Stainless steel casting plays a vital role in the aerospace industry, providing unparalleled durability and precision for critical components. With its exceptional strength and versatility, stainless steel casting is the go-to choice for manufacturing a wide range of aerospace applications.
Stainless steel casting in the aerospace industry is primarily achieved using different alloys, with the two most common being 304 and 316 stainless steel. While 316 stainless steel is preferred for its higher temperature resistance and superior corrosion resistance, 304 stainless steel offers greater strength and hardness, making it suitable for applications that require high strength.
Various casting methods, including investment casting, sand casting, centrifugal casting, and die casting, can be employed to produce aerospace components using stainless steel casting. Additionally, the use of laser machines enables the engraving of trademarks or patterns on products made from stainless steel casting.
Key Takeaways:
- Stainless steel casting provides unmatched durability and precision for critical aerospace components.
- 304 and 316 stainless steel alloys are commonly used in aerospace applications, each with its own advantages.
- Different casting methods, such as investment casting and sand casting, can be utilized for stainless steel casting in aerospace.
- Laser engraving allows for the customization of aerospace products made from stainless steel casting.
- The choice between 304 and 316 stainless steel casting depends on specific application requirements.
The Versatility of Stainless Steel Casting in Aerospace
Stainless steel casting offers a wide range of alloys and the investment casting process, making it highly versatile for various aerospace applications. With its exceptional strength, durability, and corrosion resistance, stainless steel casting has become an indispensable component in the aerospace industry. It is used in the manufacturing of critical components such as turbine blades, engine mounts, and structural parts.
One of the key advantages of stainless steel casting is the ability to utilize different alloys to meet specific requirements. The most commonly used alloys in aerospace applications are 304 and 316 stainless steel. While 316 stainless steel offers superior corrosion resistance and temperature resistance, 304 stainless steel is known for its high strength and hardness. The choice between these alloys depends on the specific needs and preferences of the application.
The investment casting process is widely employed in aerospace stainless steel casting due to its precision and dimensional accuracy. This process allows for the production of complex and intricate parts with fine details, ensuring the highest quality and performance. The investment casting process involves creating a wax pattern, coating it with a ceramic shell, and then melting the wax to leave a cavity. Molten stainless steel is then poured into the cavity, creating the final product with excellent surface finish and dimensional accuracy.
In addition to its versatility in alloy selection and casting process, stainless steel casting also allows for further customization. Products made of stainless steel can be engraved with trademarks or patterns using laser machines, adding aesthetic value and personalization to aerospace components. This level of customization is crucial in the aerospace industry, where precision and attention to detail are paramount.
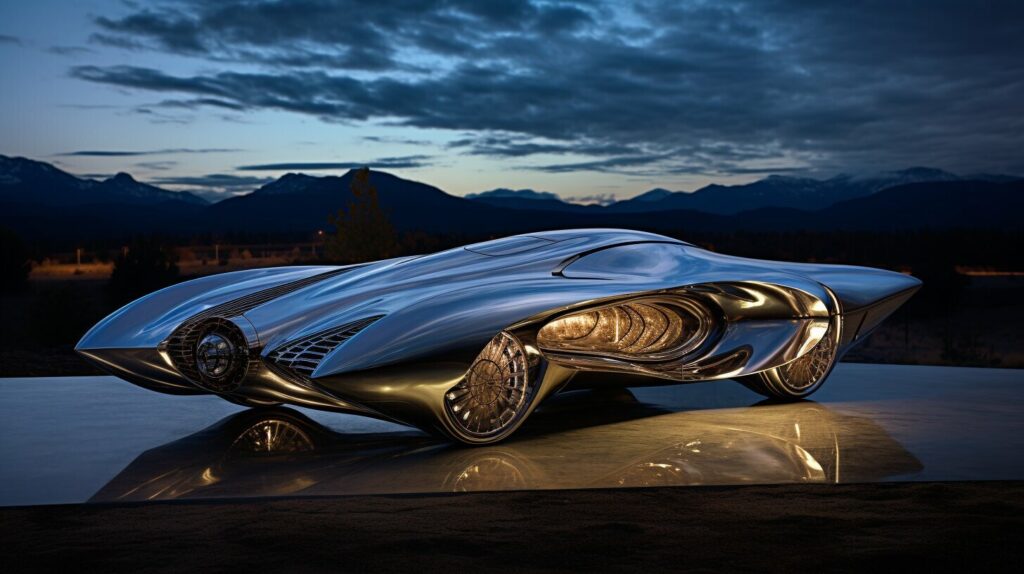
Properties | 304 Stainless Steel | 316 Stainless Steel |
---|---|---|
Corrosion Resistance | Good | Excellent |
Temperature Resistance | Up to 870°C (1600°F) | Up to 925°C (1700°F) |
Strength | High | Lower than 304 |
Hardness | High | Lower than 304 |
Corrosion Resistance and Surface Finish in Aerospace Stainless Steel Casting
When it comes to aerospace applications, corrosion resistance and surface finish are crucial factors to consider in stainless steel casting. The harsh environments and demanding conditions that aerospace components are exposed to require materials that can withstand corrosion and maintain optimal performance over time.
Choosing the right supplier for stainless steel casting in aerospace is essential to ensure the highest level of corrosion resistance. Welded areas are particularly vulnerable to corrosion, and a reliable supplier will use techniques to minimize the formation of corrosion-prone areas during the casting process. Additionally, the selection of the appropriate stainless steel alloy is important to ensure optimal corrosion resistance. The composition of the alloy, including elements such as chromium and nickel, plays a critical role in its ability to resist corrosion.
Alongside corrosion resistance, surface finish is another important consideration in aerospace stainless steel casting. The surface finish affects not only the aesthetics of the component but also its performance. A smooth and uniform surface finish is essential for minimizing turbulence and maximizing airflow in aerospace applications. This, in turn, contributes to improved fuel efficiency and overall performance of the aircraft.
Furthermore, surface finish influences the component’s resistance to corrosion. A high-quality surface finish can help create a protective barrier against environmental elements, preventing the formation and growth of corrosion. It is important to choose a supplier with expertise in achieving the desired surface finish for aerospace components, as the process requires precision and meticulous attention to detail.
Corrosion Resistance and Surface Finish: The Key to Long-Lasting Aerospace Components
In conclusion, corrosion resistance and surface finish are vital considerations in the aerospace industry when it comes to stainless steel casting. By selecting the appropriate stainless steel alloy, working with a reputable supplier, and achieving the desired surface finish, manufacturers can ensure the longevity and performance of aerospace components. With the right combination of corrosion resistance and optimal surface finish, stainless steel casting continues to be a preferred choice for critical applications in the aerospace industry.
The Strength and Mechanical Properties of Stainless Steel Casting in Aerospace
Stainless steel casting in aerospace applications offers exceptional tensile strength, high-temperature resistance, and the necessary mechanical properties for aviation requirements. This makes it a preferred choice for producing critical components that can withstand the demanding conditions of the aerospace industry.
One of the most commonly used alloys in stainless steel casting is 304 stainless steel. It possesses remarkable strength and hardness, making it suitable for areas that require high strength. 304 stainless steel contains iron, chromium, nickel, and a small amount of carbon. This composition gives it excellent durability and the ability to withstand significant mechanical stress.
For applications where higher temperature resistance and superior corrosion resistance are needed, 316 stainless steel is the preferred choice in the aerospace industry. With higher levels of chromium, nickel, and the addition of molybdenum, 316 stainless steel exhibits excellent resistance to corrosion and oxidation at elevated temperatures. These properties make it ideal for critical aerospace components that are exposed to extreme conditions.
Alloy | Tensile Strength (MPa) | Melting Point (°C) | Corrosion Resistance |
---|---|---|---|
304 Stainless Steel | ≥515 | ≥1400 | Good |
316 Stainless Steel | ≥515 | ≥1375 | Excellent |
The choice between 304 and 316 stainless steel casting depends on the specific needs and preferences of the aerospace application. It’s essential to consider factors such as temperature, corrosion resistance, and mechanical stress when selecting the appropriate alloy. With the right choice, stainless steel casting can provide the strength and mechanical properties necessary to meet the rigorous demands of aviation.
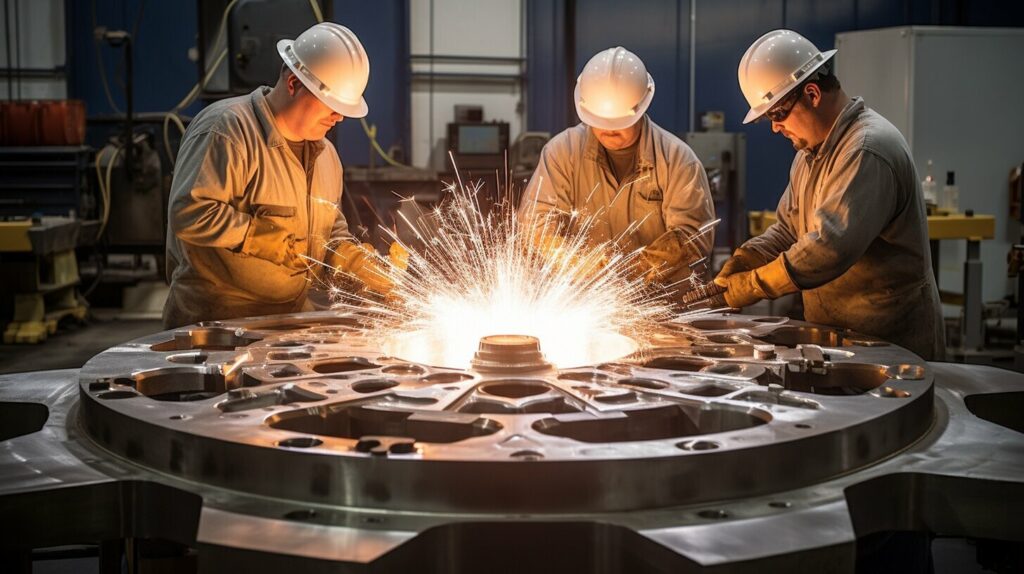
Overall, stainless steel casting offers a reliable solution for aerospace applications. Its exceptional tensile strength, high-temperature resistance, and mechanical properties make it an invaluable material for producing critical components in the aviation industry.
Precision and Dimensional Accuracy in Stainless Steel Casting for Aerospace
The precision investment casting process is essential for producing stainless steel castings with greater dimensional accuracy, making it ideal for critical aerospace components. Whether it’s turbine blades, engine mounts, or landing gear components, precision and dimensional accuracy are of utmost importance in the aerospace industry.
Investment casting, also known as the lost-wax casting process, allows for intricate designs and complex geometries to be faithfully reproduced in stainless steel. This highly versatile casting method involves creating a wax pattern of the desired component, coating it with a ceramic shell, and then melting away the wax to leave behind the shell. Molten stainless steel is then poured into the shell, filling the void left by the wax pattern. The result is a near-net shape component with exceptional dimensional accuracy and a smooth surface finish.
By utilizing the precision investment casting process, aerospace manufacturers can achieve tight tolerances and intricate details that other casting methods may struggle to replicate. This ensures that critical components fit together seamlessly and perform reliably under extreme conditions. Whether it’s maintaining the integrity of structural components or optimizing the aerodynamic performance of airfoils, the precision and dimensional accuracy of stainless steel castings are paramount in achieving the highest level of performance and safety in aerospace applications.
Advantages of Precision Investment Casting
The precision investment casting process offers numerous advantages over other casting methods when it comes to producing stainless steel castings for aerospace applications. Firstly, it allows for the production of complex geometries and intricate details that would be difficult or impossible to achieve through other casting processes. This makes it an ideal choice for aerospace components that require precise shaping and intricate internal structures.
Additionally, precision investment casting provides excellent surface finishes, reducing the need for additional machining or finishing operations. This not only saves time and costs but also ensures that the final components meet the stringent quality requirements of the aerospace industry. The smooth surface finish of precision investment castings also minimizes the risk of stress concentration points, enhancing the overall durability and fatigue resistance of the components.
Furthermore, the precision investment casting process allows for the use of various stainless steel alloys, including the widely used 304 and 316 stainless steels. The versatility of stainless steel casting, combined with the precision of the investment casting process, makes it an ideal choice for a wide range of aerospace components, from engine components to structural elements.
Advantages of Precision Investment Casting |
---|
Ability to produce complex geometries and intricate details |
Excellent surface finishes, reducing the need for additional machining |
Wide range of stainless steel alloys can be used |
In conclusion, the precision investment casting process plays a crucial role in the aerospace industry by enabling the production of stainless steel castings with unparalleled dimensional accuracy. This process offers numerous advantages, including the ability to create complex geometries, excellent surface finishes, and the use of various stainless steel alloys. By harnessing the power of precision investment casting, aerospace manufacturers can ensure the reliable performance and longevity of critical components, further advancing the safety and efficiency of aviation.
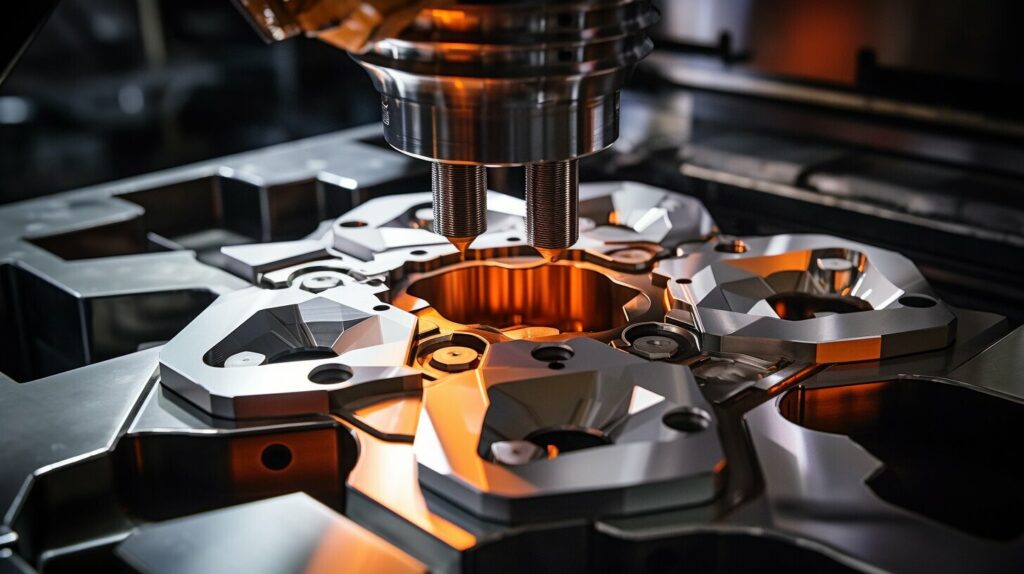
Stainless steel casting has revolutionized aerospace applications, providing unparalleled strength, durability, and precision, driving the rising demand across a wide range of industries. The versatility of stainless steel casting in the aerospace industry cannot be overstated. With its ability to withstand extreme temperatures, resist corrosion, and maintain structural integrity, stainless steel casting has become the go-to choice for critical components in aircraft and spacecraft.
When it comes to aerospace applications, the choice between 304 and 316 stainless steel casting depends on the specific needs and preferences of the application. While 316 stainless steel offers superior temperature and corrosion resistance, 304 stainless steel excels in strength and hardness. Different casting methods, such as investment casting, sand casting, centrifugal casting, and die casting, can be utilized to achieve the desired shape and properties.
Furthermore, stainless steel casting allows for intricate engravings, trademarks, and patterns to be etched onto the products using advanced laser machines. This not only adds a distinctive aesthetic appeal but also enhances the identification and branding of aerospace components.
As the demand for durable and precise aerospace components continues to grow, stainless steel casting remains at the forefront of innovation. Its exceptional mechanical properties, resistance to corrosion, and ability to achieve dimensional accuracy make it indispensable in the aerospace industry. Whether it’s for aircraft engines, landing gear, or even spacecraft propulsion systems, stainless steel casting proves to be a reliable and versatile manufacturing process that meets the stringent requirements of aerospace applications.
FAQ
Q: What is the second most commonly used alloy in stainless steel casting for aerospace?
A: The second most commonly used alloy in stainless steel casting for aerospace is 304 stainless steel, which has properties and applications similar to 316 stainless steel.
Q: What are the main components of 304 stainless steel?
A: 304 stainless steel contains iron, chromium, nickel, and a small amount of carbon.
Q: Why is 316 stainless steel preferred in aerospace applications?
A: 316 stainless steel is preferred in aerospace applications due to its higher temperature resistance and superior corrosion resistance.
Q: Can 304 stainless steel be used in high-strength applications?
A: Yes, 304 stainless steel is stronger and harder, making it suitable for places that require high strength.
Q: What casting methods can be used for 304 stainless steel?
A: Various casting methods can be used for 304 stainless steel, including investment casting, sand casting, centrifugal casting, and die casting.
Q: Can products made of 304 stainless steel be engraved?
A: Yes, products made of 304 stainless steel can be engraved with trademarks or patterns using a laser machine.
Q: How do you choose between 304 and 316 stainless steel for casting?
A: The choice between 304 and 316 stainless steel casting depends on the specific needs and preferences of the application.