Die casting and sand casting are two popular methods used in producing aluminum castings. While both processes involve pouring molten metal into a mold, there are significant differences in how the molds are created and how the metal is handled. Though these popular methods have different approaches, the aluminum castings produced still have the same mechanical properties.
In this article, we will explore the definitions of each method, their differences, and the comparison of sand casting vs die cast parts. Whether you are a manufacturer looking to optimize your casting process or simply learning more about the two casting methods, this article will provide valuable insights into casting aluminum alloys.
Quick Definition of Die Casting Process
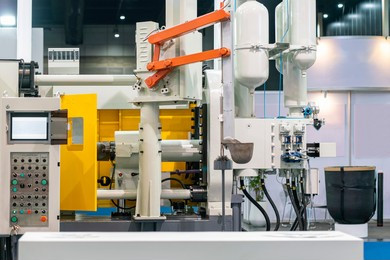
Aluminum die casting is a popular manufacturing process that involves injecting molten aluminum into a mold cavity under high pressure. This results in a high-quality, precise, and detailed casting that can be used in various industries.
The liquid metal is injected into the metal mold cavity using an extreme-pressure injection system. The aluminum quickly solidifies and takes on the shape of the mold. The mold is then cooled, and as the metal solidifies, it is ejected from the metal molds.
Applications of Die Cast Aluminum
Aluminum parts made from die casting are ideal for producing high-volume, intricate parts that require tight tolerances, such as automotive parts, electronic components, and household appliances.
Quick Definition of Sand Casting Process
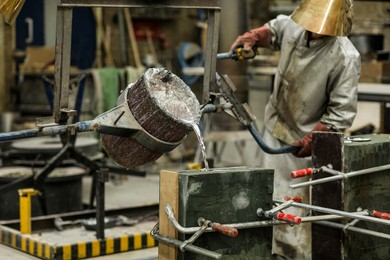
Aluminum sand casting is a popular method for manufacturing aluminum components. It is a cost-effective and efficient way to create complex shapes and designs that cannot be achieved through other casting methods.
Aluminum sand casting involves pouring molten aluminum into sand-casting molds. The sand mold is created by packing sand around a desired pattern. It is then removed, leaving behind a cavity in the shape of the pattern. Molten aluminum is poured into the cavity, and once it cools and solidifies, the sand is broken away to reveal the final product.
Applications of Sand Cast Aluminum
Sand casting can produce low-volume, large parts that do not require tight tolerances, such as engine blocks, pump housings, and valve bodies.
Primary Difference between The Two Casting Processes of Cast Aluminum
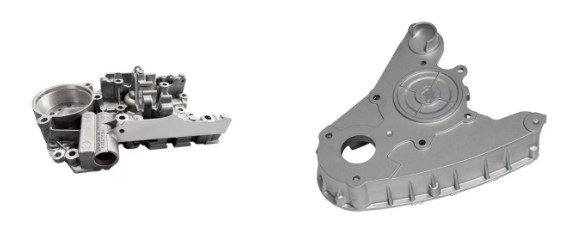
Materials Used for Molds
The process of aluminum die casting begins with creating a mold cavity. This can be done through various methods, such as CNC machining, 3D printing, or manual casting. Die casting requires a metal mold created using a computer-aided design (CAD) program. The mold is then machined to the desired shape and size. It requires precise preparation of the mold, which can take several weeks to create.
The molds used in die casting are typically made of steel and are designed to withstand high temperatures and pressures. It can be reused and immediately ready for another die-casting process.
Sand casting uses a mold made of sand, which is packed around a pattern of the desired part. It is a simpler process than die casting and requires less preparation time.
Entire Process
Die casting involves injecting molten metal into a metal mold, where it solidifies and takes the shape of the mold. This method is commonly used for high-volume production of small to medium-sized parts. The process is also highly automated.
Sand casting involves packing a mixture of sand and a bonding agent around a pattern representing the shape of the desired part. Molten metal is then poured into the mold, which is allowed to cool and solidify before the sand is removed. Sand casting is typically used for the low-volume production of large complex parts.
Sand castings, on the other hand, allow for greater flexibility in the size and shape of the parts that can be produced. It also allows for using a wider range of alloys, including those that are difficult to machine or have high melting points.
Overall Cost
Die casting is typically more expensive than sand casting due to the higher upfront costs associated with tooling and equipment.
Sand casting, however, generally costs less than die casting, as the molds are low-cost and easier to produce. However, the resulting metals may have more variability and require more post-processing work.
The choice between die casting and sand casting will depend on the project’s specific requirements. If precision is critical and the volume of parts to be produced is large enough to justify the tooling costs, die casting may be the better option. If cost is a primary concern and the parts can tolerate some variability, sand casting may be the more economical.
Mass Production Efficiency
Die casting allows for faster cycle times, meaning more parts can be produced in less time. Additionally, die-casting molds are typically made of steel, allowing for longer mold life; therefore, more parts can be produced before the mold needs to be replaced.
On the other hand, sand casting typically requires more finishing work to remove excess material and achieve the desired surface finish, which can slow down the production process.
Comparison of Die Casting vs Sand Casting Final Product
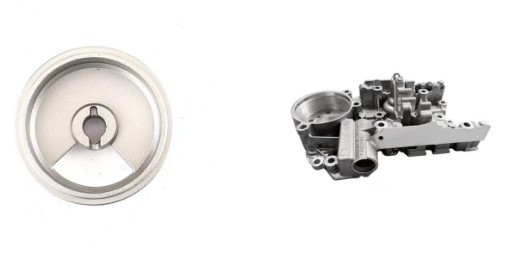
Surface Finish
Due to the high pressure applied to the molten aluminum, die casting produces parts with a smooth surface finish.
Sand casting, on the other hand, may not produce as smooth of a surface finish due to the texture of the sand mold used.
Dimensional Accuracy
Die casting is when molten metal is injected into a steel mold, or die, under high pressure. This results in a highly accurate and precise casting with minimal post-machining required.
While sand casting is more flexible in terms of mold design, it tends to have lower dimensional accuracy due to the inherent variability of the sand mold.
Machining Requirements
The die-casting process results in a near-net-shape part that requires minimal machining. Die castings can often be used as-is, with only minor surface finishing required.
Sand castings typically require more machining than die castings, as the sand molds are not as precise as die-cast molds. Sand castings may require additional machining to achieve the desired dimensions, surface finish, and other properties.