Investment casting or lost wax casting is a manufacturing process that has been used for many years to create intricate investment cast using multiple wax patterns. It is a versatile manufacturing process that is used to produce parts in a wide range of sizes and shapes, including complex components.
Investment casting offers a number of advantages over other methods of casting, including higher accuracy, better surface finish, and lower production costs.
In this article, we’ll explain how investment casting works, the benefits it provides, and how it can be a cost-effective in manufacturing an investment material.
The Investment Casting Process
Also called as lost wax process, it involves using a wax tree or ceramic shell mold to form a cast around the desired object and pouring liquid metal into ceramic molds to form the desired shape. It is quite different from sand casting, since it uses a different mold material in creating its mold cavity.
This production process is popular in many industries, such as aerospace, automotive, and medical, due to its ability to create complex components with tight tolerances.
Creation of Master Pattern
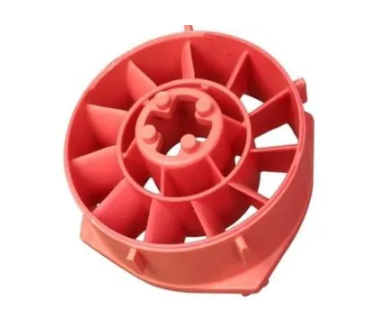
The process of creating a master pattern begins with designing a three-dimensional part. This design is used to create a wooden or plastic model, which serves as the basis in several wax patterns.
The model is then used to produce wax patterns, which is the exact replica of the part that will be cast. The master pattern is a critical component of this process, as it serves as the basis for all subsequent investment castings.
The pattern must be designed to be strong enough to withstand the high temperatures of the metal and the pressure of the metal being poured into the mold.
Wax Pattern Assembly

The wax pattern assembly is an essential part of the investment casting process. It requires precision and skill to ensure the desired part is created. The wax pattern must be of the highest quality and carefully assembled to get the desired result. Additionally, the mold must be heated and properly prepared to ensure the metal material solidifies correctly.
The wax pattern assembly process begins with the selection of the wax used to create the pattern. The wax must be of a certain quality and consistency for the process to work properly. Once the wax is chosen, it is heated and melted in a wax pot. From there, the pattern pieces are made by injecting wax.
Additionally, the mold must be heated and properly prepared to ensure the molten metal is poured in correctly.
Coating The Wax Pattern
The process of coating the wax pattern is an important step in the investment casting process.
The wax pattern is then coated with refractory materials such as ceramic slurry, silica, or zirconia. The refractory ceramic material acts as a barrier between the wax and the molten metal, ensuring that the molten metal does not seep into the wax pattern and weaken it.
The ceramic slurry is applied by either brushing, spraying, or dipping the wax pattern into the material. This coating is then allowed to dry before it is placed into the mold. The level of the coating will depend on the desired part being done and the type of metal being used.
Investment of Ceramic Mold
The ceramic mold is then heated in a kiln. As the wax melts, it leaves behind a hollow negative of the intended casting.
The type of ceramic shells used for the mold must be chosen carefully. Different materials have different melting points, so it is important to choose a material that can handle the temperature of the molten metal being poured into the mold.
Removal of Residual Wax
The most common method of removing residual wax from the casting is by using a chemical solvent. These solvents can be applied to the casting before or after the metal is poured. Depending on the type and amount of the remaining wax, the solvent can dissolve the wax and leave the casting clean and ready for the next step.
Another method of removing remaining wax is by using heat. Heat can be applied to the casting before or after the metal is poured. The heat will soften the wax and allow it to be more easily removed. This method is often used when dealing with thicker and more stubborn melted wax deposits.
Finishing or Secondary Machining for a Smooth Surface Finish
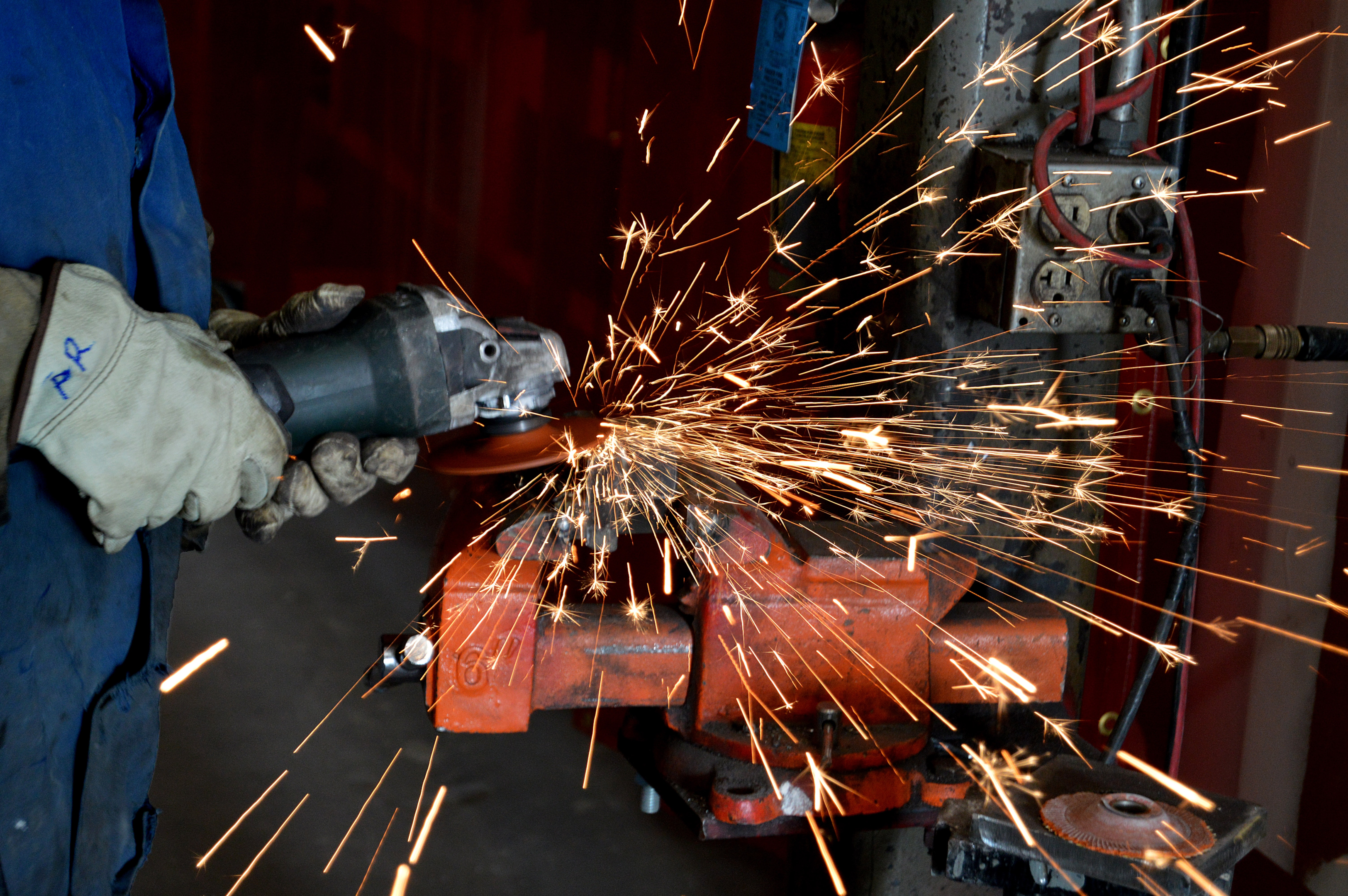
When it comes to investment casting, secondary machining is an important step in the process. This is because the investment casting process does not always yield a fine detail. The casting may have imperfections or the part may not meet the customer’s exact specifications.
Secondary machining can also be used to improve the surface finish of the part. This is especially important in applications where the part needs to be aesthetically pleasing.
Metal Alloys Used in Investment Casting Manufacturing Process
Metal alloys are used in investment casting because they have superior mechanical properties, such as strength, durability, and corrosion resistance.
The alloy must be able to withstand high temperatures and pressures during the casting process, as well as in the finished metal casting. Additionally, the alloy must produce a uniform and consistent high quality castings.
Stainless Steel
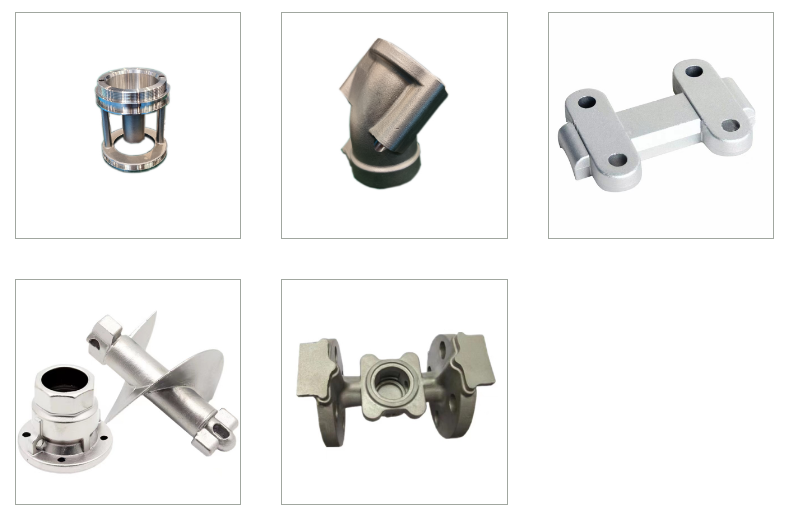
One of the most popular metals used in investment casting is stainless steel. While the strength of other metals may vary, stainless steel is highly resistant to wear and corrosion. This makes it the ideal material for creating precision parts that must withstand extreme conditions.
Unlike other metals, stainless steel can be used in a variety of different applications. It is strong enough to be used for parts that require strength and durability, yet can also be used for parts that require intricate detailing and intricate shapes.
Aluminum
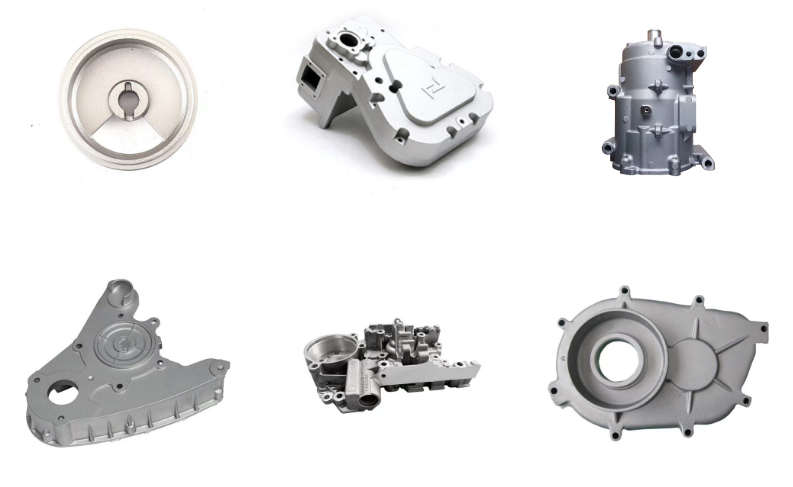
Aluminum alloy is a mixture of different metals, including copper, zinc, magnesium and silicon. Each alloy has different properties and characteristics, and the right alloy must be chosen depending on the component’s application.
This type of alloy has a higher strength-to-weight ratio than pure aluminum, making them suitable for components that require strength but are still lightweight.
Carbon Steel

Carbon steel is an ideal material for investment casting because it is strong, durable, and cost-effective. Heat treating can improve its strength and wear resistance. This makes it ideal for parts that will be exposed to high levels of mechanical stress or friction, such as engine components.
The ductility of carbon steel also makes it an ideal material for investment casting, as it is able to be formed into complex shapes without compromising its strength.
Investment Casting Advantages
Investment casting offers a number of advantages over other manufacturing processes, no wonder it is becoming increasingly popular in manufacturing engineering across a variety of industries.
High-Quality and Precision Casting
The primary advantage of investment casting is the ability to produce parts with high precision and accuracy. The wax patterns are generally machined from steel or aluminum, so each component is created with exacting tolerances. This allows for the production of complex parts with tight tolerances and minimal material waste.
Low Production Cost
The process is much less labor-intensive than other metalworking methods, making it a cost-effective solution for producing precision parts. The process also does not require any specialized or expensive tooling or machinery, making it an ideal choice for businesses with limited budgets.
Additionally, the process is relatively quick, with parts being able to be completed in as little as a few hours.
Wide Range of Alloys and Metal Casting
Many metals and alloys are suitable for investment casting, including aluminum, stainless steel, brass, bronze, and even titanium. This allows for a wide range of parts to be created, as the right alloy can be chosen for the specific application.
For example, steel alloys can be used to create components with different levels of strength and hardness. Aluminum alloys can be used to create components with a wide range of strength, hardness, and corrosion resistance.
Applications of Investment Castings
Investment casting, also called lost-wax casting, is a precision casting process used to produce components with intricate shapes and fine details. This process is used to create parts for a wide array of industries, from aerospace and automotive to medical and consumer goods.
Automotive Industry
One of the most common uses for investment castings in the automotive industry is for engine components. Many of the parts found in an engine, such as pistons, valves, and rocker arms, are made using investment castings.
Investment castings are also used to create other important automotive components. These include brake and suspension parts, transmission components, and gearbox components. Investment castings are also used to make many of the decorative parts found on cars, such as trim pieces and badges.
Turbine Blades
Turbine blades are integral components of jet engines and other types of turbines, and as such must be designed and manufactured to exacting standards. Investment casting process offer excellent dimensional accuracy and repeatability, reducing the need for additional machining operations and ensuring that blades have a consistent shape and size.
Machine Tools
This casting process is used for producing components for machine tool spindles and other rotating components. This is because investment casting can produce components with a high degree of accuracy, which is essential for the efficient operation of a machine tool.
Which Casting Service is Better?
Different casting services may have different levels of expertise in creating complex parts. If your project requires a complex shape or intricate details, you should look for a casting service that specializes in that type of work.
When choosing a casting process, it’s important to consider the size and complexity of the part, the desired accuracy and surface finish, and the budget. Investment casting is typically the best choice for complex parts with tight tolerances, while other casting processes are more suitable for larger and simpler parts.