When it comes to manufacturing high-quality metal parts for consumer goods, one method stands out: aluminum die casting. This innovative process produces precise and smooth metal components with exceptional durability. At our company, we understand the importance of delivering products that meet the highest standards of quality and reliability. That’s why we rely on aluminum die casting for our consumer goods. Let’s explore why this process is the go-to choice for producing top-notch products that last.
Key Takeaways:
- Aluminum die casting produces accurately defined and textured-surfaced metal parts.
- It offers advantages such as corrosion resistance, high conductivity, and a high strength-to-weight ratio.
- The rapid production capabilities of aluminum die casting make it cost-effective and efficient for high-volume production.
- Aluminum die castings are ideal for complex part geometries and thin walls in consumer goods.
- Choosing aluminum die casting ensures the strength, durability, and longevity of your products.
Advantages of Aluminum Die Casting
Aluminum die casting offers numerous advantages in the manufacturing industry. One of the key benefits is the lightweight nature of aluminum die castings, which allows for the creation of lightweight components without compromising on strength. This makes aluminum die castings ideal for industries where weight reduction is crucial, such as automotive and aerospace.
Another advantage of aluminum die casting is its excellent corrosion resistance. Aluminum naturally forms a protective oxide layer when exposed to air, which helps prevent corrosion. This makes aluminum die castings suitable for use in various environments, including outdoor and marine applications.
Rapid production capabilities are another significant advantage of aluminum die casting. The process allows for cost-effective mass production, making it a preferred choice for industries that require high volumes of parts in a short period. The ability to produce complex shapes and thin walls with excellent dimensional stability further enhances its efficiency and cost-effectiveness.
Aluminum die casting enables the production of finished products with excellent surface finishes, making it a favored choice for industries that emphasize aesthetics and quality.
In summary, the advantages of aluminum die casting include lightweight components, corrosion resistance, and rapid production capabilities. These factors contribute to the popularity of aluminum die casting in various industries, ensuring the production of high-quality, durable, and efficient consumer goods.
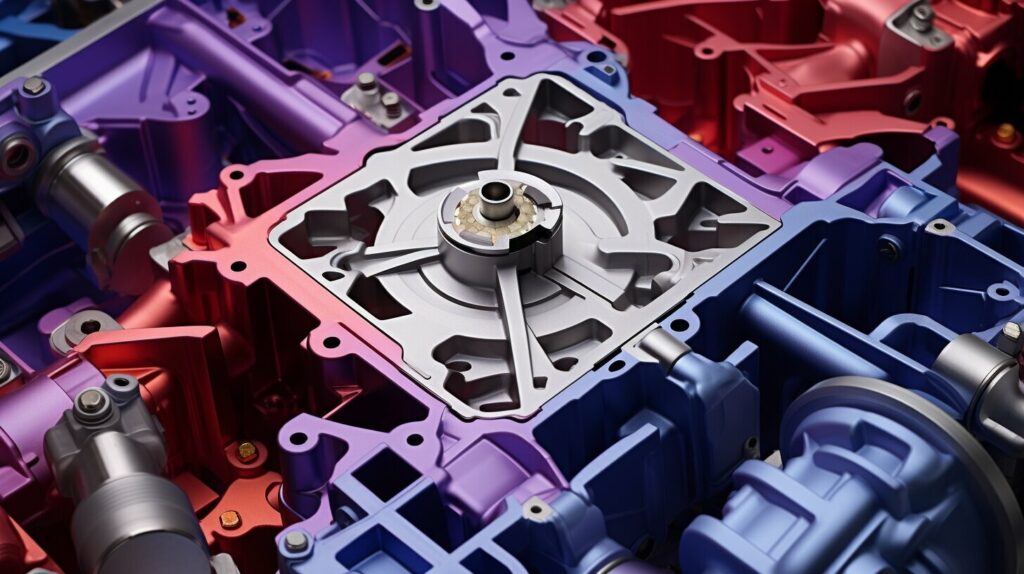
Aluminum Die Casting Product Segmentation
Aluminum die casting is a versatile manufacturing process that finds applications in various industries. Let us explore some of the key sectors where aluminum casting products are widely used.
Transportation Sector
One of the prominent areas where aluminum die castings have made a significant impact is the transportation sector. With increasing fuel efficiency requirements and the need for lightweight components, aluminum castings have become the go-to choice for automotive companies. The use of aluminum in engines, transmission housings, and other critical parts helps reduce overall weight without compromising on strength and safety. This, in turn, contributes to improved fuel efficiency and performance.
Aerospace Industry
The aerospace industry is another sector that relies heavily on aluminum die castings. In the quest for creating dense and high-quality parts at lower costs, manufacturers in the aerospace sector have turned to die casting as an effective solution. Aluminum castings offer the required precision, durability, and strength necessary for aerospace components, while also meeting stringent quality standards. The use of aluminum castings in aircraft wings, engine components, and structural elements helps reduce weight, enhance fuel efficiency, and improve overall performance.
Asia Pacific Region
The Asia Pacific region, particularly China, plays a crucial role in the global market for aluminum castings. It holds the largest share in the market and is expected to continue its growth trajectory in the coming years. The region’s dominance can be attributed to the booming automotive and aerospace industries, increased infrastructure development, and the presence of a large manufacturing base. With its favorable economic conditions and rising consumer demand, the Asia Pacific region offers immense opportunities for aluminum die casting manufacturers.
Industry | Key Applications |
---|---|
Transportation | Automotive components, engine parts, transmission housings |
Aerospace | Aircraft wings, engine components, structural elements |
Asia Pacific Region | China, India, Japan, South Korea |
With its wide range of advantages and diverse applications, aluminum die casting continues to shape industries and deliver exceptional results in terms of performance, durability, and cost-effectiveness.
Alternatives to Die Casting – Sand and Investment Casting
While die casting is a popular manufacturing process, there are alternatives available that offer their own unique advantages. Two commonly used alternatives to die casting are sand casting and investment casting.
Sand Casting
Sand casting is the oldest and most widely used casting method in the industry. It involves pouring molten metal into sand molds without using high pressure. Sand casting offers versatility in creating parts with various shapes, sizes, and complexities. It is a cost-effective option for producing large and heavy components, making it suitable for applications such as automotive engine blocks, cylinder heads, and other large industrial parts.
Investment Casting
Investment casting, also known as precision casting, is a process that uses molds made from wax patterns or refractory materials. It allows for the production of intricate and highly detailed parts with tight tolerances. Investment casting is commonly used in industries such as aerospace, firearms, jewelry, and dental, where the quality and precision of the finished product are of utmost importance. It produces parts with excellent surface finishes and dimensional accuracy.
Both sand casting and investment casting have their own advantages and are suitable for different applications. Sand casting is a cost-effective option for producing large and heavy components, while investment casting is ideal for creating intricate and precise parts. Manufacturers must consider factors such as cost, complexity, production volume, and part size when deciding between these alternatives to die casting.
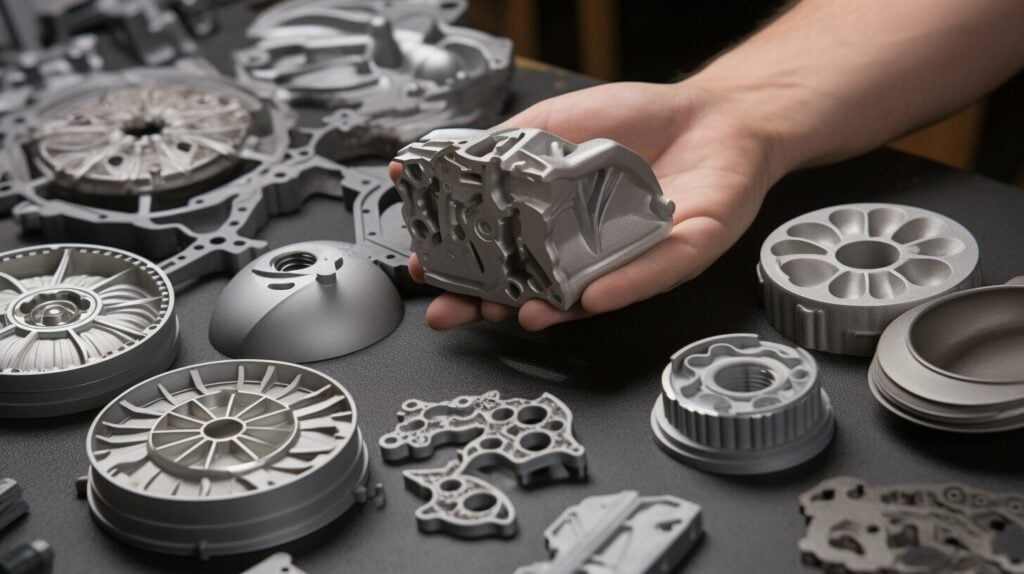
Aluminum Die Casting Process and Surface Finishing Options
When it comes to aluminum die casting, the process involves heating and melting aluminum at high temperatures before injecting it into pre-shaped molds with the help of high-pressure injection. This manufacturing technique can be carried out using either a hot chamber or a cold chamber machine, depending on the specific requirements of the project at hand.
Once the casting process is complete, there are several surface finishing options available to enhance the final product’s aesthetics and performance. One popular choice is anodizing, which involves creating a corrosion-resistant and durable protective layer on the surface of the die-cast aluminum. Anodizing not only enhances the appearance of the finished product but also provides added protection against wear and tear.
Another surface finishing option is powder coating. This technique involves applying a dry powder to the die-cast aluminum surface, which is then cured under heat to form a protective and decorative coating. Powder coating offers a wide range of colors and textures, allowing manufacturers to customize the appearance of their products while also improving durability.
In addition, chem film, also known as chromate conversion coating, is a surface finishing option commonly used in the aerospace industry. It involves applying a conversion coating to the die-cast aluminum surface to enhance its corrosion resistance and provide electrical conductivity. Chem film is often used on parts that require reliable electrical grounding or when a conductive surface is needed.
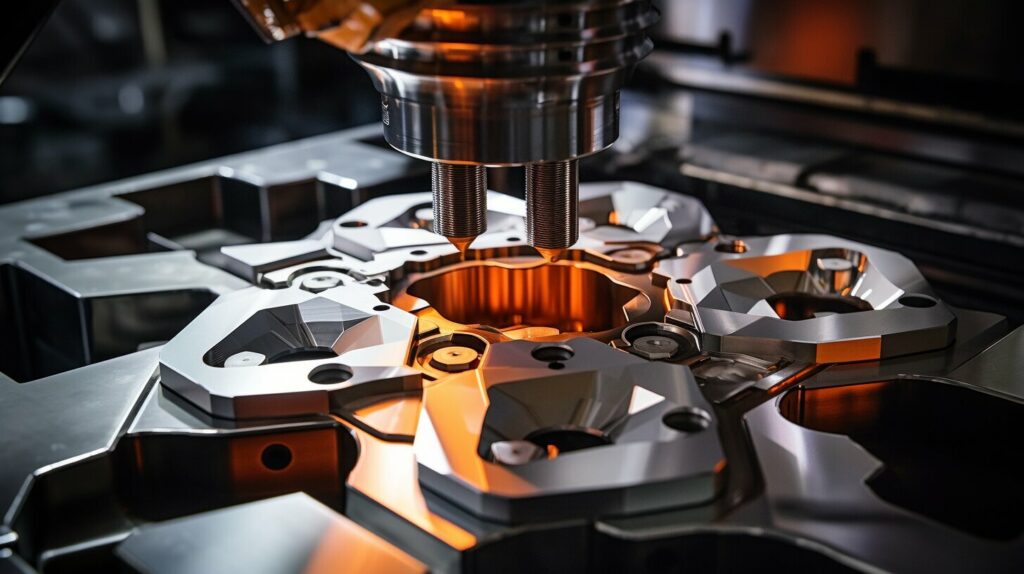
Comparative Overview of Surface Finishing Options:
Surface Finishing Option | Advantages |
---|---|
Anodizing | – Corrosion resistance – Durable protective layer – Aesthetically appealing |
Powder Coating | – Wide range of colors and textures – Enhanced durability – Customizable appearance |
Chem Film | – Improved corrosion resistance – Electrical conductivity – Suitable for aerospace applications |
“The surface finishing options available for aluminum die casting allow us to not only protect the finished products from corrosion but also enhance their appearance and performance. Whether it is anodizing, powder coating, or chem film, each option offers unique benefits that cater to different industry requirements.”
With these various surface finishing options, manufacturers can ensure that their aluminum die castings not only meet the desired standards of quality and durability but also have an appealing aesthetic appeal. The choice of surface finishing option depends on the functional requirements and desired appearance of the final product, allowing for versatility in design and performance.
Conclusion
In conclusion, aluminum die casting is a highly reliable and efficient manufacturing process that delivers exceptional quality and durability for consumer goods. With its ability to produce accurately defined, smooth, and textured-surfaced metal parts, this process is ideal for creating lightweight components without compromising strength. The corrosion resistance and excellent dimensional stability of aluminum die castings make them a preferred choice in various industries.
By choosing aluminum die casting, manufacturers can ensure the longevity and reliability of their products. The rapid production capabilities of this process allow for cost-effective mass production, making it a practical solution for high-volume manufacturing. With the ability to create complex shapes and thin walls, aluminum die casting finds extensive applications in the transportation, aerospace, electronics, furniture, and construction industries.
Investing in aluminum die casting guarantees the production of high-quality parts that meet the stringent requirements of consumer goods. The advantages of this process, including its lightweight nature, excellent surface finishes, and corrosion resistance, ensure that products manufactured using aluminum die castings will stand the test of time. As the demand for durable and high-performing consumer goods continues to rise, aluminum die casting remains an indispensable manufacturing process.
FAQ
What is aluminum die casting?
Aluminum die casting is a manufacturing process that produces accurately defined, smooth, and textured-surfaced metal parts by forcing molten metals, such as aluminum, into a mold form using high-pressure systems.
What are the advantages of aluminum die casting?
Aluminum die castings offer advantages such as corrosion resistance, high conductivity, good stiffness, and a high strength-to-weight ratio. The process allows for rapid production, making it cost-effective and efficient for producing high volumes of parts quickly. Aluminum die castings also have excellent dimensional stability for complex part geometries and thin walls, making them ideal for use in consumer goods.
What industries use aluminum die casting?
Aluminum die casting is used in various industries, including the transportation sector and the aerospace industry. It is also popular in the production of consumer goods.
What are the alternatives to die casting?
The alternatives to die casting are sand casting and investment casting. Sand casting is the oldest and most widely used casting method, while investment casting uses molds made from wax patterns or refractory materials.
How does the aluminum die casting process work?
The aluminum die casting process involves heating and melting aluminum at a high temperature, then forcing it into pre-shaped molds using high-pressure injection. The process can be done using a hot chamber or cold chamber machine, depending on the specific requirements.
What surface finishing options are available for aluminum die castings?
There are several surface finishing options available for aluminum die castings, including anodizing, powder coating, and chem film. Anodizing creates a corrosion-resistant and durable protective layer, powder coating enhances durability and provides a range of colors and textures, and chem film provides electrical conductivity while offering protection against corrosion.