Stainless steel casting is a precise and complex process used to create intricate components for a wide range of industries. One of the crucial aspects of the stainless steel casting process is shell molding, which contributes significantly to the quality and reliability of the final product. At KT-Foundry, we understand the importance of crafting top-notch stainless steel castings, which is why we employ shell mold casting techniques to achieve the highest levels of dimensional accuracy and precision.
Key Takeaways:
- Shell molding plays a vital role in the stainless steel casting process
- Precision and reliability are essential for crafting high-quality stainless steel castings
- KT-Foundry employs shell mold casting to achieve superior dimensional accuracy
- Crafting quality stainless steel castings requires meticulous attention to detail
- Our commitment to excellence ensures that we deliver top-notch stainless steel castings to our clients
The Shell Mold Casting Process
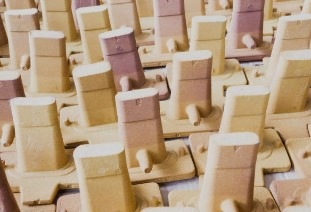
At KT-Foundry, we understand the importance of precision and reliability in stainless steel casting. This is why we utilize the technique of shell molding, a precision casting process known for its ability to produce intricate stainless steel components with thin shell walls and high dimensional accuracy.
The shell mold casting process involves creating resin-bonded sand molds, called shell molds. These molds are made by coating a pattern with a resin binder. Once the binder has cured, the pattern is removed, leaving behind a hollow shell mold. This mold is then filled with molten metal, creating a high-quality component.
One of the key advantages of shell molding is the use of a resin binder, which allows for greater control over the final shape and surface quality of the component. The resin binder also creates a uniform mold surface, resulting in a superior cast surface finish.
Shell molds are typically made in two halves, which are joined together to form the complete mold. This allows for the creation of complex shapes and internal cavities. The use of multiple shell molds also provides greater flexibility and efficiency in the casting process.
The shell molding process is suitable for a variety of metal alloys, including stainless steel, and is particularly effective for casting reactive materials. The resulting component has excellent dimensional accuracy and minimal gas-related defects, making it a preferred choice for many stainless steel casting applications.
The Steps of the Shell Mold Casting Process
The shell mold casting process involves the following steps:
- Creation of a metal pattern
- Coating the pattern with a resin binder
- Sprinkling sand onto the coated pattern to create a shell mold
- Curing the binder to harden the shell mold
- Removing the pattern from the shell mold to create a hollow cavity
- Joining the two halves of the shell mold
- Pouring molten metal into the shell mold
- Cooling the mold to solidify the metal
- Breaking the mold and removing the component
At KT-Foundry, we have extensive experience in shell mold casting, allowing us to meet the most demanding specifications for precision stainless steel components. Contact us today to see how we can assist you with your casting needs.
Achieving Thin Shell Walls and Dimensional Accuracy
Shell molding is an intricate metal casting process that enables the creation of thin shell walls with high dimensional accuracy. This process is similar to sand casting, but the use of resin-bonded sand molds, known as shell molds, enables the creation of thin-walled shells easily.
Multiple shell molds can be used to achieve even thinner walls, and the process of assembling shell halves can further enhance dimensional accuracy. When casting reactive materials, it is crucial to use suitable metal alloys that can withstand high temperatures and resist corrosion. By carefully selecting the appropriate materials and techniques, a thin-walled shell can be created that meets the most demanding specifications.
The creation of thin-walled shells involves coating a pattern with a resin binder that hardens to create a shell mold. The pattern is then removed, leaving a hollow cavity that can be filled with molten metal. The cavity is then surrounded by a second shell, and the two shell halves are assembled to form a complete mold. The molten metal is poured into the mold, and once it cools and solidifies, the shell is removed to reveal the final product with precise dimensions and a superior surface finish.
The ability to achieve thin shell walls and high dimensional accuracy makes shell molding a popular choice for many stainless steel casting applications. At our foundry, we utilize shell mold casting techniques to produce precision components that meet the most rigorous specifications.
The Advantages of Shell Mold Casting
When it comes to stainless steel casting processes, shell mold casting offers numerous advantages over other casting methods. Here are some of the key benefits:
- Superior cast surface finish: The smooth surface finish produced by shell molding is unmatched by other casting processes. This is due to the fine sand used to create the mold, as well as the surrounding shell that helps to minimize gas-related defects.
- Reusable pattern: A major benefit of shell mold casting is that the pattern used to create the mold can be reused several times. This reduces the overall cost of production and ensures consistent quality.
- Lower machining costs compared to other casting processes: The dimensional accuracy achieved through shell molding means there is less material to remove during machining, thereby reducing the overall cost of production.
- Surrounding shell: The shell that surrounds the mold helps to minimize gas-related defects by providing a barrier to the atmosphere. This leads to fewer defects and higher quality castings.
- Very few gases: Shell mold casting produces very few gases during the process, making it a preferred choice for certain stainless steel casting applications.
Overall, the combination of superior surface finish, reduced machining costs, and the ability to reuse patterns make shell mold casting a preferred choice for producing high-quality stainless steel components. At KT-Foundry, we are committed to utilizing the most advanced techniques to ensure that your stainless steel castings meet the highest standards of quality and reliability.
Applications of Stainless Steel Shell Mold Casting
Stainless steel shell mold casting has found extensive applications in various industries, where the precision and strength of stainless steel castings are crucial. Let us explore some of the specific applications:
- Cylinder heads: The cylinder head is an essential component of the internal combustion engine, where it seals the top of the cylinder block. The high strength and rigidity of stainless steel castings make them suitable for cylinder head applications.
- Gear housings: Stainless steel shell mold casting is ideal for producing gear housings, where the precision and dimensional accuracy are critical to ensuring smooth and efficient gear operation.
- Connecting rods: Connecting rods are used in internal combustion engines to connect the piston to the crankshaft. The high strength, rigidity, and corrosion resistance of stainless steel castings make them an excellent choice for connecting rod applications.
These are just a few examples of the versatility of shell mold casting in delivering high-quality components for demanding applications. At our company, we use our expertise in stainless steel casting to produce precision components for various industries, meeting the most stringent quality requirements.
The Shell Mold Casting Process for Non-Ferrous Metals
Besides stainless steel, shell mold casting is ideal for non-ferrous metals like aluminum alloys. The process begins with the creation of a metal pattern that matches the desired shape of the final product. This pattern is coated with phenolic resin, which creates a hardened shell upon curing.
Compared to sand casting, shell mold casting for non-ferrous metals offers a very smooth surface finish and high dimensional accuracy. This is because of the use of a finer sand resin mixture and the creation of a thin-walled shell, which ensures precise replication of pattern details. The use of a phenolic resin binder is also ideal for non-ferrous metals as it has excellent bonding properties and high resistance to heat.
At KT-Foundry, we specialize in custom shell mold casting for non-ferrous metals, producing high-quality components with excellent dimensional accuracy. The process involves careful design and production of metal patterns, the creation of multiple shell molds, and the use of cutting-edge casting techniques. Our expertise in shell mold casting for non-ferrous metals has helped numerous clients across various industries fulfill their casting requirements with ease.
The Shell Mold Casting Process Compared to Sand Casting
When compared to sand casting, shell mold casting offers numerous advantages. Firstly, the use of resin-bonded sand molds, or shell molds, eliminates the need for a sand resin mixture, thus reducing the risk of defects due to improper sand mixing. Additionally, the creation of hardened shells offers a higher degree of dimensional accuracy, resulting in greater precision in cast components.
The surface finish of shell mold castings is superior due to the finer grain size of the resin-bonded sand used in the process. In contrast, sand casting produces rougher surfaces due to the coarseness of the sand grains. Moreover, shell mold castings require minimal post-casting machining, leading to significant cost savings for manufacturers.
Overall, the shell mold casting process has proven to be a reliable and cost-effective alternative to sand casting for producing high-quality components with superior dimensional accuracy and surface finish.
Conclusion
At KT-Foundry, we understand the importance of crafting high-quality stainless steel castings. Our expertise in shell mold casting allows us to achieve precise dimensional accuracy and superior surface finishes, resulting in top-notch components for demanding applications. Throughout this article, we have explored the intricacies of the stainless steel casting process, with a focus on the advantages of shell mold casting. We have discussed the various techniques used to achieve thin shell walls and high dimensional accuracy, and we have highlighted the versatility of the process in producing components for a range of industries. By utilizing the shell mold casting process, we can ensure the production of cost-effective, high-quality stainless steel castings with very few defects. This process offers numerous advantages over traditional sand casting, including the ability to create complex geometries, the reusability of patterns, and the superior cast surface finish. In conclusion, by partnering with KT-Foundry, you can take advantage of our expertise in shell mold casting to produce top-quality stainless steel castings that meet the most demanding specifications. Contact us today to learn how we can help you achieve your stainless steel casting goals.
FAQ
Q: What is shell mold casting?
A: Shell mold casting is a precision casting process used to produce intricate stainless steel components. It involves the use of resin-bonded sand molds, known as shell molds, which are created by coating a pattern with a resin binder.
Q: What are the advantages of shell mold casting?
A: Shell mold casting offers several advantages over other casting processes. These include superior cast surface finish, reusability of patterns, and lower machining costs compared to other casting processes. The surrounding shell also helps minimize gas-related defects.
Q: What kind of applications can stainless steel shell mold casting be used for?
A: Stainless steel shell mold casting is commonly used for applications such as cylinder heads, gear housings, and connecting rods, where precision and strength are crucial.
Q: Can shell mold casting be used for non-ferrous metals?
A: Yes, shell mold casting can be used for non-ferrous metals like aluminum alloys. It offers benefits such as achieving a smooth surface finish and utilizing suitable metal patterns and phenolic resin binders.
Q: How does shell mold casting compare to sand casting?
A: Shell mold casting offers distinct advantages over sand casting, such as the use of resin-bonded sand molds, the creation of hardened shells, and superior cast surface finish and dimensional accuracy.
Q: What are the key benefits of shell molding?
A: The key benefits of shell molding include the ability to achieve thin shell walls and high dimensional accuracy, as well as the versatility of using multiple shell molds and the precision of assembling shell halves.
Q: What materials are suitable for shell molding?
A: Shell molding is suitable for various metal alloys, including stainless steel and non-ferrous metals like aluminum alloys. The choice of material depends on the specific application requirements.
Q: Can shell mold casting be used for casting reactive materials?
A: Yes, shell mold casting can be used for casting reactive materials. However, certain considerations must be made to ensure the safety and success of the casting process.