The casting process is used in many industries to create objects from various materials. It involves pouring molten metal into a mold and allowing it to cool and take shape. There are a number of different metal casting techniques available, each with its own advantages and drawbacks.
In this article, we will explore the 9 different types of casting techniques and discuss the best applications for each. We will explain the process of each technique and provide some examples of products that have been created through the casting process.
Importance of the Casting Process
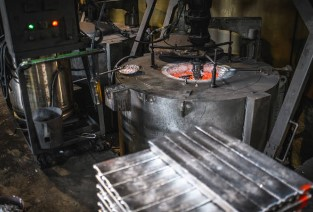
The casting process is very important for maintaining the quality of the solid metal castings being produced. The metal mold casting used is made with precise measurements, allowing for exact replication of the part being cast. Additionally, the mold cavity can be made of a variety of materials, which can affect the strength and durability of the part.
It begins with the creation of a mold cavity, which is used to cast the molten metal into the desired shape. This pattern is usually made from wood, plastic, or metal. Once the pattern is completed, it is placed in a mold and filled with molten metal at high temperatures.
Different Types of Metal Casting Methods
Choosing the best type of metal casting method can be a difficult decision. There are different factors to consider such as material, cost, precision, and difficulty of casting processes.
Lost foam casting process
Lost foam casting is a process that utilizes polystyrene foam to create metal castings. It is a type of evaporative-pattern casting process, which uses a foam pattern that is placed in a flask and covered with a refractory material.
The foam pattern is then heated, causing the foam to evaporate and leave a void in the refractory material. The molten metal is then poured into the void and allowed to cool, resulting in a metal casting with near-net shape characteristics.
Investment casting or Lost Wax Casting Process
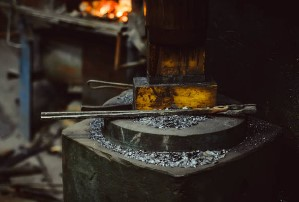
The investment casting process begins with the creation of a wax pattern of the desired part. This pattern is made in a 2-piece mold and is then coated in refractory material.
This process, also known as precision casting or lost wax casting, is used to make components for a variety of industries, from aerospace and automotive to medical and consumer products.
Sand casting
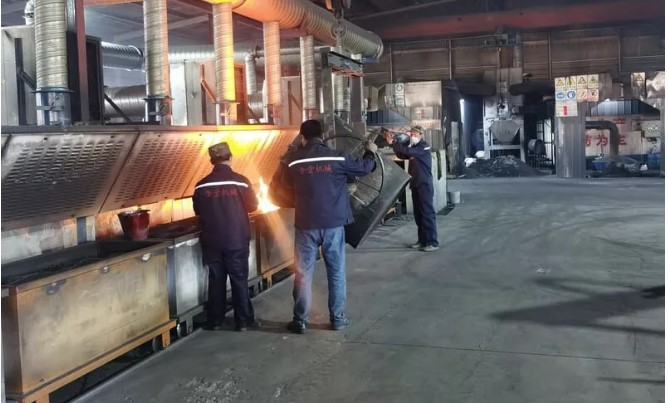
Sand casting is one of the oldest and most established metal casting methods in history. The process involves pouring molten metal into a sand mold, which is then allowed to solidify and cool.
The sand casting process begins with the creation of sand molds, which typically consist of a two-part sand and clay mixture. This mixture is usually composed of a finer grade of sand for the core, and a coarser grade of sand for the outer layer, or cope.
Permanent mold casting
Permanent mold casting is similar to die casting, except that the molds are made from steel, cast iron, or graphite. The metal mold is designed to produce a high-quality, repeatable part, and many of the molds can produce thousands of parts before they need to be replaced.
The molds are heated to a specific temperature before the liquid metal is poured into them. The temperature of the molds is crucial, as it affects the properties of the final parts.
The permanent mold casting process is often used for parts that require high precision and repeatability. It is also used for applications where the parts need to be heat-treated, has a high level of corrosion resistance, or in producing hollow castings.
Centrifugal casting
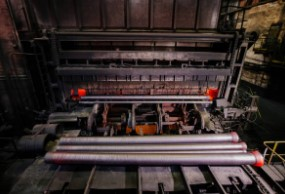
Centrifugal Casting is a metal casting process that uses centrifugal force to form cylindrical components. The centrifugal casting process begins with the pouring of molten metal into a rotating mold.
The vertical centrifugal casting process begins by placing a mold in a centrifuge and spinning it at a high speed. Molten metal is then poured into the mold, and the centrifugal force imparted by the spinning forces the metal to fill the mold cavity in a controlled and even manner.
Semi centrifugal casting process is a relatively new casting technology and innovative manufacturing process that has been developed to fill a gap in the metal casting industry. It is a recommended process for producing sleeve composite metal castings, pipes, or cylinders.
Die casting Process
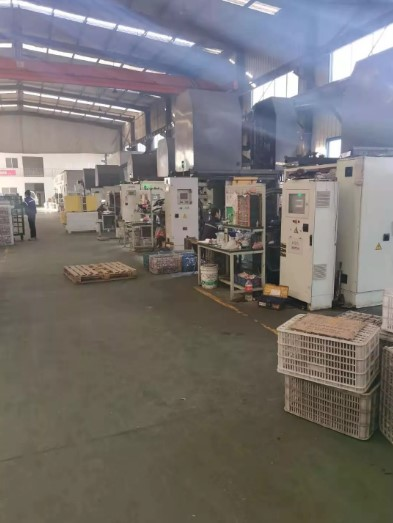
The die-casting production begins with the creation of a die or mold. The die is then placed into a die-casting machine, which is filled with molten metal such as aluminum, zinc, or magnesium. The die is then injected with molten metal, which takes on the shape of the die-casting parts.
In gravity die casting, the die is held in a vertical orientation and the molten metal is poured into the die’s cavity. Due to the force of gravity, the molten metal flows into all of the intricacies of the die and solidifies as it cools.
In low-pressure die casting, the molten metal is then forced into the die cavity using a low-pressure injection system. The die cavity is created by a die mold, which is made from an alloy or steel.
In high-pressure die casting, the die is heated to the proper temperature and filled with liquid metal. The die is pressurized with hydraulic force, pushing the liquid metal into the die cavity.
Continuous casting
Continuous casting is commonly used in the large-scale production of industrial components, such as railway tracks, steel pipes, and automotive parts. The process begins with the melting of the metal in a furnace, where it is then poured into a water-cooled mold cavity.
As the molten metal passes through the mold, it is solidified into a continuous strand. This strand is then passed through a series of rollers that help shape and refine the metal castings.
Vacuum Die Casting Method
The vacuum die-casting process uses a die-casting machine to inject molten metal into a die under vacuum conditions. The die is made from a hard material such as steel or aluminum and has a cavity with a precise shape. This mold cavity is filled with molten metal, usually, aluminum or zinc alloys injected into the cavity under vacuum conditions.
Squeezing die-casting
Squeeze Die Casting is a metal casting method used to produce parts with intricate shapes. It is a type of die-casting process where molten metal is forced into a die cavity at high pressure.
The process involves two halves of a precision metal mold cavity being closed together with the metal placed in between.
Advantages of Different Types of Casting Process
Lost foam casting process
Because the foam casting pattern is not destroyed in the casting process, it can be reused multiple times, providing low production costs. It can also produce castings without a sand core.
Investment casting
Investment casting is a versatile process that can be used to produce parts from a wide range of materials. The process is well-suited to producing parts made from non-ferrous metals, stainless steel, and titanium.
Sand casting
Sand casting can be used to quickly produce a wide variety of parts and components. The process allows for the production of complex shapes and intricate details that would be difficult to replicate with other methods.
Permanent mold casting
Permanent mold casting offers extremely high precision compared to other casting processes. The molds used in this process are designed to last for many years, providing a long-term solution for metal casting needs.
Centrifugal casting
The centrifugal casting process can produce parts with a high degree of accuracy and consistency with almost no metal consumption. This is because the force of the centrifugal force creates a uniform rate of solidification. This means that the end product is much more resistant to casting cracks, warping, and other issues that can occur during the manufacturing process.
Die casting
Die-casting molds are highly precise, allowing for parts with tight tolerances and smooth surface quality. It requires minimal raw materials and is a relatively inexpensive process. The process is also relatively easy to set up and requires minimal manual labor. This makes it ideal for high-volume production runs.
Continuous casting
This process reduces the risk of injury due to the use of automated systems. Workers are able to work from a safe distance from the molten metal and no longer need to be in direct contact with the hot material. This reduces the risk of burns and other injuries.
Vacuum die casting
Vacuum casting reduces the amount of scrap created during production. This is because the process is much more efficient and accurate, resulting in fewer errors and less scrap material.
Squeezing die-casting process
This process is capable of producing intricate parts with thin walls and tight tolerances. This process also increases production speed by allowing for faster cooling times and eliminates the need for secondary operations, such as trimming and grinding.
Disadvantages of Different Types of Casting Process
Lost foam casting process
The foam pattern material can be difficult to handle and the process is not suitable for producing parts larger than a few inches in size. Additionally, the process is not suitable for producing parts with intricate details, such as fine threads or sharp edges.
Investment casting
Using investment casting takes time to complete the process. The wax pattern must be created and then allowed to cool and harden. This step alone can take several days, and the entire process can often take weeks. This can be a major deterrent for companies that need to produce components quickly.
Sand Casting
Sand casting is prone to defects due to the nature of the process. The sand molds used in the process are vulnerable to wear and tear, and the high temperatures involved in the process can cause the metal to become brittle, leading to defects in the finished product. In addition, the sand molds can become contaminated, resulting in an impure product.
Permanent Mold Casting
The design of the mold is a limiting factor in the permanent mold casting process, as changes in design can be difficult and costly. This can be a problem for companies that need to incorporate frequent design changes into their production process.
Centrifugal casting
Centrifugal casting requires a higher degree of skill and experience than other casting techniques. This can make it difficult for those without experience to use and can also lead to higher costs due to the need for skilled labor.
Die casting
Porosity is an issue with die-cast parts and can lead to components that are weaker than expected. This is because the molten metal can become trapped in tiny cavities in the tooling, resulting in weak points.
Continuous casting
Continuous casting produces a large amount of waste. This is because the process involves the removal of extra metal from the casting. This waste is often discarded and can result in significant environmental pollution.
Vacuum die casting
The vacuum die-casting process is expensive due to the complicated machinery and high-pressure environment that are used. The process can also create inconsistencies in the size, shape, and surface finish of the parts.
Squeezing die-casting process
A major disadvantage of squeeze die casting is that it is a relatively expensive process. The tooling, setup, and maintenance costs associated with this type of casting process can add up quickly.
Frequently Asked Questions
How to choose the best casting method to pour molten metal?
The best casting method to pour molten metal depends on the desired end product. A lot of factors are needed to consider, so important to consult with a foundry expert to ensure the best casting method is chosen for the project.
Which has the cheapest production costs?
The sand casting process is relatively inexpensive compared to other casting methods because sand is a plentiful and relatively inexpensive material. Additionally, the cost of sand casting is kept low due to the minimal tooling and equipment required for the process.