The traditional metal casting techniques can be time-consuming, expensive, and limited in design flexibility–from creating metal casting molds to pouring molten metal and controlling how it cools.
The advent of 3D-printed metal castings technology has transformed this process offering a range of benefits over traditional methods.
However, it is limited to small batches of metal castings. For mass production, it is still recommended to use traditional foundry methods.
Advantages of 3D Printing in Metal Casting Process
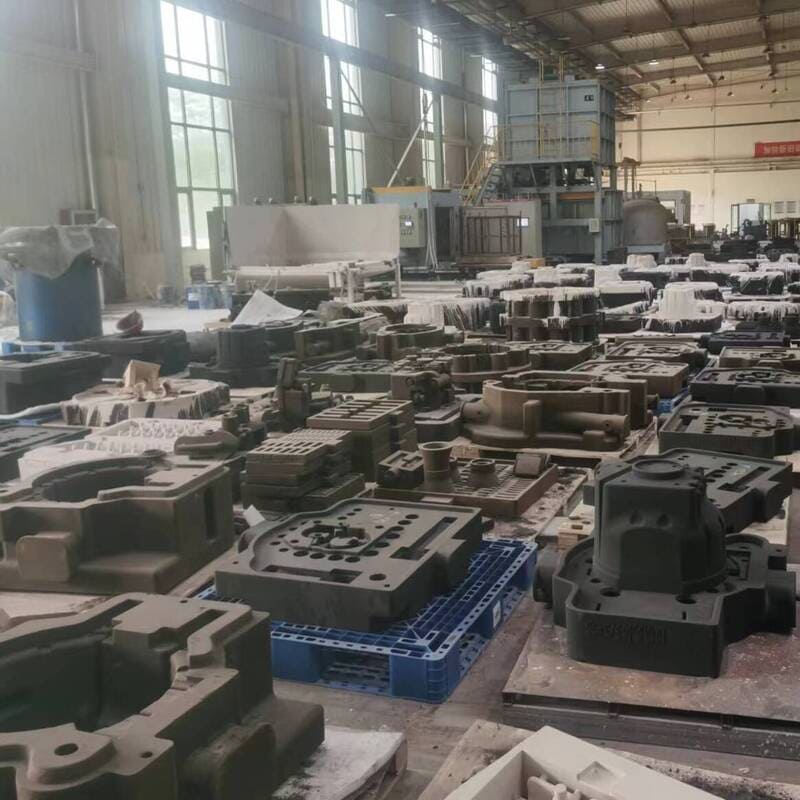
Reduced Lead Times
With 3D printing, metal parts can be produced quickly and easily, often in a matter of hours, depending on the complexity of the design. This means that manufacturers can produce parts on-demand and in low-volume, reducing the need for large inventories and decreasing customer lead times.
Its ability to change design quickly can provide businesses with a competitive advantage in the market due to the increased speed of production.
Design Freedom
Metal 3D printing technology provides a high degree of design freedom and flexibility that is impossible with a traditional metal casting method. 3D printing allows designers to create complex geometries and intricate designs of final cast parts.
Cost Savings
It eliminates the need for high material costs for traditional manufacturing methods such as die casting or investment casting.
Metal 3D printing reduces the labor-intensive process of traditional casting. This can lead to part consolidation, where multiple cast parts can be combined into a single component, reducing assembly time and costs.
However, if you aim for mass production, traditional metal casting processes are more cost-efficient.
Improved Accuracy and Precision
The 3D printing process allows for producing parts with tolerances as low as a few microns.
It also enables the production of parts with controlled microstructure and grain orientation. This is important for parts that require specific material properties, such as high strength or fatigue resistance.
Traditional casting processes determine the material’s microstructure by the cooling process, which can be difficult to control. With metal 3D printing, the microstructure can be controlled by adjusting the printing parameters, allowing for precise control of material properties.
Better Quality Control
3D printing enables real-time production process monitoring, allowing for better quality control. During the printing process, sensors can be used to monitor parameters such as temperature, humidity, and powder flow, which can affect the quality of the final part.
By monitoring these parameters in real time, adjustments can be made to ensure that the part is produced with the desired quality of the metal casting.
In addition, the metal parts are built up layer by layer, allowing for consistent material properties throughout the part.
Materials Used for 3D Printing Material
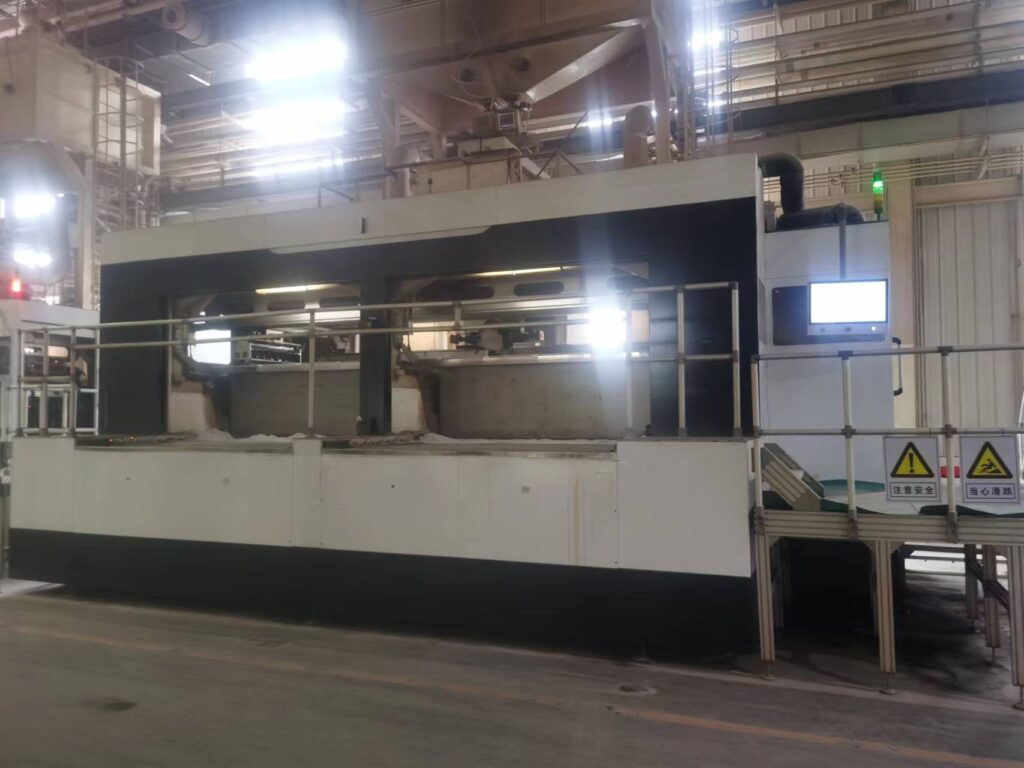
Types of Metals
Stainless steel is a popular material for metal 3D printing due to its strength, corrosion resistance, and low cost.
Titanium is a strong material commonly used in aerospace and medical applications. It is biocompatible and has excellent corrosion resistance.
Aluminum is a popular material in the automotive and aerospace sectors due to its low cost and light weight. It’s lightweight and strong, and it’s easy to machine.
Cobalt-chrome is a biocompatible material commonly used in medical and dental applications. It has good wear resistance and can be polished to a high shine.
Copper is useful in electrical and thermal applications. It is also used in jewelry-making and decorative applications.
Metal Powders
These are exclusively finely ground metals used exclusively for 3D printing process. They are produced using various methods, including gas atomization, plasma atomization, and mechanical milling.
The choice for metal powders depends on the application’s specific requirements, including strength, durability, corrosion resistance, and cost.
In many cases, the properties of the final 3D-printed part depend on the composition of the metal powder used. For example, a part’s strength, ductility, and corrosion resistance can be adjusted by varying the alloy composition.
Alloy Composition and Customization
Customization can be achieved by blending different metal powders to create a desired alloy composition. For example, a blend of stainless steel and copper powders can create a highly-strength material and good electrical conductivity.
Consumers can expect greater flexibility in alloy composition and customization.
Techniques for 3D Printed Metal Casting
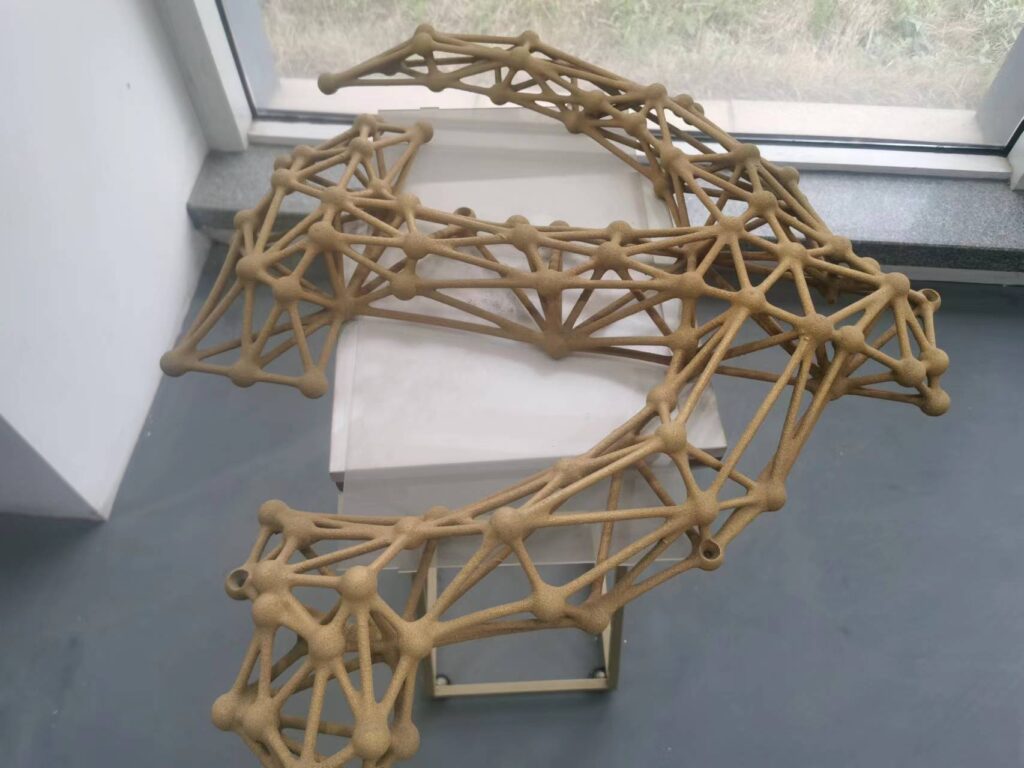
Direct Metal Laser Sintering
Direct Metal Sintering (DMS) is a type of metal 3D printing technique that uses a high-powered laser to fuse metal powder into a solid object. It is also known as selective laser sintering (SLS) or laser powder bed fusion (LPBF).
A thin layer of metal powder is spread evenly over a build platform in DMS. A high-powered laser is then used to selectively melt the metal powder in specific areas, according to a 3D digital model. As the laser moves over the metal powder, it fuses the particles, layer by layer, to create a solid metal object.
However, there are also some limitations to DMS. One of the main limitations is that it can be expensive compared to other metal 3D printing techniques due to the high cost of the laser and other equipment required.
In addition, DMS may not be suitable for parts that require extremely high levels of accuracy or surface finish, as the melted metal powder can sometimes result in rough surfaces or other imperfections.
Binder Jetting Technology
This technique is also known as powder bed and inkjet 3D printing.
The binder jetting technique involves spreading a thin layer of metal powder evenly over a build platform. Then, a print head deposits a liquid binding agent onto the powder material in specific areas according to a 3D digital model.
The binding agent acts as an adhesive, holding the metal powder particles together in the desired shape.
Investment Casting or Lost Wax Casting
Investment casting process requires an expandable wax pattern. It can be made with 3D printing or CNC machining. The investment casting patterns are coated with multiple layers of a ceramic slurry, which can dry between each layer to create hard ceramic shells around the wax.
Sand Casting Process
The sand casting process uses CAD software to create a 3D model of the desired part. 3D printing finishes the physical master pattern for the sand molds and sand cores.
Once the sand mold is complete, liquid metal is poured into the mold through a small opening. The metal fills the cavity left by the 3D-printed pattern in the sand and is allowed to cool and solidify. Once the metal has cooled, the sand mold is broken to reveal the finished metal part.
The sand casting mold is reinforced with a mixture of clay and water, which helps glue sand, hold its shape, and prevent the sand from breaking apart during the casting process.
Future of 3D Printing for Metal Casting
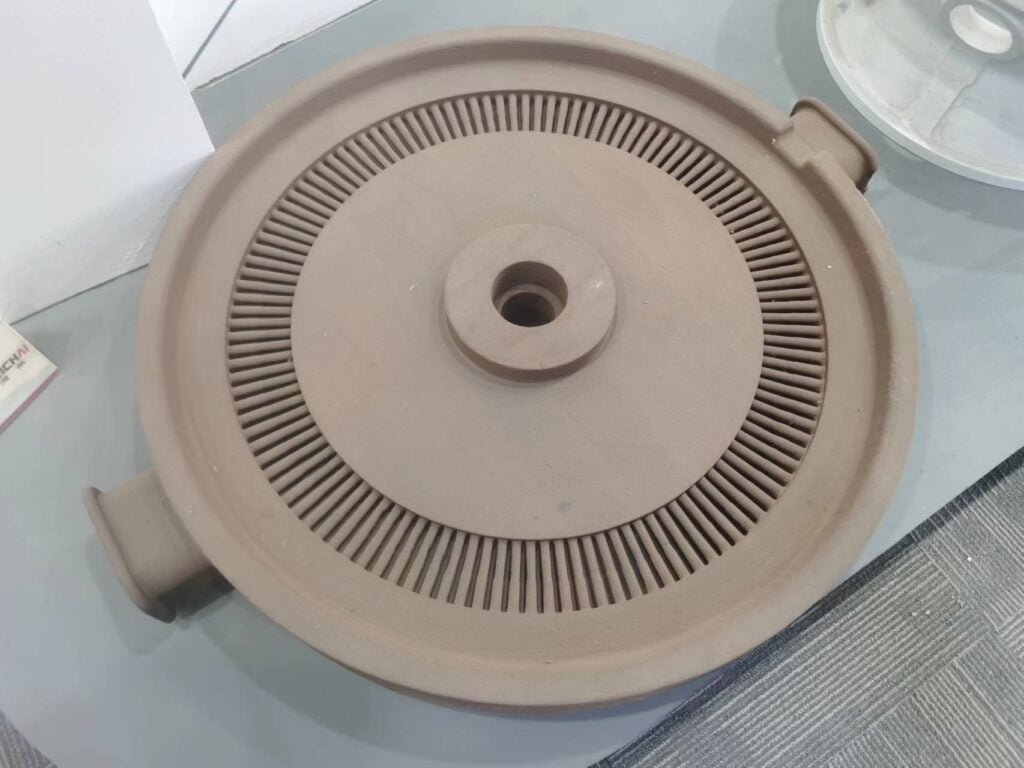
Potential for New Applications
In the future, metal 3D printing could be used to create entire structures, such as airplane wings or rocket engines.
It can also revolutionize the automotive industry by enabling the production of lighter, stronger, and more efficient parts. It could also be used to create custom parts and reduce the time and cost of rapid prototyping.
As technology advances and becomes more accessible, we can expect to see even more innovative applications of metal 3D printing in the future.
Integration With New Technologies
Metal 3D printing can be integrated with AI to improve the design and optimization of parts. AI algorithms can analyze data from simulations and experiments to identify a part’s most efficient design.
It can also create custom parts for robots with complex geometries and materials, improving their functionality and performance.
As metal 3D printing continues evolving and integrating with new technologies, we expect even more innovative applications and solutions to emerge.
Comparison to Die Casting Process
Creating patterns in die casting involves incorporating the same precision and accuracy as the part. Metal components are manufactured in a cold or hot chamber die-casting machine.
3D printing can produce parts quickly for producing small quantities, while die casting typically requires more time to produce tooling and set up the production process.