Stainless steel contains a minimum of 10.5% chromium by mass. This element gives stainless steel its characteristic corrosion resistance by forming a thin, adherent, and protective oxide layer on its surface when exposed to air. It also typically contains other elements, such as nickel, molybdenum, titanium, and copper, contributing to their specific properties and performance characteristics.
Different stainless steel grades have unique properties, such as high-temperature resistance, increased strength, and corrosion-resistant properties.
The 304 and 316 stainless steels are the common grades used in different industries. Understanding the difference between the two grades can help you choose the most suitable material for your application and why it is better than other stainless steel grades.
What is a 304 Stainless Steel?
304 stainless steel is a type of austenitic stainless steels, which is the most commonly used type of stainless steel alloys. It is the most widely used stainless steel grade known for its superior corrosion resistance, good formability, and readily welded.
The melting point of 304 stainless steel is around 1400-1450°C (2552-2642°F). This high melting point is due to the presence of chromium and nickel in the alloy, which improves the steel’s high-temperature strength and resistance to oxidation.
304 stainless steel has a high heat resistance and can withstand temperatures up to 870°C (1600°F) without undergoing significant structural changes or losing strength. At elevated temperatures, the steel may experience some loss of tensile strength, but it retains its shape and is not prone to deformation.
What is a 316 Stainless Steel?
316 stainless steel is a type of austenitic stainless steel, a non-magnetic stainless steel alloy. These high-quality steel products are often used in harsh environments, such as corrosive chemicals or marine environments. It also offers excellent corrosion resistance, excellent weldability, and formability.
The melting point of 316 stainless steel is around 1375-1400°C (2500-2552°F). This is due to chromium, nickel, and molybdenum in the alloy.
It also has high heat resistance that can withstand temperatures up to 870°C (1600°F) without significant structural changes or loss of strength. However, prolonged exposure to high temperatures can also lead to sensitization in 316 stainless steel, causing the formation of chromium carbides at the grain boundaries and reduced corrosion resistance.
To prevent sensitization, the steel can be annealed or heat-treated to promote the re-dissolution of the carbides and restore its corrosion resistance.
Main Differences: 304 vs 316 Stainless Steel
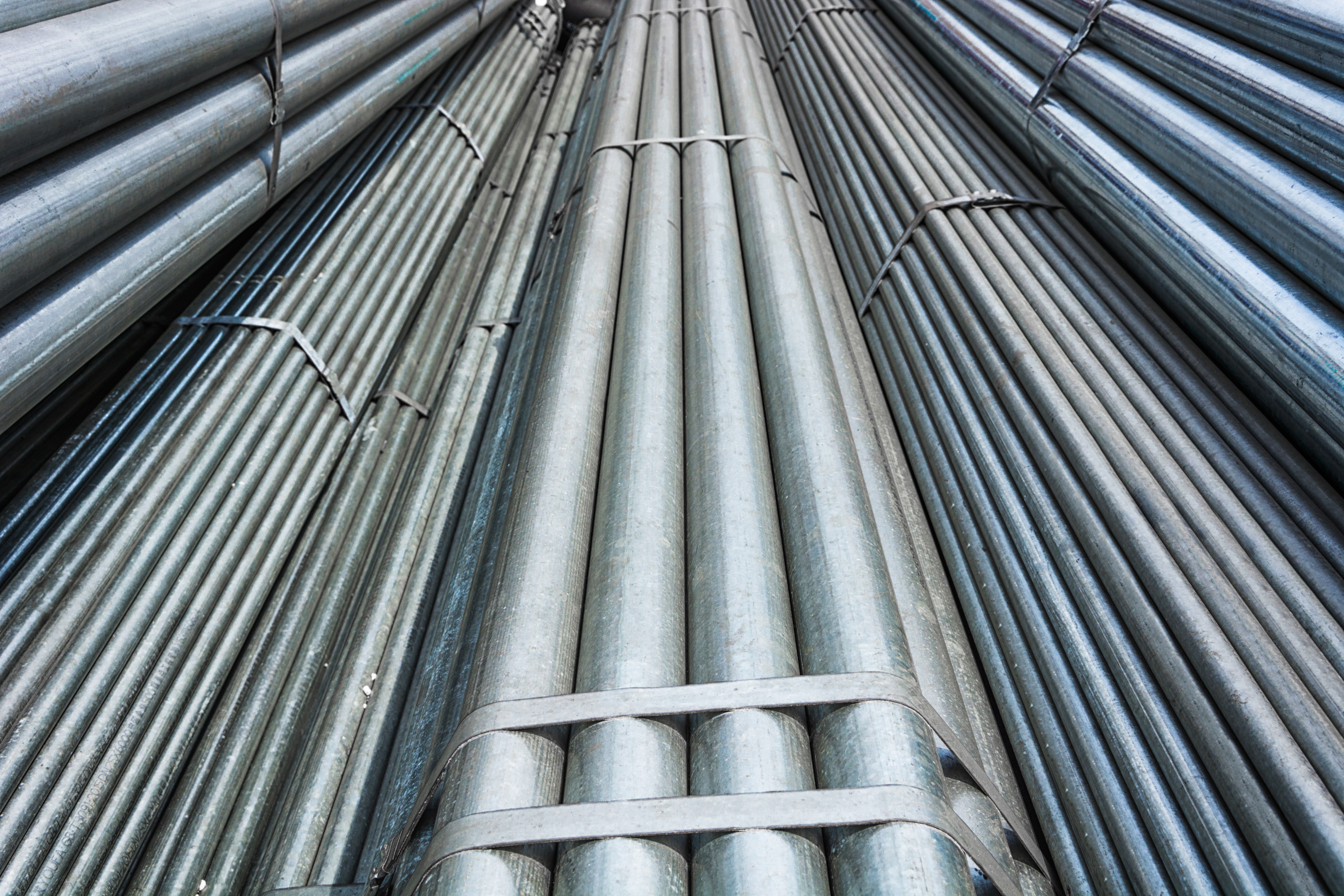
Due to its strength, durability, and corrosion resistance, stainless steel is widely used in various industries. However, 316 and 304 stainless steels offer different mechanical properties that must be present in different applications. Here are the main differences between 304 vs 316 stainless steel that you should consider.
Chemical Composition
304 stainless steel has a minimum of 18% chromium and 8% nickel with a maximum of 0.08% carbon.
Adding chromium and nickel content to 304 stainless steel provides excellent corrosion resistance and makes it suitable for various applications. The low carbon content helps prevent carbide precipitation, which can cause intergranular corrosion in such applications.
316 stainless steel may have a minimum of 16% chromium, 10% nickel, and additional alloys of 2% molybdenum with a maximum of 0.08% carbon.
Adding molybdenum to 316 stainless steel enhances corrosion resistance, particularly in environments containing chlorides or other corrosive and oxidation agents. The higher nickel content also improves corrosion resistance and makes it suitable for coastal regions. The low carbon content helps prevent carbide precipitation and intergranular corrosion.
The higher nickel and additional molybdenum content of 316 stainless steel make it stronger and provide extreme durability than 304 stainless steel. However, 304 stainless steel is still a suitable choice for applications where cost is a primary consideration, and high corrosion resistance is not critical.
Corrosion Resistance
304 stainless steel has excellent corrosion resistance due to the presence of chromium in its chemical composition. Additionally, the low carbon content in 304 stainless steel helps prevent carbide formation at the grain boundaries, which can lead to intergranular corrosion in some environments.
While 304 stainless steel is highly corrosion-resistant, it may still be susceptible to corrosion and chloride pitting. It is a versatile and corrosion-resistant alloy suitable for a wide range of applications, particularly those that do not involve exposure to strong disinfectants or high temperatures.
The chromium oxide layer acts as a barrier, preventing oxygen and other corrosive substances from penetrating the surface of the steel and causing corrosion.
316 stainless steel is highly corrosion-resistant and is ideal for use in harsh environments, such as marine or chemical processing applications like in custom wire baskets.
Tensile Strength and Durability
Regarding tensile strength, 316 stainless steel generally has higher tensile strength than 304 stainless steel. Adding molybdenum in 316 stainless steel improves its strength and durability, making it more resistant to pitting and crevice corrosion than 304 stainless steel.
However, the exact difference in tensile strength and yield strength between 304 and 316 stainless steel can vary depending on the specific grade and thickness of the alloy.
When it comes to durability, both 304 and 316 stainless steel are highly durable alloys that are resistant to corrosion, staining, and rust. However, molybdenum in 316 stainless steel makes it more resistant to certain types of corrosion, such as those caused by exposure to chlorides and other harsh chemicals.
316 stainless steel is often preferred in environments where resistance to corrosion is a critical factor, such as in the marine environment.
Price Difference
In general, 316 stainless steel is more expensive than 304 stainless steel due to its higher nickel and molybdenum content. These additional alloying elements improve its resistance to corrosion and overall performance of 316 stainless steel, making it a preferred choice for applications that require greater durability.
The price of stainless steel can also be influenced by availability, market demand, and manufacturing costs. The cost of producing stainless steel can vary depending on the manufacturing process used, the grade and quality of the raw materials, and other factors.
Applications of 304 Stainless Steel
Food and Kitchen Equipment
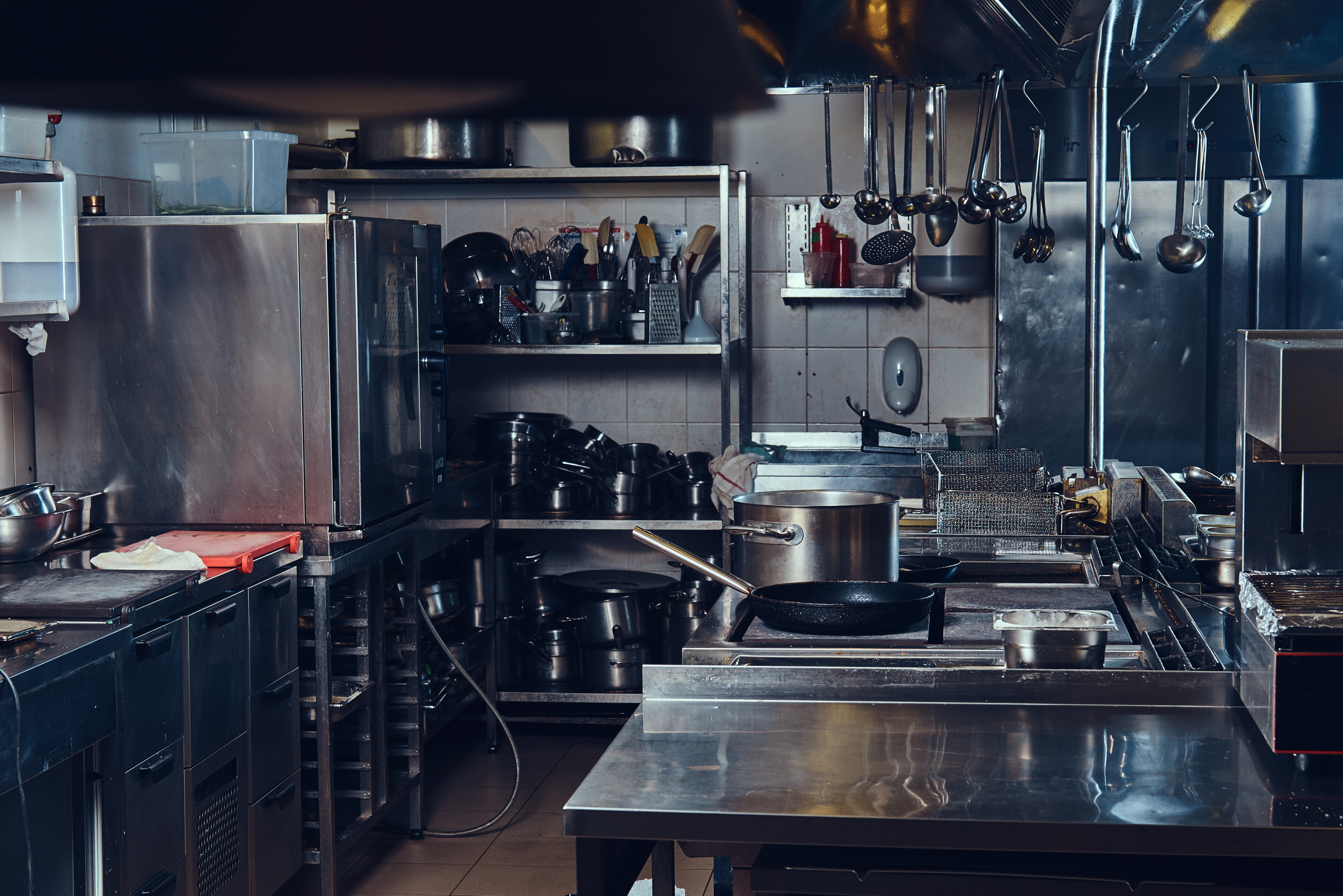
304 stainless steel is commonly used in food and kitchen equipment due to its excellent corrosion resistance, durability, and ease of cleaning. Stainless steel is a popular material for food preparation and storage equipment due to its non-reactivity with acidic or alkaline foods, which helps preserve the food’s flavor and quality. It is also non-porous, which helps to prevent the growth of bacteria and other microorganisms.
Storage Tanks
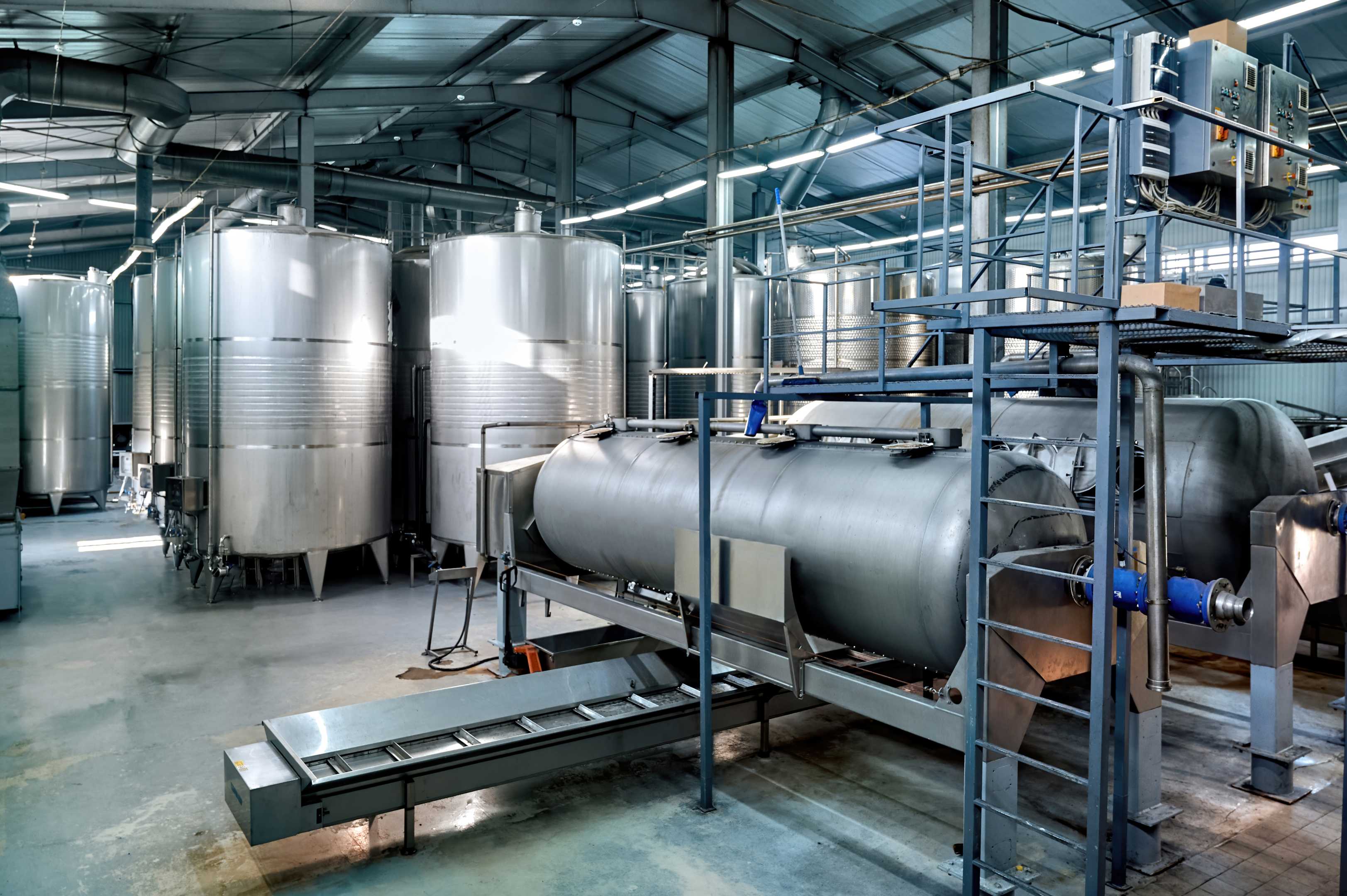
304 stainless steel has good temperature resistance, allowing it to be used for storage tanks exposed to high or low temperatures. The use of this grade in storage tanks is driven by its combination of excellent resistance to corrosion, durability, and hygiene, which help to ensure safe and reliable storage of liquids and other materials in a wide range of industries.
Applications of 316 Stainless Steel
Pharmaceutical and Medical Applications
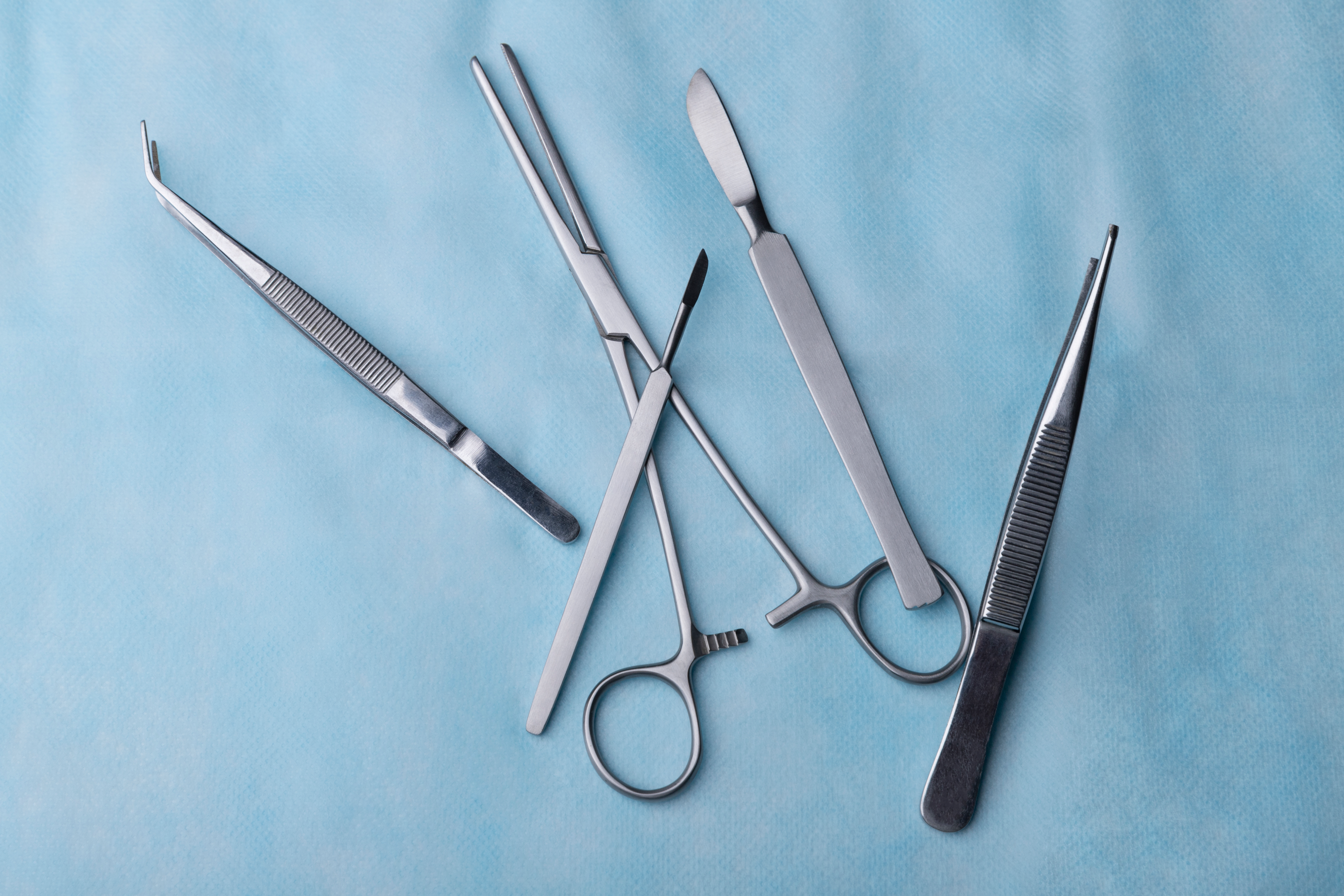
316 stainless steel is commonly used in pharmaceutical and medical applications due to its excellent corrosion, biocompatibility, and high-temperature resistance. This makes it suitable for medical implants, surgical instruments, and other medical equipment that come into contact with the human body. These properties help to ensure the safety and efficacy of medical treatments and pharmaceutical products.
Marine Applications
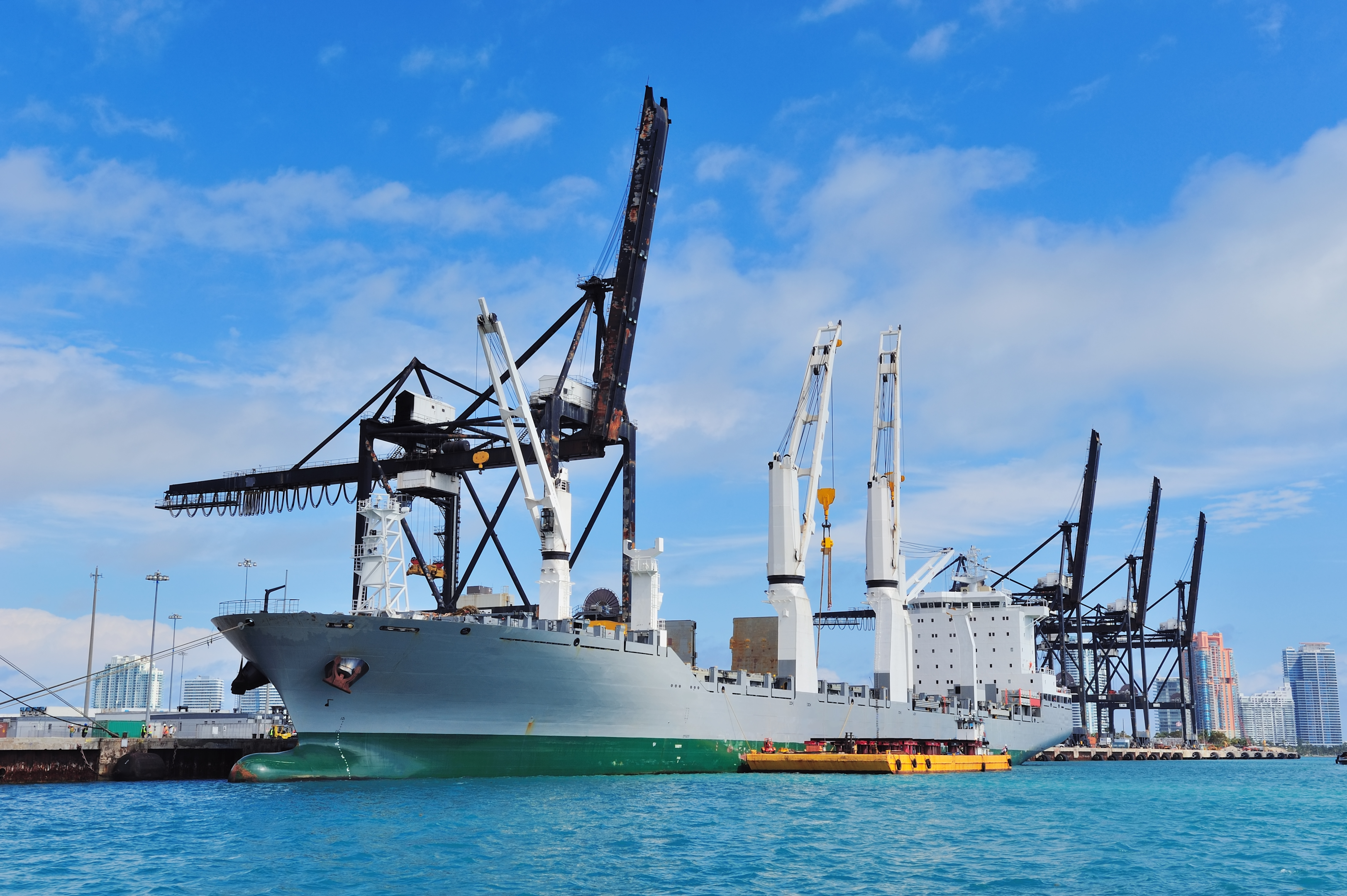
316 stainless steel is commonly used in marine applications due to its excellent corrosion resistance and durability in seawater environments. The marine environment can be particularly harsh, with exposure to saltwater, high humidity, and extreme temperatures, making it essential to use materials that can withstand these conditions. These properties ensure the safe and reliable operation of marine equipment and structures.