Grey cast iron is a widely used material in various engineering applications. The American Society for Testing and Materials (ASTM) has established standards for the different grades of metal castings made from gray iron that a manufacturer or a consumer may use as reference.
These need to be identified in separately cast test bars to ensure the quality and strength of the material. It is also important to meet special requirements to prevent casting defects.
Gray Cast Iron from a Casting Foundry
Gray cast iron, or ASTM A48, is one of the most commonly used metals in the casting foundry industry. It is a ferrous alloy composed of iron, carbon, and traces of graphite flakes and is renowned for its excellent casting and mechanical properties.
It has a excellent machinability, low melting point, and good fluidity, making it suitable for producing complex shapes. Grey iron also has excellent wear resistance and tensile strength.
The quality of the component made from gray cast iron will depend on a suitable iron grade. Once the grade of iron has been selected, the iron is melted in a furnace and then poured into a mold. Pattern equipment is used to mold gray iron castings, usually made of sand or metal.
Depending on the application, the component may require various finishing techniques, such as machining, grinding, or painting.
Material Grades of ASTM A48 Class
Different grades of iron have different properties, and the grade selected depends on the application for which the casting is intended. The different grades of ASTM A48 are classified according to their tensile strength, chemical composition, and physical properties.
Grade 20 is the lowest grade of gray iron, and it is used for smaller castings, such as small parts for engines, pumps, and valves. Grade 25 is used for larger castings, such as structural components and large machine parts. These low grades of gray iron castings have a low modulus of elasticity and high damping capacity.
Grade 30 gray iron castings are made from iron, carbon, and silicon. Gray iron contains a high percentage of carbon, usually ranging from 2.20 to 2.90 percent. This grade is strong and wear-resistant, making them ideal for various applications.
Grade 40 of gray iron is a high-strength, ductile grade of gray iron. Compared to lower grades, it has higher tensile strength and higher hardness. Grades 40 and up have a higher modulus of elasticity and lower damping capacity.
ASTM A48 Grade 60 is the highest grade of grey cast iron. It is also one of the higher-grade materials in the standard and is used for various components.
In general, the higher the material grade of the gray iron castings, the higher tensile strength and higher hardness it has.
ASTM A48 Standard Specifications
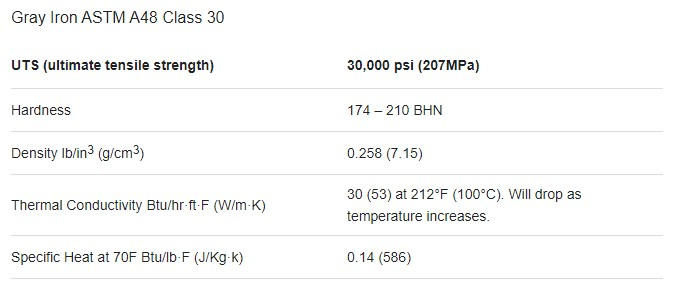
A manufacturer uses a test bar or an original sample of the casting to identify the tolerance range, pressure tightness, and other standards. A visual examination can be done to check the surface finish quality and key dimensions. The above chart is a sample of a specification of gray iron.
Chemical Composition
Grade 20 ASTM A48 comprises approximately 3.50-3.70% carbon and 2.00-2.30% silicon. Other elements found in Grade 20 ASTM A48 include up to 0.30% manganese, up to 0.60% phosphorus, and up to 0.05% sulfur.
At its core, Grade 30 ASTM A48 is composed primarily of iron. The iron content is usually between 98 and 98.5%. Carbon is typically present at a rate of around 2.2%; silicon is at 2.3%, and manganese is at 0.3%. Phosphorus is usually present at a rate of 0.25 percent, and sulfur at 0.2%.
The exact chemical composition of Grade 40 ASTM A48 varies from one manufacturer to another, but the overall composition is typically in the range of 2.0-3.0% carbon, 0.3-1.4% silicon, 0.4-1.0% manganese, 0.05-0.35% phosphorus, 0.05-0.35% sulfur, and 0.2-0.5% magnesium.
Grade 60 has a high carbon content at the 3.5-4.0% scale, making it ductile and strong. The silicon content is usually 1.75-2.25%. The manganese and sulfur content are usually 0.30-0.50% and 0.15-0.30%, respectively.
Tensile Strength
Manufacturers and consumers consider tensile strength as the important specification for gray iron castings.
Grade 20 ASTM A48 has a tensile strength of 20,000 psi. It has the minimum tensile strength among all grades of gray iron castings. It is ideal for applications that require a heavy-duty material that can withstand high tensile loads and pressure.
Grade 30 ASTM A48 is a carbon-steel material with a tensile strength of at least 30,000 pounds per square inch (psi). It is a general-purpose gray iron that is very strong and wear-resistant.
The tensile strength of Grade 40 ASTM A48 is a minimum of 40,000 psi (275 MPa). It has good machinability and weldability and can create various products, including engine components, machine parts, and structural components.
The tensile strength of Grade 60 ASTM A48 is a minimum of 60,000 pounds per square inch (psi). This is a medium carbon, grey iron used in various applications, including those requiring high strength and good corrosion resistance. Its high tensile strength of 60,000 psi makes it an ideal choice for parts for which a great deal of stress and wear is a significant consideration.
Hardness
Grade 20 has a hardness of approximately 200 Brinell. It is a nodular cast iron heat treated to produce a more uniform microstructure, improving mechanical properties and machinability.
Grade 30 ASTM A48 has a Brinell hardness of approximately 187. This steel grade is ideal for applications that require wear and tear resistance, as its hardness ensures that the surface will remain in good condition.
Grade 40 ASTM A48 has a Brinell hardness of 207-255, making it a medium-hard material. Its hardness makes it ideal for components that need high wear resistance, such as gears and cams.
Grade 60 This grade is highly resistant to shock and has a hardness of around 382 Brinell. It is very wear-resistant and can handle heavy loads and impacts, making it an excellent choice for many machine parts.
Applications of Gray Iron Castings
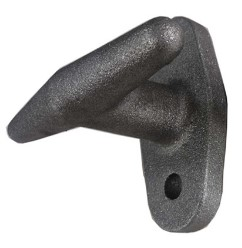
Cylinder Liners
The high carbon and silicon levels in gray iron produce a solid and rigid material that is very resistant to wear and tear. The low cost of production makes them ideal for use in mass-produced parts such as cylinder liners.
Its machinability makes them perfect for cylinder liners, where precision is essential for engine performance.
Train Parts
Gray iron castings are particularly used for producing train parts due to their excellent durability and strength. Gray iron castings can create parts such as brake shoe holders, axle boxes, buffer brackets, brake linkages, guide links, and even complete train frames.
Motor Vehicles
Gray iron is ideal for automotive applications due to its strength, durability, and low cost. It is commonly used for engine blocks, cylinder heads, transmission cases, flywheels, and brake drums. Additionally, gray iron can be machined easily, making it an ideal choice for components that require precise tolerances and intricate designs.