Ensuring the safe and efficient use of carbon steel castings in various applications is of utmost importance at KT-Foundry. This is achieved through employing a comprehensive range of Non-Destructive Testing Methods that allow for defect detection without causing any harm or destruction to the material. Our industrial NDT solutions include advanced techniques such as Visual inspection, Ultrasonic testing, Magnetic Particle Inspection, Radiographic Testing, and Dye Penetrant Testing, which help maintain the structural integrity of low carbon steel A588 – a material known for its high strength and weathering characteristics, often utilized in structures such as bridges and transmission towers.
Key Takeaways
- KT-Foundry uses a variety of NDT methods for defect detection in carbon steel castings.
- NDT techniques are critical in ensuring material reliability and structural integrity.
- Visual inspection, Ultrasonic testing, and Magnetic Particle Inspection are some of the advanced NDT techniques employed at KT-Foundry.
- Non-Destructive Testing plays a significant role in quality control and safety assurance in steel castings.
- Effective implementation of NDT methods prevents potential failures in service and enhances overall carbon steel casting performance.
An Overview of Non-Destructive Testing in Cast Steel Production
Non-Destructive Testing (NDT) plays a vital role in maintaining quality control throughout all stages of cast steel production, from raw material evaluation to in-service inspections. By leveraging various NDT techniques, we at KT Foundry ensure effective detection and assessment of diverse defects, including cracks, incomplete penetration, and porosity, which could pose service hazards if left unchecked. Our practices are designed to comply with Non-Destructive Evaluation (NDE) methodologies, focusing not only on defect detection but also on predicting the performance of steel castings through analysis and simulations to minimize development time and testing costs.
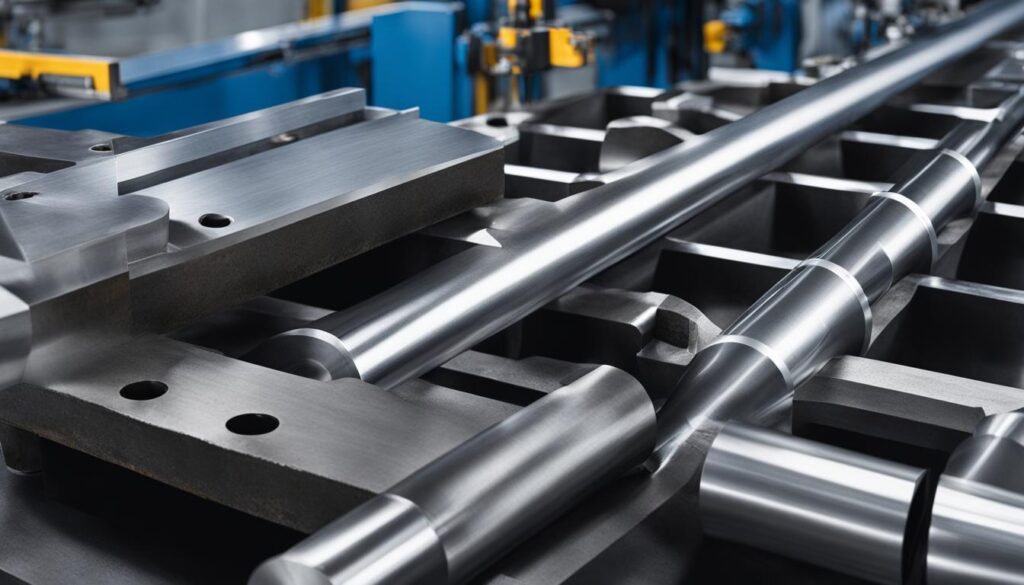
To emphasize the significance of NDT in guaranteeing the quality of cast steel products, we’ve compiled a brief overview of the primary techniques employed in cast steel production:
- Visual Inspection
- Magnetic Particle Testing (MPT)
- Ultrasonic Testing (UT)
- Penetrant Testing (PT)
- Radiographic Testing (RT)
Through the implementation of these various techniques, our manufacturing process achieves a robust quality assurance framework, resulting in consistently high standards of product performance and longevity.
Our commitment to Non-Destructive Testing yields reliable and high-quality cast steel products that meet the demanding requirements of various industry applications.
Broadening our understanding of the diverse NDT techniques available allows us to apply the most appropriate method for each stage of the production process. The table below outlines some of the essential features and applications of these techniques, demonstrating their value in ensuring the integrity of cast steel products.
NDT Technique | Applications | Advantages | Limitations |
---|---|---|---|
Visual Inspection | Assessment of surface defects, general material condition, and joint quality | Cost-effective, simple and quick method | Limited to surface defects, reliant on inspector skill and experience |
Magnetic Particle Testing | Detection of surface and near-surface discontinuities in ferromagnetic materials | High sensitivity, rapid results, easy interpretation | Restricted to ferromagnetic materials, depth sensitivity diminishes with material depth |
Ultrasonic Testing | Identification of internal and sub-surface defects, measurement of material thickness | High resolution, accurate sizing and location of defects, no risk of radiation exposure | Requires skilled inspection personnel, limited detectability in complex geometries or coarse grain structures |
Penetrant Testing | Detection of surface-breaking defects on nonporous materials | Effective on various materials, cost-efficient, visual indication of defects | Restricted to surface-breaking defects, surface must be free of contaminants |
Radiographic Testing | Inspection of subsurface and surface discontinuities, evaluation of material integrity | Comprehensive analysis, permanent record, applicable to a wide range of materials | Requires specialized equipment, potential safety hazards from radiation, limited defect sizing accuracy |
In conclusion, NDT enhances every aspect of cast steel production, improving component reliability, and minimizing the risk of service hazards. By utilizing the appropriate NDT techniques at critical stages of manufacturing, we ensure that our cast steel products meet stringent quality standards and consistently deliver the highest levels of performance.
The Significance of NDT for Carbon Steel Casting Integrity
The implementation of Non-Destructive Testing (NDT) is essential for maintaining the integrity of carbon steel castings at KT-Foundry. NDT plays a critical role in ensuring the quality of our castings by providing an extensive assessment of materials’ suitability and durability over their intended lifecycle. The application of NDT methods helps prevent potential failures in service by identifying and rectifying any issues that may arise.
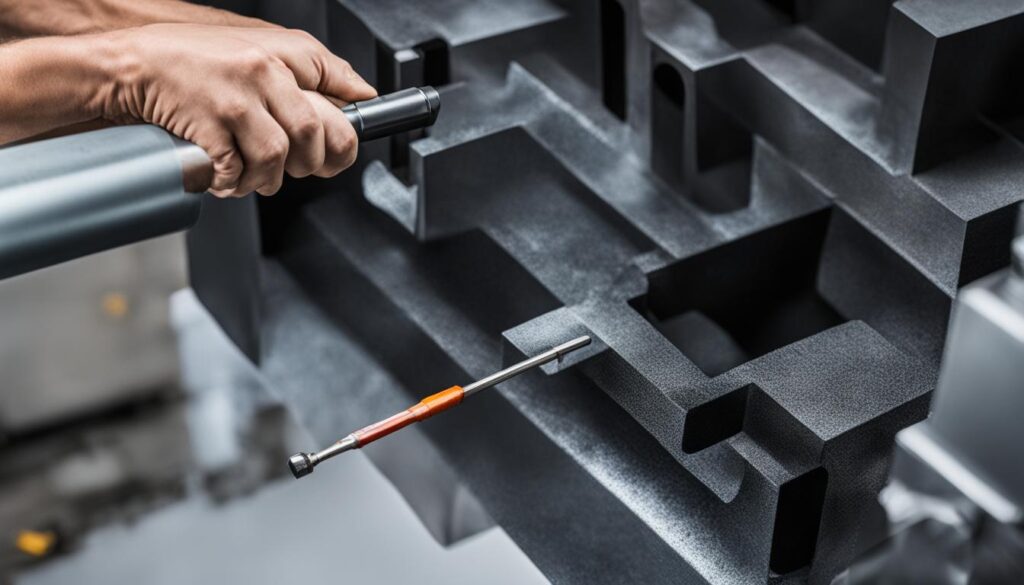
At KT-Foundry, we recognize the significance of NDT in guaranteeing high-performance carbon steel components. Our NDT applications examine both the presence and the compliance of flawed attributes against stringent specification requirements. These requirements are set forth by standards such as ASTM A703 and A781, ensuring our castings meet the highest possible quality measures.
Quality assurance in the casting industry involves a systematic process that is geared toward detecting and correcting any potential issues. This process includes the application of several NDT methods, ranging from visual inspections to more advanced ultrasonic and radiographic testing. By using these diverse techniques, we can successfully identify an array of defects and prevent any compromised components from being put into service.
“Quality assurance in casting plays a vital role in delivering top-tier, reliable products to our customers.”
NDT’s significance in ensuring the integrity of carbon steel casting components cannot be overstated, given the inherently fluctuating nature of the casting process. Emphasizing quality assurance through the entire lifecycle ensures that we consistently produce safe and reliable components that meet the demanding performance expectations of various industrial and infrastructural applications.
Visual Inspection: The First Line of NDT in Carbon Steel Castings
At KT-Foundry, we recognize the immense value of visual inspection as the most commonly employed Non-Destructive Testing (NDT) method and an essential first step in identifying surface defects in carbon steel castings. This cost-effective process enables a thorough assessment of the casting’s external and internal aspects using various tools such as magnifying glasses, mirrors, and boroscopes.
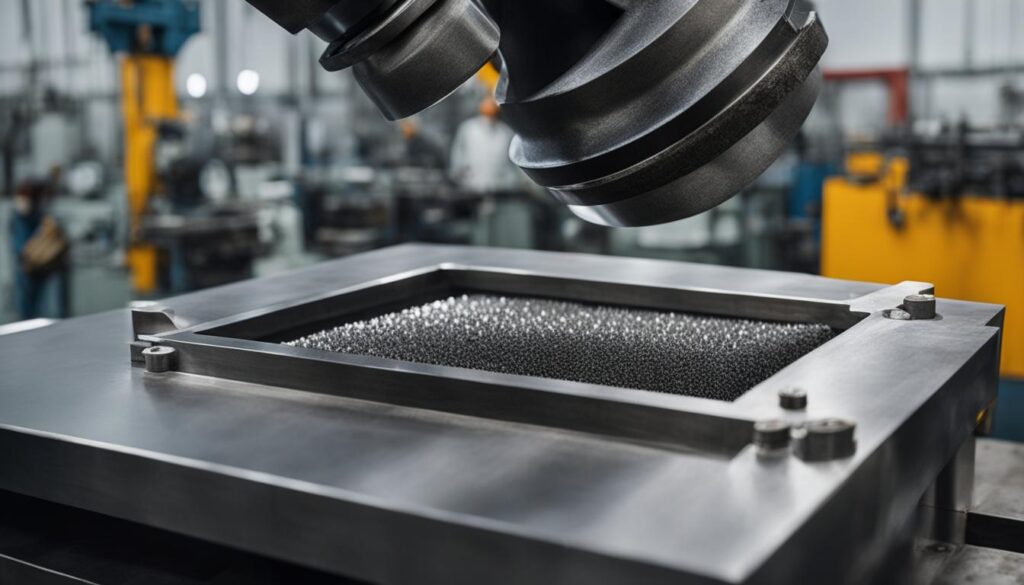
However, visual inspection has its limitations, as it is subject to subjective interpretation and is effective only for detecting discontinuities that are visually apparent. Ambiguity in casting specifications often leads to challenges in agreeing on what constitutes as an “injurious” defect, underlining the importance of clear standards for defect identification and remediation. Below, we outline the various Visual Inspection Applications and discuss their corresponding limitations in the Steel Casting Visual NDT process.
Applications and Limitations of Visual Inspection in Steel Casting
- Direct Inspection: Involves the naked eye or basic magnifying tools to examine the casting for visible defects. While expedient and affordable, the effectiveness can be compromised by human error or subjectivity.
- Boroscope Inspection: Employs a flexible tube with a camera to inspect the casting’s internal cavities, improving defect identification accuracy. However, its application is limited to non-complex internal structures and surface discontinuities.
- Computed Tomography (CT) Scan: Uses advanced imaging technology to create a 3D rendering of the casting, presenting detailed insight into the internal structures. Despite its high accuracy, it is more expensive and time-consuming compared to other visual inspection techniques.
Visual inspection stands as an invaluable component in the NDT process, serving as the first line of defense in detecting defects in carbon steel castings. However, given its limitations, it is crucial to supplement visual inspection with more advanced NDT techniques to ensure comprehensive defect identification and remediation.
In conclusion, balancing the Visual Inspection Limitations with the strengths of other NDT methods is the key to successful quality assurance in carbon steel casting production. By employing a diverse range of techniques and employing well-defined standards, we can effectively identify and treat defects in carbon steel castings, ensuring the highest level of product integrity for our valued clients.
Magnetic Particle Testing in Detecting Surface Flaws
At KT-Foundry, we employ Magnetic Particle Testing (MPT) as a sensitive technique for detecting both surface and near-surface discontinuities in our ferromagnetic carbon steel castings. This non-destructive testing method is an essential component of our quality assurance process, allowing us to uncover crucial flaws that might otherwise be missed by visual inspection alone.
MPT relies on the generation of a magnetic field and the application of ferrous particles that accumulate at points of irregularity, such as cracks and lack of fusion. This is achieved through a variety of methods, including:
- Yoke technique
- Prod technique
- Central conductor technique
These methods offer distinct advantages when it comes to detecting surface flaws in ferromagnetic material inspections, such as those found in our carbon steel castings. They enable us to quickly and accurately identify potential problem areas and rectify them before they escalate into more severe issues.
“Meticulous attention to detail is of utmost importance in our Magnetic Particle Testing process.”
However, it is important to recognize that MPT is not without its limitations. As the depth of the material being inspected increases, the sensitivity of this method tends to diminish, with a corresponding decrease in its ability to accurately detect flaws. Consequently, attention to detail is of utmost importance in our MPT procedures, as even minor oversights can potentially result in significant consequences.
Method | Benefits | Limitations |
---|---|---|
Yoke Technique | Portable and suitable for inspecting irregular shapes | Inability to detect flaws located too deep within the material |
Prod Technique | Effective for detecting surface and near-surface flaws | Can cause burns on the material surface if not applied properly |
Central Conductor Technique | Excellent for inspecting long, cylindrical components | Limited to components with centralized, conductive cores |
In summary, our Magnetic Particle Testing process plays a vital role in our efforts to ensure surface flaw detection and maintain the highest possible quality standards for our carbon steel castings. By combining MPT with other non-destructive testing methods, we aim to provide our clients with products that meet and exceed their expectations while ensuring both safety and performance.
Employing Ultrasonic Testing for Internal Defect Detection
At KT-Foundry, we utilize Ultrasonic Testing (UT) to uncover internal discontinuities in carbon steel castings, employing high-frequency sound waves that reflect off imperfections within the material. This advanced method serves as an indispensable tool for Internal Defect Ultrasonic Detection in steel castings and remains a crucial aspect of our overall quality control process.
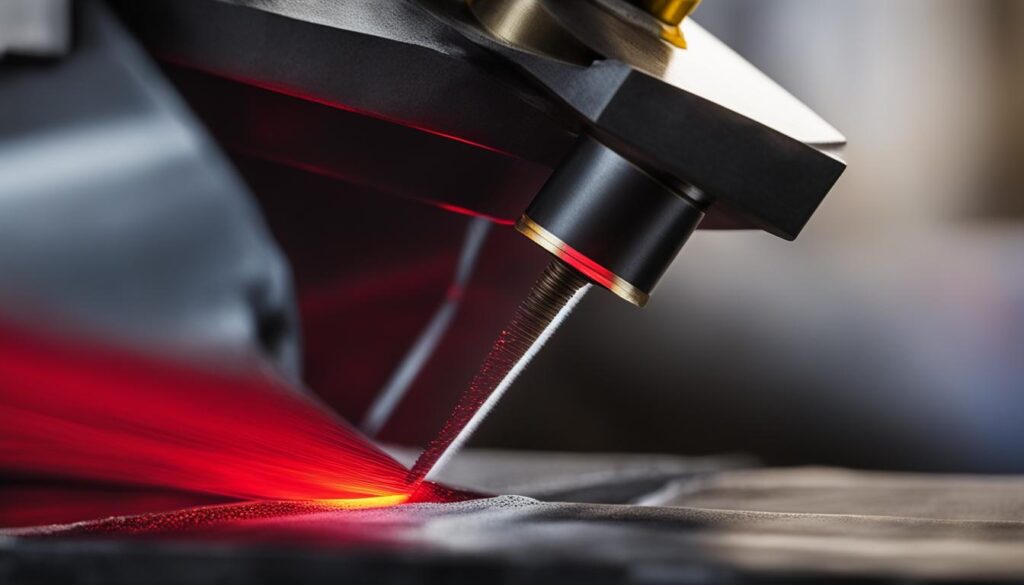
Techniques and Equipment Used in Ultrasonic Testing
The UT procedure involves multiple components, including a transducer emitting ultrasonic pulses transmitted into the material via couplants such as oil. Reflective waves are monitored to ascertain the presence and nature of internal flaws using sophisticated NDT Equipment, such as pulse-receivers and display monitors calibrated with standard blocks for accurate defect characterization.
There are several Ultrasonic Testing Techniques applied at KT-Foundry, including:
- Normal Beam Inspection for volumetric flaw detection
- Angle Beam Inspection for assessing welds and other complex geometries
- Phased Array Ultrasonics for increased precision in defect imaging
Additionally, our expert team employs specialized data analysis software to accurately record, analyze, and store Ultrasonic Testing data.
Interpreting Ultrasonic Testing Results for Steel Castings
The interpretation of ultrasonic testing results is a specialized skill at KT-Foundry, requiring expert analysis to precisely locate and size defects such as voids or cracks within steel castings. Crucial factors like sound wave reflection pattern, signal strength, and the time of flight are meticulously analyzed to gain insights into the nature of detected anomalies.
Effective Ultrasonic Testing Interpretation is key to fully understanding the true condition of each casting, ensuring both the safety and longevity of the final product.
Our highly sensitive evaluation process allows for Defect Analysis in Steel Castings and paves the way for informed decision-making regarding the usability and treatment of the inspected castings.
In conclusion, employing Ultrasonic Testing at KT-Foundry has proven invaluable for the consistent delivery of high-quality carbon steel castings. Our dedication to incorporating state-of-the-art NDT techniques, paired with our commitment to Interpreting UT Results with precision, ensures that our clients receive products of unparalleled integrity and reliability.
Advancing Quality Control with Radiographic Testing (X-Ray)
At KT-Foundry, we employ advanced Radiographic Testing techniques to visualize the internal structure of carbon steel castings and ensure the highest level of Quality Control in Steel Casting. By capturing differential absorption of X-ray or gamma-ray radiation on a recording medium such as film, we can detect both subsurface and surface discontinuities. This powerful method showcases variations in material thickness and integrity, providing a comprehensive analysis of the casting.
Radiographic Testing, including gamma radiography with Cobalt 60 and X-rays, offers numerous advantages, such as:
- Improved detection of subsurface and surface discontinuities;
- Greater precision in identifying material thickness variations;
- Enhanced assessment of internal structure integrity;
- Minimized disruptions in production processes;
- Reduced risk of casting failures due to unresolved defects.
Here at KT-Foundry, our commitment to incorporating X-Ray NDT methods has led us to push the boundaries of Radiographic Testing Advancements, resulting in better outcomes for our clients and the industries they serve.
Quality control of steel castings is vital in ensuring the safety and efficiency of the products and equipment in which they are used. Radiographic Testing is pivotal in achieving this level of confidence, ensuring our clients receive reliable and high-performing materials, every time.
Overall, our reliance on Radiographic Testing for carbon steel castings demonstrates a dedication to excellence, allowing us to deliver unparalleled quality and performance in every casting that passes through our facility.
Dye Penetrant Testing: Unveiling Surface Discontinuities in Castings
At KT-Foundry, we utilize the Dye Penetrant Testing (PT) method as an effective non-destructive testing (NDT) technique to detect surface-breaking defects in our carbon steel castings. This sensitive and straightforward process allows us to identify and rectify discontinuities, such as cracks and porosity, in both ferrous and non-ferrous materials. Such attention to detail ensures that our castings meet the highest industry standards when it comes to safety and reliability.
The Process of Dye Penetrant Testing
The Dye Penetrant Testing Process can be broken down into a series of methodical steps that allow for accurate detection of surface discontinuities in castings:
- Pre-cleaning of the casting surface to remove any contaminants or residue
- Application of penetrant dye to the clean surface
- Allowing the penetrant to dwell and penetrate any surface cracks or defects
- Removal of excess penetrant from the surface, without disturbing the penetrant within defects
- Application of developer to draw out the penetrant from inside the discontinuities, creating a visible indication of defects
- Inspection of the casting surface under proper lighting conditions to observe and document any indications of defects
- Post-cleaning of the casting surface to remove residual dye and developer
While considered one of the more basic NDT techniques, Dye Penetrant Testing has proven to be a valuable and cost-effective method for Surface Discontinuity Detection. It works exceptionally well for materials like carbon steel castings, enabling us to locate and correct defects that could compromise the quality, performance, and safety of our products.
“Dye Penetrant Testing provides a sensitive and simple approach for identifying surface defects in both ferrous and non-ferrous materials, ensuring casting quality and performance.”
By employing the Dye Penetrant Testing Process, KT-Foundry remains committed to maintaining the highest quality standards, upholding our reputation for producing reliable and durable carbon steel castings. Our meticulous attention to detail and dedication to excellence in NDT Dye Inspection set us apart from competitors, as we continue to deliver products that meet and exceed industry standards and customer expectations.
Impact of NDT on Casting Performance and Reliability
The adoption of Non-Destructive Testing (NDT) at KT-Foundry has proven to be transformative in ensuring the performance and reliability of carbon steel castings. By integrating a range of NDT techniques, from visual inspection to more complex ultrasonic and radiographic tests, the company assures that each casting meets the demanding and critical applications it’s designed for—be it infrastructure or industrial machinery.
The combination of NDT methods and the expertise of our trained personnel ensure that each casting adheres to customer specifications and fulfills its designed role effectively and safely. Below are some key benefits that NDT offers:
- Improved casting performance by detecting defects and irregularities before they become critical issues.
- Enhanced reliability in cast steel components, as each part is thoroughly inspected and analyzed to ensure it meets the required standards.
- Greater customer confidence and satisfaction, owing to a more consistent and superior-quality end product.
Furthermore, NDT helps in evaluating the casting performance across various sectors:
Industry Sector | NDT Application |
---|---|
Aerospace | NDT methods ensure the integrity and safety of critical components, such as turbine engine parts, landing gear, and airframe structures. |
Automotive | NDT is used to verify the integrity of engine blocks, transmission cases, suspension components, and other critical parts in automotive manufacturing. |
Construction | NDT plays a major role in ensuring the safe installation and performance of support beams, bridge components, and other crucial infrastructure elements. |
Energy | NDT is applied to detect defects that could affect the performance and reliability of power generation equipment, such as turbines, heat exchangers, and piping. |
In conclusion, the comprehensive application of NDT methods contributes significantly to the reliability in cast steel products. The ability to detect and rectify defects early in the manufacturing process allows for the production of high-quality components that meet the demanding requirements of various industries, providing customers with peace of mind when using KT-Foundry’s carbon steel castings.
Conclusion
At KT-Foundry, our commitment to excellence is reflected in the comprehensive Non-Destructive Testing (NDT) processes we employ to ensure reliable and high-quality carbon steel castings. We leverage a diverse array of NDT methods, which allows us to detect and resolve potential defects early on, ultimately delivering high-performance products that meet the stringent requirements of our clients.
Our experienced staff is proficient in the various NDT techniques, such as Visual inspection, Ultrasonic testing, Magnetic Particle Inspection, Radiographic Testing, and Dye Penetrant Testing. These methods enable us to examine the integrity of cast steel components thoroughly, ensuring that they adhere to the applicable industry standards and perform effectively and safely in their intended applications.
At KT-Foundry, we believe in continuous improvement. This philosophy drives us to advance NDT within the foundry industry and seek innovative approaches in both the manufacture and validation of our carbon steel castings. Our commitment to NDT excellence ensures that our clients can rely on the superior quality and performance of our products, now and into the future.
FAQ
What are the main Non-Destructive Testing methods used in carbon steel casting?
The main Non-Destructive Testing methods employed in carbon steel casting include Visual Inspection, Magnetic Particle Testing, Ultrasonic Testing, Radiographic Testing (X-Ray), and Dye Penetrant Testing. These methods help detect defects and maintain the structural integrity of the castings.
What is the significance of Non-Destructive Testing in cast steel production?
Non-Destructive Testing is crucial in cast steel production as it detects defects and discontinuities without causing harm to the material, allowing it to be used after inspection. It offers a comprehensive assessment of material adequacy and prevents potential failures in service, complying with industry standards such as ASTM A703 and A781.
How does Magnetic Particle Testing detect surface flaws in carbon steel castings?
Magnetic Particle Testing detects surface and near-surface discontinuities in ferromagnetic carbon steel castings by generating a magnetic field and applying ferrous particles that accumulate at the point of irregularity. This method reveals defects such as cracks and lack of fusion, although its sensitivity diminishes with increased material depth.
What is Ultrasonic Testing and how is it used for internal defect detection?
Ultrasonic Testing is an NDT method that uses high-frequency sound waves to uncover internal discontinuities in carbon steel castings. A transducer emits ultrasonic pulses that are transmitted into the material and reflective waves are monitored to ascertain the presence and nature of internal flaws. This method requires expert analysis and specialized equipment for accurate defect characterization.
How does Radiographic Testing (X-Ray) enhance quality control in carbon steel casting?
Radiographic Testing (X-Ray) allows visualization of the internal structure of carbon steel castings by capturing differential absorption of X-ray or gamma-ray radiation on a recording medium such as film. The method can detect both subsurface and surface discontinuities, showcasing variations in material thickness and integrity, and providing a comprehensive analysis to enhance quality control measures.
What is the process of Dye Penetrant Testing and how does it detect surface discontinuities in castings?
Dye Penetrant Testing is an NDT method used to detect surface-breaking defects on nonporous materials, such as carbon steel castings. The process involves applying penetrant to the material’s surface, allowing it to seep into voids or cracks, followed by the application of a developer to draw out the penetrant, creating visible indications of defects. This method is effective for identifying defects such as cracks and porosity.