As a foundry worker employed for many years, we understand the importance of choosing the right casting method for your project. When it comes to stainless steel casting, two popular methods are sand casting and investment casting. Both methods have their own advantages and disadvantages, and the choice between the two depends on various factors. In this article, we will provide an in-depth comparison of these two casting methods, exploring the casting process, types of molds used, and the advantages and disadvantages of each method.
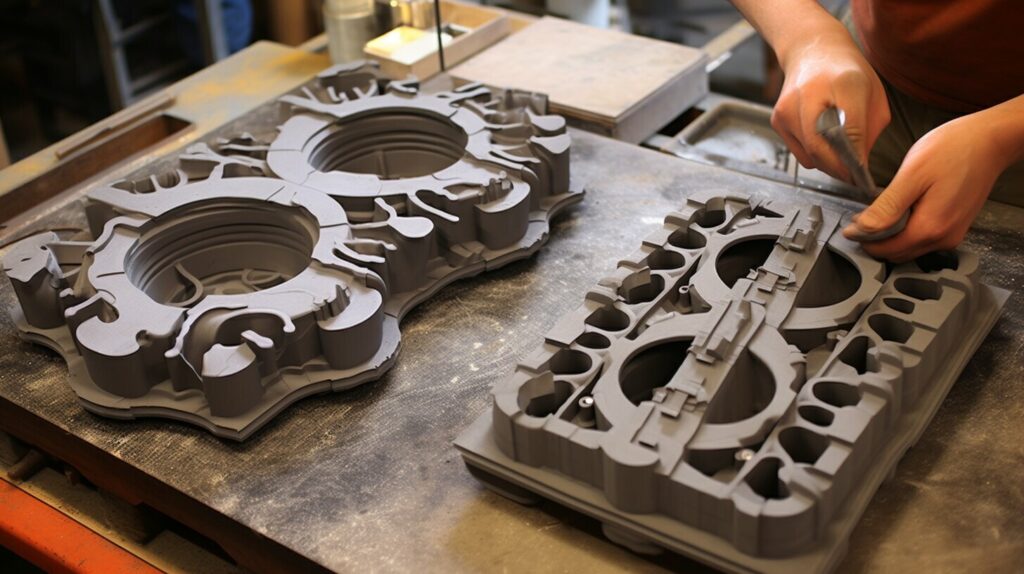
- Sand casting and investment casting are both popular casting methods for stainless steel casting.
- The choice between sand casting and investment casting depends on various factors, including the desired surface finish, production volume, and budget.
- Sand casting involves creating molds using sand as the mold material, while investment casting uses a wax pattern to create a ceramic mold.
- Investment casting offers certain advantages, such as the ability to create complex shapes with tight tolerances and reduced machining costs.
- Ultimately, the decision between sand casting and investment casting should be based on the specific application and project requirements.
Understanding Sand Casting
When it comes to casting metal parts and components, one of the most widely used methods is sand casting. This process involves creating a mold using sand as the primary material. The sand is mixed with a binding agent that helps hold the mold together and create a cavity into which the molten metal is poured.
Sand casting is a versatile technique that can be used to produce both small and large parts, depending on the size of the mold. The process also allows for the creation of complex shapes and designs that may be difficult or impossible to achieve with other casting methods.
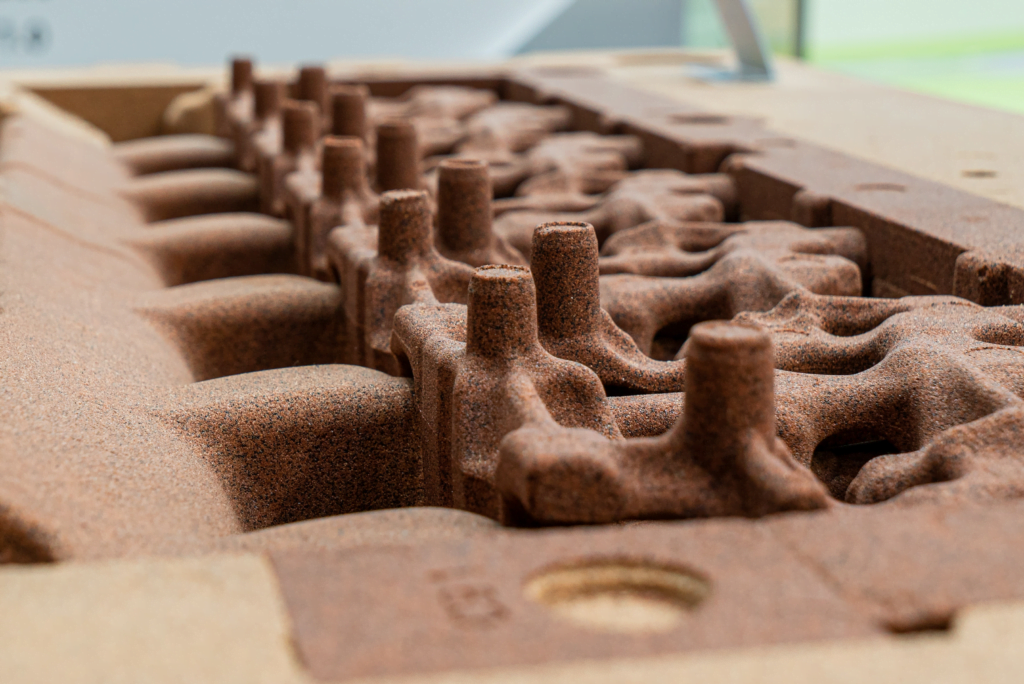
To begin the process of sand casting, a pattern or model is created of the final product. This pattern is then used to create a mold by pressing it into a mixture of sand and binder. Once the mold is formed, it is allowed to dry and then the pattern is removed.
The finished mold is then heated to a high temperature to remove any remaining moisture and prepare it for the pouring of molten metal. The metal is poured into the mold cavity, where it is allowed to cool and solidify. Once the metal has hardened, the mold is broken apart and the finished product is removed.
There are various techniques used in sand casting, such as green sand casting, dry sand casting, and shell molding. Each technique has its own advantages and disadvantages, depending on the size and complexity of the product being cast.
Overall, sand casting is a popular choice because it is relatively inexpensive and allows for the creation of a wide range of metal parts and components. However, it does have some limitations in terms of surface finish and dimensional accuracy.
Exploring Investment Casting
Investment casting, also known as lost-wax casting or precision casting, is a casting method that involves creating a mold from a wax pattern. The process starts by creating the wax pattern, which is then coated in a ceramic shell. The ceramic shell is heated to remove the wax pattern, leaving behind a cavity that can be filled with molten metal. Once the metal solidifies, the ceramic shell is broken away to reveal the final metal casting.
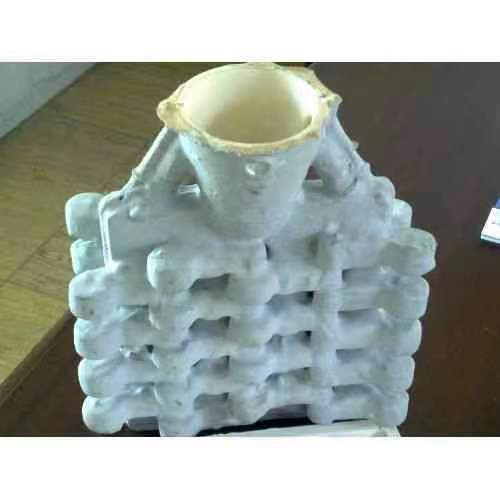
This casting method is ideal for creating complex shapes with tight tolerances and intricate details. Investment casting is commonly used in the aerospace, automotive, and medical industries for creating components such as turbine blades, engine parts, and dental implants.
The advantages of investment casting over other casting methods include:
- Ability to create intricate and complex shapes
- High precision and accuracy
- Smooth surface finish
- Reduction in material waste
- Capability to use a variety of metals and alloys
Investment casting is typically used for casting metals such as stainless steel, aluminum, and titanium. This casting method is suitable for both ferrous and non-ferrous metals. The process can also be used to create multi-alloy components by fusing different metals together.
In addition, investment casting can reduce machining costs as the final product requires little to no additional finishing. The process also allows for the creation of near-net-shape components, further reducing the need for machining.
Overall, investment casting offers numerous advantages over other casting methods, making it a popular choice for creating high-precision components with complex shapes and tight tolerances.
Comparing Sand Casting and Investment Casting
Now that we have examined sand casting and investment casting separately, it’s time to compare the two methods. When it comes to sand casting vs. investment casting, there are a few key differences to consider.
Sand Casting | Investment Casting | |
---|---|---|
Casting process | Uses sand molds to create the desired shape | Uses a wax pattern that is coated in refractory material to create the mold |
Surface finish | Rougher surface finish | Smooth surface finish |
Production runs | Ideal for low to medium volume production runs | Ideal for high volume production runs |
Suitability | Ideal for larger and simpler shapes | Ideal for complex and intricate shapes with tight tolerances |
Casting defects | Prone to casting defects such as shrinkage, porosity, and sand inclusions | Less prone to casting defects due to the use of expendable wax patterns |
While both sand casting and investment casting have their advantages and disadvantages, investment casting is generally considered the better option for creating high-quality, complex parts. Investment casting is also commonly used for casting stainless steel, due to its superior strength and quality. However, sand casting remains a popular choice for simpler parts and lower volume runs.
In the next section, we will briefly touch upon other casting methods that may be worth considering.
Comparing Sand Casting and Investment Casting
Other Casting Methods and Considerations
While sand casting and investment casting are prevalent casting methods, other techniques exist that may be better suited for your needs.
Die Casting: This process is ideal for mass-producing complex parts with high accuracy and dimensional consistency. Die casting utilizes a mold, typically made of steel, and is best suited for non-ferrous metals.
Centrifugal Casting: This process is used to create cylindrical objects such as pipes, tubes, and rings. Rotation is used to distribute the molten metal into the mold, resulting in a high-quality, dense product.
Permanent Mold Casting: In this process, a reusable mold, typically made of metal, is used to create parts. The process is best suited for high-volume production and is ideal for ferrous and non-ferrous metals.
When considering which casting method to use, it’s important to understand the properties of the metal or alloy being cast. Ferrous metals, such as steel and iron, are best suited for sand casting, while non-ferrous metals, such as aluminum and brass, are better suited for investment casting. However, other casting methods, such as die casting and permanent mold casting, can also be used for certain types of metals.
Ultimately, the choice of casting method depends on the specific needs of your project. It’s crucial to evaluate factors such as surface finish, production volume, and dimensional accuracy when selecting a casting method that will produce the desired results.
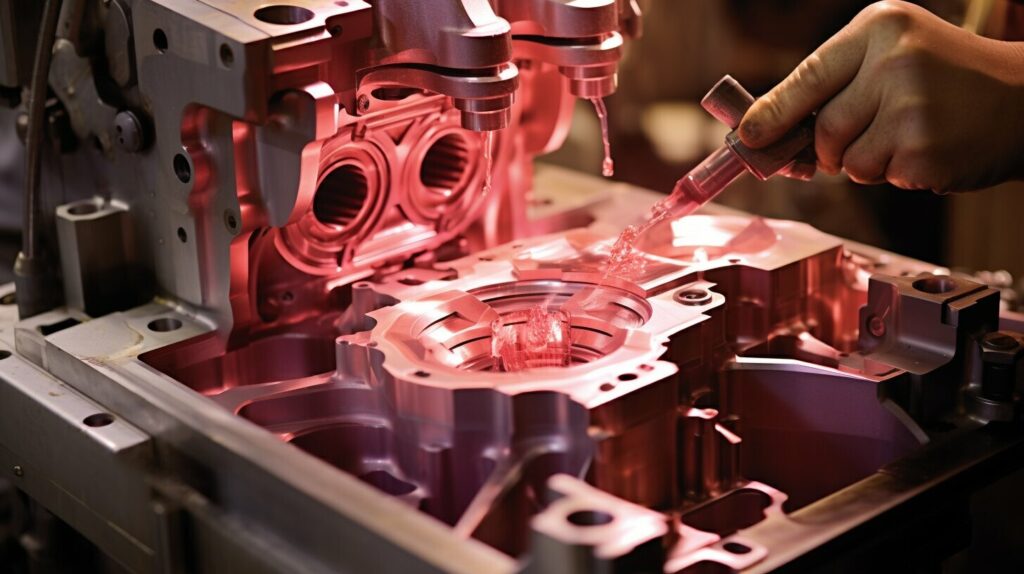
Conclusion
In conclusion, choosing between sand casting and investment casting depends on various factors, including the desired surface finish, production volume, and budget. While sand casting is a widely used method, investment casting offers numerous advantages such as the ability to create complex shapes with tight tolerances and reduced machining costs.
Investment casting also produces superior quality and strength when it comes to stainless steel casting. The investment casting process allows for the creation of intricate molds that result in high-quality castings that require minimal finishing. This means that the investment casting process reduces machining costs compared to other casting methods.
The Benefits of Investment Casting
Investment casting also enables the use of a wider range of materials, including both ferrous and non-ferrous metals. Whether casting small or large parts, investment casting provides a cost-effective solution to achieve high-quality, complex parts.
The investment casting process also allows for the creation of multiple complex parts in a single cast, resulting in reduced production time and costs. This is especially significant in large-volume productions where consistency and quality are crucial.
The Role of Casting Mold in Investment Casting
One of the key advantages of investment casting is the use of casting molds. These molds allow for high accuracy in the cast parts, which reduces or eliminates the need for additional machining. Such a reduction in machining reduces the cost of production significantly.
The casting molds are also created with high-quality materials, and they can be reused numerous times. This makes the investment casting process cost-effective and eco-friendly compared to other casting methods.
Overall, the investment casting process provides numerous advantages over sand casting and other casting methods. It is an ideal solution for producing high-quality, complex parts that require minimal machining and finishing.
FAQ
Q: What is sand casting?
A: Sand casting is a casting method that involves creating molds using sand as the mold material. Molten metal is then poured into the mold, allowing it to solidify and create the desired shape.
Q: What is investment casting?
A: Investment casting, also known as lost-wax casting or precision casting, is a casting method that uses a wax pattern to create a mold. The wax pattern is coated with a ceramic material, then heated to remove the wax. Molten metal is then poured into the ceramic mold to create the final casting.
Q: What are the advantages of sand casting?
A: Sand casting offers advantages such as lower tooling costs, suitability for large and complex parts, and the ability to cast various metals and alloys.
Q: What are the advantages of investment casting?
A: Investment casting allows for the creation of highly intricate and complex shapes, offers excellent surface finish, and produces parts with tight tolerances. It is also suitable for a wide range of metals and alloys.
Q: What are the disadvantages of sand casting?
A: Some disadvantages of sand casting include the possibility of casting defects, rougher surface finish compared to investment casting, and the need for additional machining or finishing operations.
Q: What are the disadvantages of investment casting?
A: Investment casting can have higher tooling costs compared to sand casting, and the process can be time-consuming. It may also not be suitable for very large or heavy parts.
Q: Which casting method is better for stainless steel?
A: Investment casting is often preferred for stainless steel casting due to its ability to produce high-quality, complex shapes with tight tolerances. It also results in reduced machining costs for stainless steel parts.
Q: Are there other casting methods besides sand casting and investment casting?
A: Yes, besides sand casting and investment casting, there are other casting methods such as die casting, centrifugal casting, and permanent mold casting.
Q: Which metals are suitable for the casting process?
A: The casting process can be used for both ferrous and non-ferrous metals, including stainless steel, aluminum, bronze, and various alloys.