Gray or Grey cast irons are made from pig iron. It is a remelted compound of iron and carbon content. There are also traces of some minerals, such as manganese, phosphorus, and silicon.
Gray iron castings are usually used in automotive engine blocks, cookware, electrical boxes, valve bodies, cylinder liners, machine parts, and many more.
Some of its properties include thermal conductivity, strength, and density. Among most cast irons, this type of iron castings is widely used and has been around in the industry of iron castings for many years already.
In addition to that, there are higher strength gray irons that still come at a low cost.
Sometimes, it is called gray iron, grey cast iron, grey iron, or gray cast iron. Though it is called by different names, all are cast irons, have a grey appearance, and have the same properties.
What is a Grey Cast Iron
Grey cast iron is a cast iron that has a graphitic microstructure. With silicon as an additional component, it stabilizes the carbon, which results in the presence of graphite flakes. Under the microscope, the graphite flakes can be easily identified.
Its mechanical properties may change depending on the size and shape of graphite flakes that can be found in its graphitic microstructure. However, the size of the matrix structure of the flake graphite is unable to control.
Properties of a Gray Iron
Cast irons are widely used because they can easily be molded, even in complex shapes. Its properties are also easy to change. It can be done by adjusting the materials that will be melted and their cooling rate. Even with different components, the melting process of the pig iron and the casting process remain the same.
Tensile Strength
Tensile strength refers to the ability of the gray iron castings to withstand a pulling force. Its tensile strength is measured with the amount to load the grey cast iron can handle before it breaks or stretches.
In general, gray cast irons have a relatively low tensile strength. Fortunately, the tensile strength of grey cast iron can be increased by adding copper or magnesium.
The minimum tensile strength of cast irons is classified according to a specific ASTM specification. In this case, it is classified under the international standard A-48.
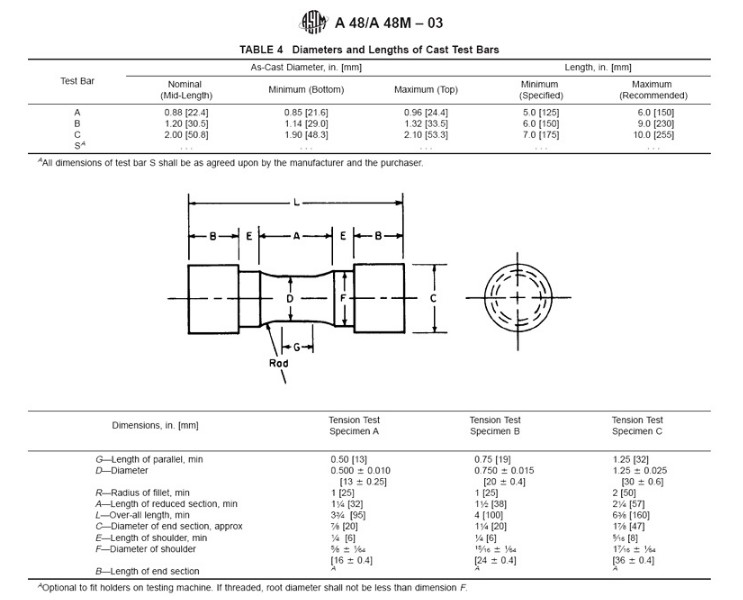
Like grey cast iron, other cast irons are classified by their minimum tensile strength in KSI.
Compressive Strength
This refers to the endurance of metals or iron alloys. Gray iron has a high compressive strength that can be compared to steel, making it a great choice for hydraulic parts and bases.
Though it has a relatively low tensile strength, gray iron has a high strength which is thrice its tensile strength. It is one of the strong points of a gray iron among other cast irons.
Hardness
Gray iron castings are generally hard and can increase their hardness from 20 to 60.
The hardness of gray iron is determined by the Brinell Hardness Test. The grey cast iron is tested by using a scale of penetration to a material sample.
Though grey iron is hard, it is a brittle material. It will not be able to bear such a huge and heavy load. Doing so may lead to countless new cracks.
Modulus of Elasticity
To easily understand, the modulus of elasticity refers to the measurement of the elasticity of the gray iron. A gray cast iron has a non-permanent resistance to deformation.
A gray cast iron that is under stress tends to deform. But since it has elasticity, once the stress is removed, the grey iron will return to its previous state.
Due to the presence of graphite, gray iron castings produce plastic deformation even under low stresses. Hence, the stress-strain curve is not linear.
The strength of gray cast iron is correlated with its elastic modulus. The elastic modulus increases as the gradient rises.
Good Wear Resistance
Another essential feature of grey iron is its wear resistance. In terms of abrasion, fretting, and some types of corrosive wear, they are comparable to medium carbon steels, but the graphite helps them withstand metal-to-metal wear.
When the mating material is hardened steel, this is, in fact, the case, as the graphite offers lubrication and a low-wear interface. As a result, they don’t seize when used in applications like screw thread and similar ones.
Physical Properties
The damping capability of the grey irons is influenced by the graphite content. It has the capacity to dampen elastic vibrations or deformations. In this situation, vibrations are considered to be absorbed by the graphite.
Due to its graphite structure, dimensional stability is also relatively unstable. The mechanisms causing this include the internal oxidation of the graphite flakes and the transformation of pearlite into ferrite, both of which cause growth.
Operating temperatures should be kept below 400°C to lessen these consequences.
Thermal Conductivity
Thermal conductivity is defined as the measurement of how much heat is transferred by a solid material through conduction. The thermal conductivity of most liquids and solids varies with temperature.
Since the gray iron structures resemble those of metal with simple carbon content, they share many characteristics, including thermal conductivity and thermal expansion. However, grey iron possesses a high thermal conductivity than iron with compacted flake graphite.
Grey cast iron is frequently used in vehicle engines, cylinder head, and other castings because of its strong heat fatigue resistance.
Electrical Properties
The graphite structure present in the grey iron castings has an effect on its electrical properties. All grey iron can resist electricity more than steel.
Gray iron castings that have coarse graphite components are more resistant to electricity than iron castings with finer graphite structures.
Resistance to Corrosion
Grey irons have better corrosion resistance than medium carbon steel in most circumstances. The matrix may disintegrate as corrosion develops, leaving graphite protruding from the surface of the gray iron.
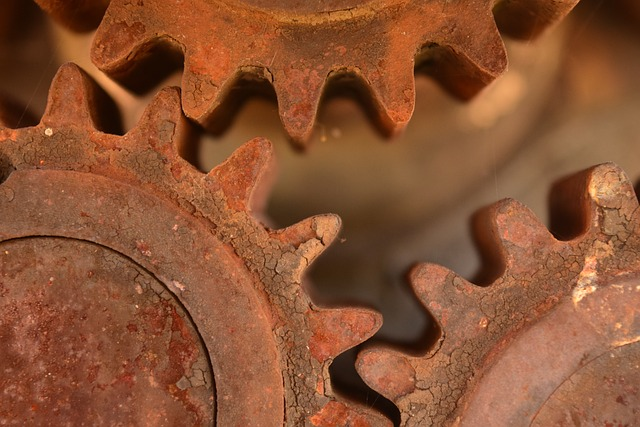
Welding Performance
Gray cast iron has poor weld repair capability. Weld repair castings are prone to cracking, and some of them have faults like hard patches, pores, excessive stresses, and many others. These are frequently fixed by specific materials like electrodes, heating before the welding process, and slow cooling.
Applications of Grey Cast Irons
Machine Parts
Grey cast iron has long been a preferred metal for engine blocks because of its low rates of metal-to-metal wear. Grey irons have been utilized for gears, cams, and machine ways with low wear rates; these components need to be tension alleviated before final machining.
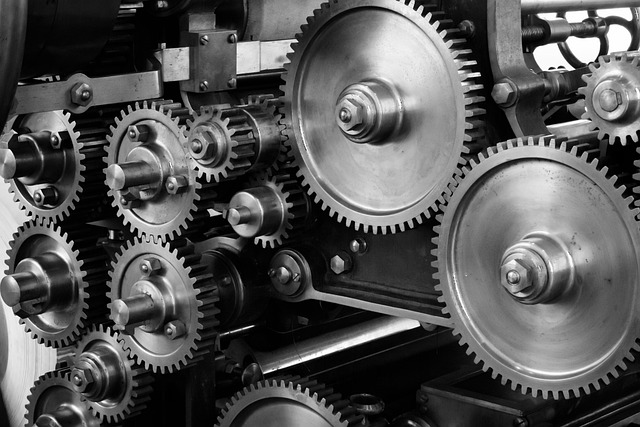
When the highest level of wear resistance is required, flame hardening should be employed.
Gray Iron Pipes
Grey iron is resistant to attacks by alkalis, salinity, and some acids. This cast iron has been used frequently for many years already in water and sewage pipelines.
The advantages of using gray iron in pipes are they have thicker walls and have a similar rate of corrosion as steel. However, it also has its drawbacks, such as internal corrosion during extreme conditions, no mechanical strength, and often manufacturing defects.
Other Cast Iron Type Constant
Ductile Cast Iron
Also known as spheroidal graphite cast iron, ductile cast iron is a form of metal that exhibits significant fatigue, impact, and corrosion resistance.
Compared to other types of iron, ductile cast iron, which typically has a carbon concentration of 0.08% to 0.60%, ductile cast iron has a substantially higher carbon content (3.0% to 3.9%). This distinction explains why ductile iron responds to corrosion in a different way.
A graphitic layer is present in ductile iron. Graphite builds up as a graphitic coating on the metal’s surface when corrosion starts. The following corrosion and galvanic behavior of ductile iron are influenced by the adhesion and porosity of this layer.
White Cast Iron
When carbon in the solution cannot solidify into graphite, white cast iron is created. White cast irons are difficult to manufacture because they are brittle and hard. They stand out because they are the only cast iron family member to include carbon as an iron carbide only.
The lower carbon equivalents give white cast iron a light appearance. It maintains good hardness and strength at higher temperatures and has a strong compressive strength.
White cast iron retains its hardness for just a brief time, even up to a red heat, and great wear resistance. To increase toughness, castings are occasionally created with a white structure in certain places and a grey or flaky structure in others.
Due to their lack of impact resistance and the challenge of preserving the structure in thicker portions, these cast irons have a limited range of applications.
Malleable Cast Iron
When a white cast iron goes into a heat-treatment process, it becomes malleable. Its graphite content separates off gradually. This process gives the surface tension ample time for the graphite to get round up rather than become flake graphite. The malleable cast iron is quite similar to mild steel.
In addition to this, malleable cast iron is resistant to corrosion and features excellent toughness.