At our company, we understand the importance of a reliable and long-lasting pump housing. That’s why we recommend cast iron pump housing for demanding applications that require durability and performance. Cast iron pump housings offer a superior level of strength and resistance to wear and corrosion, making them an ideal choice for a wide range of industries.
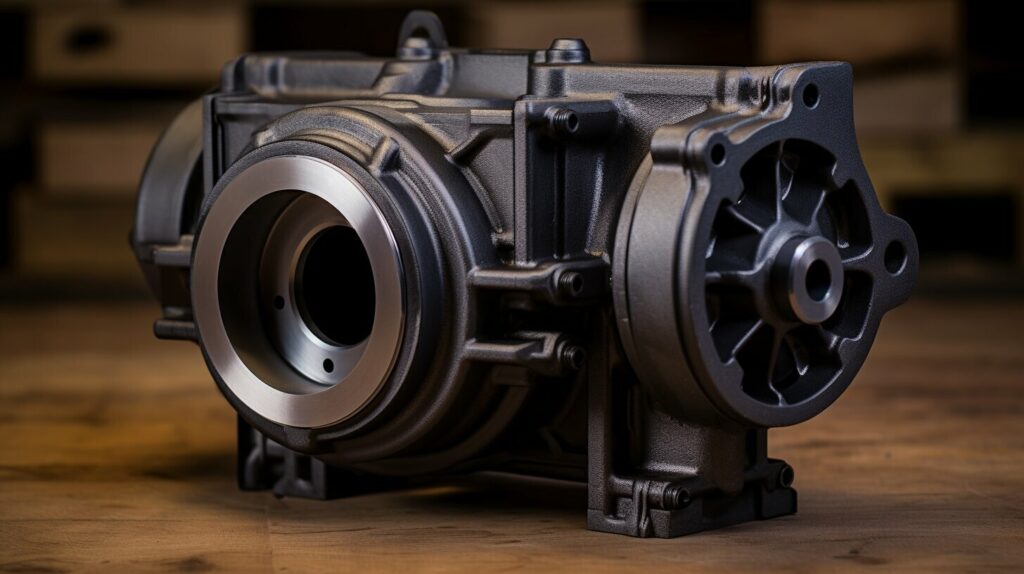
Key Takeaways:
- Cast iron pump housing is a reliable and durable choice for demanding applications.
- Cast iron pump housing offers superior strength and resistance to wear and corrosion.
- Choosing cast iron pump housing can enhance performance and increase longevity.
The Advantages of Cast Iron Pump Housing
When it comes to pump housing, choosing the right material is crucial for ensuring the long-term performance and durability of your equipment. Cast iron has become a popular choice due to its many advantages, which make it a reliable and cost-effective option for demanding applications.
Superior Durability
One of the primary reasons why cast iron is an excellent choice for pump housing is its exceptional durability. Cast iron is a hard, strong material that can withstand high levels of stress and heavy use without cracking or deforming. This durability makes it an excellent choice for pumps that need to perform in harsh conditions or frequently handle abrasive materials.
Compared to other materials such as plastic or aluminum, cast iron is much less likely to wear down or degrade over time. This means that cast iron pump housings can provide reliable and consistent performance for years, making it an excellent investment for businesses and organizations that rely on pumps for their operations.
Resistance to Corrosion and Wear
Another benefit of cast iron pump housings is their resistance to corrosion and wear. Cast iron is highly resistant to rust and other forms of corrosion, which helps to prevent damage and extend the lifespan of the pump housing. In addition, cast iron is also resistant to wear, which means that it can handle repeated use without suffering from excessive damage or degradation.
Ability to Withstand High Pressure and Temperature
Cast iron has high tensile strength and can withstand high levels of pressure and temperature without suffering from deformation or failure. This makes it a reliable choice for pumps that need to handle high-pressure applications or handle fluids at high temperatures. Cast iron pump housings can handle pressures of up to 300 psi, making it a suitable choice for many different types of pumps.
Overall, the advantages of cast iron pump housings make them a popular choice for a wide range of applications. Their superior durability, resistance to corrosion and wear, and ability to withstand high pressure and temperature make them an excellent investment for businesses and organizations that rely on pumps for their operations.
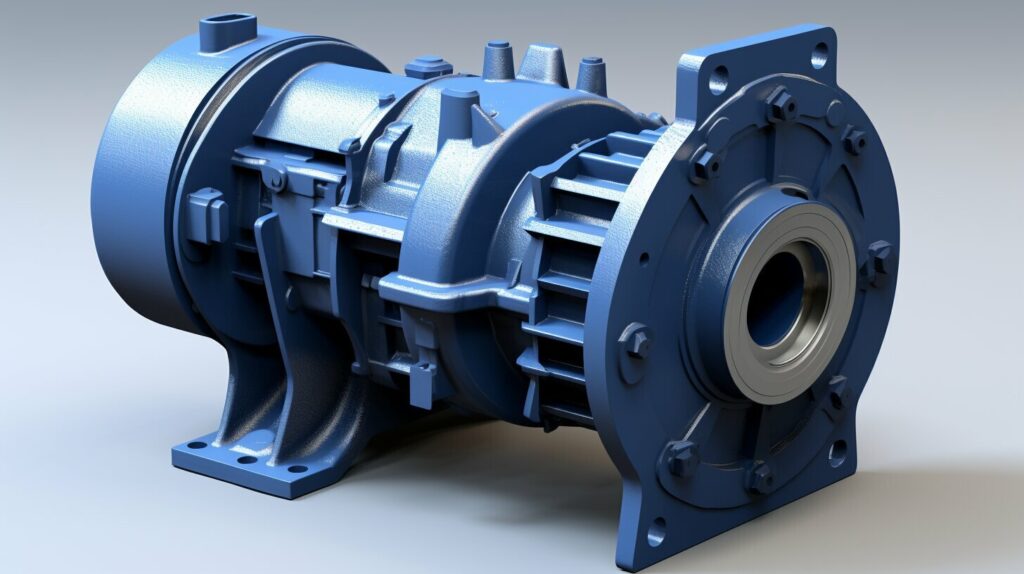
The Casting Process: Creating Cast Iron Pump Housings
At our company, we take pride in using the highest quality materials and processes to create cast iron pump housings that meet the rigorous demands of our customers. The casting process is a critical step in the creation of these durable and high-performance components.
Firstly, the process begins by creating a sand mold that is shaped to match the desired dimensions of the pump housing. The sand mold is then coated with a refractory material to enhance the mold’s ability to withstand the high temperatures involved in the casting process.
Next, molten cast iron is poured into the sand mold, filling the spaces and taking the shape of the mold. Once the mold is filled, the cast iron is left to cool and solidify, a process that may take several hours depending on the size and complexity of the casting.
After the cast iron has cooled and solidified, the sand mold is broken away to reveal the freshly cast pump housing. The housing may then undergo additional finishing and machining processes to ensure it meets the desired specifications and quality standards.
Casting Process Steps | Description |
---|---|
Create Sand Mold | A mold is created from sand to match the dimensions of the pump housing. |
Coat with Refractory Material | The sand mold is coated with refractory material to enhance its ability to withstand high temperatures. |
Pour Molten Cast Iron | Molten cast iron is poured into the sand mold, filling the spaces and taking the shape of the mold. |
Cool and Solidify | The cast iron is left to cool and solidify, a process that may take several hours. |
Break Away Sand Mold | The sand mold is broken away to reveal the freshly cast pump housing. |
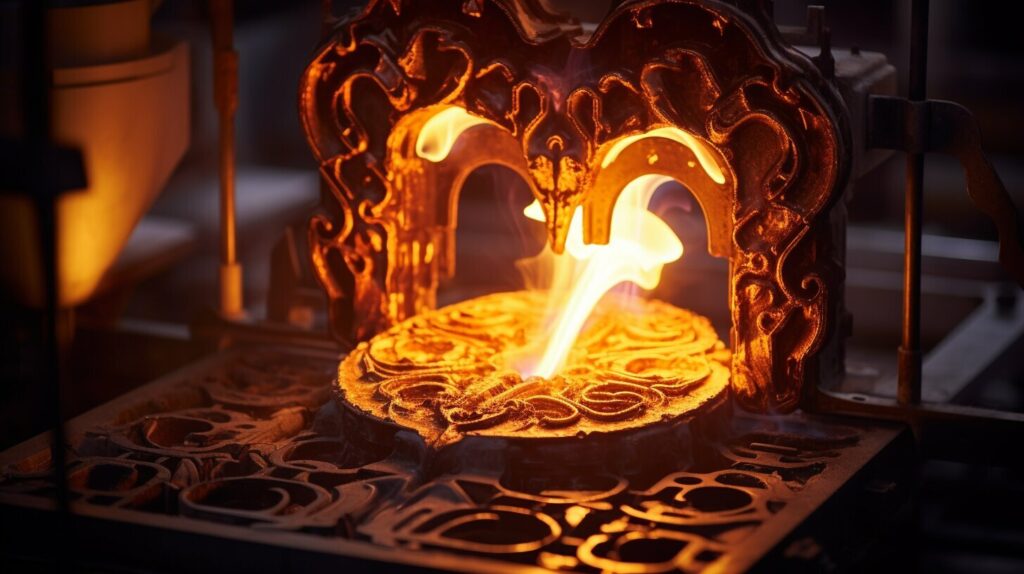
The casting process is a complex and precise method of creating cast iron pump housings that are durable and of a high quality. At our company, we take every step necessary to ensure that our cast iron pump housings meet the requirements and exceed the expectations of our customers.
The Strength and Performance: Cast Iron Pump Housing vs. Other Materials
When it comes to pump housing materials, cast iron stands out as a top performer for its exceptional strength and durability. In fact, compared to other materials such as carbon steel and bronze, cast iron pump housing offers superior performance in demanding applications.
One of the main advantages of cast iron pump housing is its ability to withstand high pressure and temperature. Cast iron is also highly resistant to corrosion and wear, making it an ideal choice for industrial and heavy-duty applications where downtime and maintenance costs must be minimized.
Composed mainly of iron, carbon, and silicon, cast iron is known for its high carbon content, which provides it with a unique combination of ductility, hardness, and strength. Its microstructure consists of graphite flakes embedded in a matrix of iron, which create an interlocking structure capable of withstanding significant stresses.
When compared to carbon steel, cast iron offers several advantages. While carbon steel is stronger and more rigid than cast iron, it is also more brittle and prone to cracked under high stress. Cast iron, on the other hand, is more ductile and able to withstand external forces without breaking. For this reason, cast iron is an ideal choice for applications where shock resistance is critical.
Bronze is also a candidate for pump housing but lacks the superior strength and durability offered by cast iron. Bronze is softer than cast iron, which makes it more prone to wear and deformation over time. Cast iron can handle heavier loads and has better corrosion resistance, making it a better choice for harsh environments where reliability is key.
Overall, if you are looking for strength, durability, and reliability, cast iron pump housing is the way to go. Its ability to withstand high pressure, temperature, and corrosive environments make it an ideal choice for a wide range of applications.
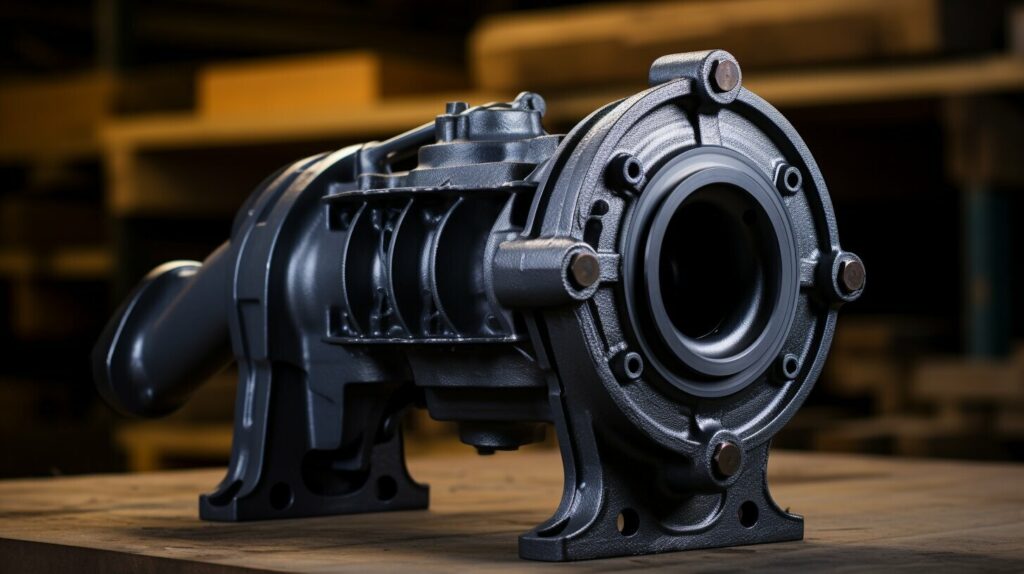
The Casting Process: Creating Cast Iron Pump Housings
Creating a cast iron pump housing involves a casting process that utilizes sand molds to create the desired shape of the housing. The process starts with the selection of the proper sand material to create the mold. The sand is then packed around a pattern of the pump housing, and the pattern is removed to create the mold cavity.
The molten cast iron is poured into the mold cavity and allowed to cool and solidify. After solidification, the sand mold is broken away from the housing, leaving behind a rough casting that requires additional processing to achieve a finished component.
The casting process allows for precise and complex shapes to be created, providing flexibility in design and the ability to create components that cannot be easily machined. This process also ensures that the resulting housing has a consistent and homogenous structure, with no weaknesses or defects that could compromise its strength and reliability.
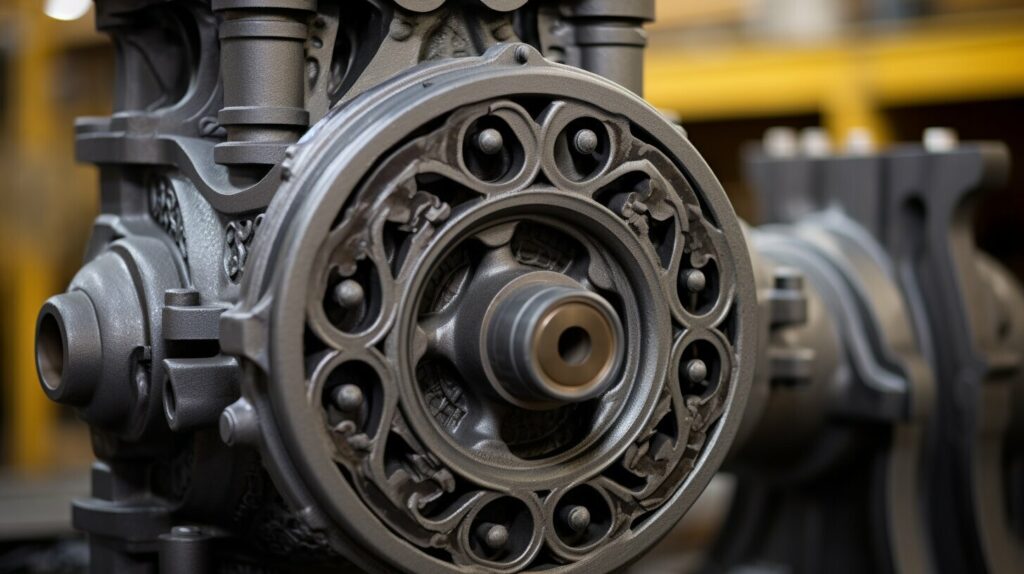
At our company, we follow strict quality control measures during the casting process to ensure that all cast iron pump housings meet the highest standards of performance and durability. Our experienced team of professionals ensures that each casting is thoroughly inspected for any defects or inconsistencies before it is approved for use.
By using the casting process to create cast iron pump housings, we are able to provide our customers with high-quality components that meet their exact specifications.
The Importance of Choosing a Cast Iron Pump Housing
As we have discussed, a cast iron pump housing offers a range of advantages over other materials such as carbon steel and bronze. Its superior durability, resistance to wear and corrosion, and ability to withstand high pressure and temperature make it an ideal choice for demanding applications.
When selecting the right cast iron pump housing for your requirements, it is essential to consider factors such as case sizes, compatibility with different pump parts, material specifications, and the quantity and performance requirements. This will ensure that you have a pump housing that not only meets your current needs but is also suitable for any future requirements.
Case Sizes
Cast iron pump housings come in a range of case sizes to meet different requirements. It is important to choose the right size for your pump to ensure optimal performance and efficiency. Choosing a housing that is too small or too large can affect the performance and longevity of your pump.
Compatibility with Pump Parts
It is important to ensure that your cast iron pump housing is compatible with the other pump parts you are using. This includes components such as impellers, motors, and seals. Choosing a housing that is incompatible with your other parts can lead to reduced performance and premature failure.
Material Specifications
Cast iron pump housings come in different materials and grades. It is important to choose a material that is suitable for your application. For example, some applications may require a higher grade of cast iron for increased durability and strength.
Quantity and Performance Requirements
When selecting a cast iron pump housing, it is important to consider your quantity and performance requirements. Choosing a housing that is designed for a lower performance or quantity than required can lead to increased wear and premature failure. On the other hand, choosing a housing that is designed for a higher performance or quantity than required can result in unnecessary costs.
Investing in a high-quality cast iron pump housing can help enhance the performance and longevity of your pump. We recommend carefully considering your requirements and selecting a housing that is designed to meet those needs for optimal results.
In the realm of industrial manufacturing, experience and expertise play a pivotal role in determining the quality and reliability of products. KT-Foundry, a distinguished name in the field, has established itself as a leading manufacturer of Cast Iron Pump Housing, leveraging its rich experience and commitment to customer satisfaction.
FAQ
Q: What are the benefits of using cast iron pump housing?
A: Cast iron pump housing offers enhanced performance and longevity. It is highly durable, resistant to corrosion and wear, and can withstand high pressure and temperature.
Q: What advantages does cast iron material have for pump housing?
A: Cast iron is known for its superior durability and strength. It is a reliable and long-lasting material that can handle demanding applications. It is also resistant to corrosion, making it ideal for pump housings.
Q: How is cast iron pump housing created?
A: Cast iron pump housing is created through a casting process. This involves creating a sand mold, pouring molten cast iron into the mold, and allowing it to cool and solidify before removing the mold.
Q: How does cast iron pump housing compare to other materials?
A: Cast iron pump housing is stronger and more durable compared to materials like carbon steel and bronze. It offers reliable performance and can withstand demanding conditions for extended periods.
Q: How do I select the right cast iron pump housing for my requirements?
A: When selecting a cast iron pump housing, it is important to consider factors such as case size, compatibility with pump parts, material specifications, and your specific quantity and performance requirements.