Heat-treating cast steel is an important process for strengthening and improving its wear resistance. Cast steel is an alloy of iron and carbon, and it has been used for centuries to create a variety of tools, from swords to surgical instruments.
Heat treatments can help increase its hardness, strength, and wear resistance, making it an ideal material for a wide range of applications. In this article, we will explore why cast steel should be heat treated, the process involved, and the benefits it can provide.
What is Heat Treatment Process?
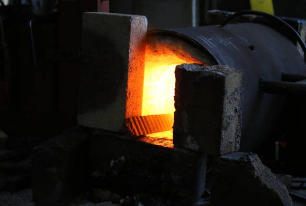
The heat treatment process is used to alter the mechanical properties of metal castings, such as tensile strength, final hardness, ductility, and toughness. The process can also be used to produce desired metallurgical properties, such as grain size refinement and the creation of desirable microstructures.
The process involves heating of a metal casting without changing its shape or form. Once the material is chosen, the cast is heated in a furnace to the desired temperature. It is important to note that the temperature must be consistent and even throughout the ductile cast iron, malleable cast iron, or any type of cast iron.
Next, the cast is held at the desired temperature for a specific period of time. This is known as the “holding time.” During this time, the metal undergoes a series of chemical and physical changes. The time-temperature relationship plays a huge role in achieving the desired material properties.
Once the holding time is complete, the cooling cycles of the metals are done in a controlled manner. The rate and method of cooling depend on the desired properties. In some cases, the cast may undergo fan-assisted cooling, or it may be quenched in oil or water.
Finally, the steel castings are tested to ensure the desired mechanical properties were achieved. This is done through a variety of tests, such as hardness tests, impact tests, tensile tests, and more. If the desired properties are not achieved, the heat treatment process must be repeated.
Importance of Heat Treatment
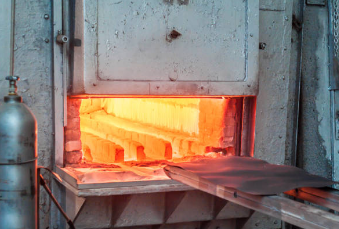
Heat treatment is a vital step in the production of metal castings. Without it, the casting would have inferior strength and durability. Heat treatment ensures that the high alloy steel castings have the desired properties and is free from defects. It also helps to improve the dimensional accuracy, surface finish, and other aspects of the casting.
If the metal is heated too quickly, it can lead to quench cracking or other damage. If the metal is heated too slowly, it can lead to a decrease in strength and hardness of the metal. The heat treatment process can also be used to make the molten metal more resistant to corrosion and wear as it forms.
The heat treatment process is also used to improve the appearance of the many cast irons. It can be used to give the metal an attractive finish, such as a polished look or a matte finish. This can be done by controlling the temperature and time of the heat treatment process.
Without the heat treatment process, the quality of the final product would be significantly lower.
Different Heat Treatment Processes in Cast Iron
The most common heat treatment processes for cast iron are the annealing process, normalizing heat treatment, stress relief heat treatment, and quenching. Each of these processes has its own purpose and benefits.
Annealing Process
Annealing is a heat treatment process that is used to soften and strengthen cast iron. It involves slowly heating the metal to a temperature below the recrystallization point of its crystal structure and then slowly cooling it down.
The annealing process begins by heating the cast iron at a lower critical temperature. This is typically done in a furnace or kiln and the temperature is carefully monitored. Once the cast iron reaches the desired temperature, it is allowed to cool slowly to room temperature.
The heating and cooling process is equally important, as it helps to reduce the amount of residual stress on the metal. If the metal is rapidly cooled, it can cause internal stresses that can lead to cracks and fractures.
Normalizing Iron Castings
The normalizing heat treatment process for cast iron is a two-step process that involves heating and cooling the material. The first step is to heat the cast iron to its upper critical temperature (the temperature at which austenite transforms to pearlite and ferrite).
This temperature is usually around 900 – 980 degrees Celsius, depending on the type of cast iron. The cast iron is then held at this temperature for a period of time to allow for homogenization or an even distribution of the alloying elements.
Once the material is homogenized, it is cooled rapidly in the air. This rapid cooling helps to normalize the structure of specific cast iron types, as it prevents the formation of pearlite and ferrite. The appropriate cooling rate helps to increase the material properties, as well as to improve its wear and corrosion resistance.
Stress Relief Heat Treatment
Stress relief heat treatment is a process that is used to reduce the internal stresses of metal parts, especially those that have a complex or intricate shape. The process works by heating the part to a specific temperature, allowing the metal to relax and release the stresses that have built up inside it.
The process begins by preheating the part to a specific temperature. This temperature is typically between 400 and 800 degrees Celsius, depending on the type of metal being used. Once the part has been preheated, it is then brought up to the stress relief temperature.
For ductile cast irons and gray cast irons, the ideal stress relief temperature is between 550 and 650 degrees Celsius. For austenitic stainless steel, the stress relief temperature is 425 and 925 degrees Celsius. Carbon steel has lower stress relief temperatures at 600 to 675 degrees Celsius.
Quenching
Quenching heat treatment is a process used to harden cast iron and increase its wear characteristics. It involves heating the metal to its critical temperature, cooling it quickly, and then tempering it.
The process of quenching heat treatment begins by heating cast iron to its critical temperature. This is the point at which the metal’s microstructure begins to change, allowing it to gain strength and wear resistance. The metal is then rapidly cooled, usually in a liquid or gas, such as water or oil. This cooling process is what gives the metal its hardness.
Tempering
Once the metal has cooled, it is then tempered. Tempering is the process of reheating the metal to a lower temperature, allowing the metal to become more ductile and less brittle. This helps to reduce the risk of cracking or warping of the quenched steel during use.
Benefits of Heat Treatment Processes in Alloy Steel Castings
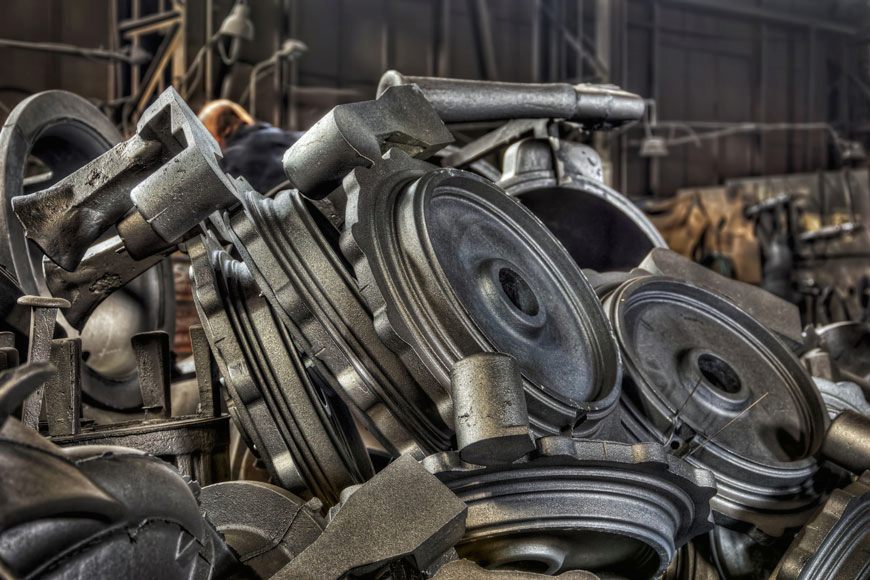
Heat treatment processes can provide numerous benefits in the production of alloy steel castings. With this process, you can have a more durable, longer-lasting product with improved performance characteristics.
Increased Ductility and Impact Resistance
One of the main benefits of heat-treating metal castings is increased ductility. Ductility refers to the ability of a material to deform plastically under stress. The process can increase the ductility of a metal, which makes it more malleable and less brittle. This can be very beneficial for applications that require the metal to be formed into complex shapes without fracturing.
Heat treatment of metal castings can also improve the material’s impact resistance. Impact resistance is the measure of a material’s ability to withstand forces of shock or impact. Heat treating can increase the impact resistance of a metal, making it better able to withstand impacts without fracturing or deforming.
Better Wear Resistance
The improved wear resistance that comes with heat treatment is due to the creation of a hard surface that is more resistant to abrasion and corrosion. By increasing the hardness and strength of the metal, heat treatment can help to improve the overall lifespan of the metal.
This improved resistance to wear and tear can also help to reduce maintenance costs.
What to Consider When Choosing Heat Treatment Methods
When selecting a heat treatment method, there are a few factors to consider, including the desired outcome, the metal or alloy composition, and the transformation temperature of the material. By understanding these factors and choosing the right heat treatment process, you can ensure that your metal or alloy has the desired properties.
Material Used in Metal Casting
When selecting heat treatment methods for metal casting, it is important to consider the material being used in the process. The type of material used will determine the best course of action for properly treating the metal. Different materials will require different methods of heat treatment in order to achieve the desired results.
When working with ferrous materials, such as steel, it is important to understand the concept of tempering. his process is typically done with a furnace, in which the metal is heated and then cooled at a controlled rate.
When working with non-ferrous materials, such as aluminum or magnesium, quenching can help to strengthen the finished product and make it more resistant to wear and tear.
Transformation Temperature
Another factor to consider is the transformation temperature of the metal casting, as this will determine the range of temperatures that the metal can be exposed to without undergoing a transformation. Specific steel may undergo a structural transformation, such as the formation of austenite or the precipitation of carbides.
For example, heat treatments may require a longer exposure to lower temperatures before they affect mechanical properties, while others may require a shorter exposure to a higher temperature.