The die-casting process is a manufacturing process that involves using a metal mold or die to create complex, high-precision metal parts. The process involves injecting molten metal, typically aluminum alloy or zinc, under high pressure into the die cavity, where it solidifies and shapes the mold.
Die-cast aluminum parts are widely used in various industries for their lightweight, strength, and durability. However, to improve their performance and wear resistance, subjecting them to a surface treatment process is essential.
Anodizing, powder coating, and electroplating are some of the most common surface finishing options for aluminum die castings, each with unique benefits. By subjecting cast aluminum alloys to surface treatment, industries can ensure that their products are more durable, functional, and has a smooth surface.
This article will discuss the importance of surface treatment in die-cast aluminum parts, the different surface treatment options available, and their benefits.
Understanding Anodizing for Metal Surface
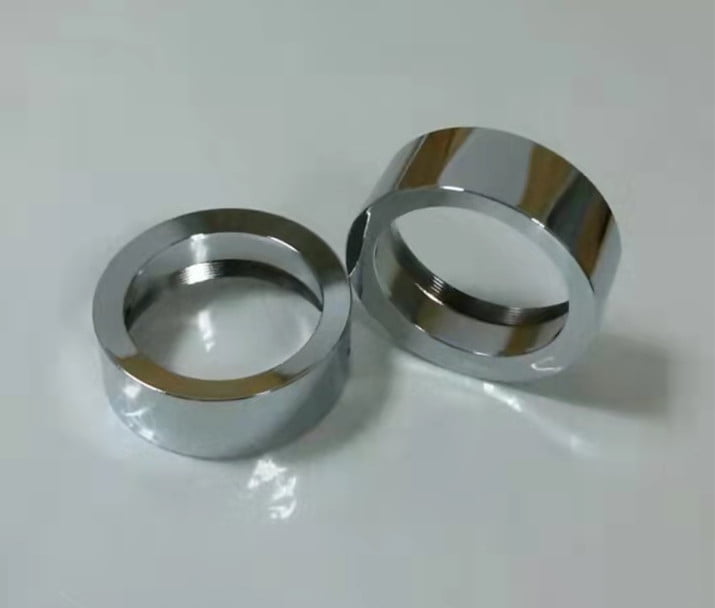
Anodizing is an electrochemical reaction process that involves creating a thin layer of oxide on the surface of an aluminum die-cast part. The process involves placing the part in an electrolytic solution and passing static electricity through it. This causes the die-casting parts to oxidize and create a hard and abrasion-resistant surface.
It is a widely used surface treatment process that protects the surface of aluminum castings. The process provides several benefits, including improved corrosion resistance, durability, and aesthetic properties.
The die-cast parts are cleaned to remove any dirt, grease, or other contaminants that may be present on the surface. Otherwise, it may have a pure chemical reaction affecting the surface quality. The metal part is then treated to prepare it for anodizing. This typically involves etching the surface with an acidic solution to create a porous surface layer to help the oxide layer form.
The metal part is placed in an electrolytic solution, which acts as the anode in an electrical circuit. An electric current is passed through the solution, causing the metal to oxidize and create a layer of oxide on the surface. The type of anodizing solution used, and the process’s duration will determine the oxide layer’s thickness and properties.
An anodized aluminum alloy typically has a sky-blue shade. If desired, the aluminum die-casting surface can be dyed to produce a range of colors for a decorative finish. It involves immersing the part in a dye solution and allowing the dye to be absorbed by the porous oxide layer.
Types of Anodizing
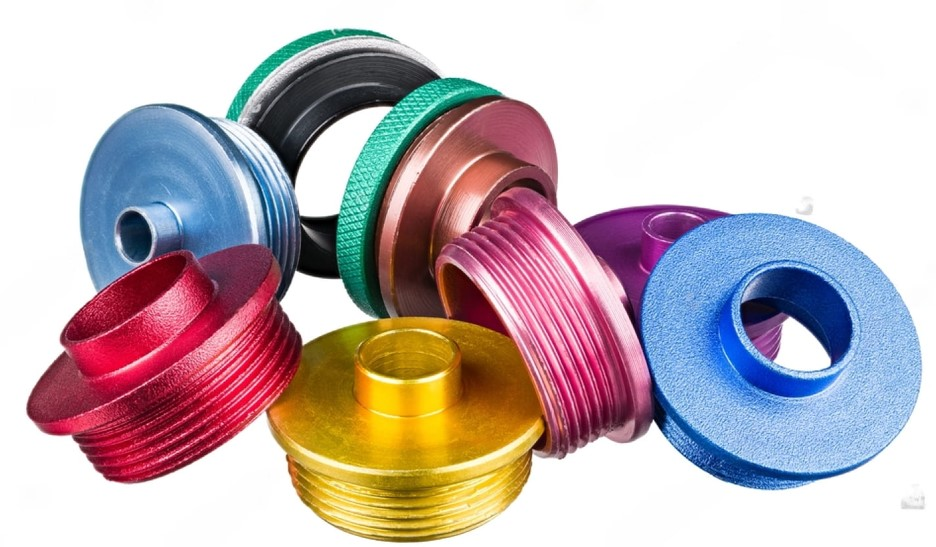
Chromic Acid
Chromic acid anodizing, also known as Type I anodizing, is a surface treatment process that involves creating a thin layer of oxide on the surface of a metal part, typically aluminum. The process uses a chromic acid solution to create the oxide layer, which is typically thinner than the oxide layers produced by other anodizing processes.
Chromic acid anodizing is primarily used for cosmetic purposes, as it can produce a clear or yellowish coating that enhances the appearance of the part.
However, chromic acid anodizing has some limitations. The process can be more difficult to control and produce toxic fumes and waste, making it less environmentally friendly than other anodizing processes.
Sulphuric Acid
Sulfuric acid anodizing, also known as Type II anodizing, is a surface treatment process that involves creating a layer of oxide on the surface of a metal part, typically aluminum. The process uses a sulfuric acid solution to create the oxide layer, which is typically thicker and more durable than the oxide layers produced by chromic acid anodizing.
The thickness of the oxide layer can be controlled by adjusting the concentration of the acid solution, the solution’s temperature, and the process’s duration. Sulfuric acid anodizing is a widely used and well-established process that is relatively low-cost and environmentally friendly.
Hard Coating Process
Hard coat anodizing, also known as Type III anodizing or hard anodizing, is a specialized form of sulfuric acid anodizing that produces a thicker and more wear-resistant oxide layer on the surface of a metal part, typically aluminum.
The hardness of the coating can be further increased by using special additives or post-treating the part with a sealing process. Due to its exceptional hardness, hard coat anodizing is often used as a substitute for other surface treatments, such as hard chrome plating, which can be environmentally hazardous.
Tartaric Sulphuric Acid
Tartaric sulfuric acid anodizing, also known as TSA anodizing or electrolytic coloring, is a type of anodizing process involving a mixture of sulfuric acid and tartaric acid to create a thicker, more uniform and highly corrosion-resistant oxide layer on the surface of aluminum parts.
This process also enables the metal surface to be colored in a broader range of colors than other anodizing processes. Tartaric sulfuric acid anodizing is mainly used in aerospace and industrial products where high strength and corrosion resistance are required, and aesthetic appeal is also important.
The process is more complex and requires more control than traditional anodizing processes. The result is a high-quality surface resistance with excellent corrosion resistance and color consistency.
Benefits of Anodizing
Increased Corrosion Resistance
Anodizing creates a layer of aluminum oxide on the surface of a metal part, which provides a barrier that prevents further oxidation or corrosion of the metal. The oxidation process produces a layer of aluminum oxide tightly bound to the metal surface, forming a hard, durable, and corrosion-resistant coating.
The thickness of the oxide layer can be controlled by adjusting the anodizing process parameters such as voltage, time, and temperature. Thicker oxide layers provide better corrosion resistance, offering a more effective barrier to protect the metal from corrosion.
Additionally, some anodizing processes, such as sulfuric acid anodizing, can be sealed after anodizing, which further improves the corrosion resistance of the coating.
Durability
The oxidation process produces a layer of aluminum oxide tightly bound to the metal surface, forming a hard, durable, and wear-resistant coating. Some anodizing processes, such as hard coat anodizing, produce an even thicker and harder oxide layer, which provides exceptional durability and wear resistance.
Aesthetic Appeal
Some anodizing processes, such as tartaric sulfuric acid anodizing or electrolytic coloring, offer a more comprehensive range of color options, from vibrant shades to subtle pastels. Using dyes during the anodizing process can further enhance the aesthetic appeal of the metal part.
Anodizing also provides a consistent surface finish, with a uniform oxide coating layer covering the whole part’s surface. This results in a visually pleasing appearance that can add to the overall appeal of the finished product.
Common Mistakes to Avoid in Anodizing
Failure to remove all oils, dirt, and other contaminants from the surface can result in a weak or uneven oxide scale. Proper cleaning and preparation of the metal surface before anodizing is critical to ensure that the oxide layer forms correctly.
Failure to follow the correct parameters can result in a weak or inconsistent oxide layer. The anodizing process parameters, such as voltage, temperature, and time, must be carefully controlled to achieve the desired oxide layer thickness and quality.
Failure to follow the correct parameters can result in a weak or inconsistent oxide layer. Quality control measures, such as inspection, testing, and documentation, are critical to ensure that the finished product meets the desired specifications.
Powder Coating for Aluminum Die Cast
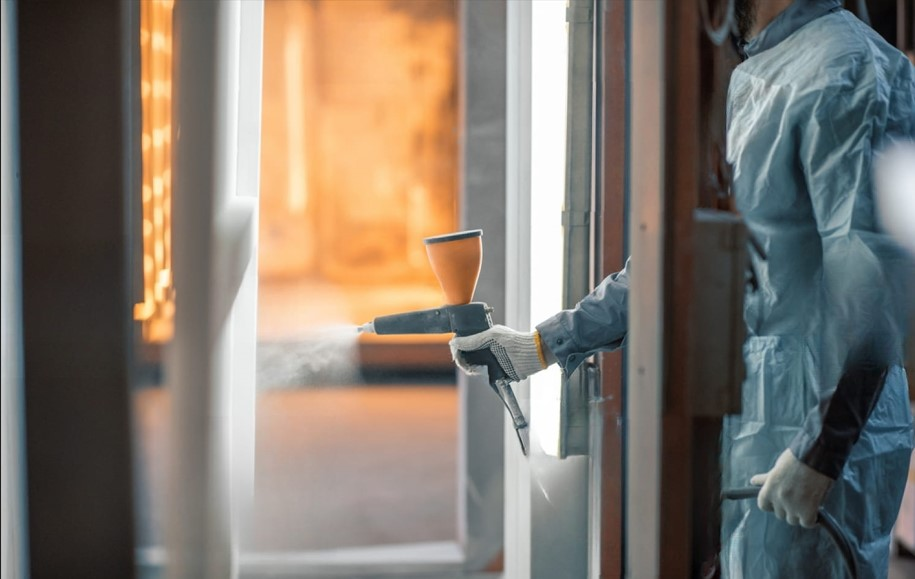
Powder coating is a surface treatment method commonly used for aluminum die castings. It involves applying a dry powder, which is typically made of polyester, epoxy, or a blend of both, onto the surface of the part using a spray gun. The powder is then cured in an oven, melts, and forms a durable and uniform coating.
It offers several advantages over surface treatment methods, such as anodizing or painting. It provides a thicker and more even coating, which can better protect the part from corrosion, abrasion, and UV damage.
Powder coating also offers various colors and finishes, allowing manufacturers to create parts with specific aesthetic or functional requirements.
Additionally, powder coating is environmentally friendly as it produces less waste and releases fewer pollutants than other coating methods. The powder used in the process is recyclable, reducing the waste generated.
Types of Powder Coating
Thermoset
Thermoset powder coating is a type of powder coating used for aluminum die castings. Thermoset powder coatings are made from cross-linked polymers that are cured through a chemical reaction during curing.
A dry powder is applied to the surface of the aluminum die casting using an electrostatic spray gun. The part is then heated in a curing oven, where the powder melts and flows to form a continuous film. During this process, the polymers in the coating cross-link to form a strong and durable surface.
Thermoplastic
Thermoplastic powders are made of polymer resins that soften when heated and harden when cooled, without a chemical reaction, like thermoset powders. Unlike thermoset powder coatings, the polymer resins in the coating do not cross-link during the curing process.
It is an effective and versatile surface finishing option for aluminum die cast, offering excellent mechanical properties and customization options. However, it may not be as durable as thermoset powder coatings in extreme environments and may not offer the same level of impact resistance.
Epoxy Powder Coating
Epoxy powder coating is a thermosetting powder coating used for aluminum die casting. Epoxy powder coatings are made from a blend of epoxy resin and hardeners, which undergo a chemical reaction during curing to form a highly durable and impact-resistant coating.
Polyester
Polyester powder coatings are made from a blend of polyester resin and hardeners, which undergo a chemical reaction during curing to form a durable and aesthetically pleasing coating. It offers several advantages over other coating methods, including excellent resistance to UV light, weathering, and corrosion.
Advantages of Powder Coating
Efficiency
Powder coating brings efficiency for several reasons. It is a faster and more efficient process than traditional wet painting methods. The dry powder is applied using an electrostatic spray gun, which charges the particles and causes them to adhere evenly to the surface of the aluminum die-casting. This eliminates the need for time-consuming preparation steps like masking and sanding.
It is a more environmentally friendly process than traditional wet painting methods. It does not require solvents or VOCs (volatile organic compounds), which can harm workers and the environment.
Cost-Effective
Powder coating provides a more durable and long-lasting finish than traditional wet painting methods. The thermosetting powders used in powder coating cure at high temperatures, resulting in a hard, durable, and impact-resistant coating that is less prone to chipping, scratching, and fading. This reduces the need for frequent touch-ups or recoating, which can save on material and labor costs over time.
Coverage
The dry powder has a high transfer efficiency, which means that a high percentage of the powder is deposited onto the part’s surface, reducing the amount of overspray and waste.
Powder coating can be customized to meet specific design and functional requirements, which can help to optimize coverage and protection. This includes applying multiple layers, creating textured or matte finishes, and adding features like UV resistance, chemical resistance, and electrical conductivity.
Common Mistakes to Avoid in Powder Coating
Uneven application of the powder coating can lead to variations in the film thickness, resulting in an uneven finish or reduced durability. Proper equipment and application techniques can help ensure consistent coverage.
Powder coating requires a specific temperature and time to cure properly. Failure to follow the manufacturer’s guidelines for curing can result in an insufficiently cured coating, which can lead to adhesion problems or reduced durability.
Grounding is essential to ensure proper adhesion of the powder coating. If the part is not grounded correctly, the powder coating may not adhere properly, resulting in an uneven finish or adhesion problems.
Electroplating Process for Aluminum Casting
Electroplating can be used for aluminum castings. However, aluminum is a non-ferrous metal and requires a different process than ferrous metals like iron and steel. It involves using a different electrolyte solution and anodes designed explicitly for aluminum.
One of the challenges with electroplating aluminum is that it is a very reactive metal and can quickly form a natural oxide layer that can prevent the adhesion of the plating material. To overcome this, the aluminum surface must be pre-treated with a chemical etch or other surface preparation techniques to remove the oxide layer and improve adhesion.