At KT-Foundry, we understand the importance of achieving defect-free excellence in aluminum die casting. As a cost-effective method for manufacturing high-quality metal components, aluminum die casting plays a crucial role in various industries. However, the die casting process can be prone to defects that compromise the overall quality of the cast parts.
Common defects in aluminum die casting include porosity, blisters, cold shuts, misruns, shrinkage defects, sink marks, die marks, sticking, erosion, and cracks. These defects can be caused by factors such as improper mold design, incorrect temperatures, inadequate venting, and more.
Key Takeaways:
- Understanding the root causes of defects in aluminum die casting is essential for achieving defect-free excellence.
- Porosity, blisters, cold shuts, misruns, shrinkage defects, sink marks, die marks, sticking, erosion, and cracks are common defects to watch out for in aluminum die casting.
- Proper mold design, appropriate mold temperatures, controlled filling speeds, and good venting are key factors in preventing defects.
- Addressing these defects helps ensure the production of high-quality aluminum die cast components.
- KT-Foundry specializes in aluminum die casting and is committed to helping our customers achieve defect-free excellence.
With our expertise in aluminum die casting and commitment to quality, [Company Name] is dedicated to providing flawless casting solutions to our customers in a wide range of industries. Contact us today to learn more about our services and how we can help you achieve defect-free excellence in aluminum die casting.
Common Defects in Aluminum Die Casting: Porosity
Porosity is a common defect in aluminum die casting that can significantly impact the quality and integrity of the cast components. It refers to the presence of holes or voids in the solid metal, which can weaken the structural integrity and compromise the functionality of the final product. Understanding the causes of porosity and implementing effective solutions is essential for achieving defect-free excellence in aluminum die casting.
There are two main causes of porosity in aluminum die casting: solidification shrinkage and gas porosity. Solidification shrinkage occurs when the molten metal cools too quickly during the casting process, leading to shrinkage and the formation of internal voids. Gas porosity, on the other hand, happens when air or gases get trapped in the mold cavity and become entrapped in the solidified metal.
To address porosity issues, manufacturers can implement several solutions. Modifying the mold design to allow for proper venting and reducing the risk of entrapment of air or gas is crucial. Additionally, optimizing the casting operation conditions, such as controlling the temperature and ensuring a smooth metal flow, can help minimize the formation of porosity. Implementing effective degassing techniques and using suitable alloys can also contribute to reducing porosity in aluminum die casting.
By addressing the root causes of porosity and adopting the appropriate solutions, manufacturers can significantly enhance the integrity and quality of their aluminum die cast components. Minimizing porosity not only improves the overall aesthetics of the final product but also ensures its durability and performance, meeting the highest standards of defect-free excellence.

Table: Comparison of Causes and Solutions for Porosity in Aluminum Die Casting
Causes of Porosity | Solutions for Porosity |
---|---|
Solidification shrinkage due to rapid cooling | Modify mold design to optimize cooling and allow for proper venting Control casting temperature and metal flow to reduce shrinkage Implement degassing techniques and use suitable alloys |
Gas porosity caused by trapped air or gases | Improve mold design to minimize air or gas entrapment Optimize casting operation conditions for smooth metal flow Implement degassing techniques and use suitable alloys |
Addressing porosity is critical in achieving defect-free excellence in aluminum die casting. By identifying the root causes and implementing effective solutions, manufacturers can enhance the quality, durability, and performance of their cast components, ensuring customer satisfaction and meeting the highest industry standards.
Common Defects in Aluminum Die Casting: Blisters
Blisters are a commonly encountered defect in the aluminum die casting process. These defects manifest as raised bubbles on the surface of the cast component and are typically caused by gas porosity. When high-pressure air or gas becomes trapped within the casting, it exerts force on the material, resulting in the formation of blisters.
To address the issue of blisters in aluminum die casting, several solutions can be employed. One effective approach is to adjust the mold cooling rate, ensuring that the cooling process is neither too slow nor too rapid. Improving water flow and increasing cooling time can also help minimize the risk of blisters. Additionally, altering the temperature of the alloy being cast can reduce thermal differences and subsequently lower the likelihood of blister formation.
By implementing these solutions and closely monitoring the casting process, manufacturers can significantly reduce the occurrence of blisters in aluminum die casting, resulting in higher-quality and defect-free components.
“Effective control over the cooling rate and temperature, along with proper mold design and venting, are crucial to address the issue of blisters in aluminum die casting.” – KT-Foundry
Table: Solutions for Addressing Blisters in Aluminum Die Casting
Cause of Blisters | Solution |
---|---|
Gas porosity | Adjust mold cooling rate |
Improve water flow | |
Increase cooling time | |
Change temperature of the alloy |

Common Defects in Aluminum Die Casting: Cold Shuts
In the process of aluminum die casting, cold shuts are a common defect that can impact the quality of the final cast components. Cold shuts occur when molten metal flows into the mold via multiple channels but cools too quickly, resulting in incomplete fusion of the metal streams. This leads to visible indentations or gaps on the surface of the cast component, affecting both the aesthetics and structural integrity.
The root causes of cold shuts can vary, but they are often attributed to poor gating system design, inadequate material fluidity, or low pouring and mold temperatures. When the molten metal does not merge seamlessly, it leaves behind visible defects that can compromise the performance of the cast component.
To prevent cold shuts in aluminum die casting, manufacturers can take several steps. Modifying the gating system design can help ensure proper flow and distribution of molten metal throughout the mold, reducing the risk of incomplete fusion. Increasing the pour temperatures can also improve the fluidity of the metal, allowing for better flow and reducing the chances of cold shuts. Additionally, improving the gas permeability of the mold can help create a more uniform and controlled cooling environment, reducing the formation of cold shuts.

Table: Solutions for Cold Shuts
Cause | Solution |
---|---|
Poor gating system design | Modify the gating system design to ensure proper flow and distribution of molten metal |
Lack of material fluidity | Increase pour temperatures to improve fluidity |
Low pouring or mold temperatures | Optimize mold temperature to reduce the risk of cold shuts |
Common Defects in Aluminum Die Casting: Misruns
Misruns are a common defect in the aluminum die casting process, where the molten metal fails to completely fill the mold, resulting in incomplete components. This defect can occur due to various factors, including poor mold design, inadequate gating system design, or insufficient fluidity of the molten metal.
Causes of misruns in aluminum die casting can be attributed to factors such as improper mold filling, excessive turbulence during the casting process, or inadequate venting. These issues can lead to incomplete filling of the mold, resulting in misruns.
Causes of Misruns in Aluminum Die Casting:
- Poor mold design
- Inadequate gating system design
- Insufficient fluidity of the molten metal
To address the issue of misruns, manufacturers should carefully evaluate the mold design and gating system design. By making necessary modifications to improve the mold filling and reduce turbulence during the casting process, it is possible to prevent misruns and ensure complete filling of the mold.
Solutions for Misruns in Aluminum Die Casting:
- Optimize mold design and gating system design
- Ensure sufficient fluidity of the molten metal
- Control and reduce turbulence during the casting process
By implementing these solutions, manufacturers can minimize the occurrence of misruns in aluminum die casting, resulting in high-quality and fully completed components.
Causes of Misruns | Solutions for Misruns |
---|---|
Poor mold design | Optimize mold design and gating system design |
Inadequate gating system design | Ensure sufficient fluidity of the molten metal |
Insufficient fluidity of the molten metal | Control and reduce turbulence during the casting process |
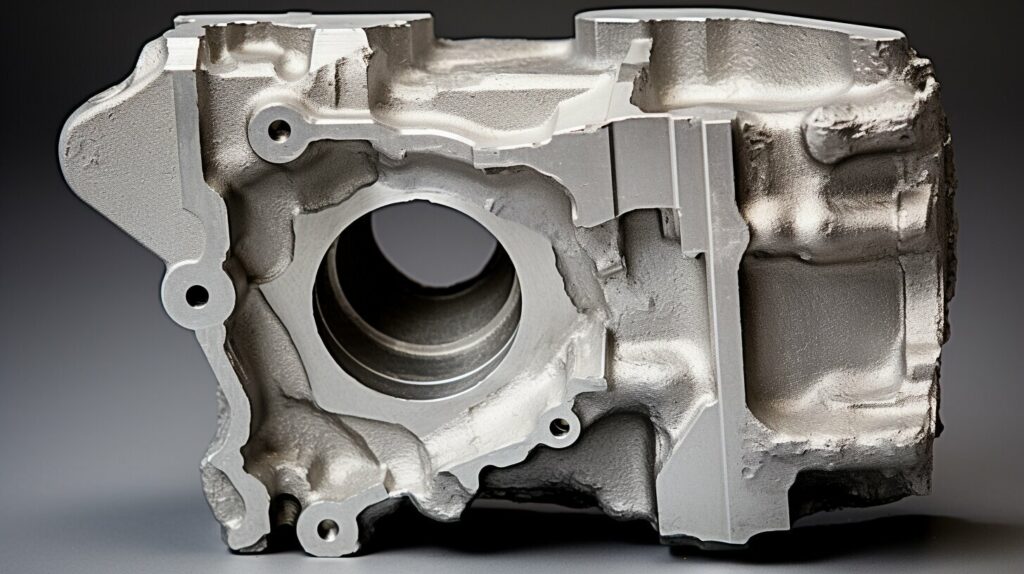
Other Defects in Aluminum Die Casting: Shrinkage and Sink Marks
In addition to the common defects mentioned earlier, aluminum die casting can also suffer from shrinkage defects and sink marks. Shrinkage defects occur due to the reduced density of the metal during solidification, leading to voids or cavities in the cast components. Sink marks, on the other hand, are depressions that appear on the surface of the castings.
Shrinkage defects can be caused by factors such as improper gating design, inadequate cooling, or excessive alloy shrinkage. To prevent shrinkage defects, manufacturers can take several measures. First, optimizing the design of the casting can help ensure uniform solidification and minimize the risk of shrinkage. Controlling mold temperature is also crucial in preventing shrinkage defects. By maintaining the proper temperature, manufacturers can reduce the cooling rate and minimize the formation of voids. Additionally, adjusting the pouring temperature and using alloys with lower shrinkage can also help prevent shrinkage defects in aluminum die casting.
Sink marks, on the other hand, occur when the mold is opened too early, causing depressions on the surface of the cast components. To prevent sink marks, manufacturers need to ensure that the mold is properly cooled and solidified before opening it. Additionally, optimizing the gating system design can help minimize the formation of sink marks. By adjusting the placement and size of the gates, manufacturers can control the flow of molten metal and reduce the risk of sink marks.
Cause of Shrinkage Defects | Solution for Shrinkage Defects |
---|---|
Improper gating design | Optimize casting design for uniform solidification |
Inadequate cooling | Control mold temperature to reduce cooling rate |
Excessive alloy shrinkage | Adjust pouring temperature and use alloys with lower shrinkage |
Cause of Sink Marks | Solution for Sink Marks |
---|---|
Mold opened too early | Ensure proper cooling and solidification before opening the mold |
Improper gating system design | Optimize gating system design to control molten metal flow |
By addressing shrinkage defects and sink marks, manufacturers can further enhance the quality of their aluminum die castings. By implementing the appropriate design modifications, optimizing mold temperatures, and controlling the gating system, manufacturers can minimize the occurrence of these defects and achieve defect-free excellence in aluminum die casting.
“Optimizing mold temperature is crucial in preventing shrinkage defects.”
Key Takeaways:
- Shrinkage defects in aluminum die casting are caused by factors such as improper gating design, inadequate cooling, or excessive alloy shrinkage.
- To prevent shrinkage defects, manufacturers can optimize casting design, control mold temperature, and adjust pouring temperature and alloy selection.
- Sink marks occur when the mold is opened too early, and they can be prevented by ensuring proper cooling and solidification, as well as optimizing the gating system design.
- Addressing shrinkage defects and sink marks is crucial in achieving defect-free excellence in aluminum die casting.

Other Defects in Aluminum Die Casting: Die Marks, Sticking, Erosion, and Cracks
While porosity, blisters, cold shuts, and misruns are common defects in aluminum die casting, there are also other issues that can occur during the process. These defects include die marks, sticking, erosion, and cracks. Understanding the causes of these defects and implementing appropriate solutions is crucial to achieving defect-free excellence in aluminum die casting.
Die marks are traces left on the surface of the castings due to contact with the die-casting mold cavity. These marks can be caused by factors such as improper mold release agents, insufficient cooling, or excessive contact pressure. To reduce the occurrence of die marks, manufacturers can optimize mold maintenance, ensure proper alignment and lubrication, and control the temperature and pressure during the casting process.
Sticking refers to unintended fusion between the molten metal and the die surface. This defect can occur when the die surface is too rough or when the temperature of the molten metal is too high. To prevent sticking, manufacturers can improve the surface finish of the die, apply suitable release agents, and control the temperature and flow rate of the molten metal.
Erosion occurs when the turbulent flow of molten metal causes wear and tear on the mold surface. This defect can lead to reduced mold life and inferior casting quality. Manufacturers can reduce erosion by optimizing the gating system design, controlling the flow rate of the molten metal, and using mold materials with higher resistance to erosion.
Cracks can also appear on the surface of the castings, often in a linear or wavy pattern. These cracks can be caused by factors such as thermal stresses, material shrinkage, or improper mold design. To prevent cracks, manufacturers can optimize the cooling and spraying techniques, control the mold temperature, and ensure uniform solidification of the molten metal.
Table: Comparison of Causes and Solutions for Die Marks, Sticking, Erosion, and Cracks in Aluminum Die Casting
Defect | Causes | Solutions |
---|---|---|
Die Marks | Improper mold release agents Insufficient cooling Excessive contact pressure | Optimize mold maintenance Ensure proper alignment and lubrication Control temperature and pressure |
Sticking | Rough die surface High temperature of the molten metal | Improve die surface finish Apply suitable release agents Control temperature and flow rate |
Erosion | Turbulent flow of molten metal Inadequate mold materials | Optimize gating system design Control flow rate of molten metal Use erosion-resistant mold materials |
Cracks | Thermal stresses Material shrinkage Improper mold design | Optimize cooling and spraying techniques Control mold temperature Ensure uniform solidification |
By addressing these defects and implementing the appropriate solutions, manufacturers can achieve high-quality aluminum die castings with fewer flaws. At KT-Foundry, we are committed to providing flawless casting solutions to our customers. Contact us today to learn more about our aluminum die casting services and how we can help you achieve defect-free excellence.
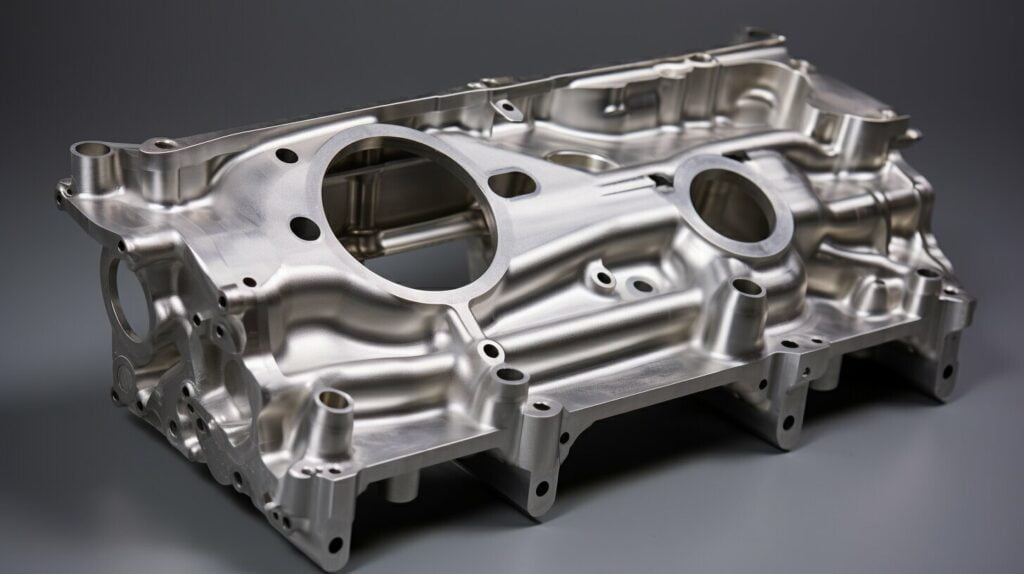
Conclusion
Achieving defect-free excellence in Aluminum Die Cast production requires a comprehensive understanding of the common defects that can occur and the corresponding solutions. By addressing issues such as porosity, blisters, cold shuts, misruns, shrinkage defects, sink marks, die marks, sticking, erosion, and cracks, manufacturers can ensure the production of high-quality components.
To prevent these defects, proper mold design, appropriate mold temperatures, controlled filling speeds, and good venting are essential. By implementing these measures, manufacturers can minimize the occurrence of defects and achieve defect-free excellence in Aluminum Die Cast production.
At KT-Foundry, we are committed to providing flawless casting solutions to our customers in various industries. With our expertise in Aluminum Die Casting and dedication to quality, we offer customized services to help you achieve defect-free excellence. Contact us today to learn more about our services and how we can assist you in preventing flaws in Aluminum Die Cast production.
FAQ
What are some common defects in aluminum die casting?
Some common defects in aluminum die casting include porosity, blisters, cold shuts, misruns, shrinkage defects, sink marks, die marks, sticking, erosion, and cracks.
What causes porosity in aluminum die casting?
Porosity in aluminum die casting can be caused by solidification shrinkage or gas porosity. Solidification shrinkage occurs when the molten metal cools too quickly, causing it to shrink and create voids. Gas porosity is caused by trapped air or gas in the mold during the casting process.
How can porosity in aluminum die casting be prevented?
To prevent porosity, manufacturers can modify the mold design, improve casting operation conditions, and ensure proper venting to reduce the risk of porosity.
What causes blisters in aluminum die casting?
Blisters in aluminum die casting are caused by gas porosity. When high-pressure air or gas is trapped within the casting, it pushes the material outward, resulting in blisters.
How can blisters in aluminum die casting be prevented?
Blisters can be prevented by adjusting the mold cooling rate, improving water flow, increasing cooling time, or changing the temperature of the alloy to reduce thermal differences.
What causes cold shuts in aluminum die casting?
Cold shuts, also known as cold laps, occur when molten metal flows into the mold via multiple channels but cools too quickly. This can be caused by poor gating system design, lack of material fluidity, or low pouring or mold temperatures.
How can cold shuts in aluminum die casting be prevented?
Cold shuts can be prevented by modifying the gating system, increasing pour temperatures, and improving the mold’s gas permeability.
What causes misruns in aluminum die casting?
Misruns occur when the molten metal cools too quickly and does not completely fill the mold, resulting in incomplete components. Similar conditions as cold shuts, such as poor mold design, gating system design, or fluidity of the molten metal, can cause misruns.
How can misruns in aluminum die casting be prevented?
To prevent misruns, manufacturers should carefully evaluate the mold design, gating system design, and fluidity of the molten metal to ensure complete filling of the mold and avoid incomplete components.
What are some other defects in aluminum die casting?
Other defects in aluminum die casting include shrinkage defects, sink marks, die marks, sticking, erosion, and cracks.
How can shrinkage defects and sink marks in aluminum die casting be prevented?
Shrinkage defects can be prevented by optimizing the design of the casting, ensuring uniform solidification, controlling mold temperature, and using an appropriate pouring temperature. Sink marks can be prevented by avoiding opening the mold too early and causing depressions on the surface of the cast component.
What causes die marks, sticking, erosion, and cracks in aluminum die casting?
Die marks are traces left on the surface of the castings due to contact with the die-casting mold cavity. Sticking refers to unintended fusion between the molten metal and the die surface. Erosion occurs when the turbulent flow of molten metal causes wear and tear on the mold surface. Cracks can appear on the surface of the castings, often in a linear or wavy pattern.
How can die marks, sticking, erosion, and cracks in aluminum die casting be prevented?
Die marks can be reduced by improving mold maintenance. Sticking can be resolved by optimizing gating system design. Erosion can be minimized by ensuring proper cooling and spraying techniques. Cracks can be prevented by addressing the causes of cracks and implementing appropriate solutions.