As the leading manufacturer in the aluminum die cast industry, KT-Foundry is proud to offer superior grade manufacturing solutions that leverage the lightweight advantage of aluminum die cast components. Automotive die casting, specifically with aluminum, has revolutionized the manufacturing process for a variety of automotive components. Through the use of die casting, precise shapes and dimensions can be achieved by injecting molten metal into a mold cavity under high pressure. This technique offers numerous advantages, including precision and accuracy, swift production, strength and durability, design flexibility, material efficiency, and superior surface finish.
Key Takeaways:
- Aluminum die casting allows for the production of complex and intricate components with precision and accuracy.
- Swift production is achieved through the high-speed, high-pressure injection of molten metal into molds.
- Aluminum die cast components are known for their strength, durability, and suitability for demanding applications.
- The design flexibility of aluminum die casting enables the creation of complex geometries and innovative solutions.
- The material efficiency of aluminum die casting reduces waste and optimizes resource utilization.
Experience the Precision of Aluminum Die Casting
Through our state-of-the-art aluminum casting process, we achieve unparalleled precision in manufacturing die cast components, ensuring high-quality, exacting dimensions, and intricate designs. Die casting aluminum offers remarkable accuracy, allowing us to create complex and intricate automotive components with ease. The molten metal is injected into carefully designed molds under high pressure, resulting in precise shapes and dimensions that meet the strictest industry standards. With our expertise in precision die casting, we can produce components with tight tolerances and intricate details that are essential for the optimal performance of automotive systems.
Our advanced die casting technology enables us to achieve consistent results, ensuring that each component meets the required specifications. By utilizing computer-aided design (CAD) software and advanced manufacturing techniques, we can optimize the design and production process to minimize errors and maximize efficiency. This attention to detail guarantees the exacting dimensions and intricate designs that are crucial for the success of automotive applications.
In addition to precision, die casting offers a rapid production cycle, allowing for efficient high-volume manufacturing. Once the molds are created, the injection process is fast, ensuring swift production turnaround times. This makes die casting aluminum an ideal choice for automotive manufacturers who require large quantities of components without compromising on quality or precision.
Advantages of Aluminum Die Casting: |
---|
1. Precision and Accuracy: Achieve exacting dimensions and intricate designs. |
2. Swift Production: Rapid production cycle for high-volume manufacturing. |
3. Strength and Durability: Create components that withstand demanding automotive applications. |
4. Design Flexibility: Enable the production of complex geometries and innovative solutions. |
5. Material Efficiency: Reduce waste and optimize resource utilization. |
6. Superior Surface Finish: Eliminate the need for additional finishing processes. |
With our expertise in aluminum die casting, we are committed to delivering components that exceed expectations in terms of precision, quality, and design. As the automotive industry continues to pursue innovation, efficiency, and sustainability, our die cast solutions play a vital role in driving these advancements. By harnessing the lightweight advantage of aluminum and harnessing the capabilities of precision die casting, we empower automotive manufacturers to enhance fuel efficiency, improve performance, and meet the evolving demands of the industry.
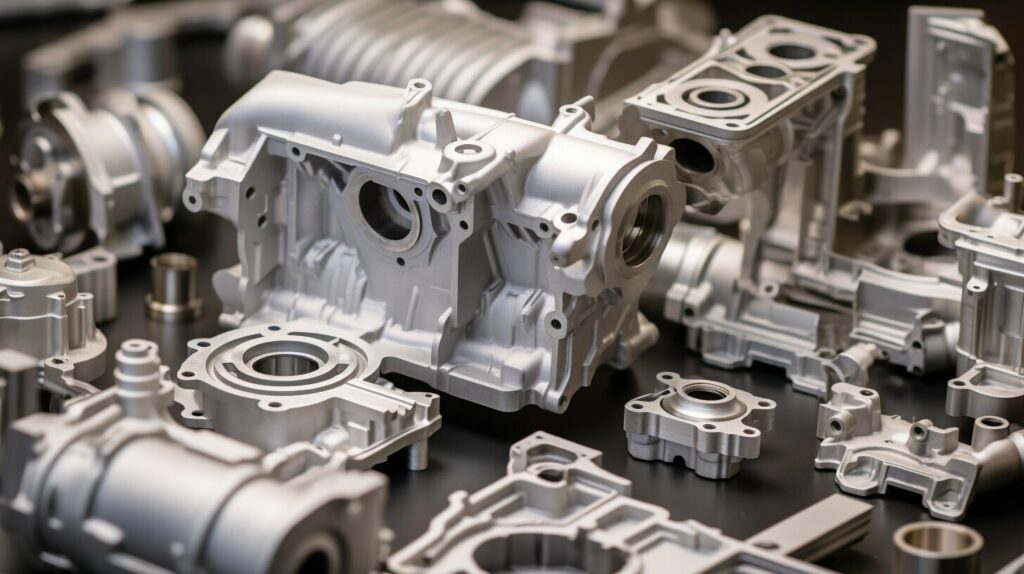
“Through our precision die casting process, we provide automotive manufacturers with high-quality components that meet the strictest standards of precision and performance. Our commitment to excellence ensures that every die cast component we produce is a testament to the capabilities of aluminum die casting.”
Swift Production with Aluminum Die Casting
KT-Foundry, as a leading aluminum die casting manufacturer, is known for our ability to provide swift production solutions that meet the highest quality standards in the industry. With our state-of-the-art facilities and expertise in aluminum die casting, we can efficiently produce a wide range of components for various applications, including automotive, aerospace, electronics, and more.
One of the key advantages of aluminum die casting is its ability to deliver swift production. The process involves injecting molten aluminum into a mold cavity under high pressure, resulting in precise and intricate shapes. This not only ensures excellent dimensional accuracy but also reduces the need for extensive post-processing.
By leveraging our advanced die casting techniques and rigorous quality control measures, we are able to streamline the production process, reducing lead times and improving overall efficiency. Our experienced team closely monitors every stage of production to ensure that each component meets the specified requirements and exceeds customer expectations.
At KT-Foundry, we take pride in our commitment to delivering high-quality die casting services. Our skilled engineers and technicians work diligently to optimize the manufacturing process, minimizing waste and maximizing material efficiency. With our expertise in die casting and extensive knowledge of different alloys, we can recommend the most suitable material for each application, ensuring optimal performance and longevity of the components.
Advantages of Swift Production with Aluminum Die Casting |
---|
High precision and dimensional accuracy |
Reduced post-processing requirements |
Shorter lead times |
Improved production efficiency |
Optimized material utilization |
Cost-effective manufacturing |
With our swift production capabilities and dedication to excellence, KT-Foundry is your trusted partner for all your aluminum die casting needs. Contact us today to learn more about our services and how we can help bring your designs to life.
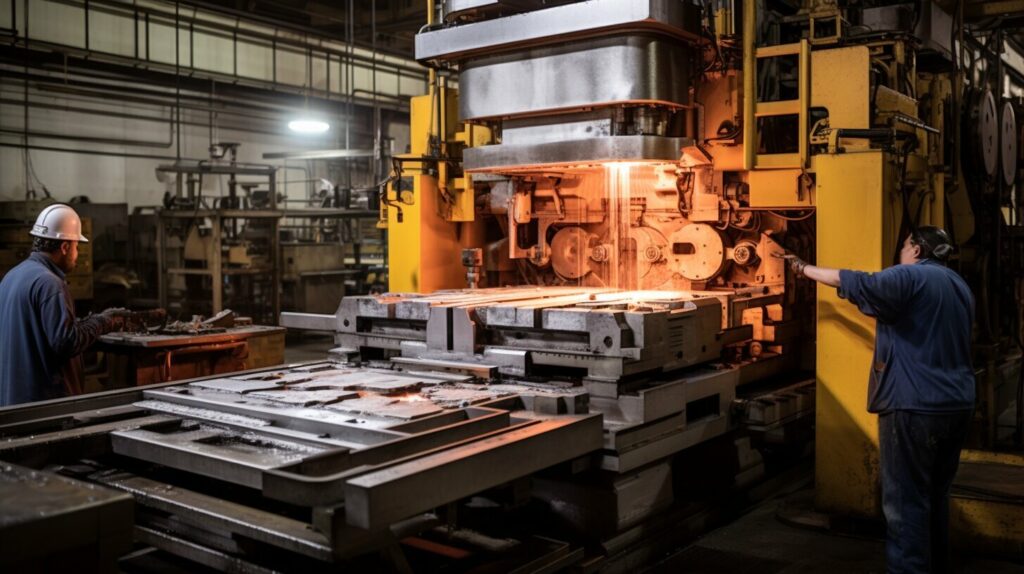
Our aluminum die cast components are crafted from premium materials, ensuring exceptional strength and durability, making them ideal for critical applications in industries such as automotive, aerospace, and electronics. The die casting process allows for the production of complex and intricate shapes that maintain their structural integrity under demanding conditions.
Using high-quality aluminum die casting materials, our components offer superior strength, withstanding heavy loads and extreme temperatures. The die cast parts are engineered to meet stringent performance requirements, providing reliable performance and long-lasting durability.
“Our aluminum die cast components are engineered to meet the highest standards of quality and performance, making them the preferred choice for demanding applications.”
With the use of die cast alloy, our aluminum die casting products exhibit excellent mechanical properties, including high tensile strength and impact resistance. This makes them well-suited for critical applications that require reliable and robust components.
Furthermore, the die casting process ensures tight tolerances and dimensional accuracy, reducing the need for post-processing and enabling seamless integration with other parts. This level of precision contributes to the overall performance and reliability of the end product.
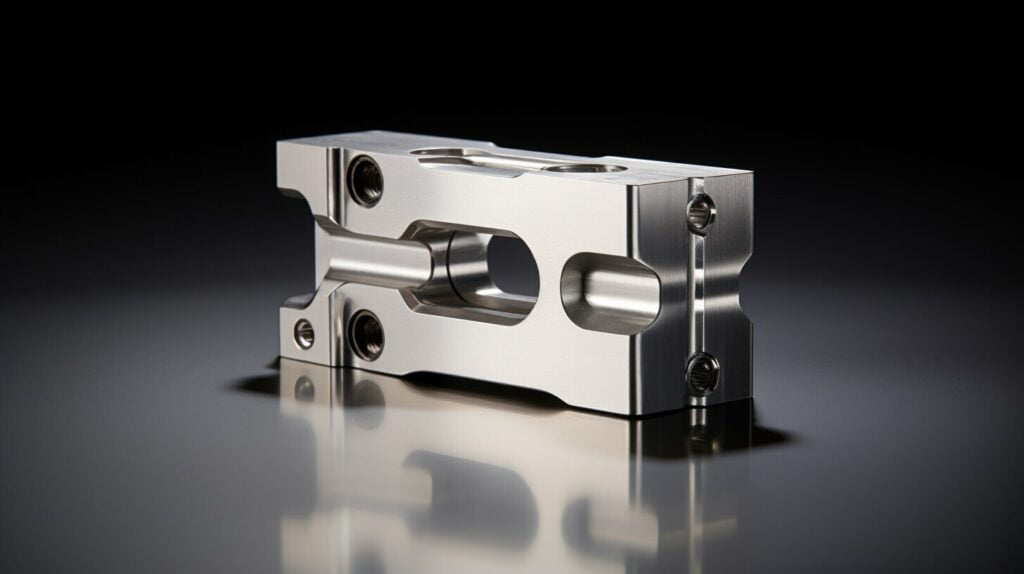
Advantages of Aluminum Die Cast Components |
---|
Exceptional strength and durability |
Precision and dimensional accuracy |
Wide range of applications |
- Automotive industry: engine parts, transmission parts, steering and suspension components, body and exterior parts, electrical and electronic parts.
- Aerospace industry: structural components, engine parts, landing gear components.
- Electronics industry: enclosures, heat sinks, connectors.
Design Flexibility for Innovative Solutions
The aluminum die casting industry is renowned for its superior design flexibility, allowing engineers to create complex geometries and innovative solutions that meet the diverse demands of modern industries. With this manufacturing process, intricate and detailed components can be produced with exceptional precision and accuracy. The injection of molten aluminum into a specialized mold cavity under high pressure ensures that even the most intricate designs are faithfully replicated, resulting in components that fit seamlessly into complex assemblies.
This design flexibility extends to various industries, including automotive, aerospace, electronics, and more. Engineers can push the boundaries of conventional design, explore unique geometries, and optimize functionality. The ability to incorporate complex features, such as ribs, bosses, thin walls, and undercuts, allows for lightweight yet robust designs that meet stringent performance requirements.
Table 1: Examples of Design Flexibility in Aluminum Die Casting
Industry | Component | Design Features |
---|---|---|
Automotive | Engine Block | Complex cooling passages for efficient heat dissipation |
Aerospace | Structural Bracket | Lightweight design with intricate internal reinforcements |
Electronics | Heat Sink | Optimized fins and thermal management features |
The design freedom offered by aluminum die casting enables the optimization of component performance while reducing weight and material usage. This not only enhances the overall efficiency but also contributes to sustainability goals by minimizing waste and maximizing resource utilization. Designers can achieve high-quality results with minimal post-processing, eliminating the need for additional operations that can add time and cost to the manufacturing process.
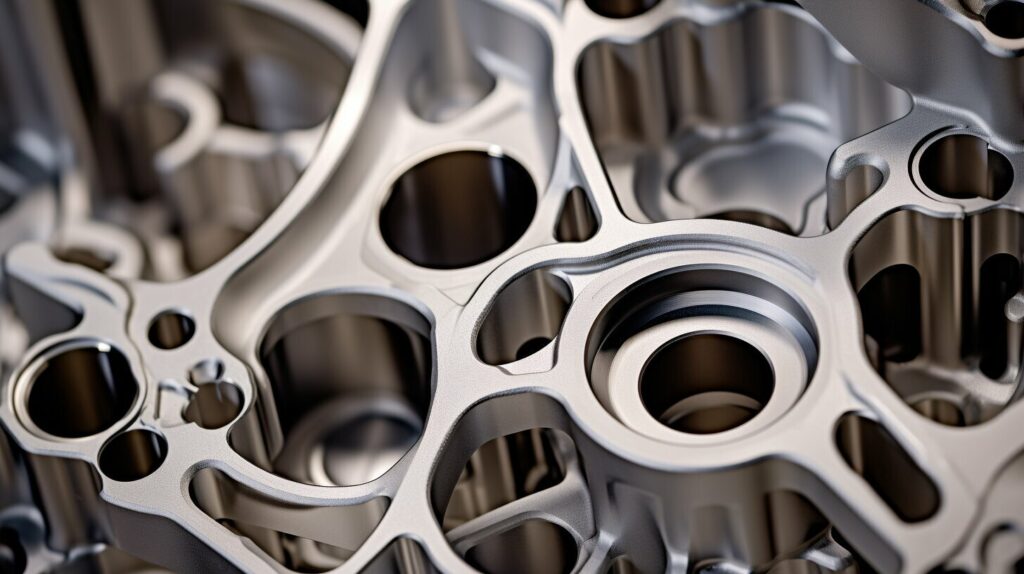
In summary, the design flexibility provided by the aluminum die casting process empowers engineers to create intricate and innovative solutions for a wide range of industries. With precision and accuracy, complex geometries can be realized, ensuring that components meet the demanding requirements of modern applications. This combination of flexibility, quality, and efficiency makes aluminum die casting a preferred choice in the manufacturing world, driving advancements in various sectors and contributing to the ongoing pursuit of innovation and sustainability.
Material Efficiency in Aluminum Die Casting
With our advanced aluminum casting process, we prioritize material efficiency, minimizing waste and optimizing resource utilization, resulting in cost-effective solutions for our customers. Aluminum die casting offers significant advantages in terms of material efficiency, making it a preferred choice for various industries.
Through our precise die casting techniques, we are able to create complex geometries and intricate designs using minimal material. The molten aluminum is injected into a mold cavity under high pressure, filling every detail with precision. This ensures that the final components are produced with minimal material consumption while maintaining their structural integrity and functionality.
In addition, the reusability of aluminum makes it a sustainable option. Any excess material or scrap generated during the die casting process can be recycled and reused, further reducing waste and minimizing environmental impact. Our commitment to material efficiency extends throughout our production process, from the careful selection of raw materials to the optimization of casting parameters, to ensure that every resource is utilized effectively.
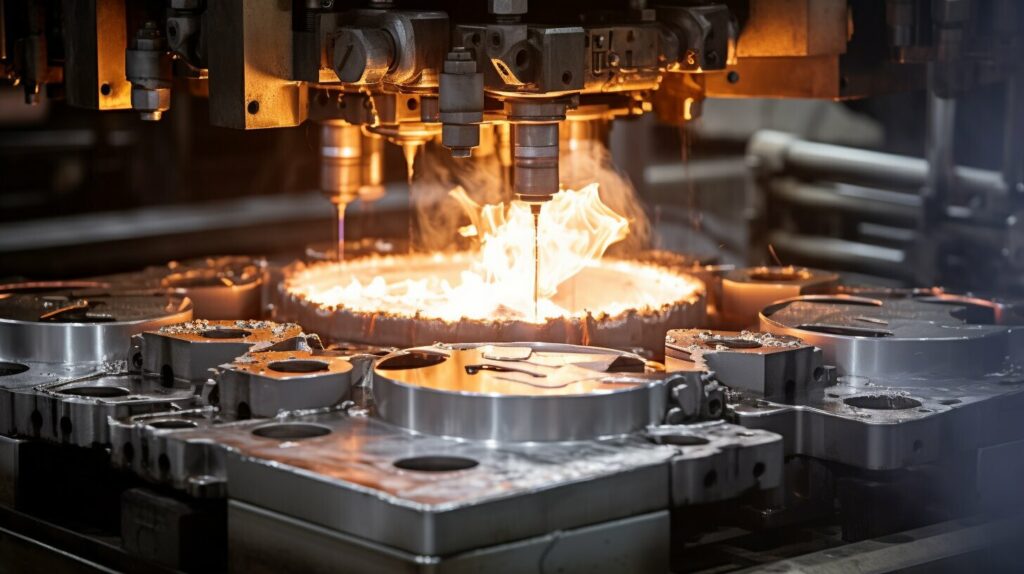
By prioritizing material efficiency in aluminum die casting, we not only contribute to a more sustainable manufacturing industry but also provide our customers with cost-effective solutions. The reduced material consumption translates into lower production costs, making aluminum die casting a highly economical choice without compromising on quality or performance.
Advantages of Material Efficiency in Aluminum Die Casting: |
---|
1. Reduced material consumption |
2. Precision and accuracy in complex designs |
3. Reusability and recycling of excess material |
4. Cost-effective solutions |
At [Company Name], we are committed to delivering high-quality aluminum die cast components that not only meet our customers’ requirements but also contribute to a more efficient and sustainable manufacturing industry. Our expertise in material efficiency, combined with our advanced casting techniques, ensures that we offer reliable and cost-effective solutions for a wide range of applications.
Superior Surface Finish with Aluminum Die Casting
As one of the leading aluminum die casting manufacturers, we take pride in delivering components with a superior surface finish, eliminating the need for costly and time-consuming post-processing. Through the precision and accuracy of the die casting process, we achieve a flawless surface that meets the highest standards of quality. Whether it’s intricate designs or smooth, polished finishes, our expertise in precision die casting ensures that every component reflects excellence.
By leveraging our advanced technologies and highly skilled workforce, we produce aluminum die cast components that are free from surface imperfections such as porosity, shrinkage, or roughness. The result is a consistently smooth and visually appealing surface that not only enhances the aesthetic appeal of the components but also improves their functionality. Our commitment to delivering superior surface finish sets us apart in the industry, offering our customers an unparalleled experience.
With aluminum die casting, the surface finish is achieved directly in the casting process, reducing the need for additional treatments. This not only saves time and resources but also ensures a more efficient production process.
Our dedication to excellence extends beyond the surface finish. We understand the importance of precision and attention to detail in every aspect of manufacturing. Through our state-of-the-art facilities and rigorous quality control measures, we ensure that each aluminum die cast component meets the highest standards of dimensional accuracy, structural integrity, and performance. Our commitment to precision die casting allows us to cater to a wide range of industries, including automotive, aerospace, electronics, and more.
Table: Advantages of Superior Surface Finish in Aluminum Die Casting
Advantages | Benefits |
---|---|
Enhanced aesthetics | Components with a flawless surface finish enhance the overall appearance of the product. |
Improved corrosion resistance | A superior surface finish provides increased protection against corrosion, ensuring the longevity of the components. |
Reduced friction | A smooth surface finish minimizes friction, allowing for smooth and efficient operation of the components. |
Easier cleaning and maintenance | A superior surface finish simplifies cleaning and maintenance processes, saving time and resources. |
Our commitment to delivering components with a superior surface finish is part of our broader mission to provide innovative, efficient, and sustainable solutions to our customers. As the global market for aluminum die casting continues to grow, we remain at the forefront, constantly pushing the boundaries of manufacturing excellence. With our unwavering focus on quality, precision, and customer satisfaction, we are confident in our ability to meet the diverse needs of industries worldwide.
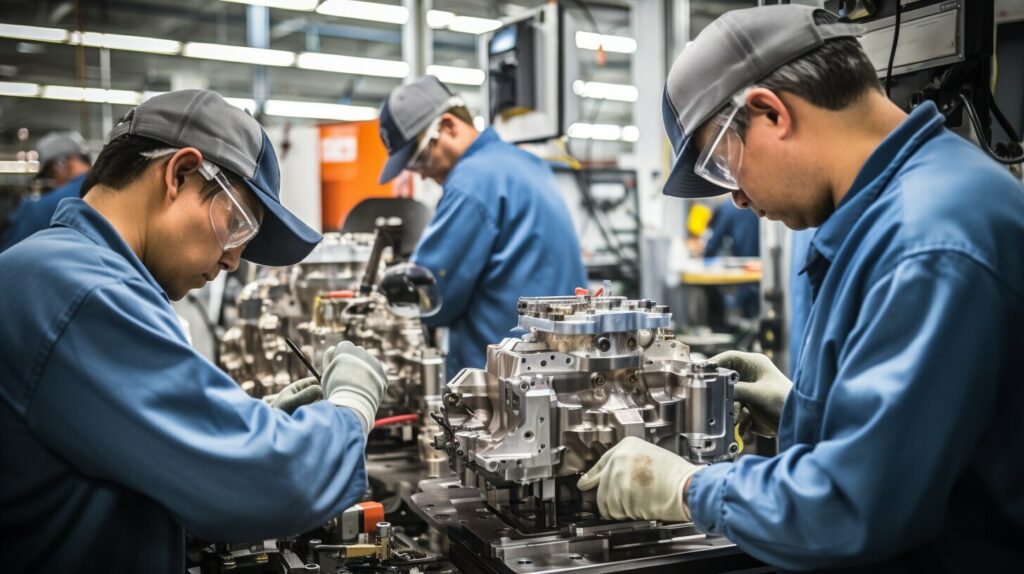
Automotive die casting, particularly with aluminum, has revolutionized the manufacturing process for a wide range of critical automotive components, including engine parts, transmission components, and body and exterior parts. The precision and accuracy achieved through the die casting process enable the production of complex and intricate components, ensuring optimal performance and durability.
One of the key advantages of aluminum die casting in the automotive industry is its ability to provide lightweight yet strong and durable components. This lightweight advantage not only improves fuel efficiency but also enhances overall vehicle performance. With its excellent strength-to-weight ratio, die-cast aluminum parts offer superior structural integrity while reducing the overall weight of the vehicle.
Die casting is widely used in the production of various automotive components, such as engine blocks, cylinder heads, transmission cases, and suspension components. The high-volume production capabilities of aluminum die casting make it an ideal solution for meeting the demands of the automotive industry. With minimal post-processing required, die casting ensures swift production and efficient manufacturing processes.
Advantages of Aluminum Die Casting in Automotive Applications: |
---|
• Lightweight components improve fuel efficiency and overall vehicle performance |
• Superior strength and durability for demanding automotive applications |
• Precision and accuracy in the production of complex components |
• High-volume production capabilities for efficient manufacturing processes |
The use of aluminum die casting in the automotive industry aligns with the industry’s pursuit of innovation, efficiency, and sustainability. By leveraging the advantages of die-cast aluminum components, automobile manufacturers can achieve lighter and more fuel-efficient vehicles while maintaining the necessary strength and performance criteria.
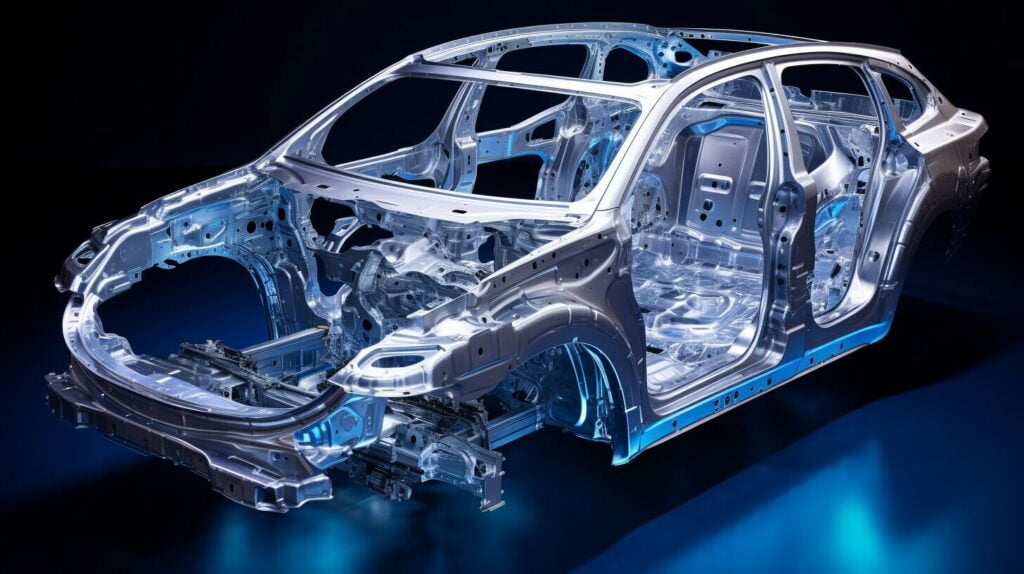
Lightweight Advantage and Vehicle Performance
Thanks to the lightweight nature of aluminum die cast components, automotive manufacturers can achieve significant improvements in fuel efficiency and overall vehicle performance, enhancing the driving experience for customers. Aluminum die casting is a manufacturing process that allows for the creation of intricate and complex components with high precision and accuracy. This makes it an ideal choice for automotive applications where lightweight yet strong parts are crucial.
Compared to other manufacturing processes, aluminum die casting offers several advantages that contribute to improved vehicle performance. The speed and efficiency of the die casting process allow for high-volume production, meeting the demands of the automotive industry. Additionally, the durability and strength of die-cast aluminum components ensure reliability and longevity, enhancing the safety and performance of vehicles.
The design flexibility provided by aluminum die casting also plays a significant role in improving vehicle performance. Manufacturers can create complex geometries and innovative solutions that optimize functionality and meet specific performance requirements. This flexibility allows for the integration of various features and functionalities, such as cooling channels, without compromising the overall weight of the component.
Aluminum die cast components offer a combination of lightweight construction and exceptional strength, making them ideal for applications that require high-performance and fuel-efficient vehicles.
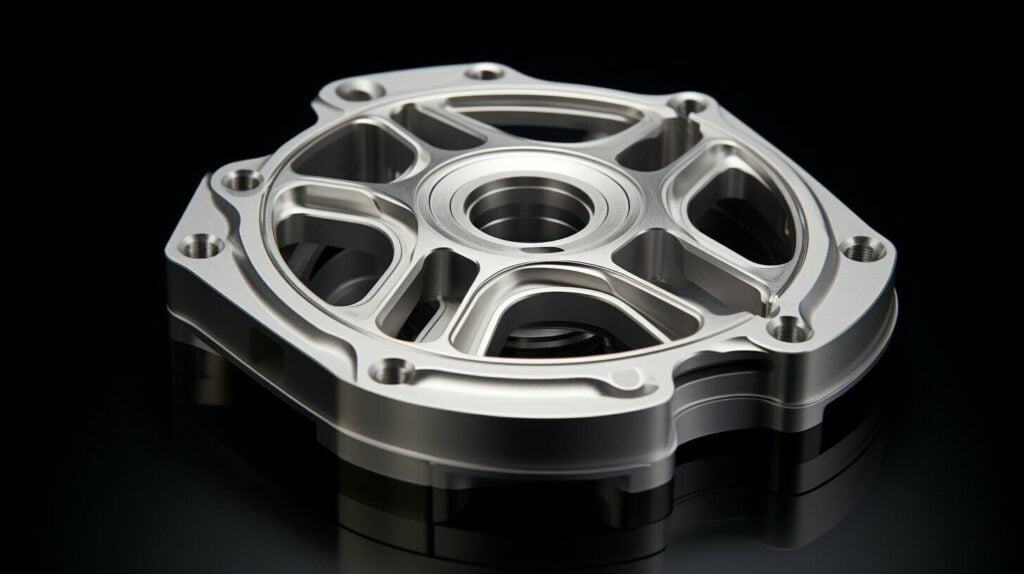
Application | Benefits |
---|---|
Engine Parts | Improved engine performance, reduced weight |
Transmission Parts | Enhanced shifting performance, increased fuel efficiency |
Steering and Suspension Components | Improved handling, reduced vibration |
Body and Exterior Parts | Lightweight construction, improved aerodynamics |
Electrical and Electronic Parts | Efficient electrical conductivity, reduced weight |
Thanks to its numerous advantages, aluminum die casting is expected to continue playing a vital role in the automotive industry. As the industry strives for innovation, efficiency, and sustainability, the lightweight advantage and performance benefits offered by aluminum die cast components make it an indispensable manufacturing process for the development of modern vehicles.
Market Outlook for Aluminum Die Casting
The aluminum die casting industry is experiencing remarkable growth, with the global market expected to reach $35.4 billion by 2028, driven by increasing demand for precision die casting solutions across a wide range of industries. This growth can be attributed to the numerous advantages offered by aluminum die casting, making it a popular choice in various applications.
The automotive sector, in particular, has witnessed significant adoption of aluminum die casting for the production of engine parts, transmission components, steering and suspension parts, body and exterior components, as well as electrical and electronic parts. The lightweight nature of die-cast aluminum components enhances fuel efficiency and overall vehicle performance, aligning with the industry’s focus on sustainability and efficiency.
Compared to other manufacturing processes, die casting stands out for its speed and efficiency, enabling high-volume production with minimal post-processing. With its ability to produce complex and intricate components with precision and accuracy, aluminum die casting offers design flexibility for innovative solutions.
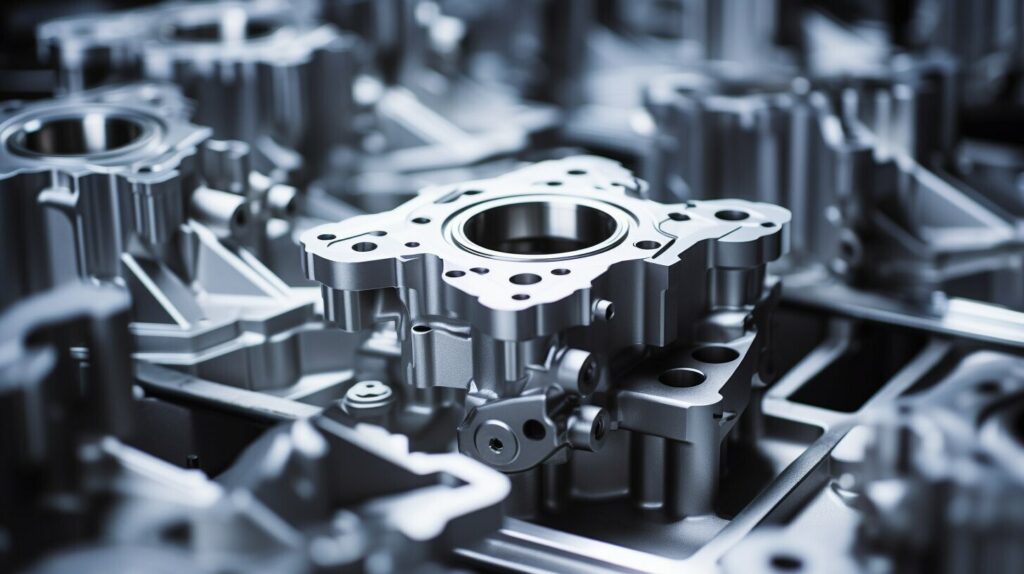
Furthermore, aluminum die casting ensures material efficiency, optimizing resource utilization and reducing waste. The process also delivers superior surface finish, eliminating the need for additional finishing processes. These factors contribute to the cost-effectiveness and overall competitiveness of aluminum die casting in the market.
As industries continue to prioritize precision, efficiency, and sustainability, the demand for aluminum die casting is expected to grow. The projected market growth highlights the importance of this manufacturing process in meeting the evolving needs and requirements of diverse industries.
Advantages of Aluminum Die Casting | Applications |
---|---|
Precision and accuracy | Engine parts |
Swift production | Transmission components |
Strength and durability | Steering and suspension parts |
Design flexibility | Body and exterior components |
Material efficiency | Electrical and electronic parts |
Superior surface finish |
Advancing Innovation, Efficiency, and Sustainability
Aluminum die casting plays a pivotal role in advancing innovation, efficiency, and sustainability within industries such as automotive, providing manufacturers with the tools they need to meet the challenges of a rapidly evolving market. With its exceptional precision and accuracy, die casting enables the production of complex and intricate components that are vital for enhancing performance and safety in vehicles.
The lightweight advantage of die-cast aluminum components cannot be overstated. This characteristic not only improves fuel efficiency but also contributes to overall vehicle performance. By reducing weight without compromising strength and durability, die-cast aluminum parts allow manufacturers to achieve optimal balance between performance and sustainability.
Furthermore, the design flexibility offered by aluminum die casting enables the creation of innovative solutions that push the boundaries of automotive engineering. Complex geometries and intricate details can be easily achieved, allowing for the integration of advanced functionalities and improved aesthetics.
Table: Automotive Components Produced Using Aluminum Die Casting
Component | Application |
---|---|
Engine Parts | Pistons, cylinder heads, engine blocks |
Transmission Parts | Gearboxes, transmission housings |
Steering and Suspension Components | Steering knuckles, control arms |
Body and Exterior Parts | Door frames, fenders, roof rails |
Electrical and Electronic Parts | Connectors, housings |
The automotive industry’s adoption of aluminum die casting has been instrumental in driving efficiency in manufacturing processes. Die casting offers swift production with high-volume capabilities, making it an ideal choice for meeting the demands of mass production. The material efficiency achieved through die casting also minimizes waste and optimizes resource utilization, aligning with sustainability goals.
With a projected market value of $35.4 billion by 2028, the aluminum die casting industry is poised for significant growth. As manufacturers continue to prioritize innovation, efficiency, and sustainability, aluminum die casting will remain a fundamental component of their strategies. By harnessing the advantages of this manufacturing process, the automotive industry can continue to revolutionize the way vehicles are crafted, delivering superior performance, fuel efficiency, and environmental sustainability.
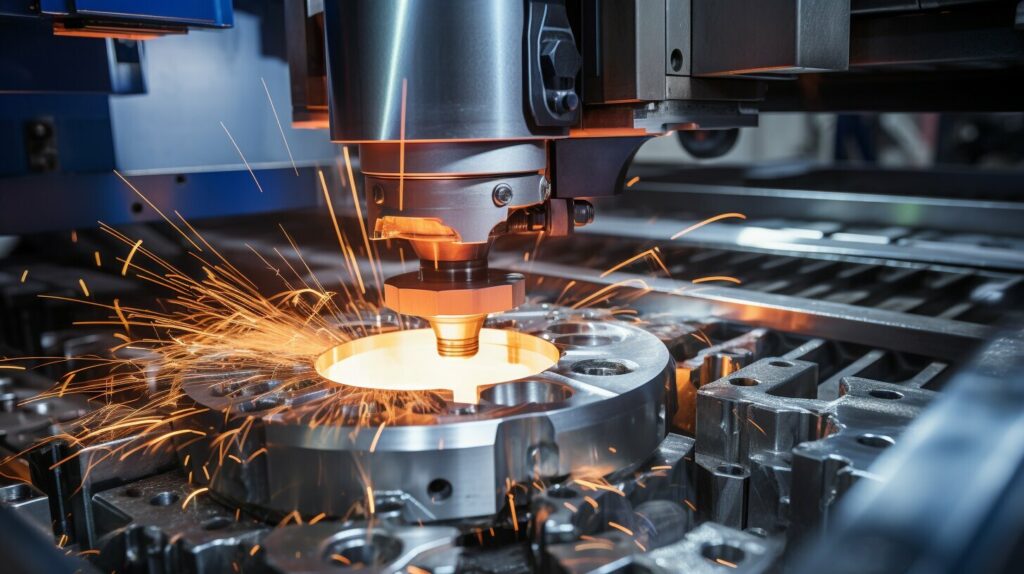
Disclaimer: The data provided in the table is for illustrative purposes only and may not represent the complete range of automotive components produced using aluminum die casting.
Conclusion
In conclusion, aluminum die casting offers unparalleled precision, swift production, strength and durability, design flexibility, material efficiency, and superior surface finish, making it the preferred choice for manufacturing a wide range of components in various industries. At KT-Foundry, we are dedicated to providing our customers with high-quality, lightweight, and cost-effective solutions that meet and exceed their expectations.
The automotive industry has particularly benefited from the advancements in aluminum die casting technology. Engine parts, transmission parts, steering and suspension components, body and exterior parts, and electrical and electronic parts are just a few examples of the automotive components that are produced using this efficient manufacturing process.
With its lightweight nature, die-cast aluminum components contribute to improved fuel efficiency and overall vehicle performance. Compared to other manufacturing processes, die casting offers speed, efficiency, and high-volume production with minimal post-processing, resulting in shorter lead times and reduced costs.
The global market for aluminum die casting is projected to grow significantly, reaching $35.4 billion by 2028. As the industry continues to evolve, the use of aluminum die casting in various sectors, including automotive, will play a vital role in driving innovation, improving efficiency, and promoting sustainability.
FAQ
What is aluminum die casting?
Aluminum die casting is a manufacturing process that involves injecting molten aluminum into a mold cavity under high pressure, resulting in precise shapes and dimensions.
What are the advantages of aluminum die casting?
Aluminum die casting offers several advantages, including precision and accuracy, swift production, strength and durability, design flexibility, material efficiency, and superior surface finish.
What automotive components are commonly produced using aluminum die casting?
Aluminum die casting is commonly used in the production of engine parts, transmission parts, steering and suspension components, body and exterior parts, and electrical and electronic parts.
How does aluminum die casting contribute to fuel efficiency and vehicle performance?
The lightweight nature of die-cast aluminum components improves fuel efficiency and overall vehicle performance.
What is the market outlook for aluminum die casting?
The global market for aluminum die casting is expected to reach $35.4 billion by 2028, indicating significant growth and potential.
How does aluminum die casting contribute to innovation, efficiency, and sustainability?
The use of aluminum die casting in industries like automotive enables innovation, improves efficiency, and promotes sustainability through the production of lightweight and cost-effective solutions.