Sand is a natural resource that is abundant and inexpensive. It is used in various applications, including construction, manufacturing, and art. The advent of 3D sand printing or additive manufacturing in industrial use has changed all that.
It allows for easy customization of molds and cores. This made the production of complex shapes in small batches or even one-off parts economically possible.
Why Sand 3d Printing Is Interesting
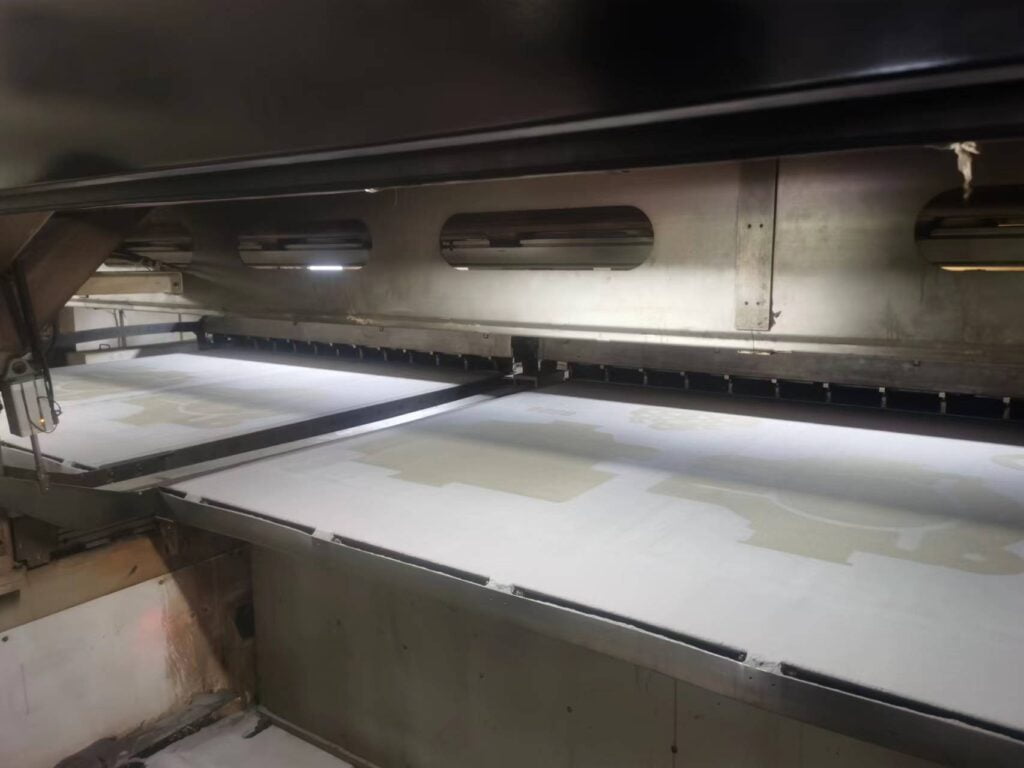
Sand 3D printing is a new technique used by metal manufacturers in the casting industry, especially in multiple-part production. Also called binder jetting, it involves the use of a 3D printer to create objects using silica sand as the raw material.
If you’re asking if can sand be 3D printed? Yes. This process allows serial production in the context of 3D sand printing. It is anticipated that, as the technology continues to advance and become more generally available, it will have an increasing influence on the manner in which components are manufactured across a number of different sectors.
Manufacturing Process of Sand Casting Cores and Molds
A 3D model is created using computer-aided design software. Its entire process needs a high level of skill and expertise and close attention to detail.
The binder is typically a liquid sprayed onto the sand layers using a print head. Once a layer of sand has been printed and bound, the printer moves on to the next layer and repeats the process. This procedure is carried out on successive layers in order to produce the finished cast item.
Once the cast part has been printed, it is removed from the printer, and the excess sand is brushed away. It is then treated with a hardening agent, which helps to strengthen the object and prevent it from crumbling.
Finally, the object is cleaned, and any support structures used during printing are removed. Any necessary finishing touches are made to the mold, such as drilling holes or adding channels to flow molten metal into the core.
Learn More About Sand Casting Material for 3D Printing
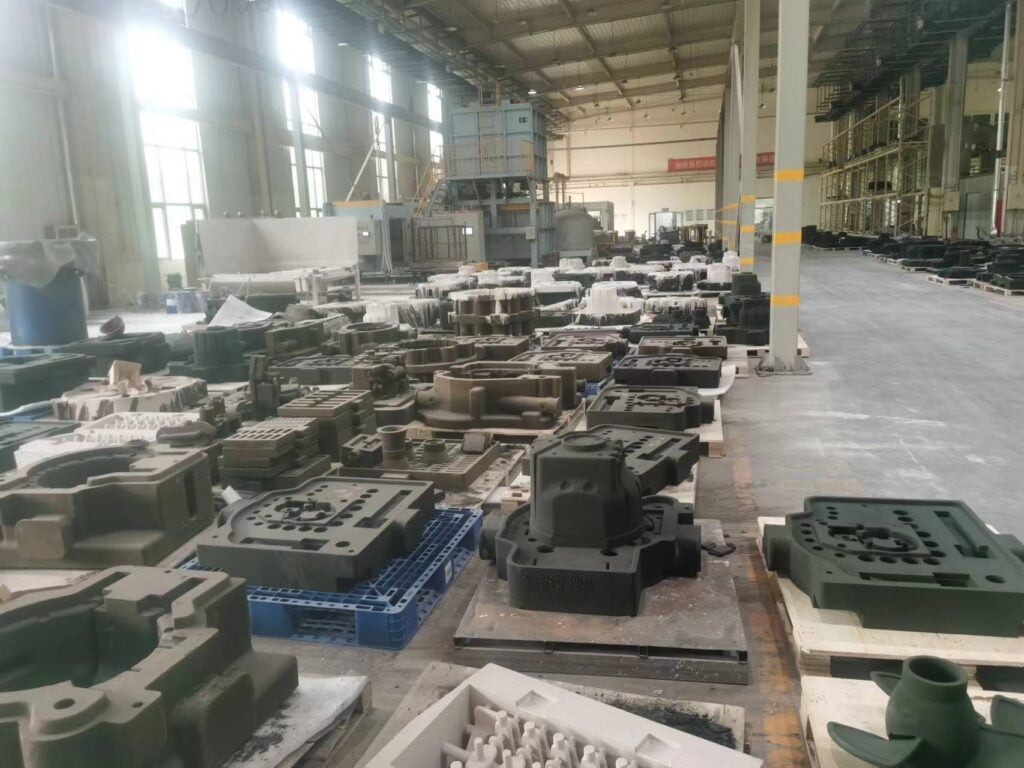
Silica sand is composed of small, rounded particles of quartz known for its excellent physical properties.
Zircon is another popular material for 3D printing. It is composed of zirconium silicate, which gives it unique properties such as high heat resistance and low thermal expansion. Zircon sand is often used in applications with critical dimensional accuracy, such as aerospace and automotive industries.
Chromite is a specialized material that requires high-temperature resistance and excellent dimensional stability. It is a combined mixture of chromium, iron, and oxygen and is known for its high melting point and excellent resistance to thermal shock.
Why Silica Sand is Best to Use for a 3D-Printed Sand
The benefits and features of each kind of sand are distinct. Silica sand, however, is the most popular choice.
Silica sand is readily available and can be easily sourced from many different locations worldwide. It is relatively inexpensive compared to other types, such as zircon or chromite. This makes it an attractive choice for foundries and customers looking to keep their project costs down.
When Should You Use 3D Sand Printing as a Production Process
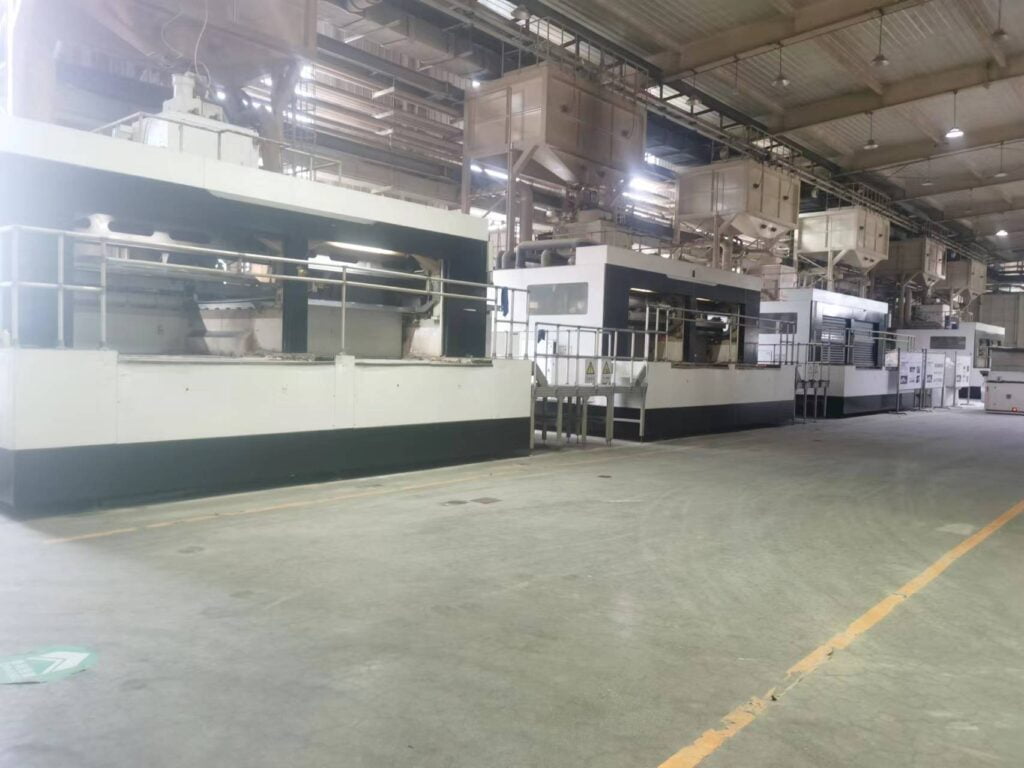
It offers a more cost-effective solution than traditional casting processes, which require the creation of expensive molds.
It can be used for rapid prototyping, allowing for quick iterations of designs and reducing the time it takes to get a product to market.
The ease of change of design in 3D sand printing makes it an ideal choice for projects where design modifications are likely to occur.
Materials Cannot Be Used for 3D Sand Printing
Not all materials are suitable for 3D sand printing, and certain materials cannot be used for this process.
Some materials, such as magnesium, can react with sand and cause combustion. These materials cannot be used for 3D sand printing.
Challenges and Limitations of 3D Sand Printing
Limited Materials
It limits the range of materials that can be used for 3D-printed sand. It is important to carefully evaluate each material and its properties to determine whether it suits this manufacturing process.
Surface Finish
The surface finish of parts and components of 3D printed sand may not be as smooth or polished as those produced with other manufacturing processes. This can impact the casting’s aesthetics and functionality.
Cost
This requires specialized equipment that can be expensive to purchase and maintain. The 3D printers used are typically more costly than traditional casting machines.
While 3D printing can be cost-effective for low-volume production runs, it can be more expensive for high-volume production runs. Traditional sand casting processes may be more cost-effective for high-volume runs due to the efficiencies gained from the economies of scale.