Welcome to our article on high-pressure die casting (HPDC)! In this section, we will provide an overview of the manufacturing process, highlighting its precision and versatility. Whether you are in the aluminum die cast industry or interested in learning more about high-pressure die casting, this article will give you valuable insights into this high-performance casting method.
Key Takeaways:
- HPDC is a manufacturing process that utilizes high hydraulic or pneumatic pressure to inject molten metal into precision-engineered dies.
- It offers superior precision and versatility, allowing for the creation of complex shapes and thin walls.
- HPDC is known for its efficiency and accuracy, producing high-quality parts quickly and cost-effectively.
- The process has advantages such as faster production rates, energy savings, and superior surface finish.
- However, HPDC also has some disadvantages, including equipment costs and technical challenges.
What is High Pressure Die Casting Process?
High-pressure die casting (HPDC) is an advanced manufacturing process that utilizes high hydraulic or pneumatic pressure to inject molten metal into precision-engineered dies. This process ensures even greater accuracy and allows for the creation of more complex shapes and thinner walls compared to traditional die casting methods. The high hydraulic pressure applied during HPDC enables the production of intricate designs and superior material properties, setting it apart from conventional casting techniques in the field.
How does High Pressure Die Casting Work?
In the HPDC process, molten metal is injected into reusable dies at high pressures. The dies are carefully designed to create the desired shape, intricacy, and wall thickness of the final product. The high hydraulic pressure ensures that the molten metal fills all the intricate details of the die cavity, resulting in precise and accurate castings. Once the metal solidifies, the dies are opened, and the casting is ejected. The casting may then undergo post-casting treatment processes such as trimming, machining, or surface finishing to meet specific requirements.
Advantages of High Pressure Die Casting:
- Precision and accuracy: HPDC allows for the creation of complex shapes with tight tolerances, ensuring high-quality castings.
- Efficiency: The high-pressure injection process enables fast production rates and shorter cycle times, meeting high-volume demands efficiently.
- Versatility: HPDC can be used with various metals, including aluminum, magnesium, and zinc, offering versatility in material selection.
- Surface finish: The process produces castings with excellent surface finish, eliminating the need for secondary machining or finishing operations.
- Strength and durability: HPDC ensures a dense and uniform structure, enhancing the mechanical properties of the castings and providing greater strength and durability.
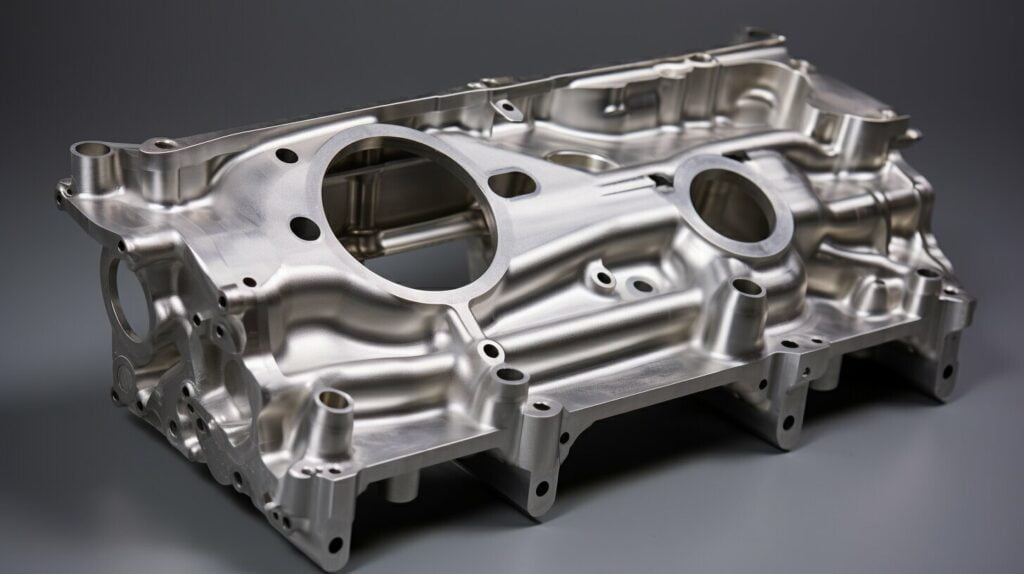
Applications of High Pressure Die Casting:
High-pressure die casting finds extensive applications across various industries, including:
- Automotive: Engine blocks, transmission housings, and other critical components.
- Lighting: Intricate fixtures and housings with superior surface finishes.
- Electrical: Connectors, switches, and heat sinks.
- Agricultural Machinery: Robust and durable parts.
- Medical: Surgical tools, implants, and diagnostic apparatus.
Advantages of High Pressure Die Casting
High-pressure die casting (HPDC) offers numerous advantages in the manufacturing process, making it a preferred choice for producing high-quality metal components. Here are some of the key advantages of using HPDC:
- Efficiency: HPDC allows for faster production rates, reducing cycle times and meeting high-volume demands efficiently. This efficiency enables manufacturers to deliver products to market quickly, maintaining a competitive edge.
- Energy Savings: HPDC reduces energy consumption compared to other casting methods, contributing to a more sustainable manufacturing process. This not only helps reduce environmental impact but also contributes to cost savings in the long run.
- Superior Surface Finish: The HPDC process ensures excellent surface finish on the cast parts, eliminating the need for secondary machining or additional finishing. This not only saves time and effort but also enhances the aesthetic appeal of the final product.
- Greater Strength and Durability: HPDC produces parts with a dense and uniform structure, resulting in superior mechanical properties such as increased strength and durability. This makes HPDC suitable for applications where robust and reliable components are required.
- Reduced Waste: HPDC minimizes material waste, as the process allows for precise control over the amount of molten metal injected into the die. This not only reduces material costs but also contributes to a more sustainable manufacturing process.
- Lower Labor Costs: Automation and process efficiency in HPDC help reduce labor costs. With advanced machinery and automated processes, manufacturers can achieve high production volumes with minimal manual labor, leading to cost savings.
With these advantages, it is clear why HPDC is widely used in various industries, including automotive, lighting, electrical, agricultural machinery, and medical. The efficiency, energy savings, superior surface finish, greater strength and durability, reduced waste, and lower labor costs make HPDC a versatile and effective casting method for producing high-quality metal components.
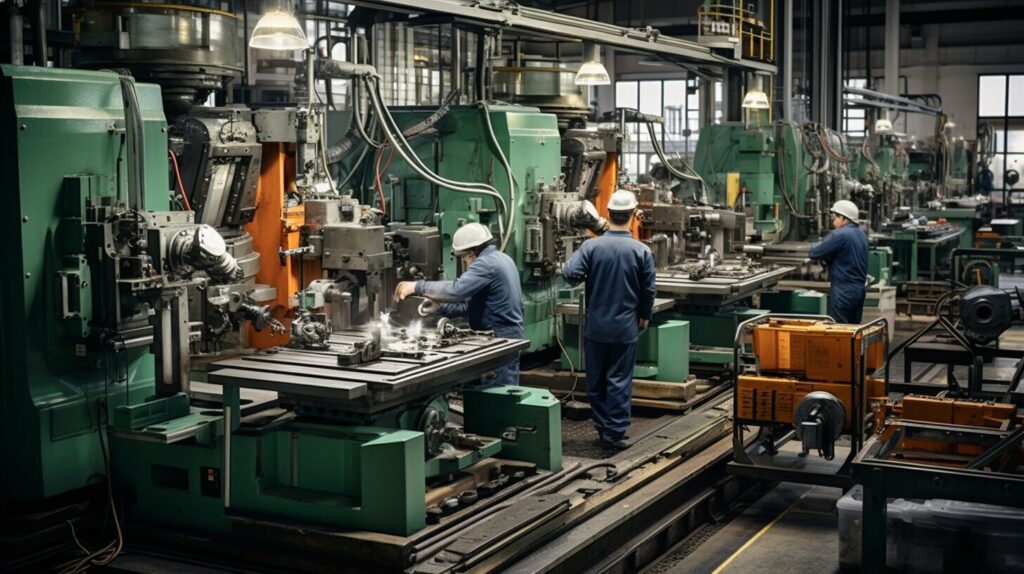
Disadvantages of High Pressure Die Casting
While high-pressure die casting (HPDC) offers numerous advantages, there are also several disadvantages that manufacturers should consider before implementing this casting method. These disadvantages include equipment costs, initial investment, maintenance, technical challenges, the complexity of the process, and potential defects.
1. Equipment Costs and Initial Investment: Implementing HPDC requires specialized machinery, including high-pressure injection systems and precision-engineered dies. These equipment costs can be substantial, making the initial investment a significant barrier, especially for smaller manufacturers with limited budgets.
2. Maintenance: The complex machinery used in HPDC requires regular maintenance to ensure optimal performance. This maintenance adds to the operational costs of the manufacturing process, and failure to properly maintain the machinery can lead to reduced productivity and increased downtime.
3. Technical Challenges and Complexity of the Process: HPDC is a sophisticated process that requires precise control over various parameters, such as temperature, pressure, and cooling rates. Achieving and maintaining these parameters can be challenging, especially when scaling up production or working with different materials. The complexity of the process often requires skilled operators and engineers to ensure successful casting outcomes.
4. Potential Defects and Solutions: Despite the precision of HPDC, potential defects can still occur during the casting process. These defects may include porosity, shrinkage, or surface blisters. Identifying and addressing these defects requires careful monitoring and potential adjustments to process parameters. Post-casting treatments may also be necessary to remedy any resulting defects, adding additional costs and time to the manufacturing process.
Disadvantage | Solution |
---|---|
Equipment Costs and Initial Investment | Explore leasing options or partnerships to reduce upfront costs. |
Maintenance | Follow a regular maintenance schedule and invest in skilled technicians. |
Technical Challenges and Complexity of the Process | Provide comprehensive training to operators and engineers to ensure a deep understanding of the process and parameters. |
Potential Defects | Implement quality control measures, such as in-process inspections and analysis, to identify and address defects early. |
High Pressure Die Casting Applications
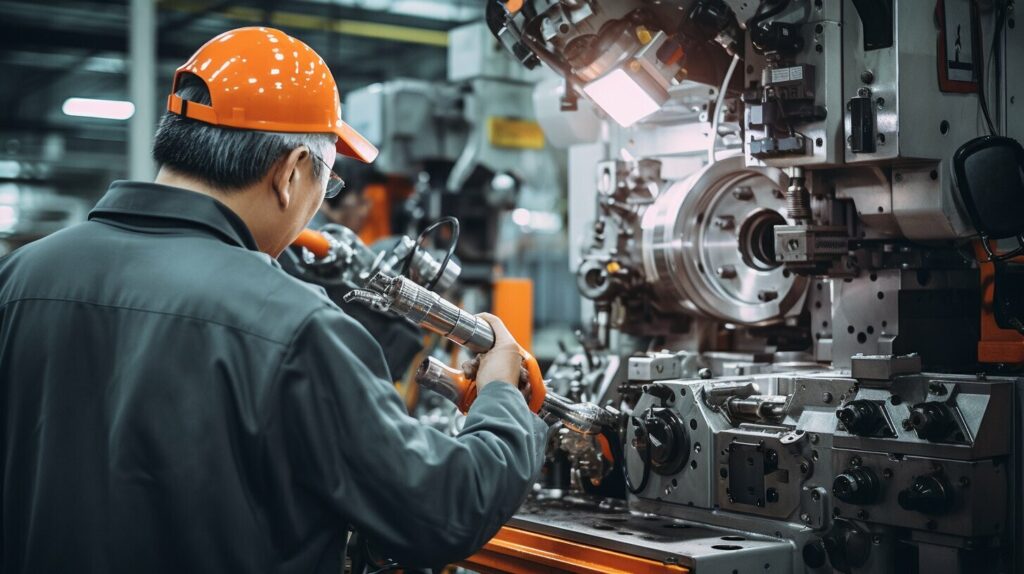
In the world of manufacturing, high-pressure die casting (HPDC) finds extensive applications in various industries. Let’s explore how HPDC is utilized in key sectors:
Automotive Industry
The automotive industry heavily relies on HPDC for the production of critical components such as engine blocks, transmission housings, and wheel frames. The high-pressure nature of the casting process ensures the creation of strong and durable parts, meeting the stringent requirements of the automotive sector.
Lighting Industry
In the lighting industry, HPDC is widely used to fabricate intricate fixtures and housings with superior surface finishes. The versatility of the process allows for the production of complex shapes, enabling the creation of aesthetically appealing lighting products.
Electrical Industry
The electrical industry benefits from HPDC in the manufacturing of components like connectors, switches, and heat sinks. HPDC ensures the creation of precise and reliable electrical parts, meeting the industry’s demand for high-quality and efficient products.
Agricultural Machinery Industry
HPDC plays a vital role in the production of robust and durable parts for the agricultural machinery industry. From tractor components to harvesting equipment, HPDC enables the manufacturing of reliable and high-performance agricultural machinery.
Medical Industry
In the medical industry, HPDC is employed to manufacture surgical tools, implants, and diagnostic apparatus. The process ensures the production of precise and hygienic medical devices, meeting the industry’s stringent quality and safety standards.
Industry | Application |
---|---|
Automotive | Engine blocks, transmission housings, wheel frames |
Lighting | Intricate fixtures, housings |
Electrical | Connectors, switches, heat sinks |
Agricultural Machinery | Tractor components, harvesting equipment |
Medical | Surgical tools, implants, diagnostic apparatus |
High-pressure die casting has revolutionized various industries, providing them with efficient and reliable manufacturing solutions. Through its versatility and ability to produce high-quality components, HPDC continues to play a crucial role in driving innovation and advancement across different sectors.
Evolution History of High-Pressure Die Casting
The history of high-pressure die casting (HPDC) can be traced back to the mid-1800s when it was first utilized in the printing industry. The process was initially employed to produce keys for printing machinery, showcasing the early potential of this casting method. Over time, HPDC expanded its horizons and found application in various other industries, shaping the way metal components are manufactured today.
The evolution of HPDC involved refining the process and incorporating advancements in technology and materials. Mold preparation plays a crucial role in HPDC, ensuring the accuracy and quality of the final product. The injection of molten metal into precision-engineered dies is a key step in achieving the desired shape and structure of the casting. Following the injection, the casting is ejected from the mold, ready for post-casting treatments, if necessary.
HPDC brought about a revolution in the manufacturing industry by providing a cost-effective method for producing high-quality metal components. Today, it continues to be a widely used casting method, offering versatility and precision in the production of complex parts.
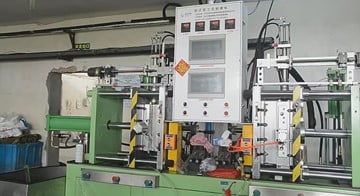
Year | Milestone |
---|---|
Mid-1800s | HPDC first used in the printing industry to produce keys for printing machinery |
Continued | HPDC evolves and expands its application into various other industries |
Present | HPDC is a widely used casting method in the manufacturing industry |
Conclusion
In conclusion, high-pressure die casting (HPDC) is a highly efficient and precise manufacturing process that offers numerous advantages. HPDC allows for fast production rates, resulting in shorter cycle times and meeting high-volume demands efficiently. The process ensures superior surface finish, eliminating the need for additional machining or finishing. It also enhances the mechanical properties of the parts, providing greater strength and durability.
While HPDC has its advantages, there are also some disadvantages to consider. The specialized machinery required for HPDC can be costly, making the initial investment a barrier for smaller manufacturers. Maintenance of the complex machinery is essential to ensure optimal performance, adding to the operational costs. The technical challenges associated with HPDC, such as precise control over various parameters, can pose difficulties during the scaling of production.
Despite the challenges, HPDC finds extensive applications in various industries. In the automotive industry, HPDC is used to manufacture critical components such as engine blocks and transmission housings. The lighting industry utilizes HPDC for intricate fixtures and housings, while the electrical industry benefits from components like connectors and switches. HPDC also plays a vital role in the agricultural machinery industry, producing robust and durable parts. Additionally, HPDC is employed in the medical industry for surgical tools, implants, and diagnostic apparatus.
Overall, high-pressure die casting is a versatile and widely used casting method that offers precise manufacturing capabilities in terms of production efficiency, quality, and cost-effectiveness. Its ability to produce complex and high-quality parts makes it a preferred choice in various industries.
FAQ
What is high-pressure die casting (HPDC)?
High-pressure die casting (HPDC) is a manufacturing process that uses high hydraulic or pneumatic pressure to inject molten metal into precision-engineered dies.
What are the advantages of high-pressure die casting?
High-pressure die casting offers faster production rates, reduces energy consumption, produces parts with excellent surface finish, ensures a dense and uniform structure, and reduces waste and material costs.
What are the disadvantages of high-pressure die casting?
Some disadvantages of high-pressure die casting include the initial investment in specialized machinery, regular maintenance costs, technical challenges, and the potential occurrence of defects that may require post-casting treatments or adjustments.
What are the applications of high-pressure die casting?
High-pressure die casting is used in industries such as automotive, lighting, electrical, agricultural machinery, and medical to manufacture components such as engine blocks, fixtures, connectors, and surgical tools.
What is the history of high-pressure die casting?
High-pressure die casting has been used since the mid-1800s, initially in the printing industry, and has evolved into a cost-effective method for producing high-quality metal components.