Welcome to KT-Foundry, where we excel in the art of aluminum die casting, ensuring the highest quality and reliability for our products. As experts in the field, we understand the importance of mastering the steps involved in the aluminum die casting process. By carefully navigating each stage, we are able to produce top-tier, robust products that meet the needs of our customers.
Aluminum die casting is a high-pressure manufacturing process that involves injecting molten aluminum into a mold cavity to form a desired shape. This method is widely used in various industries due to its versatility, cost-effectiveness, and ability to create complex shapes with high dimensional accuracy.
During the die casting process, several key steps are critical to achieving the desired outcomes. These steps include creating the die cavity, ensuring dimensional accuracy, ejecting the solidified part, and optimizing the surface finish while minimizing shrinkage. By mastering each of these steps, we are able to create aluminum castings that meet the highest standards of quality and performance.
One of the crucial factors in the aluminum die casting process is the selection of the right aluminum alloy. Different alloys offer varying mechanical properties, corrosion resistance, and porosity levels. By carefully considering these factors, we can ensure that the final product meets the specific requirements of our customers.
Dimensional accuracy is another key aspect of the die casting process. Through meticulous design and precise execution, we are able to create two halves of the die that come together to form castings with precise dimensions. Additionally, controlling the wall thickness of the cast parts is crucial to achieving the desired properties and performance.
Efficiency is a hallmark of die casting production. With high production rates and minimal waste of excess material, we are able to produce large quantities of parts quickly and cost-effectively. This makes aluminum die casting an ideal choice for industries that require high volumes of components.
There are numerous advantages to utilizing aluminum die casting in various industries. Its lightweight properties, fuel efficiency, and ability to create complex shapes make it a preferred choice, especially in applications such as the aerospace industry.
Looking towards the future, advancements in technologies such as 3D printing in mold-making and alternative casting processes offer exciting possibilities for the aluminum die casting industry. Companies like Tesla are already exploring innovative die-casting techniques to revolutionize vehicle manufacturing, further driving the evolution of this manufacturing technique.
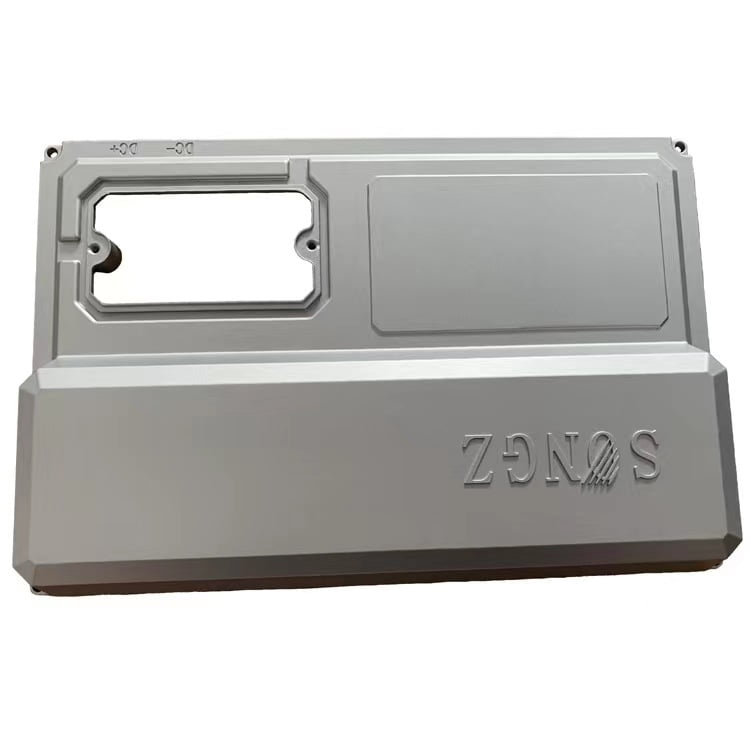
- Mastering the steps of aluminum die casting is crucial for producing top-tier, robust products.
- The selection of the right aluminum alloy is essential to achieve the desired mechanical properties and performance.
- Precise dimensional accuracy and control over wall thickness are vital for ensuring high-quality castings.
- Aluminum die casting offers efficiency in production, allowing for high volumes of parts to be produced quickly and cost-effectively.
- Advantages of aluminum die casting include its lightweight properties, fuel efficiency, and the ability to create complex shapes.
Understanding the Aluminum Die Casting Process
The aluminum die casting process is a high-pressure manufacturing technique that allows us to create intricate parts and prototypes with exceptional precision. By utilizing this method, we are able to produce durable products that meet the highest industry standards. With our expertise in aluminum die casting, we can deliver top-quality components for various applications, ranging from automotive to aerospace industries.
One of the key features of the high-pressure die casting process is its ability to rapidly produce complex shapes with consistency. The molten aluminum is injected into a die cavity under high pressure, ensuring that every detail of the mold is faithfully reproduced. This technique enables us to manufacture intricately designed parts that would be difficult or costly to produce using other manufacturing methods.
Prototyping is an essential part of the aluminum die casting process. It allows us to validate the design and functionality of the component before proceeding with mass production. Through prototyping, we can identify any areas that require adjustments or improvements, ensuring that the final product meets the required specifications. This iterative process helps us optimize the design, reduce production costs, and accelerate the time to market.
To further illustrate the significance of the aluminum die casting process, let’s take a look at an example from the automotive industry. Tesla, the renowned electric vehicle manufacturer, is close to implementing a new die-cast process that could revolutionize vehicle manufacturing. By casting the entire vehicle underbody as a single piece using an updated mold-making process with 3D printing and industrial sand, Tesla aims to reduce costs and simplify production. This innovative technique allows for the creation of a hollow subframe without the need for welding, contributing to the company’s goal of halving the manufacturing costs of its electric vehicles.
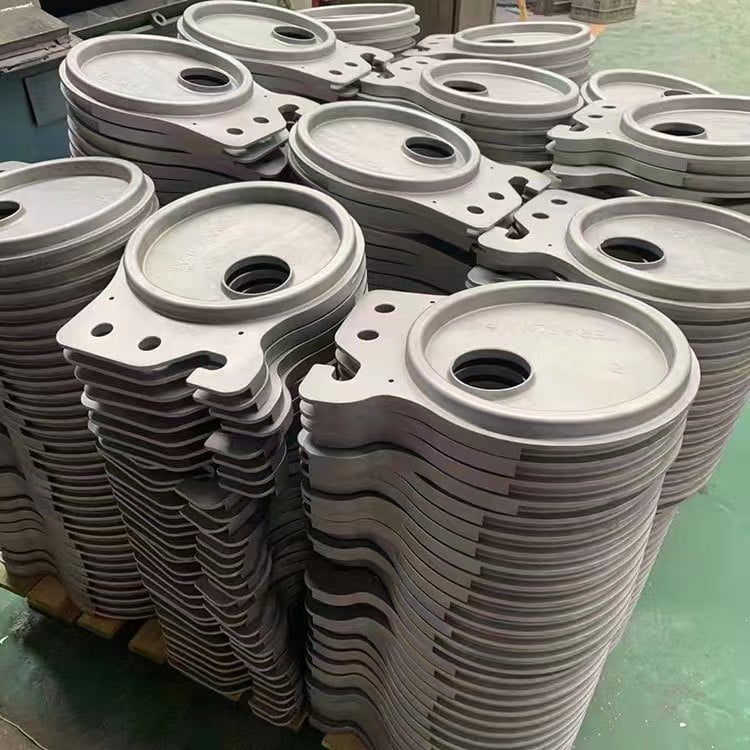
- Exceptional precision in creating complex shapes
- Rapid production with high consistency
- Ability to prototype and refine the design
- Reduction in production costs and time to market
By leveraging the aluminum die casting process, we can deliver high-quality products that meet the demands of various industries. Whether it’s producing intricate components or prototyping innovative designs, our expertise and dedication ensure that we consistently deliver exceptional results.
Navigating the Steps of Aluminum Die Casting
To ensure the highest quality end products, our aluminum die casting process involves meticulous attention to detail at every step. One of the key aspects of the process is the creation of the die cavity, which serves as the mold for the final product. This cavity is designed to have the exact dimensions and shape required for the desired part. Achieving dimensional accuracy is crucial to ensure that the final product meets the specifications and requirements of our clients.
Once the die cavity is ready, the next step is to carefully inject molten aluminum into the cavity. This is done under high pressure to ensure that the aluminum fills all the intricate details and corners of the mold. The high-pressure aspect of the process also helps in achieving a dense and solid structure, minimizing the risk of porosity and defects in the final product.
After the molten aluminum has solidified and taken the shape of the die cavity, the next step is the ejection of the part. This process requires precision to ensure that the solidified part is safely removed from the mold without causing any damage. Our skilled technicians carefully monitor this step to maintain the dimensional accuracy and surface finish of the part.
Surface finish is an important consideration in aluminum die casting. It determines the appearance and overall quality of the final product. To achieve the desired surface finish, the mold is carefully designed and polished to minimize any imperfections or blemishes. Additionally, proper control of the casting parameters and the use of appropriate release agents help in ensuring a smooth and flawless finish.
Table 1: Key Steps in the Aluminum Die Casting Process
Step | Description |
---|---|
Creation of Die Cavity | The mold for the final product is created with precision and accuracy, ensuring the desired dimensions and shape. |
Molten Aluminum Injection | Molten aluminum is injected into the die cavity under high pressure, filling all intricate details and corners. |
Ejection of the Part | The solidified part is carefully ejected from the mold, maintaining dimensional accuracy and surface finish. |
Surface Finish | The mold is designed and polished to achieve the desired surface finish, minimizing imperfections and blemishes. |
In addition to these steps, minimizing shrinkage is also a crucial aspect of the aluminum die casting process. Shrinkage refers to the reduction in size that occurs during the cooling and solidification of the molten aluminum. Our technicians carefully analyze the design and mold parameters to minimize shrinkage and ensure that the final product meets the dimensional requirements.
By navigating these steps with expertise and precision, we are able to produce high-quality aluminum die cast products that meet the strictest industry standards. Our commitment to excellence in every aspect of the process is what sets us apart and makes us a trusted partner in aluminum die casting manufacturing.
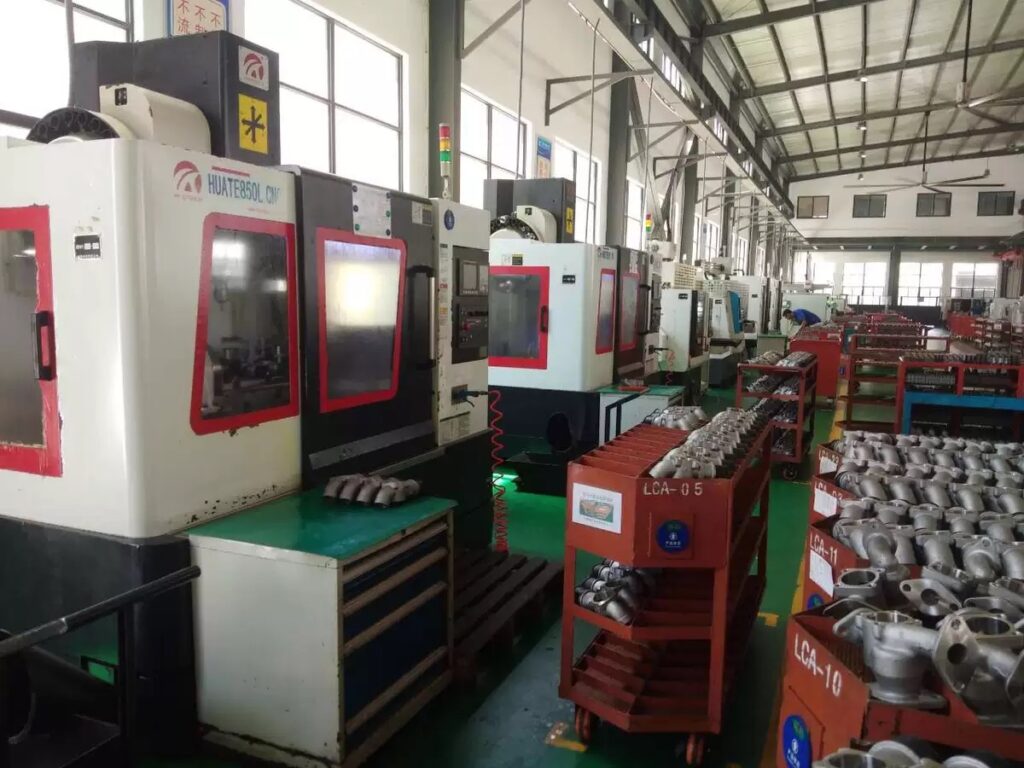
The choice of aluminum alloy plays a crucial role in determining the strength, durability, and overall quality of our die cast products. At KT-Foundry, we understand the significance of selecting the right alloy for each application, considering factors such as mechanical properties, corrosion resistance, and porosity. By carefully analyzing these aspects, we can ensure that our aluminum die castings meet the highest standards and exceed customer expectations.
One of the key considerations when selecting an aluminum alloy is its mechanical properties. Different alloys offer varying levels of strength, hardness, and ductility, allowing us to tailor our products to specific needs. For applications where high strength is crucial, we may opt for alloys such as 6061 or 7075, known for their excellent mechanical properties. On the other hand, if lightweight is a priority, alloys like 3003 or 5052 may be more suitable.
Corrosion resistance is another critical factor in aluminum alloy selection. Depending on the application, our engineers may choose alloys like 5083 or 5754, which exhibit exceptional resistance to corrosion in harsh environments. These alloys are commonly used in marine and offshore applications where exposure to saltwater or acidic conditions is prevalent.
Porosity, or the presence of small voids or air pockets within the castings, can significantly affect the quality and integrity of the final product. Our expert team at KT-Foundry carefully considers the porosity characteristics of different aluminum alloys to minimize any potential defects. By selecting alloys with low gas solubility and employing precise casting techniques, we can deliver castings with minimal porosity, ensuring superior performance and reliability.
Table 1: Comparison of Aluminum Alloys for Die Casting
Alloy Number | Mechanical Properties | Corrosion Resistance | Porosity |
---|---|---|---|
6061 | High strength, good machinability | Fair | Low |
7075 | Very high strength, excellent fatigue resistance | Good | Low |
3003 | Good formability, excellent corrosion resistance | Excellent | Low |
5052 | Medium strength, exceptional weldability | Good | Low |
5083 | High strength, excellent resistance to marine environments | Excellent | Low |
5754 | Good strength, superior corrosion resistance | Excellent | Low |
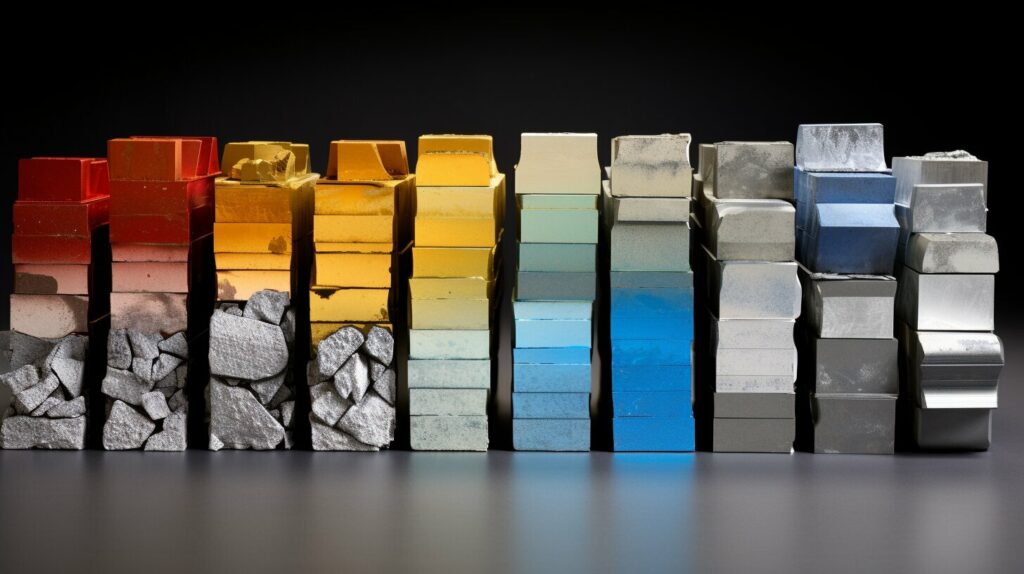
By carefully considering the suitability of different aluminum alloys based on their mechanical properties, corrosion resistance, and porosity characteristics, we ensure that our die cast products meet the highest standards and provide exceptional performance in diverse applications. At KT-Foundry, we are committed to mastering the art of aluminum alloy selection to deliver top-tier, robust die castings that exceed customer expectations.
Achieving High-Quality Dimensional Accuracy
Our commitment to high-dimensional accuracy ensures that our aluminum die cast parts meet the strictest specifications and requirements. We understand the importance of precise dimensions in the production of top-tier, robust products. To achieve this level of accuracy, we employ a meticulous process that involves careful attention to detail and the use of advanced technologies.
When it comes to dimensional accuracy, the creation of the two halves of the die is crucial. These halves are carefully crafted to exact specifications, ensuring that the desired dimensions of the final product are achieved. Our experienced team of professionals meticulously designs and constructs the die, taking into account factors such as material shrinkage and variation in wall thickness.
In addition to precision die construction, we also pay close attention to the walls and wall thickness of the cast parts. We use advanced techniques to control the wall thickness, ensuring uniformity and consistency throughout the product. This attention to detail not only enhances the dimensional accuracy but also contributes to the overall strength and performance of the cast parts.
Our dedication to achieving high-quality dimensional accuracy sets us apart in the industry. We understand that even the slightest deviation from the specified dimensions can impact the functionality and reliability of the final product. That is why we go above and beyond to ensure that our aluminum die cast parts meet and exceed the strictest standards, providing our clients with superior quality and performance.
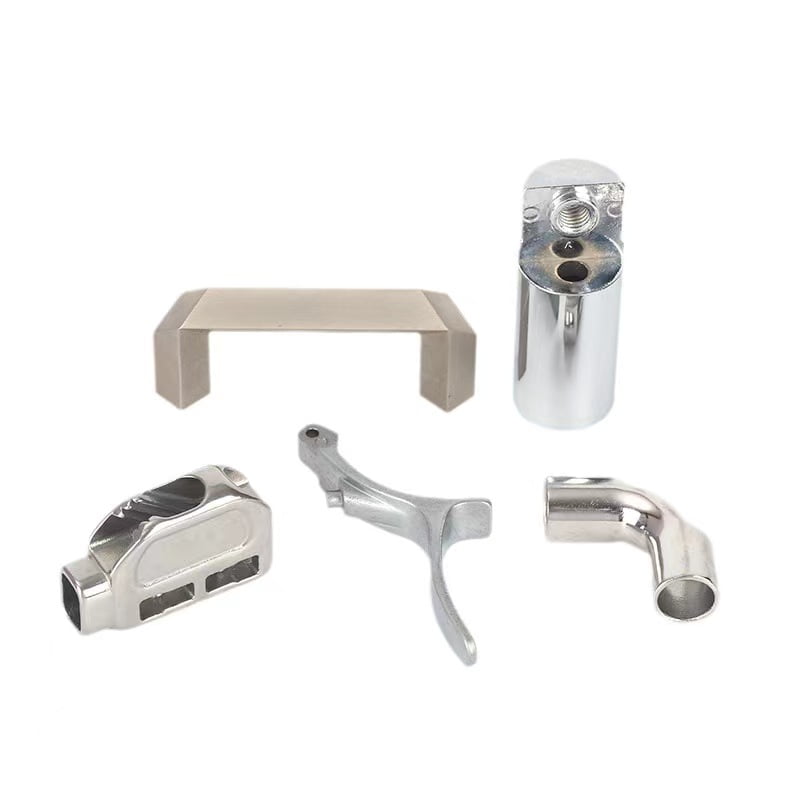
Advantages of High-Quality Dimensional Accuracy: |
---|
1. Precise fit and assembly for seamless integration with other components. |
2. Enhanced structural integrity and strength. |
3. Improved efficiency and performance of the final product. |
4. Cost savings through reduced rework and rejects. |
5. Increased customer satisfaction and trust in our products. |
Ensuring Efficient Die Casting Production
Our aluminum die casting process offers high production rates and exceptional efficiency, allowing us to meet the demands of large-scale manufacturing. With our state-of-the-art facilities and skilled team, we are able to optimize every step of the process to maximize productivity and minimize waste.
One of the key advantages of our die casting production is the ability to achieve high production rates. Our advanced machinery and optimized workflows enable us to quickly produce a large quantity of high-quality parts. This is particularly beneficial for industries that require mass production, such as automotive, aerospace, and electronics.
By leveraging our expertise in die casting, we are able to minimize the waste of excess material. Our precise design and engineering techniques ensure that each part is created with the minimum amount of material required, reducing costs and environmental impact.
Advantages of Our Die Casting Production | ||
---|---|---|
High production rates | Minimized waste of excess material | Cost-effective large-scale production |
Consistent quality control | Shorter lead times | Flexible customization options |
Our die casting production also offers several benefits in terms of quality and customization. By maintaining rigorous quality control measures throughout the production process, we ensure that each part meets the highest industry standards. Additionally, our efficient production methods allow for shorter lead times, enabling us to deliver products to our clients in a timely manner.
Moreover, our die casting process allows for flexible customization options. Whether it’s specific design requirements, surface finishes, or dimensional accuracy, we have the capabilities to tailor our production to meet the unique needs of our clients.
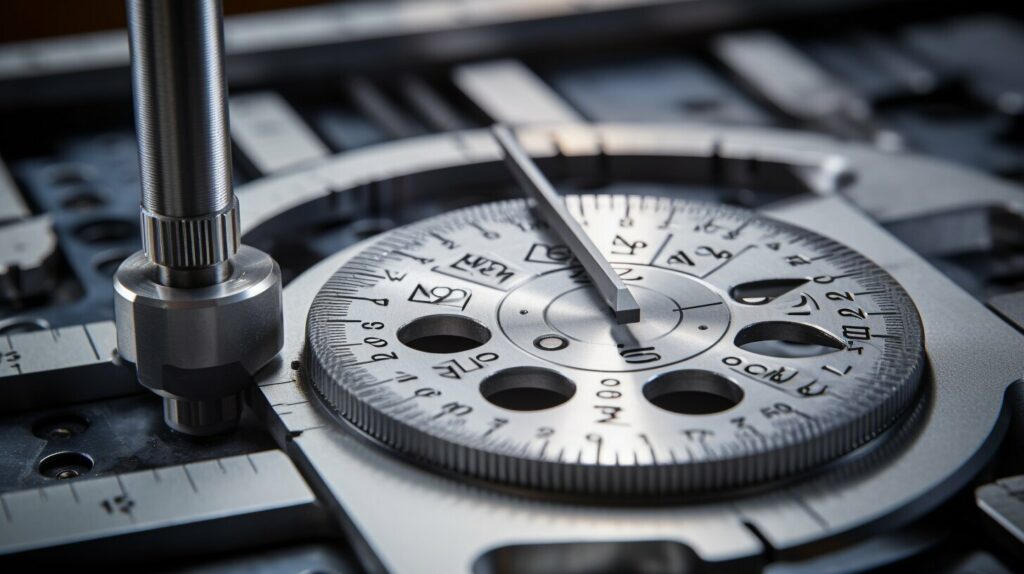
Looking to the Future
“As we continue to invest in research and development, we are constantly exploring ways to further enhance our die casting production techniques. We are excited about the advancements in alternative casting processes, such as 3D printing, which has the potential to revolutionize the industry. We are also closely following Tesla’s innovative approach to die-casting, as they push the boundaries of what is possible in vehicle manufacturing.”
In summary, our aluminum die casting process offers high production rates, exceptional efficiency, and a range of customization options. With our commitment to continuous improvement and the adoption of emerging technologies, we remain at the forefront of the die casting industry.
Advantages of Aluminum Die Casting
Aluminum die casting offers numerous advantages, making it the ideal choice for a wide range of industries and applications. One of the key benefits is its fuel efficiency. The lightweight nature of aluminum makes it an excellent option for industries such as automotive, where reducing weight can significantly impact fuel consumption. By utilizing aluminum die casting, manufacturers can produce components that are both strong and lightweight, contributing to improved fuel economy.
Additionally, the versatility of aluminum die casting allows for the creation of complex shapes with precision. This makes it particularly attractive in industries that require intricate designs, such as aerospace. Aluminum die casting provides the ability to produce intricate parts with high dimensional accuracy, enabling the manufacturing of complex components that would be challenging to achieve with other methods.
The lightweight properties of aluminum also make it highly desirable in the aerospace industry. By incorporating aluminum die-cast parts, aircraft can benefit from reduced weight, resulting in improved performance and increased efficiency. These lightweight components contribute to lower fuel consumption, allowing aircraft to carry more passengers or cargo without compromising safety or reliability.
To illustrate the advantages of aluminum die casting, let’s look at an example from the automotive industry. Tesla, the renowned electric vehicle manufacturer, is on the brink of implementing a groundbreaking die-cast process. By utilizing an updated mold-making process, Tesla aims to cast the entire vehicle underbody as a single piece. This innovative technique, combined with 3D printing and industrial sand, enables the creation of a hollow subframe without the need for welding.
This revolutionary approach has the potential to simplify production, reduce costs, and enhance the efficiency of Tesla’s assembly line. By halving the manufacturing costs of its electric vehicles, Tesla is driving the industry forward and opening up new possibilities for the future of die casting.
The Future of Aluminum Die Casting
The future of aluminum die casting looks promising, with advancements in 3D printing and other manufacturing techniques pushing the boundaries of what’s possible. One exciting development on the horizon is Tesla’s new die-cast process, which has the potential to revolutionize vehicle manufacturing. By casting the entire vehicle underbody as a single piece using an updated mold-making process with 3D printing and industrial sand, Tesla aims to reduce costs and simplify production.
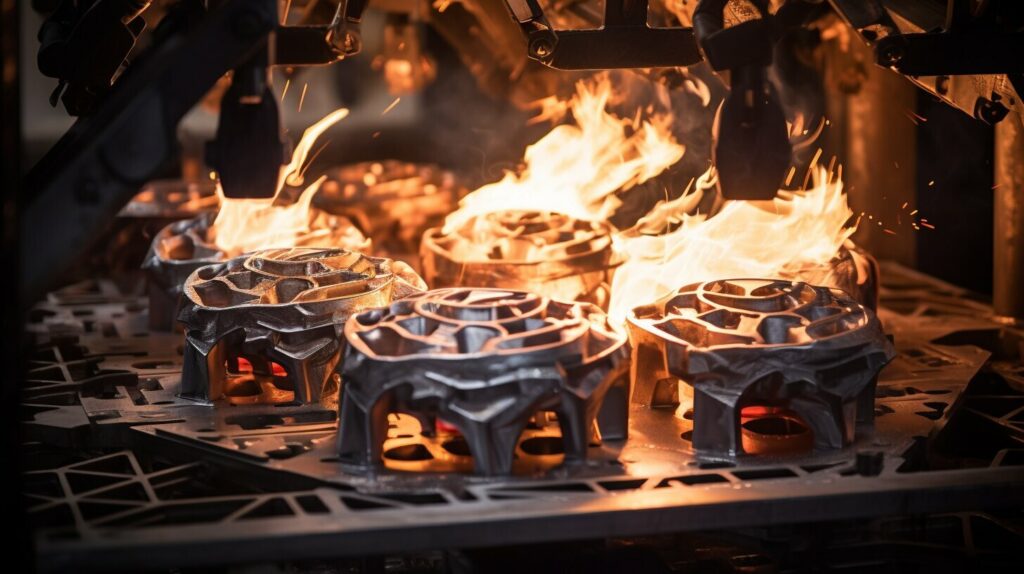
This innovative technique allows for the creation of a hollow subframe without the need for welding. By eliminating joints and seams, the structural integrity of the vehicle is enhanced, resulting in increased safety and durability. Additionally, the use of 3D printing in mold-making enables greater design flexibility, allowing for the production of complex and lightweight components.
However, there are some challenges to overcome in implementing this new process. One key challenge is the requirement for more powerful “gigapresses” capable of exerting the necessary force to cast large vehicle components in a single piece. Furthermore, the integration of the 3D-printed sand core technique may present technical difficulties that need to be addressed.
If successfully implemented, this revolutionary die-cast process could have far-reaching implications, not only for Tesla but for the entire automotive industry. It has the potential to speed up the assembly line process, increase manufacturing efficiency, and contribute to Tesla’s goal of halving the manufacturing costs of its electric vehicles. As advancements in 3D printing and other manufacturing techniques continue to push the boundaries of what’s possible, we can expect to see further innovations and advancements in aluminum die casting in the years to come.
In Summary
Mastering the steps of aluminum die casting is essential for delivering high-quality, reliable products that meet the stringent demands of various industries. At KT-Foundry, we understand the importance of expertise in the manufacturing process, and we pride ourselves on our knowledge and experience in aluminum die casting.
By understanding the aluminum die casting process and navigating its steps meticulously, we ensure the production of robust products. Our dedication to achieving dimensional accuracy, controlling wall thickness, and selecting the right aluminum alloy contributes to the high quality of our castings.
Furthermore, the advantages of aluminum die casting are significant. Its lightweight properties, ability to create complex shapes, and fuel efficiency make it a desirable choice in industries such as automotive and aerospace. The future of aluminum die casting looks promising, with emerging technologies like 3D printing and alternative casting processes on the horizon.
As we strive for excellence in our die casting production, we draw inspiration from companies like Tesla, who are pushing the boundaries of vehicle manufacturing. Tesla’s innovative die-cast process, utilizing 3D printing and industrial sand, could revolutionize the industry by reducing costs and simplifying production. While some challenges need to be overcome, this technique has the potential to speed up assembly line processes and advance the goal of more affordable electric vehicles.
FAQ
What is the new die-cast process being implemented by Tesla?
The new die-cast process being implemented by Tesla involves casting the entire vehicle underbody as a single piece using an updated mold-making process with 3D printing and industrial sand. This allows for the creation of a hollow subframe without the need for welding.
How does this new process revolutionize vehicle manufacturing?
This new die-cast process has the potential to revolutionize vehicle manufacturing by reducing costs and simplifying production. It eliminates the need for welding and allows for the creation of a more lightweight and efficient underbody. It could also speed up Tesla’s assembly line process and contribute to its goal of halving the manufacturing costs of its electric vehicles.
What are the challenges that need to be overcome for this new process?
There are a few challenges that need to be overcome for this new die-cast process. One challenge is the need for more powerful “gigapresses” to handle the casting of the entire underbody as a single piece. Another challenge is potential issues with the 3D-printed sand core technique, which is used to create the hollow subframe.
What are the potential benefits of this new die-cast process?
The potential benefits of this new die-cast process include cost reduction, simplified production, increased efficiency, and improved overall vehicle performance. By eliminating the need for welding and creating a more lightweight underbody, Tesla vehicles could become more affordable, environmentally friendly, and technologically advanced.
How does this new process align with Tesla’s goals?
This new die-cast process aligns with Tesla’s goals of reducing manufacturing costs and advancing vehicle technology. By implementing this process, Tesla aims to streamline its assembly line, improve efficiency, and ultimately make electric vehicles more accessible to the general public.