keeping the metal molten eliminates the need for separate melting and transferring processes, saving time and energy. This makes hot chamber die casting a cost-effective option for industries that require high-volume production of small parts.
Advantages of Hot Chamber Die Casting | Disadvantages of Hot Chamber Die Casting |
---|---|
Fast production cycles | Limited to metals with low melting points |
Cost-effective for high-volume production | Less precise than cold chamber die casting |
Reduced need for secondary operations | Less suitable for large and complex parts |
While hot chamber die casting offers several advantages, it is important to consider its limitations. The process is not suitable for metals with high melting points, as the continuous heating can cause premature oxidation. Additionally, hot chamber die casting may not achieve the same level of precision and strength as cold chamber die casting, making it less suitable for larger and more complex parts.
In conclusion, hot chamber die casting is an efficient and cost-effective method for producing small parts made from metals with low melting points. However, its limitations in terms of metal compatibility and precision should be considered when choosing the appropriate die casting process for a specific application.
Factors to Consider in Choosing the Right Type
Several factors should be taken into account when deciding between cold chamber and hot chamber die casting methods. The first consideration is the type of metal being used. Cold chamber die casting is typically used for metals with high melting points, such as aluminum and copper. These metals require a separate furnace for melting before being transferred to the die casting machine. On the other hand, hot chamber die casting is suitable for metals with low melting points, such as zinc and lead, as the machine has a built-in furnace to keep the metal molten at all times.
Another factor to consider is the desired production speed. Hot chamber die casting allows for faster production cycles since the metal remains molten in the machine. This makes it more suitable for high-volume production of smaller and simpler parts. Cold chamber die casting, on the other hand, is typically used for larger and more complex parts that require higher precision and strength, but slower production cycles.
The complexity of the part being cast is also an important consideration. Cold chamber die casting provides better control over the temperature and quality of the molten metal, making it suitable for parts with intricate designs and tight tolerances. Hot chamber die casting may not be able to achieve the same level of precision for complex parts.
Other factors to consider include the cost of the die casting process and the availability of the required machinery. Cold chamber die casting machines tend to be more expensive and require a separate furnace, while hot chamber die casting machines are typically less expensive and more readily available. The overall cost of the process, including material costs and production efficiency, should also be evaluated when making a decision.
Factors to Consider | Cold Chamber Die Casting | Hot Chamber Die Casting |
---|---|---|
Type of Metal | High melting point metals (e.g., aluminum, copper) | Low melting point metals (e.g., zinc, lead) |
Production Speed | Slower production cycles | Faster production cycles |
Part Complexity | Complex parts requiring higher precision and strength | Smaller and simpler parts |
Cost | Higher machine and furnace costs | Lower machine costs |
Choosing the right type of die casting method is crucial to ensure the desired outcome in terms of part quality, production speed, and cost-effectiveness. By carefully considering the type of metal, production requirements, part complexity, and cost factors, manufacturers can make an informed decision between cold chamber and hot chamber die casting methods.
Advantages and Disadvantages of Cold Chamber Die Casting
Cold chamber die casting offers certain advantages and disadvantages compared to hot chamber die casting. These factors play a crucial role in determining the most suitable casting method for a particular application. Let’s explore the advantages and disadvantages of cold chamber die casting:
Advantages:
- High melting point metals: Cold chamber die casting is ideal for metals with high melting points, such as aluminum and copper. The separate furnace allows for precise control over the temperature, ensuring the molten metal maintains its desired properties.
- Strength and durability: Cold chamber die casting results in stronger and more durable parts. The high-pressure injection process ensures excellent material integrity, resulting in parts that can withstand demanding conditions.
- Precision and complexity: The cold chamber process allows for greater precision and complexity in the cast parts. This method is ideal for larger and more intricate components that require tight tolerances and intricate geometries.
- Reduced porosity: Cold chamber die casting minimizes the risk of porosity in the cast parts. The controlled temperature and pressure help eliminate air and gas entrapment, resulting in high-quality, porosity-free products.
Disadvantages:
- Slower cycle times: Compared to hot chamber die casting, the cold chamber process typically has slower production cycles. The need to melt the metal separately and transfer it to the machine’s chamber adds extra time to the overall process.
- Higher equipment and operating costs: The cold chamber die casting process often requires more sophisticated and robust equipment, contributing to higher initial setup costs. Additionally, the separate furnace and additional material handling increase operational expenses.
- Limited material options: While cold chamber die casting is suitable for a wide range of high melting point metals, it is not suitable for metals with low melting points, such as zinc and lead. These metals require the higher temperatures provided by the built-in furnace in hot chamber die casting machines.
Summary
In summary, cold chamber die casting offers advantages in terms of handling high melting point metals, producing strong and precise parts, and reducing porosity. However, it comes with drawbacks such as slower cycle times, higher equipment costs, and limitations in material options. When deciding between cold chamber and hot chamber die casting, it is essential to consider the specific requirements of the casting process, including the type of metal, part complexity, production speed, and cost.
Advantages of Cold Chamber Die Casting | Disadvantages of Cold Chamber Die Casting |
---|---|
– Suitable for high melting point metals – Produces strong and durable parts – Allows for precision and complexity – Minimizes porosity in cast parts | – Slower cycle times – Higher equipment and operating costs – Limited material options |
Advantages and Disadvantages of Hot Chamber Die Casting
Hot chamber die casting has its own set of advantages and disadvantages in the casting industry. This method is particularly well-suited for metals with low melting points, such as zinc and lead. One of the main advantages of hot chamber die casting is its ability to achieve faster production cycles. The built-in furnace keeps the metal in a molten state at all times, allowing for quicker injection and solidification of the material. This leads to higher production rates and increased efficiency.
In addition to its faster production cycles, hot chamber die casting also offers excellent dimensional accuracy and surface finish. The consistent temperature and flow of the molten metal ensure that the final product has precise dimensions and a smooth surface. This makes hot chamber die casting ideal for producing small, intricate parts that require a high level of precision.
However, hot chamber die casting does have some limitations. Because the metal is always kept in a molten state, it restricts the choice of metals that can be used. Hot chamber die casting is best suited for metals with low melting points, as higher melting point metals may damage the furnace. This limits the range of materials that can be utilized in the hot chamber die casting process.
Advantages | Disadvantages |
---|---|
Faster production cycles | Limited choice of metals |
Excellent dimensional accuracy | Restricted range of materials |
Superior surface finish |
In summary, hot chamber die casting is a casting method that offers several advantages in terms of production speed, dimensional accuracy, and surface finish. However, its limitations in terms of material choice make it more suitable for certain applications. When selecting a die casting method, it is essential to consider the specific requirements of the project and choose the method that best meets those needs.
The Versatility of Die Casting
Die casting, whether cold chamber or hot chamber, offers a versatile method of manufacturing various parts by injecting molten metal into a die cavity. This process allows for the production of complex shapes with high precision and repeatability. Both cold chamber and hot chamber die casting have their unique advantages and applications, making them suitable for a wide range of industries and product requirements.
One of the key advantages of die casting is the ability to work with a variety of metals and alloys. Cold chamber die casting is commonly used for metals with high melting points, such as aluminum and copper. This method allows for superior control over the temperature and quality of the molten metal, resulting in high-quality castings with excellent surface finish and dimensional accuracy. On the other hand, hot chamber die casting is ideal for metals with lower melting points, such as zinc and lead. The built-in furnace in the hot chamber machine keeps the metal in a molten state, enabling faster production cycles and reducing the need for additional melting processes.
Another factor that contributes to the versatility of die casting is the wide range of part sizes and complexities that can be achieved. Cold chamber die casting is often used for larger and more intricate parts that require high strength and precision, such as automotive engine components and aerospace parts. The cold chamber process allows for the production of larger castings with complex geometries, ensuring the structural integrity and functionality of the final product. Hot chamber die casting, on the other hand, is well-suited for small and simple parts, making it ideal for applications in the electronics industry and consumer goods sector.
Advantages of Die Casting | Disadvantages of Die Casting |
---|---|
High production efficiencyExcellent dimensional accuracySmooth surface finishAbility to produce complex shapes | High setup and tooling costsLimitations on part size and design complexityLimited material options for hot chamber die castingChallenging to achieve certain surface finishes |
In summary, die casting is a versatile manufacturing process that offers a range of benefits for producing various parts. Whether through cold chamber or hot chamber die casting, manufacturers can achieve high precision and efficiency in the production of complex metal parts. The choice between the two methods depends on factors such as metal type, part size and complexity, and production requirements. By understanding the advantages and limitations of each method, manufacturers can select the most suitable die casting approach for their specific application.
Applications and Types of Die Casting Processes
Die casting is widely used in various industries, with applications ranging from high-pressure die casting to zinc die casting. This versatile manufacturing process allows for the production of intricate and complex parts with high precision and repeatability. The choice of die casting method depends on factors such as the type of metal being used, the desired production speed, and the complexity of the part being cast.
High-pressure die casting is one of the most common types of die casting processes. It involves injecting molten metal into a die cavity at high pressures, resulting in fast and accurate production of complex parts. This method is often used for manufacturing components in the automotive, aerospace, and electronics industries, where strength, durability, and dimensional accuracy are crucial.
Another type of die casting process is hot chamber casting, which is suitable for metals with low melting points, such as zinc and lead. In hot chamber die casting, the metal is kept molten in a furnace within the casting machine, allowing for faster production cycles. This method is commonly used for producing small and intricate parts, such as consumer electronics components and decorative hardware.
Example of High-Pressure Die Casting Application
“The high-pressure die casting process is ideal for producing complex geometric shapes with tight tolerances. We recently utilized this method to manufacture a critical component for the automotive industry. The part required high strength and dimensional accuracy, and the high-pressure die casting process delivered excellent results. The speed and efficiency of the process allowed us to meet tight production deadlines without compromising on quality.”
Comparison between High-Pressure Die Casting and Zinc Die Casting
Factors | High-Pressure Die Casting | Zinc Die Casting |
---|---|---|
Metal Compatibility | Wide range of metals, including aluminum and copper | Primarily used for zinc and zinc-alloy |
Production Speed | Fast production cycles | Faster production cycles due to lower melting point |
Part Complexity | Capable of producing complex and intricate parts | Suitable for small and less complex parts |
Strength and Durability | High strength and excellent durability | Good strength and durability |
When choosing a die casting process, it is important to consider the specific requirements of the application. Factors such as metal compatibility, production speed, part complexity, and desired strength and durability should be taken into account. By selecting the right method, manufacturers can achieve efficient and cost-effective production of high-quality die cast parts.
Cold Chamber Die Casting Process
The cold chamber die casting process is suitable for producing parts with longer die life and high precision. This process involves melting the metal in a separate furnace and then transferring it to the machine’s chamber. The molten metal is then injected into the die cavity under high pressure, resulting in the formation of the desired part.
One of the advantages of cold chamber die casting is its ability to handle metals with high melting points, such as aluminum and copper. These metals require a separate melting process to reach their molten state before being injected into the die. This allows for better control over the temperature and quality of the molten metal, resulting in parts with higher precision and strength.
Cold chamber die casting is often used for larger and more complex parts that require tight tolerances and intricate shapes. The longer die life associated with cold chamber die casting is beneficial for high-volume production runs, as it reduces the need for frequent tooling maintenance and replacement. This process also offers better surface finish and improved mechanical properties compared to other casting methods.
Advantages of Cold Chamber Die Casting | Disadvantages of Cold Chamber Die Casting |
---|---|
High precision and accuracyStronger mechanical propertiesLonger die lifeBetter surface finish | Higher initial investment costRequires additional melting processNot suitable for metals with low melting points |
In summary, the cold chamber die casting process is ideal for producing parts with longer die life and high precision. It offers advantages such as greater control over temperature and quality, as well as the ability to handle metals with high melting points. While it has some disadvantages, such as higher initial cost, it is a preferred choice for complex parts that require tight tolerances and strength.
Hot Chamber Die Casting Process
The hot-chamber die casting process plays a significant role in the die casting industry, offering advantages and differences compared to the cold chamber process. In hot chamber die casting, the machine has a built-in furnace that keeps the metal molten at all times. This allows for faster production cycles and eliminates the need for a separate melting process. The molten metal is injected directly into the die cavity under high pressure, resulting in precise and efficient casting.
One of the major advantages of hot chamber die casting is its suitability for metals with low melting points, such as zinc and lead. These metals can be easily melted and maintained in the machine’s furnace, ensuring a continuous flow of molten metal for rapid production. Hot chamber die casting is particularly useful for manufacturing smaller and simpler parts that require high production volumes and quick turnaround times.
While hot chamber die casting offers several benefits, it also has limitations. The use of a built-in furnace limits the types of metals that can be used in the process. Metals with higher melting points, such as aluminum and copper, cannot be effectively utilized in hot chamber die casting due to the risk of damaging the furnace. Additionally, the constant heating of the metal can sometimes lead to oxidation, which can affect the quality of the cast parts.
In summary, the hot-chamber die casting process is a valuable method in the die casting industry, especially for the production of small and simple parts with low melting point metals. It offers faster production cycles and eliminates the need for a separate melting process. However, it is important to consider the limitations of hot chamber die casting, such as the restricted use of metals with higher melting points. By carefully evaluating the requirements of the casting project, manufacturers can choose between hot chamber and cold chamber die casting to achieve optimum results.
Differences Between Hot Chamber and Cold Chamber Die Casting
Understanding the key differences between hot chamber and cold chamber die casting is essential in selecting the appropriate casting method. The die casting process involves injecting molten metal into a mold cavity under high pressure. The choice between hot chamber and cold chamber die casting depends on various factors such as the type of metal being used, production speed, and part complexity.
In cold chamber die casting, metals with high melting points, such as aluminum and copper, are used. The metal is melted in a separate furnace and transferred to the die casting machine’s chamber. This process allows for better temperature control and quality of the molten metal. Cold chamber die casting is typically used for larger and more complex parts that require higher precision and strength.
In contrast, hot chamber die casting is suitable for metals with low melting points, such as zinc and lead. The die casting machine has a built-in furnace that keeps the metal molten at all times, allowing for faster production cycles. However, the types of metals that can be used in hot chamber die casting are limited due to the lower melting point requirement. Hot chamber die casting is commonly used for smaller and simpler parts that require quicker production.
When selecting between hot chamber and cold chamber die casting, it is crucial to consider the specific requirements of the casting process. Factors such as the type of metal, part complexity, production speed, and cost should be taken into account. Both hot chamber and cold chamber die casting methods have their advantages and disadvantages, and the appropriate choice depends on the desired outcomes and constraints of the manufacturing project.
Hot Chamber Die Casting | Cold Chamber Die Casting |
---|---|
Used for metals with low melting points | Used for metals with high melting points |
Faster production cycles | Slower production cycles |
Limited to certain metal types | Offers a wider range of metal options |
Ideal for smaller and simpler parts | Suitable for larger and more complex parts |
Cold Chamber Die-Casting Process Step by Step
The cold chamber die-casting process is a versatile and efficient method of manufacturing various parts. It involves several steps that ensure the production of high-quality die castings. Here is a step-by-step overview of the cold chamber die-casting process:
- Preparation: The process begins with the preparation of the die casting machine. The die is cleaned and preheated to the desired temperature. The mold release agent is applied to ensure easy removal of the cast part.
- Injection: Once the preparation is complete, the molten metal is manually or automatically ladled into the cold chamber machine’s crucible. The machine closes and seals the chamber, and a piston injects the molten metal into the die cavity with high pressure. This ensures that the metal fills the entire cavity and takes the shape of the desired part.
- Solidification: After the metal is injected into the die cavity, it quickly solidifies under high pressure and cooling. This ensures the formation of a solid and dense part with precise dimensions.
- Ejection: Once the part has solidified, the machine opens, and the ejector pins push the casting out of the die cavity. The casting is then removed from the machine and trimmed of any excess material or imperfections.
The cold chamber die-casting process offers several advantages, such as the ability to produce complex and high-strength parts with tight tolerances. It also allows for the use of a wide range of metals, including aluminum, copper, and magnesium. Additionally, the cold chamber process offers a longer die life and better control over the quality of the castings.
However, it is worth noting that the cold chamber die-casting process may have longer cycle times compared to hot chamber die casting. This is because the metal must be preheated in a separate furnace before being transferred to the machine’s chamber. Despite this, the cold chamber process remains a preferred choice for applications that require superior part quality and structural integrity.
Application of Cold Chamber Die Casting
Cold chamber die casting finds application in various industries, including automotive, aerospace, and electronics. It is commonly used to manufacture parts such as engine components, transmission housings, and electronic enclosures. The versatility of the cold chamber die-casting process allows for the production of intricate and highly detailed parts, making it a preferred method in industries with demanding requirements.
Advantages | Disadvantages |
---|---|
– Ability to produce complex and high-strength parts | – Longer cycle times compared to hot chamber die casting |
– Tight tolerances and precise dimensions | – Requires preheating of the metal in a separate furnace |
– Wide range of metal options | – Higher initial tooling and equipment costs |
– Longer die life | – More extensive maintenance requirements |
In conclusion, the cold chamber die-casting process serves as an excellent choice for manufacturing various parts that require high precision, strength, and dimensional accuracy. Its versatility and ability to produce complex parts make it a preferred method in many industries. By understanding the step-by-step process and the advantages of cold chamber die casting, manufacturers can make informed decisions when selecting the appropriate die casting method for their specific applications.
Conclusion
In conclusion, the choice between cold chamber and hot chamber die casting depends on the specific requirements of the casting process, with both methods offering unique advantages and benefits. Cold chamber die casting is ideal for metals with high melting points, such as aluminum and copper, and is commonly used for larger and more complex parts that require higher precision and strength. The process involves melting the metal in a separate furnace and then transferring it to the die casting machine’s chamber, allowing for better temperature control and superior quality of the molten metal.
On the other hand, hot chamber die casting is suitable for metals with low melting points, like zinc and lead, and is often chosen for smaller and simpler parts that require faster production cycles. The hot chamber die casting machine has a built-in furnace that keeps the metal molten at all times, resulting in faster production speeds. However, the limitation lies in the types of metals that can be used due to their lower melting points.
When selecting the appropriate type of die casting, consideration must be given to the specific requirements of the casting process. Factors such as the type of metal, part complexity, production speed, and cost should all be evaluated. With cold chamber die casting, the emphasis is on precision, strength, and the ability to handle high melting point metals. Meanwhile, hot chamber die casting excels in speed and efficiency but is limited to metals with lower melting points.
Ultimately, the decision between cold chamber and hot chamber die casting hinges on finding the right balance between precision, speed, and material suitability. By carefully assessing the specific needs of the casting process, manufacturers can determine which method will best meet their requirements, ensuring the production of high-quality parts in a cost-effective and efficient manner.
The Versatility of Die Casting
When it comes to manufacturing precision metal components, die casting is a versatile and efficient process that delivers high-quality results. Die casting involves injecting molten metal into a mold cavity under high pressure, creating near-net-shape parts with excellent detail and dimensional accuracy.
There are two main types of die casting machines: cold chamber and hot chamber. The choice between these two types depends on the properties of the metal being used and the specific requirements of the casting process.
In cold chamber die casting, metals with high melting points, such as aluminum and copper, are melted in a separate furnace before being transferred to the machine’s chamber. This method allows for better control over the temperature and quality of the molten metal. On the other hand, hot chamber die casting is suitable for metals with low melting points, such as zinc and lead. The metal is kept molten at all times in a built-in furnace within the machine, allowing for faster production cycles.
When deciding between cold chamber and hot chamber die casting, several factors should be considered. The complexity of the part being cast, the desired production speed, and the type of metal all play a role in determining the most suitable method. Cold chamber die casting is typically chosen for larger, more complex parts that require high precision and strength. Hot chamber die casting, on the other hand, is ideal for smaller, simpler parts that require faster production cycles.
FAQ
What is die casting?
Die casting is a manufacturing process that involves injecting molten metal into a mold cavity under high pressure.
What is the difference between cold chamber and hot chamber die casting?
Cold chamber die casting involves melting the metal in a separate furnace and then transferring it to the machine’s chamber, while hot chamber die casting has a built-in furnace that keeps the metal molten at all times.
When is cold chamber die casting used?
Cold chamber die casting is typically used for metals with high melting points, such as aluminum and copper, and for larger and more complex parts that require higher precision and strength.
When is hot chamber die casting used?
Hot chamber die casting is suitable for metals with low melting points, such as zinc and lead, and for smaller and simpler parts that require faster production cycles.
What factors should be considered when choosing between cold chamber and hot chamber die casting?
Factors to consider include the type of metal being used, the desired production speed, and the complexity of the part being cast.
What are the advantages of cold chamber die casting?
Cold chamber die casting allows for better control over the temperature and quality of the molten metal and is suitable for larger and more complex parts.
What are the disadvantages of cold chamber die casting?
Cold chamber die casting has a slower production cycle compared to hot chamber die casting.
What are the advantages of hot chamber die casting?
Hot chamber die casting has a faster production cycle and is suitable for smaller and simpler parts.
What are the disadvantages of hot chamber die casting?
Hot chamber die casting is limited to metals with low melting points and has limitations in terms of the types of metals that can be used.
How can die casting be used in various applications?
Die casting is a versatile process that can be used in a wide range of applications, from automotive and aerospace industries to consumer electronics and household appliances.
Source Links
- https://www.openpr.com/news/3246286/aluminum-castings-market-predicted-to-reach-usd-171-billion-at
- https://www.seedance.com/aluminum-die-casting-market-size-share-growth-latest-trends-scope-and-report-2023-2028/
- https://cleantechnica.com/2019/07/23/tesla-files-patent-application-for-die-cast-unibody-machine/