Zinc alloys and stainless steel are two common choices that many individuals find themselves undecided between when it comes to selecting the appropriate metal for a casting component. Both of these components are metal alloys, which are formed by carefully combining metal with other alloys.
All options offer benefits, but how can you decide which one is better for you? In this article, we’ll be taking a closer look at the properties and uses of the two alloys, so you can decide which is best for the job.
The Basics of Zinc Alloys
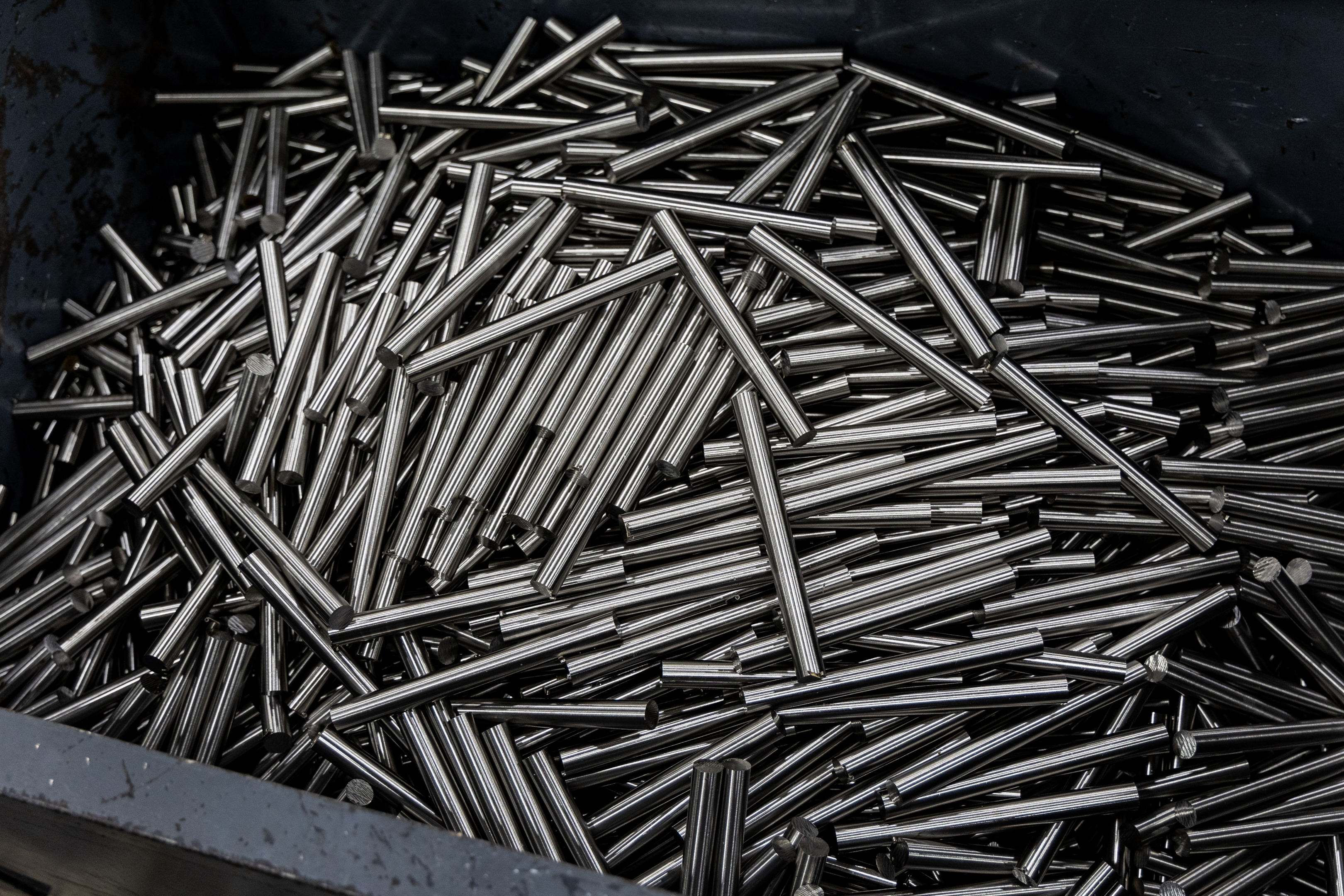
The exact composition of a zinc alloy will vary depending on the properties desired by the manufacturer. Zinc carbonate is an essential component in many alloys, including zinc-based alloys.
It is produced as a result of the reaction of zinc with carbon dioxide in the presence of humid air, which results in the formation of a protective coating on the surface of the zinc, which acts against zinc rust.
The malleability of zinc alloys makes them ideal for the intricate designs used in coins and making jewelry. The alloy metals in zinc alloy jewels can also be gold plated, making it one of the best jewelry metals. However, using too much copper in zinc alloy jewelry can cause allergic reactions in earring wearers.
Zinc aluminum is a common kind of zinc alloy that is widely used. This versatile alloy is made up of zinc and aluminum and may be used in a number of situations. Since it is so resistant to corrosion, it is an excellent choice as a material for products that are used outside.
Other types of zinc alloys that are quite well-known include soft solder, nickel silver, nickel copper, and German silver.
Advantages of Using Zinc Alloy
Low Production Costs
One of the main reasons for the inexpensive process is the low cost of the raw materials used to make zinc alloys. Zinc is one of the least expensive and abundant in natural deposits compared to other metals. This means that manufacturers can source this heavy element for their alloys cheaply.
Zinc alloys use less time required to make the desired shape, reducing production costs. It can also be used without a protective coating, sometimes increasing production costs.
Durable Against Corrosion
Zinc, when combined with other metals, produces an alloy that is far more resistant to corrosion than any of the metals that make up the alloy.
How zinc alloys are made contributes to its corrosion resistance. During the manufacturing process, zinc alloys are exposed to high temperatures and pressure, which helps to create a strong and durable material. Because of this, the zinc metal becomes more corrosion-resistant.
High Strength and Ductility
The strength of zinc alloys comes from pure-form zinc, a relatively strong metal. The other metals in the alloy make the metal durable and provide additional strength and ductility.
This soft metal’s high strength and ductility make them ideal for applications where durability and flexibility are essential. For example, zinc alloys are materials used for components such as suspension arms, brackets, and wheels. In the aerospace industry, zinc alloys are used for aircraft parts, such as landing gear, due to their strength and ability to withstand high temperatures.
Disadvantages of Using Zinc Alloy
Poor Heat Resistance
Zinc alloys are unsuitable for applications requiring high temperatures or thermal stability compared to most metals. It is due to their low melting point, low thermal conductivity, and tendency to expand and contract.
The melting point of zinc alloys ranges from 400-430°C (752-806°F), compared to other metals, such as aluminum alloys, which have melting points of 650-720°C (1202-1320°F).
When exposed to high temperatures, zinc alloys can expand, causing components to become loose and unstable. This can lead to further problems, such as cracking and failing components.
Limited Life Expectancy
The main reason for zinc alloy’s limited life expectancy is that zinc corrodes. It is a relatively reactive metal, which can easily react with environmental factors, such as oxygen and moisture. This can result in the formation of zinc oxide, which can cause the metal to become brittle and corrode over time.
Zinc alloys can also suffer from a condition known as galvanic corrosion. This occurs when two different metal components are connected in an electrical circuit. Different metals, like galvanized steel, can transfer electrons between each other, which can cause the zinc alloy to corrode more rapidly than other metals.
Defining Stainless Steel
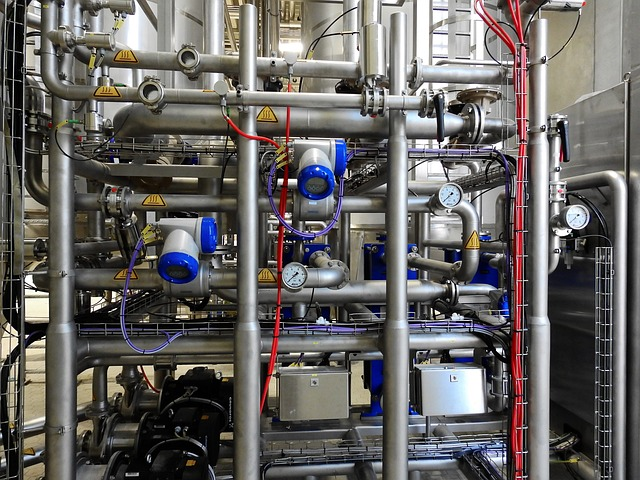
Stainless steel alloys are strong, durable, and corrosion-resistant alloys of iron, chromium, and other metals.
It is non-magnetic and known as tough material noted for its corrosion resistance compared to other grades. It is also the most ductile and formable stainless steel, making it the best choice for stainless steel jewelry.
One of the most common grades is ferritic stainless steel, which reacts to magnets. On the other hand, another grade is austenitic stainless steel, which has better protection to corrosion.
Martensitic stainless steel has the highest hardness and strength of any stainless steel, although it is not as corrosion-resistant as other grades.
Advantages of Stainless Steel
Corrosion Resistant Steel
The surface of the steel has a protective film called chromium content. It prevents oxygen from reacting with the steel, which eventually forms rust. It is used in food processing, chemical processing, marine applications, and medical equipment.
Thermally Stable
Stainless steel is able to tolerate high temperatures without suffering considerable degeneration even when it is subjected to these temperatures. This makes it an ideal choice in extreme environments where other metals may experience damage from the heat.
The heat resistance of stainless steel makes it an ideal choice for many high-temperature applications such as cookware, automotive components, industrial machinery, and furnaces. It can also be used to create fireplaces, ovens, and BBQ grills.
Low Maintenance
It is easy to clean and care for. This is because it is non-porous and does not absorb liquids, which makes it easy to wipe clean with a damp cloth and soap. This means stainless steel items do not require regular polishing or waxing to maintain their appearance.
Additionally, stainless steel items are not prone to rusting, eliminating the need for regular repainting or refinishing.
Disadvantages of Stainless Steel
Expensive Production Costs
When it comes to the production of casting alloys, stainless steel is a relatively expensive option. The primary reason is that it requires more energy and resources to manufacture than other metals.
Producing stainless steel requires much energy and labor, which can be complex and time-consuming.
Susceptible to Pitting and Staining
Pitting and staining of stainless steel can occur due to environmental factors, such as high humidity, exposure to certain chemicals, and saltwater exposure. This can lead to discoloration and corrosion of the stainless steel surface.
It may also be caused by contact with chlorine, chlorides, and other oxidizing agents.
Metal Comparison: Zinc Alloy vs Stainless Steel
Cost
When it comes to the overall cost, zinc alloy is the more affordable option. This is because it is a much cheaper material to produce and is also easier to manufacture. It also has a much lower melting point, which makes it easier to shape and form.
On the other hand, stainless steel is more costly because it is much harder to work with, requires more specialized tools and machinery, and has a higher melting point.
Heat Resistance
Both materials have excellent heat resistance, but one may be a better choice depending on the application. Zinc alloy offers good heat resistance and is easy to work with for simple applications on a budget.
Strength
Zinc alloy is also softer, making it more susceptible to dents and scratches. Stainless steel is much stronger than zinc alloy, making it a better choice for projects exposed to high stress or strain levels.
Overall, stainless steel is the better choice for strength. It is more durable and resistant to corrosion, and it can withstand more pressure and stress than zinc alloy.
Maintenance
Zinc alloys require more maintenance than stainless steel, which must be polished regularly to maintain their appearance.
On the other hand, stainless steel is more resistant to corrosion and wear and does not require as much maintenance as a zinc alloy. This makes it an excellent choice for projects that must last for many years and may be exposed to harsh conditions.