Ductile Iron is a versatile and cost-effective material used in many industries, such as automotive, oil and gas, and aerospace. It is known for its strength and durability, making it an ideal choice for various applications.
When determining the suitable ductile iron grade for your project, it’s essential to understand the specifications associated with each grade.
Ductile iron or nodular iron is produced using a process called spheroidize graphite, which creates graphite spheroids. This process increases the strength and ductility of the cast iron, allowing it to be used in applications where regular cast iron would not be suitable.
Ductile Iron Specifications According to the Ductile Iron Society
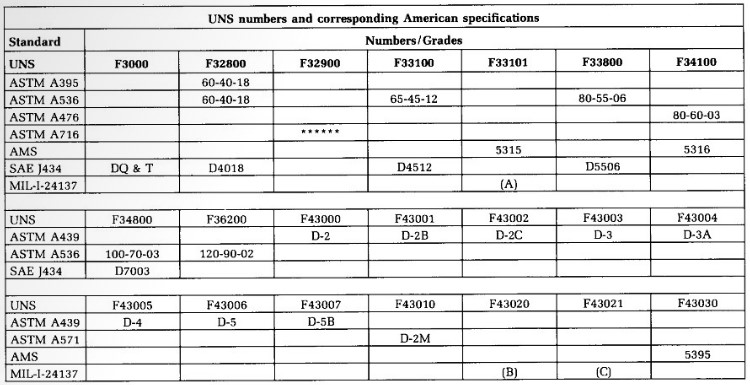
The different grades of ductile iron are based on the amount of graphite and other elements present in its matrix structure.
The grade of ductile iron refers to the amount of carbon, silicon, and other metals added to the alloy. There are several different grades of ductile iron, each with different properties and uses. The most common grades are Class 65-45-12, Class 80-55-06, and Class 100-70-03, all measured in percentages.
The first number indicates the amount of carbon, the second number indicates the amount of silicon, and the third number indicates the number of other metals present in the alloy. For example, a grade of 65-45-12 means the alloy has 65% carbon, 45% silicon, and 12% other metals.
These grades also have a standard term. The most common grades are ASTM A536 or ASTM A395, which have 60-40-18 classes. ASTM A536 is ductile iron with a tensile strength of 60,000 PSI and a yield strength of 40,000 PSI. It has good machinability and excellent resistance to wear and corrosion. ASTM A395 is a higher grade of ductile iron with a tensile strength of 70,000 PSI and a yield strength of 45,000 PSI.
Chemical Composition of Ductile Irons
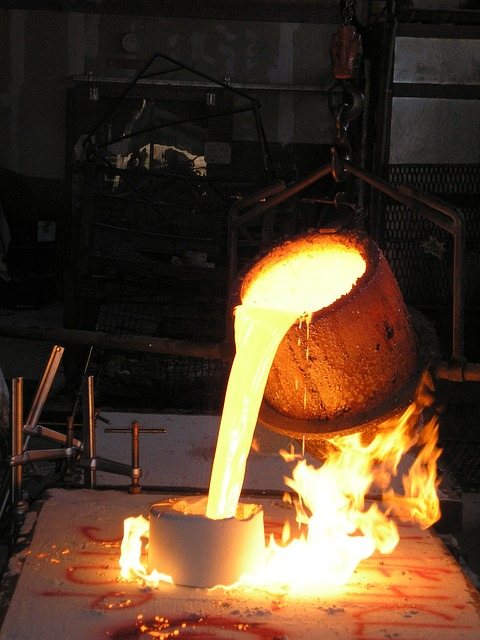
The chemical composition of ductile iron consists of iron (Fe), carbon (C), silicon (Si), manganese (Mn), phosphorus (P), sulfur (S), and small amounts of other elements. The exact composition of ductile iron varies, depending on the grade and type of iron used.
Silicon helps to improve the ductility and strength of iron. The manganese content helps to increase the hardness of the iron. The phosphorus content helps to increase the strength of the iron. The sulfur content helps to improve the machinability of the iron.
The graphite form in ductile irons is also essential for machining. The graphite particles act as lubricants, reducing friction and wear on the cutting tools during machining. This helps to reduce tool wear, improve machining efficiency, and reduce production costs.
Ferrite is an iron-based alloy with a body-centered cubic crystal structure. It comprises iron, carbon, and a small number of other elements, such as manganese and sulfur. Iron carbide is a compound consisting of iron and carbon. It is formed when the iron and carbon atoms combine during the cooling process of ductile iron.
The combination of ferrite and iron carbide in ductile iron gives it moderate ductility but good wear resistance.
Physical Properties of Ductile Irons
It is known for its strength and durability, but many don’t know that its physical properties can be further enhanced. Some processes that improve the physical properties of ductile iron castings are subsequent heat treatment, metal additives, and controlled processing.
Density
The density of ductile iron can vary depending on the composition of the alloy and the production process used. Adding more alloying elements can increase the density of ductile iron. For example, adding chromium to the alloy can increase the density of ductile iron by up to 8%.
The density of ductile iron is also affected by the heat treatment used during production. If the material is heat treated at a higher temperature, it can increase the density of the material by up to 10%.
Melting and Boiling Point
The high melting point of ductile iron makes it ideal for applications that require high heat resistance and pressure-containing parts.
For example, it is often used in automotive parts such as exhaust manifolds and gear boxes, where it is exposed to elevated temperatures for extended periods. It is also used in pipelines, as it is resistant to corrosion and can withstand high pressures.
Good Heat Conductor
Ductile iron has a higher thermal conductivity than other materials, including aluminum and steel. It can transfer heat more quickly and efficiently, allowing for better temperature control and thermal expansion.
This property is especially important in industrial applications such as heating and cooling systems, where high temperatures are necessary to achieve the desired results.
Mechanical Properties of Ductile Iron Castings
Ductile iron castings have unique mechanical properties comparable to other cast iron. Its combination of metals makes them easily cast, resulting in better mechanical properties.
Ductility
Ductility is the ability of a metal to bend or be drawn out without breaking. This characteristic is essential in applications that require a part to withstand a certain amount of stress without breaking.
Ductile iron castings have a higher ductility than other iron castings, making them a popular choice for parts that must withstand high-stress levels.
High Strength
These iron castings are machined and sandblasted to give them a smooth finish. This process gives the metal a higher strength-to-weight ratio than other materials.
Ductile Iron Castings has a tensile strength of up to 80,000 psi, making them much stronger than other cast materials. They also have a high fatigue strength, meaning they can withstand repeated stress without breaking. This makes them ideal for shock-loading applications such as engines and drivetrains.
Corrosion Resistance
The metallurgical structure of ductile iron castings also plays a vital role in their corrosion resistance. The castings are formed from a network of graphite flakes formed during the casting process. These graphite flakes are highly resistant to corrosion, providing an outer layer of protection for iron casting.
Another factor that contributes to the superior corrosion resistance of Ductile Iron Castings is the process of quenching and tempering. During this process, the castings are heated and then cooled quickly. This hardens the casting and strengthens its structure, making it more corrosion-resistant.
Impact Resistance
The increased impact resistance of ductile iron is due to its unique microstructure. The graphite in the cast iron is dispersed in a spheroidal form, which allows the material to absorb more of the impact forces and distribute it more evenly throughout the material.
This makes it an ideal choice for products that need to withstand high-impact forces, such as mining and construction equipment, as well as other industrial and consumer products.
Comparison of Ductile Iron, Gray Iron, and Spheroidal graphite iron
Each of these three types of iron has distinct advantages and disadvantages that must be carefully weighed when deciding which iron to use for your application.
Ductile iron is a type of cast iron that is highly flexible and ductile. It has a high tensile strength and is resistant to corrosion and wear. Ductile iron is also very resistant to abrasion and shock. It also has a high strength-to-weight ratio, which makes it an excellent choice for projects where weight is a significant consideration.
Gray iron, on the other hand, is a type of cast iron that is harder and more brittle than ductile iron. It has a higher melting point and is more prone to cracking and wear. Gray iron is less strong than ductile iron and more susceptible to corrosion and rust.
Spheroidal graphite iron, or nodular iron, is a type of cast iron composed of spheroidal graphite particles. It has a high strength-to-weight ratio and is very corrosion-resistant and wear-resistant. It is also highly ductile, making it an ideal choice for projects that require a high degree of flexibility.