Investment casting, or lost wax casting, is a manufacturing process used to produce complex and intricate metal components with high dimensional accuracy, surface finish, and detail. It involves creating wax patterns or models of the investment cast coated with a ceramic shell to form a mold.
Investment casting produces a wide range of parts with intricate shapes, including electrical components, medical implants, golf club heads, turbine blades, and industrial applications.
The investment casting process offers excellent dimensional accuracy, displays smooth surfaces, and the ability to cast complex shapes. It is also a cost-effective method to produce components in small and medium-sized production runs. This article will help you with what materials are suitable for investment casting.
Basic Principles of Investment Castings
Investment casting offers several advantages over other casting methods. Though a complex production process, it can produce highly detailed and quality castings with high structural integrity and fine surface finishes. The process can cast various materials, including metals, alloys, and ceramics.
Investment Casting Process
The first step in investment casting is to produce wax patterns of the desired final part. The multiple wax patterns can be made using a mold or a 3D printing technique. The wax pattern is made to the final part’s exact dimensions and surface finish requirements. A heated metal tool can remove parting lines from a wax pattern.
The wax pattern is then coated with a ceramic material that hardens into a ceramic shell, creating the mold for casting. The ceramic mold may be built up in layers to achieve the desired pattern thickness and strength, with an average wall thickness of 0.375 inches. Ceramic slurry layers are allowed to dry before the next one is added to ensure uniform surface coating until the desired thickness is reached.
Once the ceramic mold is complete, it is heat treated to high temperatures. Specialized heat-treating processes harden the ceramic shell and remove the residual wax, leaving behind a hollow cavity in the shape of the part. However, shell failures occur if the wax expands larger than refractory materials.
The mold is then filled with molten metal, which is allowed to solidify inside the cavity. Once the liquid investment material has cooled and solidified, the ceramic shell is broken away to reveal the finished part.
Advantages of Investment Casting Over Other Metal Casting Processes
Investment casting, also known as lost wax casting, offers several advantages over other metal casting processes, including sand casting, die casting, and permanent mold casting. It is relatively more accessible than a more complex production process.
It produces castings with a smooth, polished surface finish, with no parting lines or flashes. This eliminates the need for additional finishing operations and reduces material waste. It can also produce parts with very tight tolerances, allowing for complex geometries and precise shapes. This makes it ideal for producing parts with intricate features or thin walls.
Investment casting allows for producing parts with complex shapes and internal geometries that would be difficult or impossible to achieve with other casting methods. Its ability to use soluble wax cores reduces the need to assemble or join multiple parts.
Factors Affecting The Selection of Investment Casting Materials
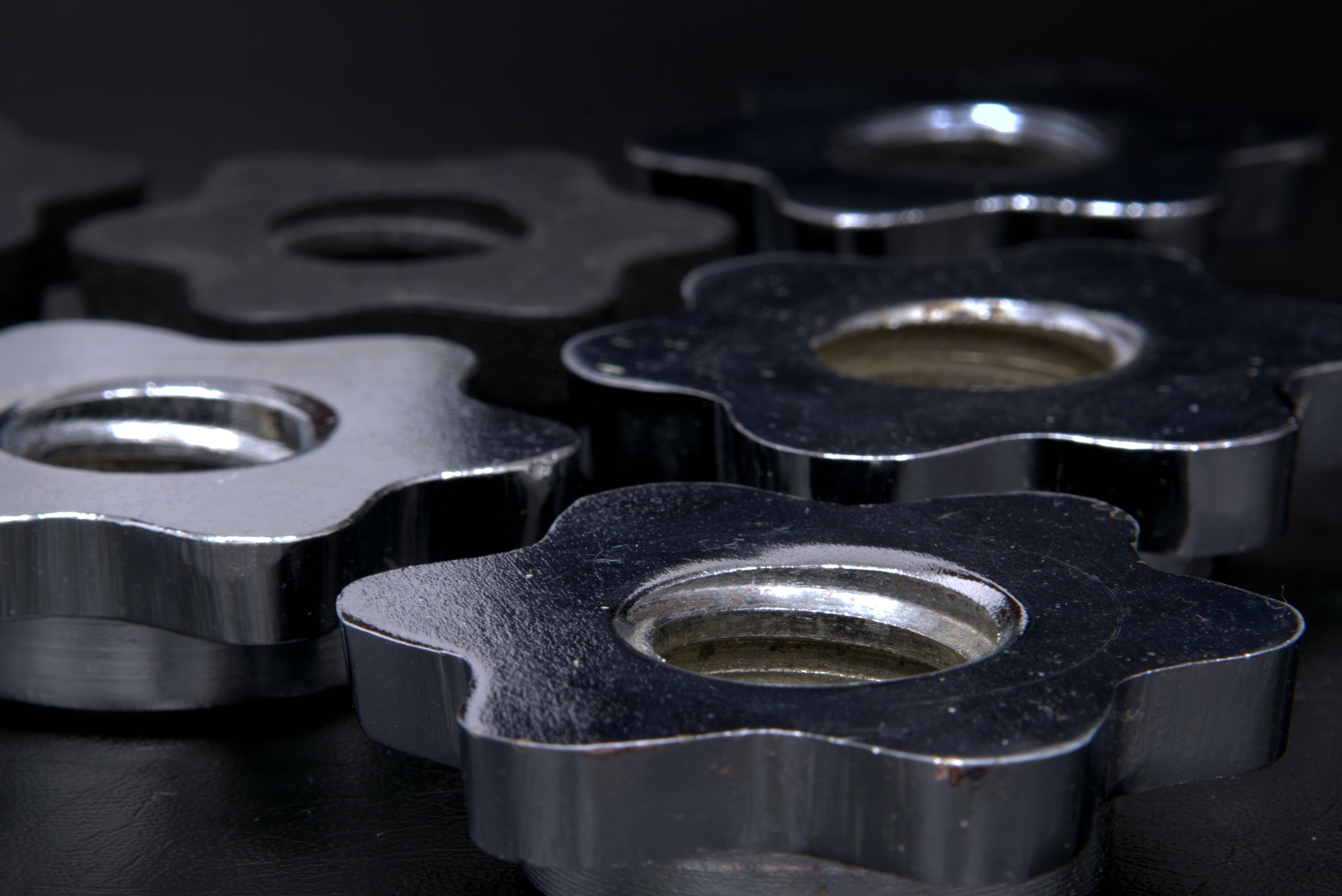
Choosing the right material for the process is one of the most critical factors in investment casting. Proper material selection for the pattern, ceramic shell, and final part ensures that the finished product meets the required superior service characteristics and performs as intended.
Strength and Durability
The material used for the final part must have the strength and durability to perform as intended. If the material is too brittle, it may crack or fail under stress, while if it is too soft, it may deform or wear out too quickly.
Dimensional Accuracy
The material used for the pattern must hold its shape during the casting process and accurately reproduce the desired dimensions of the final part. The final part may not meet the required specifications if the material shrinks or deforms during the process.
Cost
The cost of the material used for investment casting can significantly impact the overall production cost of the final part. Choosing a versatile, affordable material while still meeting the required specifications can help keep costs down.
Materials Suitable for Investment Casting Process
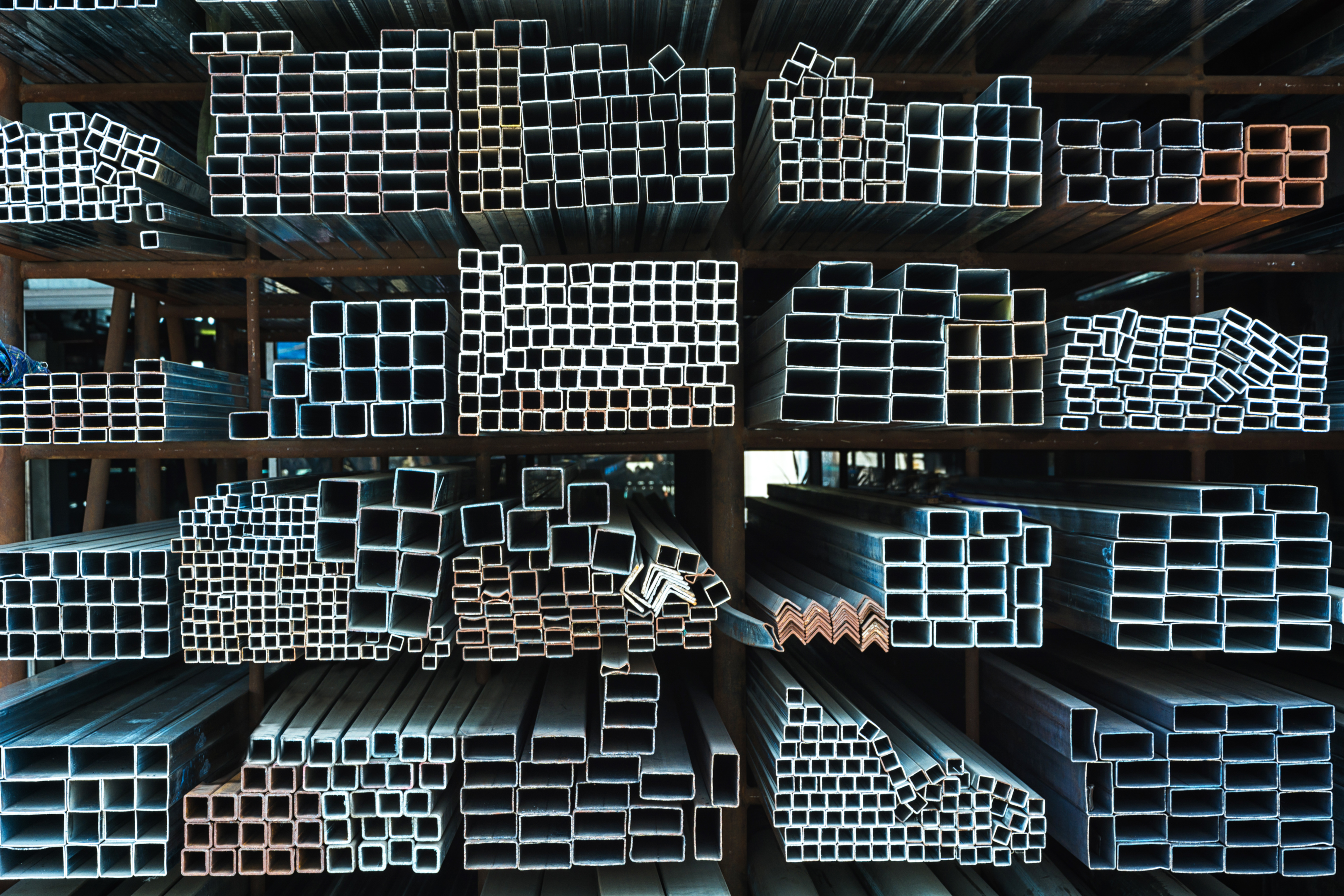
The choice of material for investment casting will depend on several factors, such as the properties required for the final part, the casting process, and the intended application.
The chemical properties of the material can also play a role in the selection process. Some materials may have higher corrosion resistance, oxidation, or other types of chemical degradation, making them better suited for specific applications.
Carbon Steel
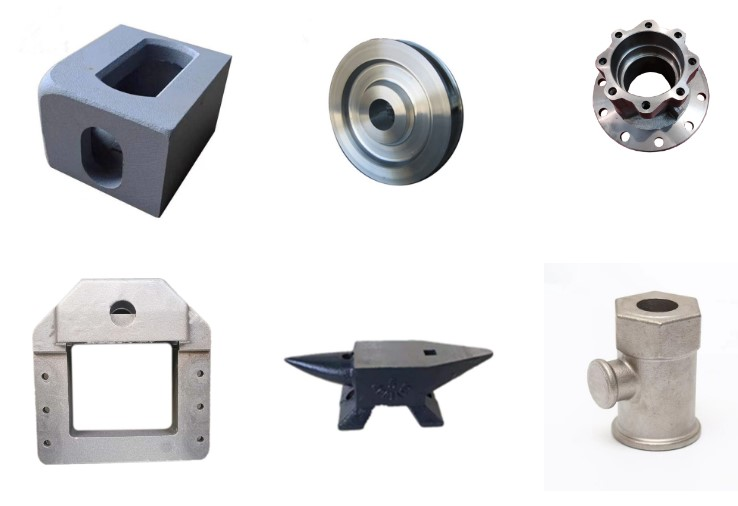
Carbon steel is a versatile material that can be used in various applications. It can be easily machined, welded, and formed to meet specific design requirements. It has beneficial mechanical properties such as high tensile strength, toughness, and wear resistance.
Carbon steel is a common low-cost material compared to other alloys, such as stainless steel or titanium. It is readily available and easily sourced, making it a cost-effective option for investment casting.
Although carbon steel is not as corrosion-resistant as other alloys, it can still be treated to improve its corrosion resistance. For instance, surface coatings or plating can be applied to protect the surface of the carbon steel from corrosion.
Stainless Steel
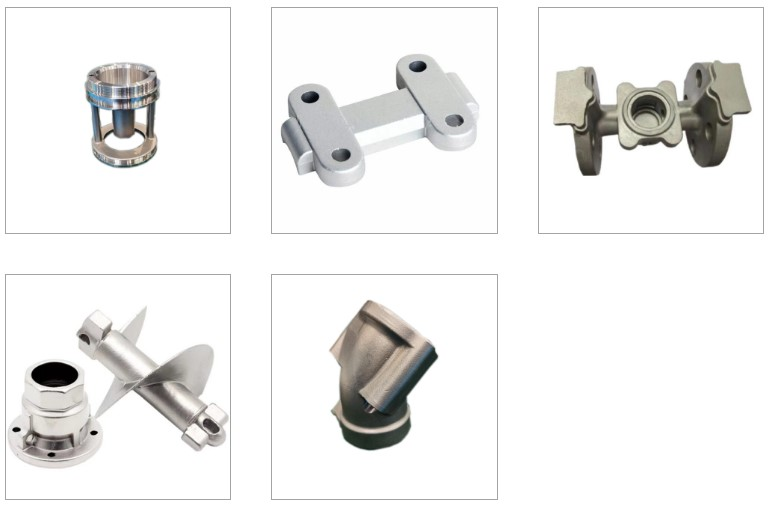
Stainless steels are high-strength alloy steels that can be used for different applications. It has a high tensile strength, which means it can withstand heavy loads and pressure without deforming or breaking.
As cast steel, it features a corrosion-resistant material that can withstand exposure to harsh environments. This resistance is due to chromium, which forms a protective oxide layer on the surface of the steel.
Stainless steel is also durable and can withstand wear and tear over time. It is also resistant to high temperatures, making it suitable for use in applications that involve heat.
Aluminum Alloy
Aluminum is lightweight, making it ideal for applications where weight is a critical factor. It has a high strength-to-weight ratio, which is strong relative to its weight. Aluminum investment casting is ideal for applications where strength is essential, but weight needs to be minimized.
Aluminum is ductile. It can be easily formed into a variety of shapes and sizes. This property makes it ideal for investment casting, where complex shapes and thin-walled sections can be easily produced.
Ductile Iron
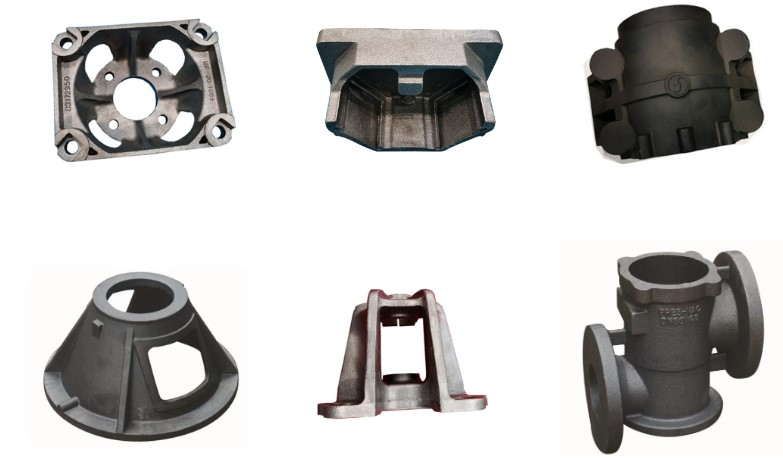
Ductile iron is a cast iron that features a ductile material. Meaning it can be easily formed into a variety of shapes and sizes. It also features high tensile strength, making it suitable for applications that require high strength and durability.
Because it is a machinable material, it can be easily cut, drilled, and shaped. This property makes it ideal for use in applications requiring precision machining.
Copper-Based Alloys
Copper-based alloys are a group of materials made primarily of copper with the addition of one or more other elements, such as zinc, tin, aluminum, nickel, or silicon. These elements can significantly alter copper’s physical and mechanical properties, making it suitable for a wide range of applications.
Beryllium copper is the strongest copper alloy with properties similar to stainless steel, which also offers high corrosion resistance.
These alloys have high electrical conductivity, making them ideal for electrical components and wiring use. It also features high malleability, easily forming into various shapes and sizes.
Considerations When Selecting The Correct Casting Material
Tensile Strength
Tensile strength is essential when selecting the suitable investment casting material because it determines the maximum stress a material can withstand before it breaks.
If the material has insufficient tensile strength, it may not be able to withstand the loads and stresses that the product will be subjected to, resulting in product failure.
For example, investment casting is commonly used in the automotive industry to produce parts such as engine blocks, cylinder heads, and transmission components. These parts are subjected to high loads and stresses, and the material selected must have the sufficient tensile strength to withstand these conditions.
Corrosion Resistance
Superior corrosion resistance is an important consideration when selecting the suitable investment casting material because it determines its ability to resist damage and degradation due to exposure to harsh environments or corrosive substances.
Investment casting produces parts such as valves, pumps, and fittings exposed to corrosive chemicals in the chemical industry. If a material with insufficient resistance to corrosion was used, the parts could corrode and fail, leading to potential safety hazards and environmental damage.
Heat Resistance
Investment casting materials with high heat resistance can withstand extreme temperatures without undergoing significant changes in their mechanical properties. This is important because exposure to high temperatures can cause materials to expand or contract, resulting in the part’s deformation or failure.
Hardness
The hardness of the material used in investment casting can affect the performance and durability of the final product. Investment casting materials with high hardness can resist wear and deformation caused by abrasive forces, impact, and other stresses. This is important because parts subject to wear and deformation may have a shorter lifespan or require more frequent maintenance.
Why Should You Choose The Correct Investment Casting Materials
Choosing the correct investment casting materials is crucial for the success of your investment casting process. The properties of the investment casting materials you use can significantly affect the quality of the final product. Some investment casting materials can have a significant impact on the environment. Choosing suitable materials can help reduce waste and minimize the environmental impact of the investment casting process.