Stainless steel is a durable and versatile material used in various products and applications. It is composed of high-performance alloys and is widely used in different industries. Its versatility and strength make it an ideal choice for many applications.
Many manufacturers and consumers prefer investment casting since it is the most common casting processes of stainless steel. Other casting processes include sand casting and die casting.
How Investment Casting Process is Done
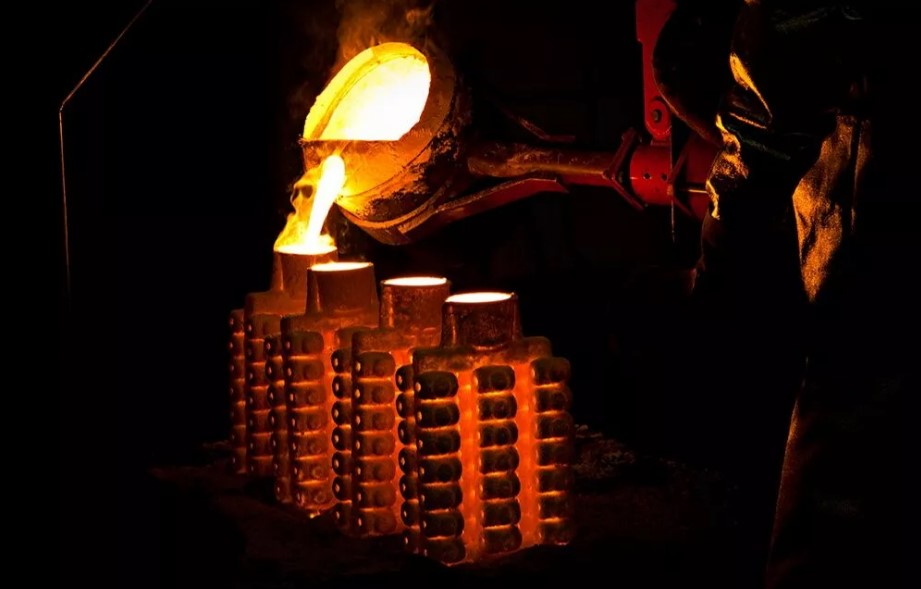
Creating stainless steel components via investment casting requires a precise and complex process. Each of these steps requires careful attention and precision to achieve the desired mechanical properties of the stainless steel casting blanks.
Preparing Wax Patterns
To ensure the highest quality of the stainless steel material, it is essential to prepare several wax patterns accurately.
Once the pattern has been designed, it should be tested in a wax model to ensure that it will produce a precision casting when used in an investment mold.
The master wax pattern should then be inspected for high dimensional accuracy, and necessary adjustments should be made before creating the ceramic mold.
Ceramic Shell Building
Ceramic shell building involves using a high-temperature oven for baking the ceramic shell and melting the wax model. The oven must be heated to a temperature higher than the alloy’s melting point to be cast. Once the shell has been baked, it is allowed to cool to room temperature.
Once the shell has cooled, it is placed in a vacuum chamber. A vacuum is used to evacuate any air inside the shell.
The shell-building process allows a casting component to have an exceptional surface quality.
Metal Forming Process
The molten stainless steel is processed using an electric furnace that reaches temperatures up to 1,650 degrees Celsius.
The molten metal is then allowed to cool and harden. After the casting has cooled and hardened, the flask is broken away, revealing the stainless steel casting.
Finishing Processes for Stainless Steel Castings
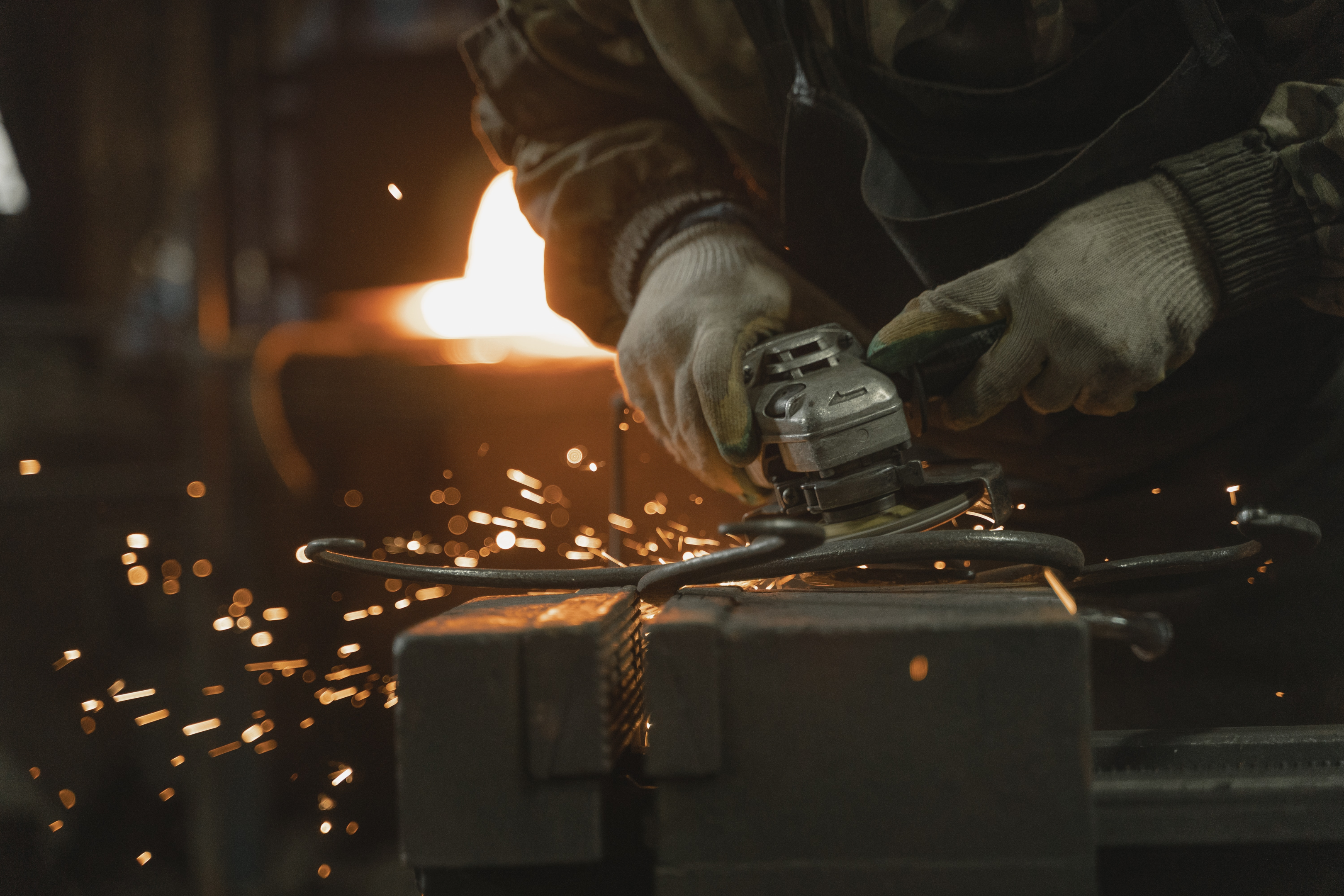
Grinding and polishing tools can be used to remove sharp edges and burrs. This is done to remove excess materials from the investment casting.
It is also coated with a protective film such as paint, electroplating, or powder coating. A chromium oxide film may also be used for parts that require a superior surface finish.
Elements Used in Stainless Steel Alloys
Iron is the base metal used in stainless steel alloys, and it is responsible for the material’s magnetic properties, strength, and ductility.
Chromium is responsible for the alloy’s smooth surface finish and corrosion resistance. The amount of chromium used in the low-carbon steel determines its corrosion-resistant properties.
Nickel is another essential element used in stainless steel alloys. It improves the alloy’s ability to withstand high temperatures.
Common Stainless Steel Investment Casting Alloy Grades Used

Martensitic Stainless Steel
Among all grades of stainless steels, martensitic stainless steel contains relatively high levels of carbon combined with alloying elements.
It may undergo heat treatment to produce different grades of stainless steel. This process can alter the physical and chemical properties of the alloy, allowing manufacturers to tailor it for specific applications.
The most common grades of martensitic stainless steel include 410, 420, and 440A. Each grade has a unique combination of elements with varying hardness and corrosion resistance levels.
Austenitic Stainless Steel
Austenitic stainless steel comprises iron, 16% to 26% chromium, and nickel, with small amounts of other elements such as molybdenum, manganese, and nitrogen.
The nickel content, conversely, provides the stainless steel investment castings with non-magnetic and physical properties.
Applications of Stainless Steel Investment Castings
Industrial Application
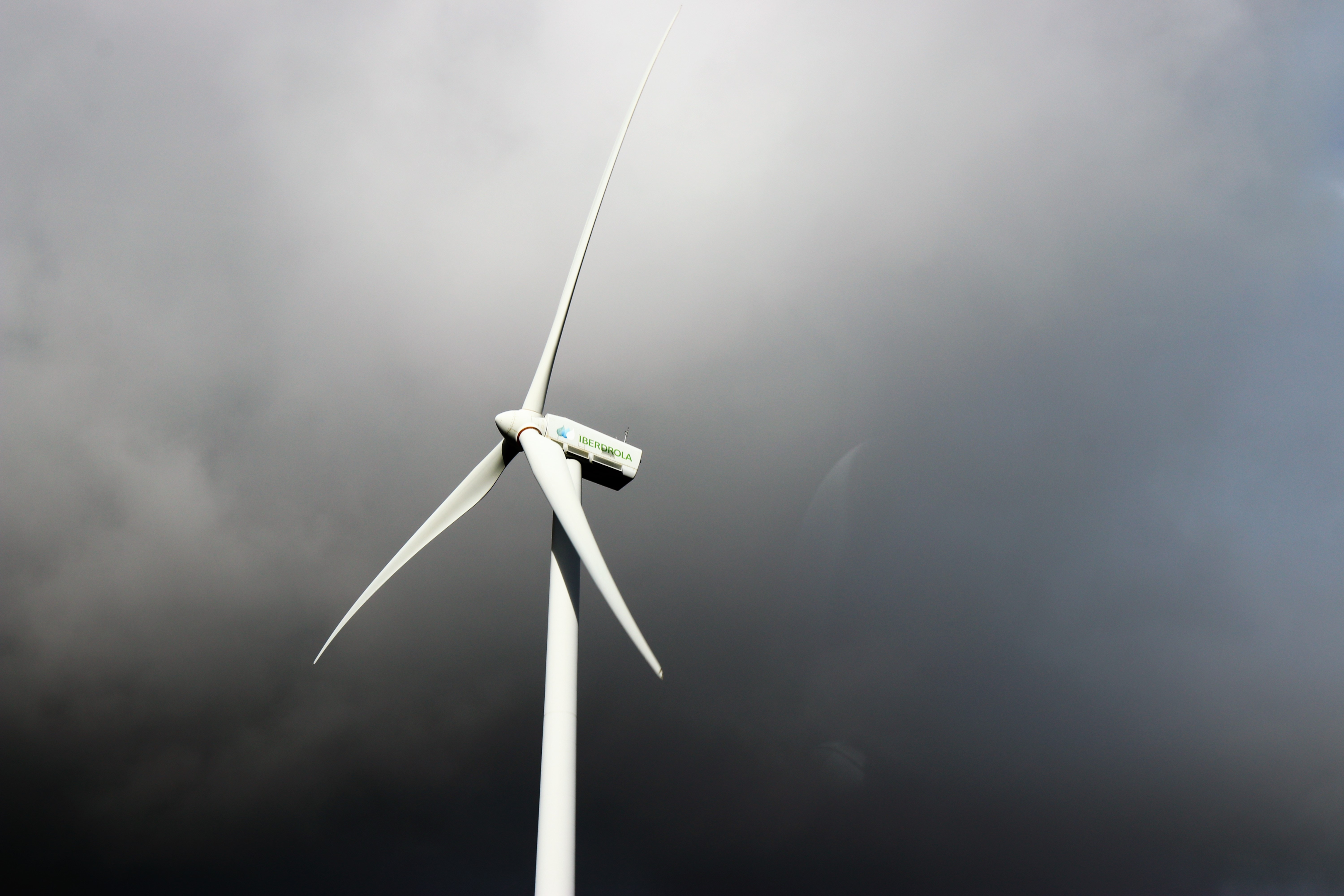
Stainless steel investment castings are used in various industrial applications, from turbine blades, automotive components, pipe fittings, medical devices, and tools. Their corrosion resistance makes them an ideal choice for components that must withstand harsh environments, such as marine environments.
Food Machinery
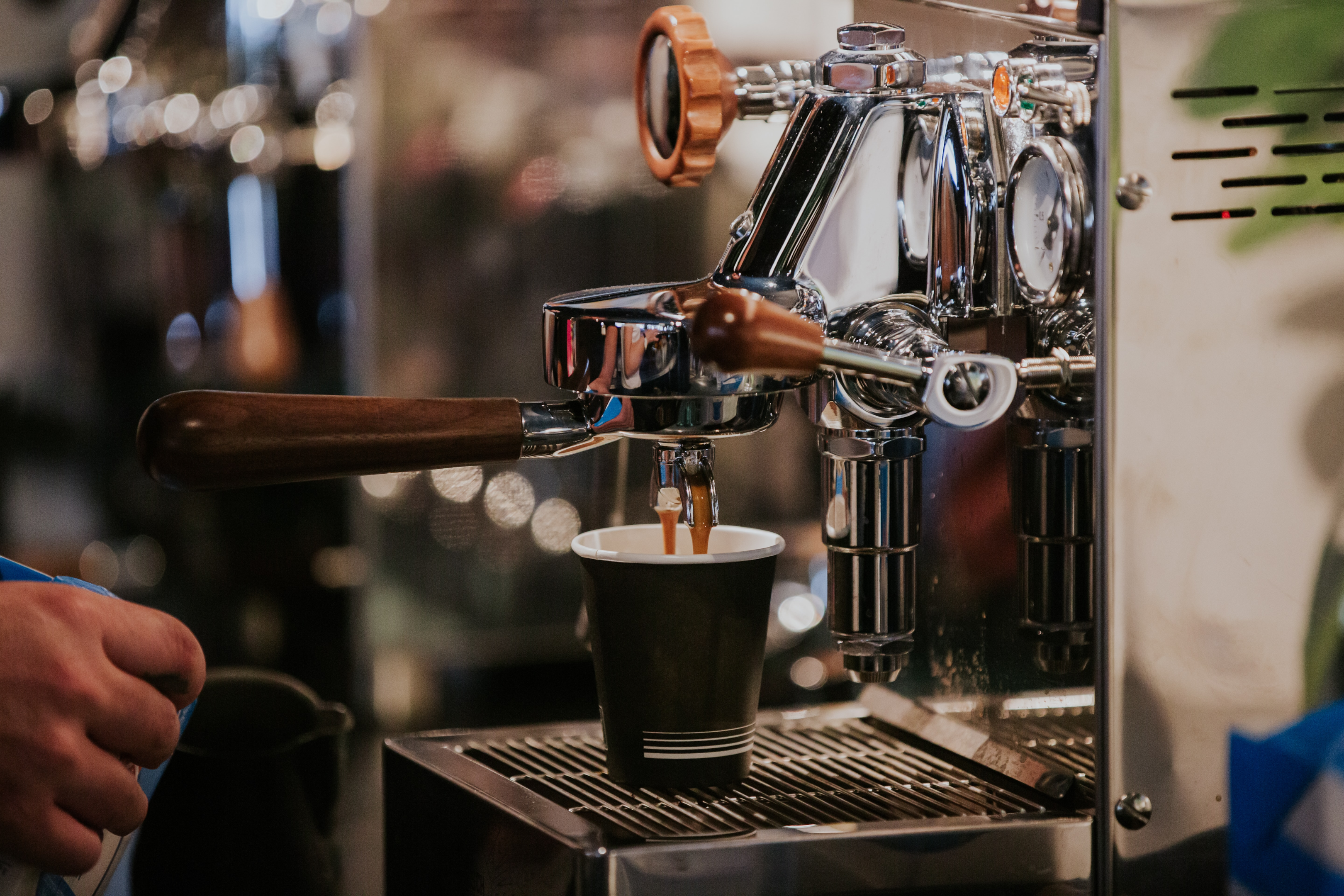
Stainless steel castings are magnetic and has good heat resistance, making it suitable for use in ovens and other high-temperature applications. It is essential to choose a grade of stainless steel that is non-reactive and does not leach chemicals into food. Grades such as 304 and 316 stainless steel are ideal for coffee machine components because of their non-reactive nature.
The metal is also non-toxic, making it safe to use in contact with food.
Medical Equipment
Investment castings are used in various medical equipment applications, including orthopedic implants, surgical tools, operating room equipment, x-ray equipment, and medical instruments.
They can be used for internal and external components, providing a reliable and cost-effective solution for manufacturers of medical devices.
Stainless steels are also ideal for components that need to be resistant to wear and tear, such as bone plates, bone screws, and hip joints.