At KT-Foundry, we specialize in stainless steel casting, an essential process in the production of high-quality automotive components. As a preferred choice for automotive manufacturers worldwide, stainless steel casting provides superior strength, corrosion resistance, and durability, making it a crucial component in the engineering of reliable and high-performance vehicles.
Our advanced stainless steel casting methods ensure the highest level of precision and consistency in each component produced, offering unparalleled quality and innovation in the automotive industry. From mechanical parts to machine components, stainless steel casting has become an indispensable component of automotive manufacturing worldwide.
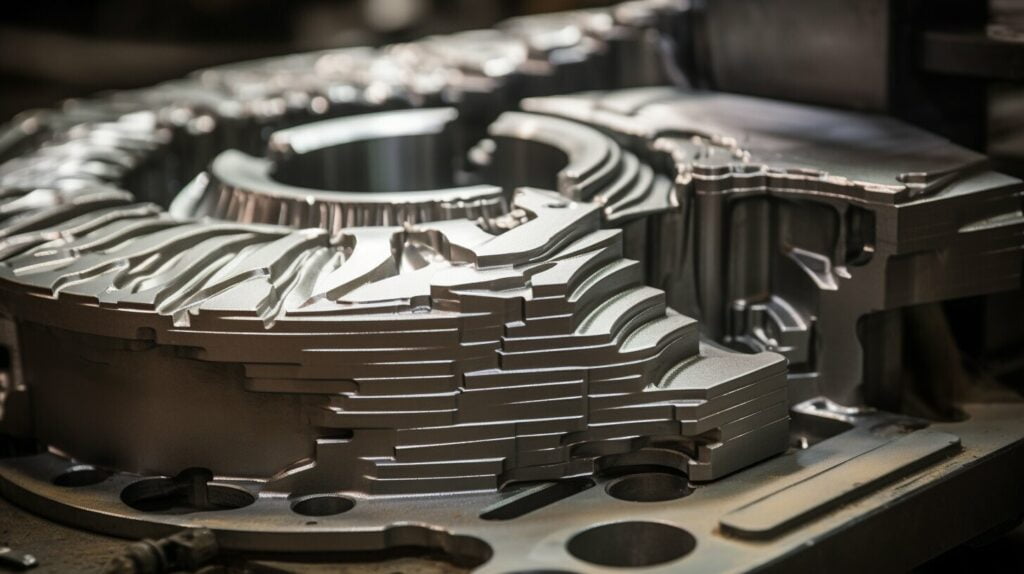
- Stainless steel casting is an essential process in the production of high-quality automotive components.
- Stainless steel casting offers superior strength, corrosion resistance, and durability, making it a preferred choice for automotive manufacturers worldwide.
- Advanced stainless steel casting methods ensure precision and consistency in each component produced.
- Stainless steel casting has become an indispensable component of automotive manufacturing worldwide.
Stainless Steel Casting: A Versatile Manufacturing Process
Stainless steel casting is a highly versatile manufacturing process that has become increasingly popular in the automotive industry. At KT-Foundry, we specialize in providing superior stainless steel casting methods that can be used for a wide variety of automotive applications.
The casting process involves pouring molten metal into a mold, which is then allowed to cool and solidify. Stainless steel casting can be done in different ways, but investment casting is the most common method used in the automotive industry. Investment casting involves creating a wax pattern of the desired part, then coating it in a ceramic shell. Once the ceramic shell has hardened, the wax is melted away, leaving behind a mold cavity that is filled with molten metal. The metal then solidifies and is removed from the mold, revealing the finished part.
The beauty of stainless steel casting is its versatility in producing parts of different shapes and sizes, with complex geometries. It is perfect for producing small to medium-sized parts used in the automotive industry. The process also uses a wide range of alloys that possess unique properties. Our highly skilled team at KT-Foundry has extensive experience in using different alloys for various applications.
The use of molds and the pouring of molten metal make stainless steel casting an extremely precise and accurate process. This ensures a high level of dimensional accuracy and consistency while maintaining the required mechanical properties of the part. Furthermore, the process allows for a superior surface finish, making it ideal for automotive components that require a sleek appearance.
Overall, stainless steel casting is a highly versatile manufacturing process that offers many advantages in terms of creating precision automotive components. With its ability to produce complex shapes, superior surface finish, and robust mechanical properties, it’s no wonder that stainless steel casting is becoming increasingly popular in the automotive industry.
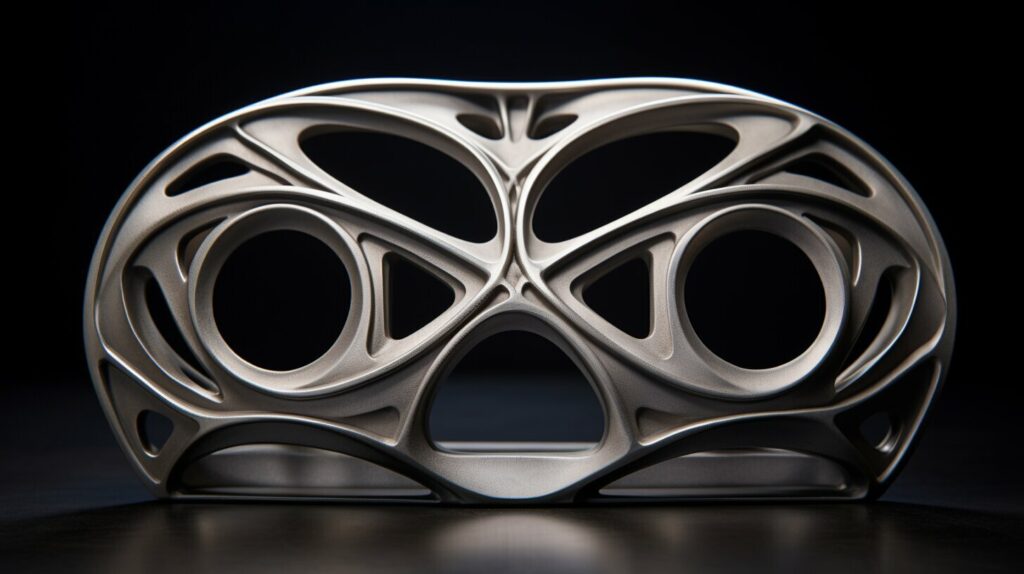
Stainless steel casting is a highly advantageous manufacturing process for producing automotive components. Our immense expertise at KT-Foundry has enabled us to understand the importance of stainless steel casting in improving automotive performance.
One of the most significant advantages of stainless steel casting is its superior corrosion resistance. Stainless steel alloys contain chromium, which reacts with oxygen to form a protective layer on the surface of the metal, preventing corrosion. This protection is especially vital in automotive components that are exposed to harsh environments and corrosive substances.
Furthermore, stainless steel casting offers excellent surface finish and robust mechanical properties. With our investment casting process, we can achieve complex shapes and intricate designs, without compromising on dimensional accuracy. The smooth surface finish of stainless steel castings minimizes friction, which improves the overall performance of automotive components.
In addition, stainless steel casting delivers high strength and durability, making it ideal for use in automotive components that need to withstand heavy loads and frequent use. The mechanical properties of stainless steel castings can be customized to meet specific requirements for different automotive applications.
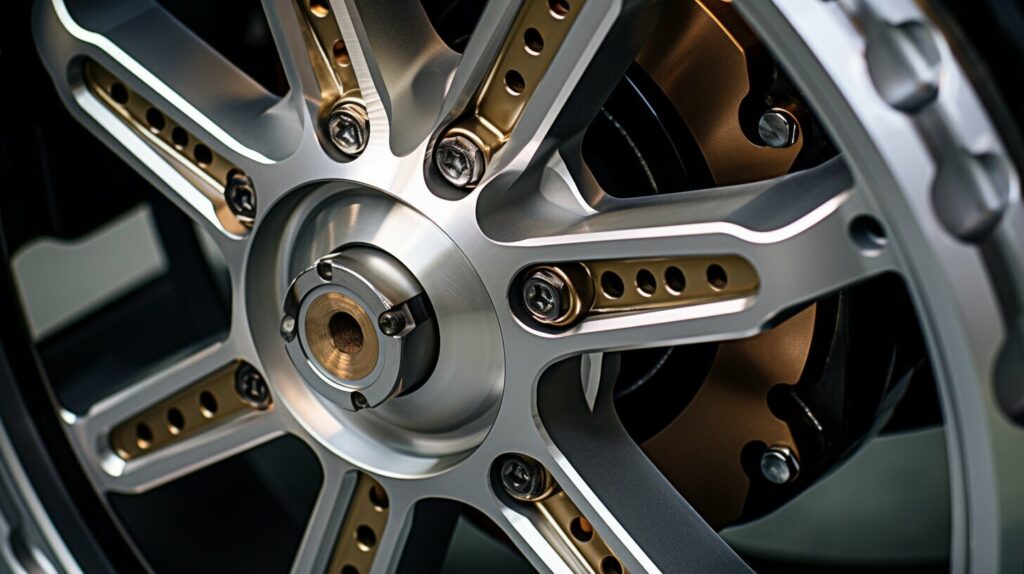
“Stainless steel casting is a highly advantageous manufacturing process for producing automotive components.”
All these advantages make stainless steel casting the preferred choice for automotive components, as it provides high tolerance and dimensional accuracy, ensuring consistent performance.
Stainless Steel Alloys for Automotive Casting
Stainless steel alloys are widely used in the automotive industry for their excellent properties such as corrosion resistance, high strength, and durability. At KT-Foundry, we specialize in the production of castings made from various stainless steel alloys to meet specific needs of automotive manufacturers.
One of the most commonly used alloys in stainless steel casting is chromium. It is known for its corrosion resistance and ability to withstand high temperatures. Austenitic stainless steel, which contains high levels of nickel and chromium, is another popular alloy used in automotive casting due to its high strength and excellent formability.
Duplex stainless steel, characterized by a mixed microstructure of ferrite and austenite, is also commonly used in automotive casting. It offers high corrosion resistance and strength, making it ideal for harsh environments. Ferritic stainless steel, on the other hand, is used in automotive casting due to its excellent resistance to stress corrosion cracking and fatigue.
Martensitic stainless steel, a hardenable alloy with high carbon content, is another important alloy used in automotive casting. It offers exceptional wear resistance and is ideal for high-stress applications such as engine components.
With our expertise in stainless steel casting, we can identify the most suitable alloy for each specific application based on factors such as environmental conditions, strength requirements, and material properties.
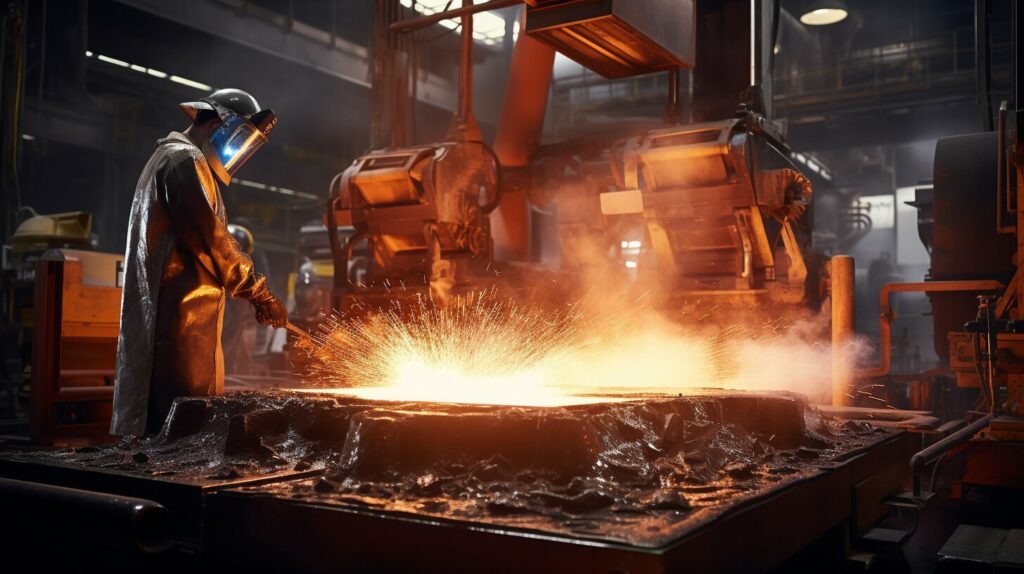
“Our commitment to using the right alloys ensures that our stainless steel castings meet the highest standards of performance and durability in the automotive industry.”
The Process of Stainless Steel Investment Casting
At KT-Foundry, we specialize in stainless steel investment casting, a process that enables us to produce high-quality, complex parts with excellent surface finish and dimensional accuracy.
The process begins with the creation of a wax pattern, which is made by injecting molten wax into a mold. This wax pattern is an exact replica of the final part and is used to create a ceramic shell in the next stage of the process.
The ceramic shell is produced by dipping the wax pattern into a proprietary slurry and then coating it with ceramic sand. The shell is then allowed to dry and harden before being placed in a furnace to remove the wax and create a mold cavity.
Once the ceramic shell has been created, molten metal is poured into the mold cavity. This process is known as lost wax casting, and it allows us to produce parts with intricate geometries and complex shapes.
After the metal has solidified, the ceramic shell is removed, and the part is finished by removing any excess material and performing any necessary post-processing steps, such as heat treatment or surface finishing.
Our investment casting process allows us to produce parts with excellent dimensional accuracy and surface finish, making it ideal for a wide range of automotive applications.
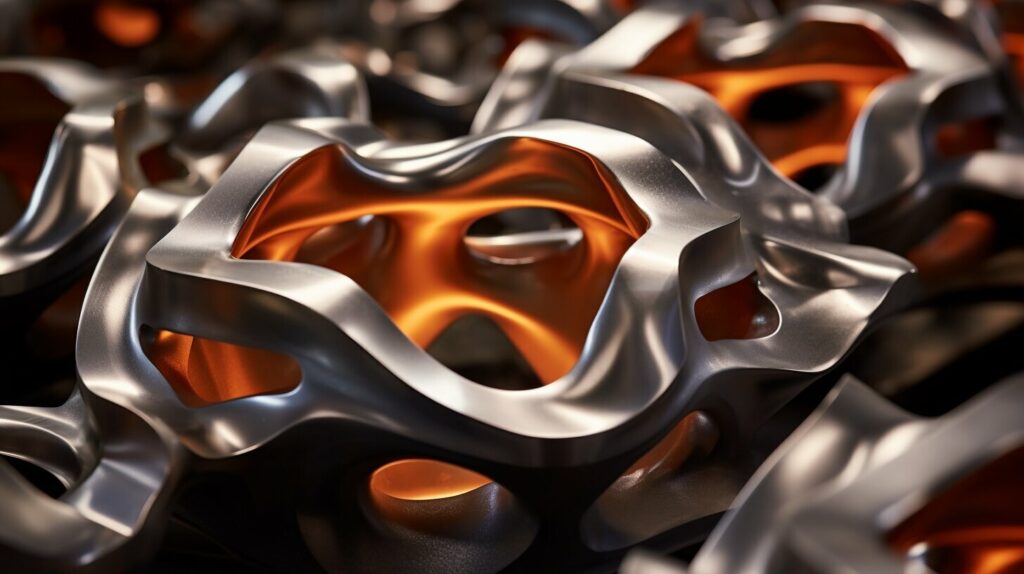
“Our investment casting process allows us to produce parts with excellent dimensional accuracy and surface finish, making it ideal for a wide range of automotive applications.”
Advancements in Stainless Steel Casting Technology
At our company, we take pride in staying up to date with the latest advancements in stainless steel casting technology. One of the areas we focus on is heat treatment, which involves subjecting the castings to controlled heating and cooling processes to optimize their mechanical properties. Heat treatment can also improve dimensional accuracy and surface finish. In addition, we use advanced simulation software to refine our casting processes, resulting in more efficient production and higher-quality castings.
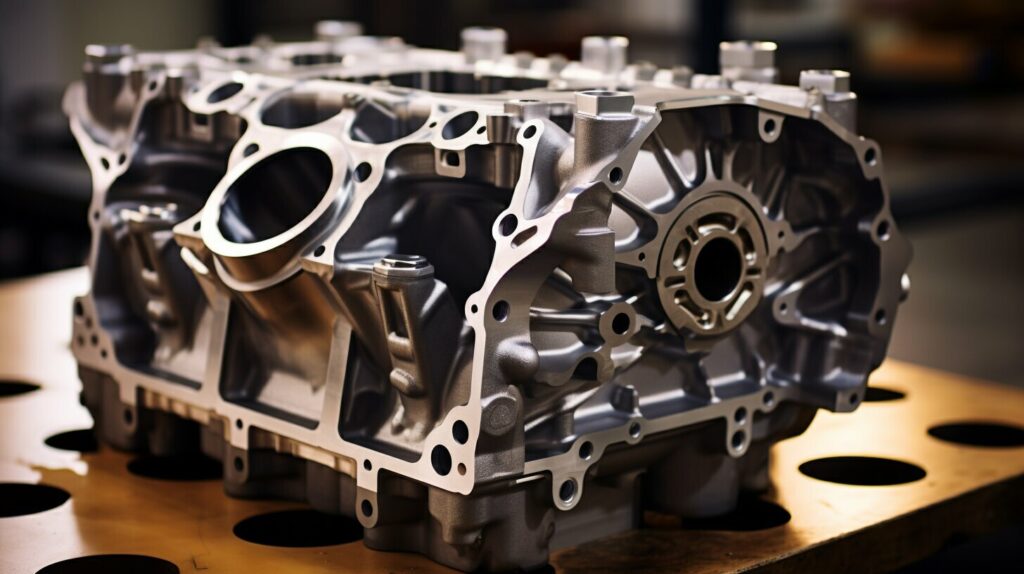
Another significant advancement in stainless steel casting is improved dimensional accuracy. This is achieved through advanced molding techniques, such as investment casting, which allows for the creation of complex shapes with high precision. In addition, we use computer-aided design (CAD) technology to produce highly accurate molds. The result is castings that meet tight tolerances and have consistent dimensional accuracy.
Surface finish is also an important consideration in stainless steel casting. We utilize a variety of finishing techniques, including shot blasting and polishing, to achieve the desired surface finish for each component. This is especially important for high-temperature applications, where surface roughness can negatively impact performance.
Speaking of high-temperature applications, stainless steel casting is an ideal choice for components in these environments. Stainless steel alloys have excellent high-temperature properties, including resistance to thermal fatigue and oxidation. With the advancements in casting technology, we can produce components that are capable of withstanding extreme temperatures while maintaining their mechanical properties.
Applications of Stainless Steel Casting in the Automotive Industry
Stainless steel casting has found significant use in the automotive industry, providing durable and reliable components for various applications. These components include automotive parts, machine components, medical equipment, and food processing equipment, among others.
Automotive parts: Stainless steel casting is commonly used in the production of automotive parts, including engine blocks, transmission components, and exhaust manifolds. The use of stainless steel in these components enhances their strength, durability, and corrosion resistance, making them ideal for harsh environments.
Machine components: Stainless steel casting is also used in the production of machine components, such as gears, pumps, and valves. These components require high strength and durability, and stainless steel casting provides these properties while maintaining tight tolerances and dimensional accuracy.
Medical equipment: Stainless steel casting is used in the production of medical equipment due to its biocompatibility and corrosion resistance. Components such as surgical instruments, implants, and diagnostic tools can be produced using stainless steel casting methods.
Food processing equipment: Stainless steel casting is commonly used in food processing equipment due to its resistance to corrosion and bacterial growth. Components such as mixers, tanks, and conveyors require high corrosion resistance and can benefit from the use of stainless steel casting.
Stainless steel casting provides a versatile and reliable manufacturing process for various automotive components, ensuring high strength, dimensional accuracy, and corrosion resistance for long-lasting performance.
Stainless Steel Casting: Preferred Choice for Automotive Components
At KT-Foundry, we understand the critical role that automotive components play in ensuring the safety and performance of vehicles. That’s why we believe that stainless steel casting is the preferred choice for producing high-quality automotive components.
One of the key benefits of stainless steel casting is its ability to meet tight tolerances while providing high strength and maintaining dimensional accuracy. This makes it an ideal choice for producing components that require precise and reliable performance, such as engine parts, suspension systems, and braking components.
Stainless steel casting offers exceptional resistance to wear and corrosion, making it well-suited for automotive components that are exposed to harsh operating conditions. This includes components that need to withstand high temperatures, such as exhaust systems and turbochargers.
Benefits of Stainless Steel Casting in Automotive Components |
---|
High strength and dimensional accuracy |
Tight tolerances for precision performance |
Exceptional wear and corrosion resistance |
Suitable for high-temperature applications |
At KT-Foundry, we have extensive experience in producing a wide range of automotive components using stainless steel casting. Our advanced casting techniques and quality control processes ensure that our components meet the exacting standards of the automotive industry. Whether you need components for passenger vehicles, commercial trucks, or heavy equipment, our team has the expertise to deliver high-quality, reliable components that meet your specific requirements.
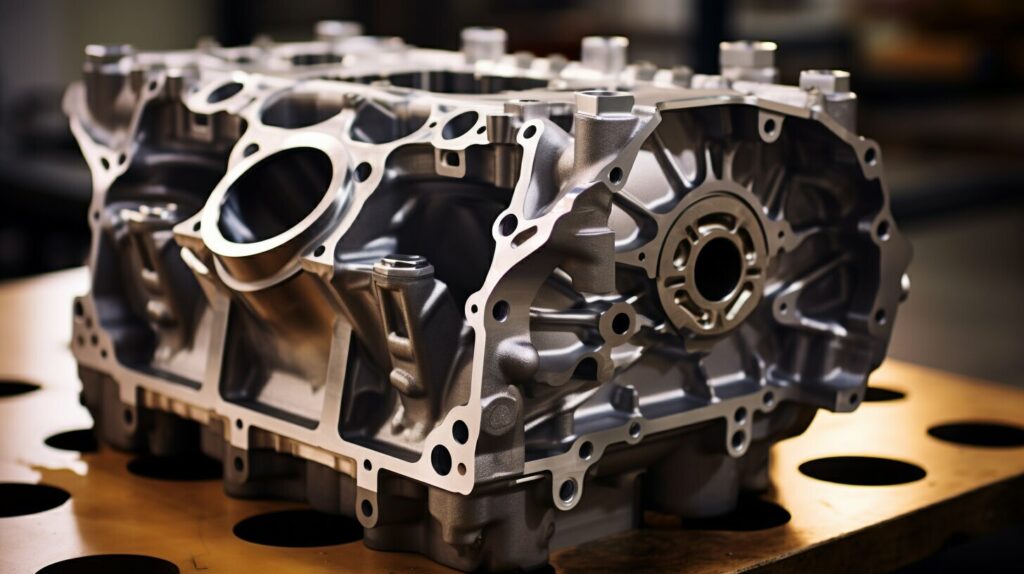
Using stainless steel casting for automotive components is a smart choice that offers numerous benefits. At KT-Foundry, we are committed to utilizing the latest techniques and technologies to produce high-quality components that meet the needs of our customers. Contact us today to learn more about how we can assist with your next automotive component project.
The Versatility and Benefits of Stainless Steel Casting
Stainless steel casting is a versatile and highly beneficial manufacturing process that has a wide variety of applications across different industries. At KT-Foundry, we specialize in providing exceptional stainless steel casting methods to meet the diverse needs of our clients.
Benefits of Stainless Steel
There are several benefits to using stainless steel in casting processes. One of the key advantages is its resistance to corrosion, making it an ideal material for automotive and marine parts, as well as applications in harsh environments. Stainless steel is also highly durable, providing a long-lasting and cost-effective solution.
Wide Variety of Applications
The versatility of stainless steel casting is reflected in the wide range of applications it can be used for. In addition to its use in automotive components, stainless steel casting is commonly used in machine components, medical equipment, food processing equipment, and many other industries. Its ability to withstand high temperatures and resist corrosion makes it a preferred choice for many applications.
At KT-Foundry, our expertise in stainless steel casting ensures that our clients receive high-quality components that meet their specific needs and requirements. Contact us today to learn more about our stainless steel casting services and how we can help you achieve exceptional results.
FAQ
What is stainless steel casting?
Stainless steel casting is a manufacturing process that involves pouring molten metal into molds, creating complex shapes and components made of stainless steel.
Why is stainless steel casting important in automotive components?
Stainless steel casting plays a crucial role in improving automotive performance by providing superior corrosion resistance, excellent surface finish, and robust mechanical properties.
What are the advantages of stainless steel casting in automotive components?
Some advantages of stainless steel casting in automotive components include its corrosion resistance, surface finish, and mechanical properties that enhance the overall quality and durability of the components.
What types of stainless steel alloys are used in automotive casting?
Stainless steel alloys used in automotive casting include austenitic, duplex, ferritic, and martensitic stainless steel, each with specific properties suitable for various automotive applications.
How does the process of stainless steel investment casting work?
The process of stainless steel investment casting involves creating wax patterns, coating them with a ceramic shell, melting out the wax to create mold cavities, and then pouring molten metal into the cavities to form the final components.
What advancements have been made in stainless steel casting technology?
Advancements in stainless steel casting technology include improved heat treatment techniques, enhanced dimensional accuracy, and superior surface finishes, making it suitable for high-temperature automotive applications.
What are the applications of stainless steel casting in the automotive industry?
Stainless steel casting finds applications in a wide range of automotive components, machine parts, medical equipment, and food processing equipment, due to its versatility, strength, and corrosion resistance.
Why is stainless steel casting the preferred choice for automotive components?
Stainless steel casting is the preferred choice for automotive components because it can meet tight tolerances, provide high strength, and maintain dimensional accuracy, ensuring the performance and longevity of the components.
What are the versatility and benefits of stainless steel casting?
The versatility of stainless steel casting lies in its ability to be used in various industries and applications, providing benefits such as corrosion resistance, superior surface finish, and the ability to create complex shapes and components.