Cast steel is a type of metal composed of iron, carbon, and other elements. It is created through casting, where molten steel is poured into a mold and allowed to cool and solidify. Cast steel is often used in place of wrought iron and is known for its superior strength compared to cast iron.
It is commonly used in constructing bridges and other structures and in producing machine tools, automotive applications, and industrial machinery. Cast steel has many benefits, including high corrosion resistance, excellent tensile strength, and a wide range of applications.
What is Cast Steel
Cast steel is made from melting a combination of iron, carbon, and other elements, depending on the good casting properties desired. It is produced in various grades, each of which has unique properties and characteristics.
The process of making cast steel is complex and requires various specialized tools and techniques. As a result, the cost of cast steel can be quite high. The casting performance of the end product depends largely on the quality of the raw materials used, the workers’ expertise, and the quality of the equipment used.
Physical and Mechanical Properties
The distinct physical properties of cast steel are a high melting point, good heat and electricity conductor, and high density. Because of its excellent heat resistance, it can be used in applications where high temperature is present. This makes it an ideal choice for heat exchanger components, engine components, and other applications where heat resistance is critical.
Cast steel is also known for its high strength, hardness, wear resistance, corrosion resistance, and malleability. The low carbon content the steel has its distinctive properties. The carbon creates a matrix of interlocking iron molecules that give the steel strength and hardness.
Steel casting also has good impact resistance. This is the ability of the material to resist a sudden shock or force. This is important in applications where the material may be exposed to sudden impacts. Cast steel typically has a high impact resistance, allowing it to absorb much energy without failing.
Cast steel also has good corrosion resistance. This is the ability of the material to resist the effects of water, chemicals, and other corrosive substances. Cast steel typically has good corrosion resistance, making it suitable for use in various applications where exposure to corrosive substances is expected.
How a Steel Casting is Produced
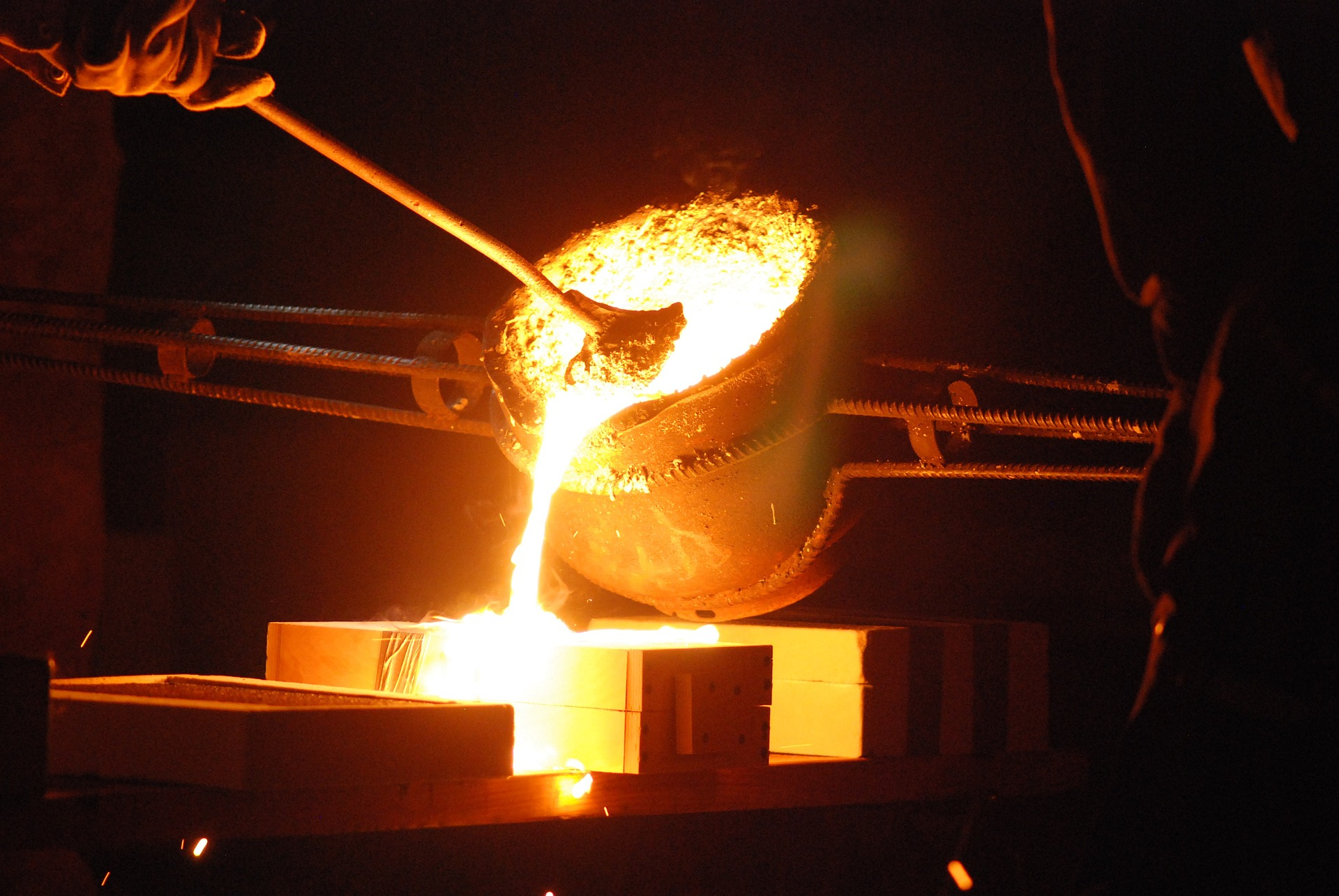
The process of steel casting involves melting steel and other alloys, pouring them into a mold, and allowing them to cool and solidify into the desired shape. To understand how steel casting works, it is important to understand the steps involved in the process.
Chemical Composition of Cast Steels
The main element of cast steel is iron. Depending on the application, cast steel may contain varying amounts of alloy steels, such as carbon, chromium, nickel, and vanadium. Carbon is used to increase the strength and hardness of the steel, while chromium and nickel are used to increase their corrosion resistance. Vanadium is also used for the higher strength and hardness of the steel.
The amount of carbon and other elements in the cast steel will affect its properties. For instance, low-carbon steel has good machinability, meaning it can be easily formed even with complex shapes. On the other hand, high-carbon steel has a higher tensile strength, meaning it is strong and durable.
Production of Alloy Steel Castings
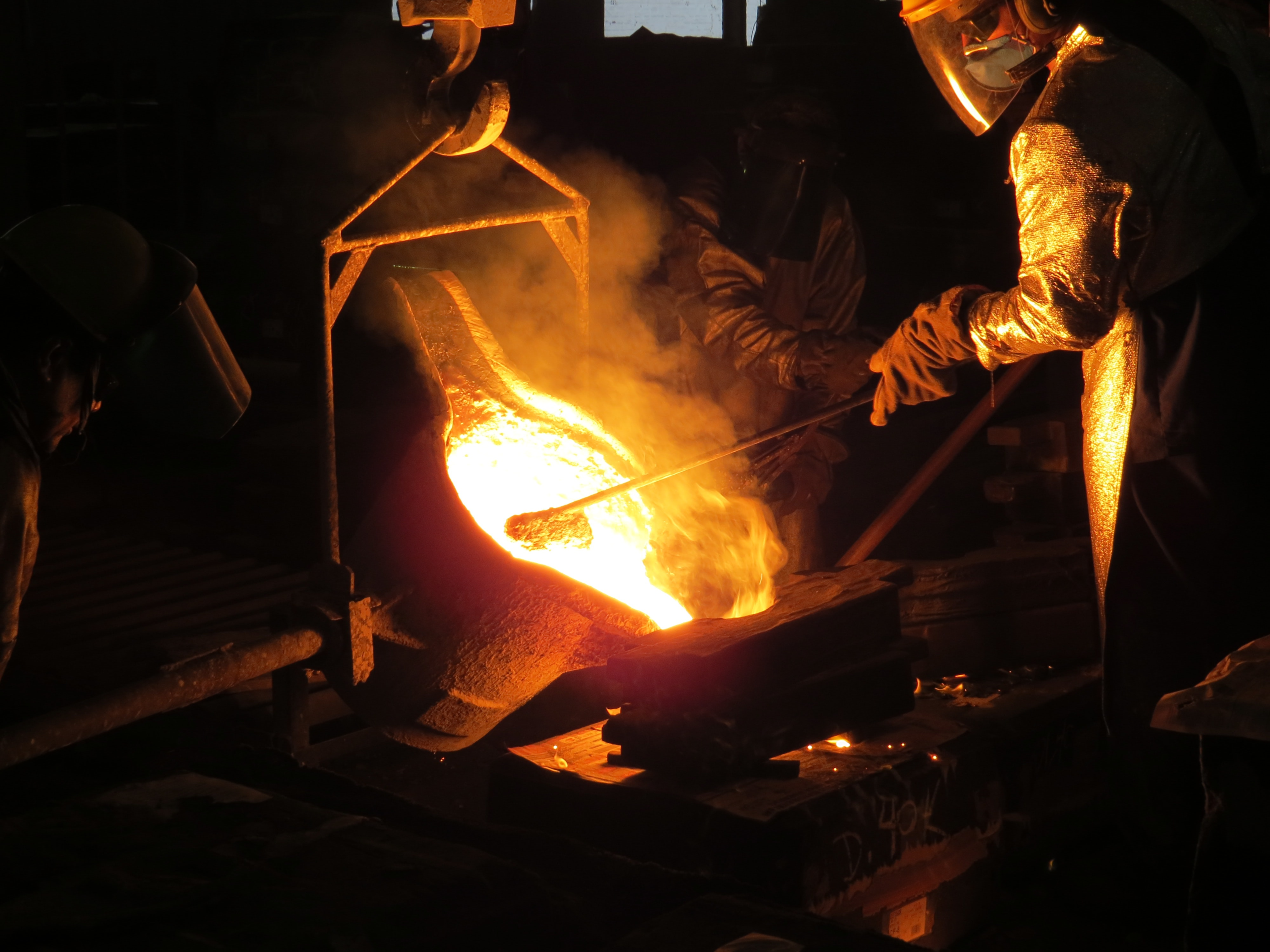
The production of cast steel begins with the selection of the correct type of steel. This is done by considering the desired properties of the steel and the required application. Once the proper alloying elements have been selected, they are melted in a furnace with iron and carbon. The molten steel is then poured into a mold. The shape of the mold will determine the shape of the final product.
Once the steel has been poured into the mold, it is allowed to cool before removing it. This cooling process is essential to avoid any cracking or distortion of the steel. The steel is heat treated to ensure it maintains its desired shape.
There are different heat treatment choices for steel castings. It includes annealing, normalizing, and tempering.
Finishing Process
Heat treatment is one of the most common methods used in casting steel’s finishing processes. Heat treatment involves heating the steel to specific temperatures and cooling it rapidly to achieve desired results.
Another finishing process used on cast steel is shot peening. This is a process where shots of metal or ceramic particles are shot at the steel at a high velocity. This creates compressive stress on the surface of the steel, which can improve its strength and fatigue resistance.
Sandblasting can also be done to improve casting properties. This process involves spraying the steel with an abrasive material such as aluminum oxide, which removes scale and other impurities from the surface of the steel. This can help improve the surface finish of the steel, as well as its corrosion resistance.
Two General Groups of Steel Castings
Carbon Steel
Carbon cast steel is made from a combination of iron and carbon. These are susceptible to corrosion, so they must be protected with a protective coating or treated with heat to make them corrosion-resistant.
The carbon content in low-carbon cast steel is typically less than 0.30% by weight. Normal carbon steel has about 0.35-1.50% carbon content in its total composition. High-carbon steel has 0.7-1.4% carbon content.
Alloy Steel
The combination of alloying elements and iron used to create alloy cast steel can vary depending on the desired properties of the final product. These elements are added to the molten iron to increase the strength and wear resistance of the alloy. Heat treatment is often used to refine further the properties of the alloy, including toughness, strength, and ductility.
Low-alloy cast steel is typically made from scrap iron mixed with small amounts of manganese, carbon, and other alloying elements. This combination of metals creates a durable material that is relatively inexpensive to produce.
High alloy steel is available in various grades, each with its unique properties. These grades are typically classified according to their carbon content. Additionally, some grades may contain other alloying elements, such as chromium, manganese, and molybdenum, which can affect the properties of the steel.
Quality Control Methods for Cast Steels
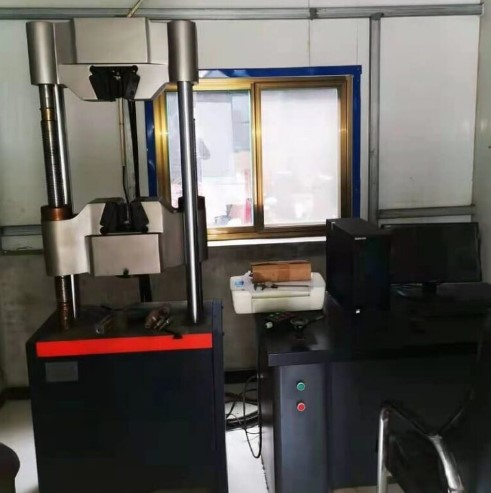
Quality control is essential for the successful production of cast steel. Quality control methods used in cast steel products are designed to ensure that the final product is free from defects, of the correct specification, and within the desired tolerances.
Chemical Analysis
The chemical analysis of cast steel can be used to determine the steel’s quality and identify any potential problems. These methods allow a quantitative measure of the elements present in the steel, such as carbon, sulfur, phosphorus, manganese, chromium, and nickel.
For example, by measuring the carbon content of the steel, it is possible to determine if the steel has been properly alloyed for the desired properties. Additionally, by measuring the sulfur and phosphorus content, it is possible to identify potential sources of defects, such as hot and cold shortness.
Visual Inspection
Visual inspection of cast steels is a relatively straightforward process. It begins with a visual inspection of the surface of the casting for any abnormalities. The inspector will then examine the casting for any visible signs of damage or defects. This includes looking for cracks, porosity, surface roughness, and other flaws.
It is also used to measure any dimensional accuracy of the casting. This is usually done using a measuring device such as a caliper or micrometer.
Hardness Testing
Hardness testing is conducted by measuring the resistance of the casting to indentation. A hardness tester, such as a Rockwell or Brinell tester, applies a force to the material and measures the indentation depth. The depth is then compared to a standard scale to determine the hardness.
Tensile Testing
Tensile testing is used to assess the material’s strength, ductility, and other properties. The strength of steel is determined by force required to break the specimen. Ductility is a measure of how much a casting can deform without breaking. Other properties, such as hardness, wear resistance, and fatigue resistance, can also be measured with tensile testing.
During the test, the specimen’s force, displacement, and strain are recorded. These values are then compared to the material’s specifications to ensure it meets the desired requirements.
Corrosion Testing
Corrosion testing is often used to evaluate the performance of various cast steels, as these materials are highly susceptible to corrosion. The most common type of corrosion test is a salt spray test, which involves exposing a sample of the material to a saline solution for a period of time and then measuring the amount of corrosion that occurs.
This test is beneficial for evaluating the corrosion resistance of cast steel, as the saline solution simulates the environment the steel may be exposed to in a real-world application.