Malleable iron is a form of iron that has been treated to become more ductile and resistant to breaking. It has a range of mechanical properties that make it suitable for a variety of applications.
It is a cast steel that undergoes annealing heat treatment to produce the desired malleable form. Malleable iron is commonly used to manufacture parts for electrical fittings, tools, pipe fittings, and other applications that require strength and durability.
What is Malleable Iron
Generally, malleable iron is a white cast iron that has been treated through a process known as annealing. The annealing process involves heating the cast iron to a specific temperature and cooling it slowly. The process forms temper carbon nodules, resulting in better ductility than regular cast iron.
Producing malleable and ductile iron is similar, but malleable cast irons are only made for small castings. The process of creating malleable iron starts with producing white iron casting. This is done by melting iron ore and other materials in a furnace and pouring them into a mold. The material then solidifies and is allowed to cool.
Iron carbide plays a critical role in the production of malleable cast iron. Once the cast iron has cooled, it is heated to a very high temperature in a process known as annealing. The heat treatment removes excess carbon from the cast iron, making it more malleable and ductile. Unlike grey cast iron, it can be bent, twisted, and hammered into various shapes without breaking.
Elements That Malleable Cast Iron Consists
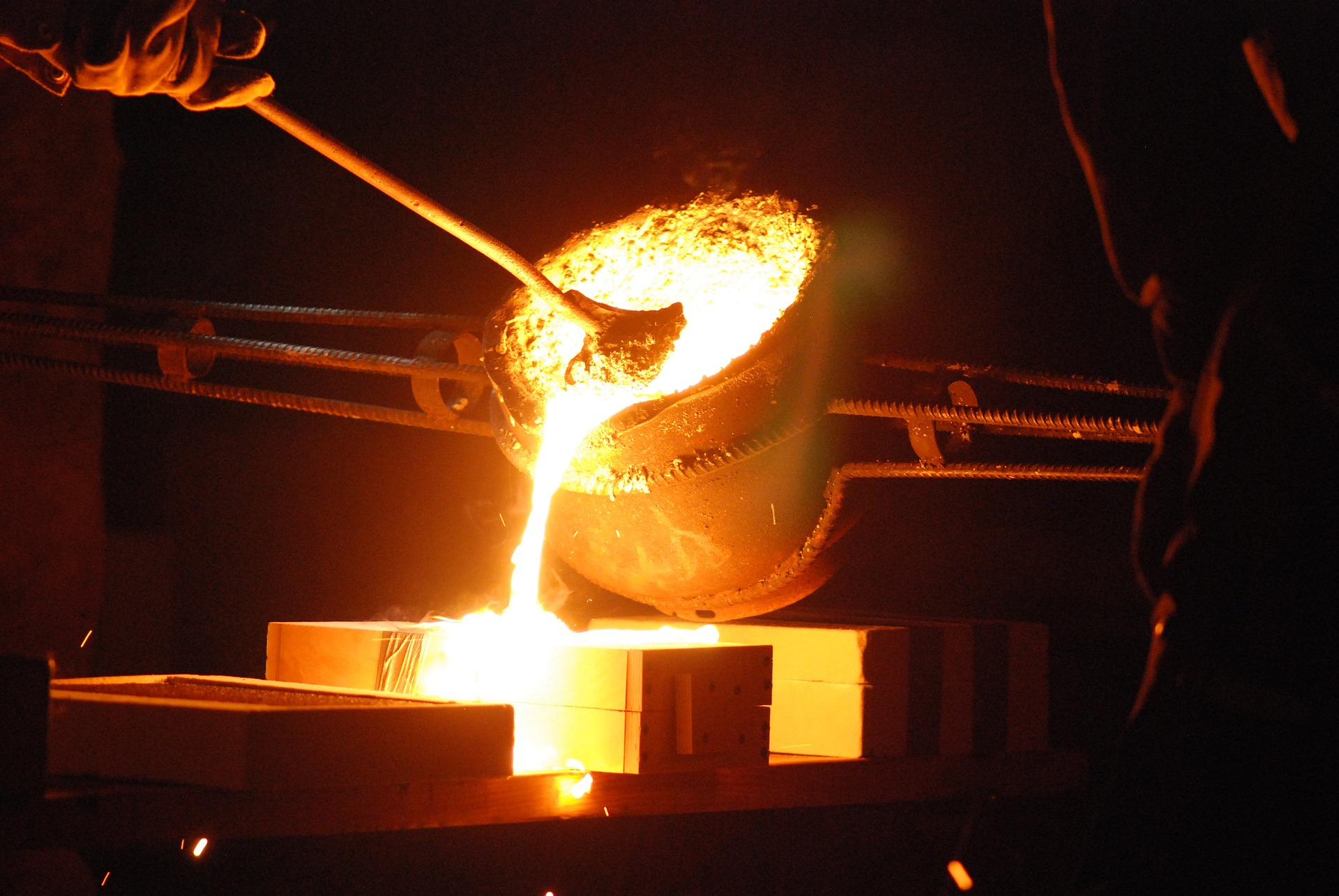
Iron is the primary element that makes up malleable cast iron. Iron is a naturally occurring element found in many forms, including iron ore. During the manufacturing process in malleable iron foundries, iron is melted down and mixed with other elements to change its chemical composition and create the malleable iron used for the iron casting parts.
Carbon is an element responsible for the strength and durability of malleable cast iron. The carbon content of iron is typically around 2.0-4.0%, although this can vary depending on the specific application. A low-carbon metallic matrix will result in weaker malleable cast iron fittings.
When manufacturing malleable cast iron, the amount of silicon in the material is carefully controlled. Too much silicon can create a brittle structure, while too little can reduce strength and durability. The right balance must be found to create malleable iron castings that possess considerable ductility.
Manganese also plays an important role in tempering malleable cast iron. When malleable cast irons are heat treated, the manganese forms a ferritic malleable iron that is both strong and malleable. This process also helps to increase the wear and corrosion resistance of the iron.
Types of Malleable Iron
Malleable iron has a variety of applications and is a popular choice for many projects. While some types may be more expensive than others, there is a type of malleable iron that can meet most needs.
Whiteheart malleable cast iron
The microstructure of Whiteheart malleable iron is composed of two main types of iron: pearlite and ferrite. The pearlite consists of flake-like layers of iron carbide and ferrite, and the ferrite is composed of tiny grains of pure iron.
The pearlite layers provide strength and hardness, while the ferrite grains provide toughness and ductility. Additionally, the ferrite or pearlite matrix gives the metal a high degree of machinability, allowing for intricate parts to be easily created.
Blackheart malleable cast iron
The microstructure of blackheart malleable iron is composed of a combination of spherical or nodular shapes of graphite and ferrite. Graphite is a form of carbon responsible for providing the metal with shock and wear resistance.
Its flake graphite is embedded within the ferrite, a type of iron that gives the metal strength and rigidity. The graphite particles are usually irregular in shape and are distributed in a matrix-like pattern within the ferrite. The particles are typically small and randomly distributed, giving the metal a homogeneous structure.
Pearlitic Malleable Iron
Pearlitic malleable cast iron is a type of cast iron that is known for its strength and high-temperature stability. It is made by slowly cooling molten iron with a specific carbon content, which forms a pearlite microstructure.
The microstructure of Pearlitic Malleable Cast Iron is composed of two interlaced phases, ferrite, and cementite. Ferrite is the base material, which consists of a lattice of iron atoms, and is relatively soft and ductile. Cementite is a hard and brittle form of carbon produced during cooling. A permanent deformation occurs if there is an absence of alternating layers of ferrite and cementite.
Properties of Malleable Cast Iron
Malleable cast iron is a type of cast iron that is strong and tough yet malleable or easy to shape or mold.
Tensile Strength
Malleable cast iron has a high tensile strength, making it suitable for applications requiring ultimate tensile strength. Malleable cast iron has a higher tensile strength than other types of cast iron, such as gray cast iron or ductile iron alloys. This is due to the addition of carbon to the alloy.
The carbon helps to increase the strength of the iron, allowing it to withstand higher levels of force before it breaks. The tensile strength of malleable cast iron can range from 30,000 psi to 70,000 psi. Its ultimate tensile strengths vary on the type of alloy used.
Resistance to Stress
The yield stress of malleable cast iron is affected by several factors. The alloy composition affects the hardness of the material, which in turn affects its tensile and compressive stress. The manufacturing process affects the grain size of the microstructure, which also affects its maximum stress.
The heat treatment and slow cooling process of malleable cast irons cause the iron to form small graphite flakes. It creates a more ductile and malleable microstructure than other cast iron types. The increased carbon content also increases the material’s strength, making it highly resistant to yield stress.
Uses of Malleable Cast Irons
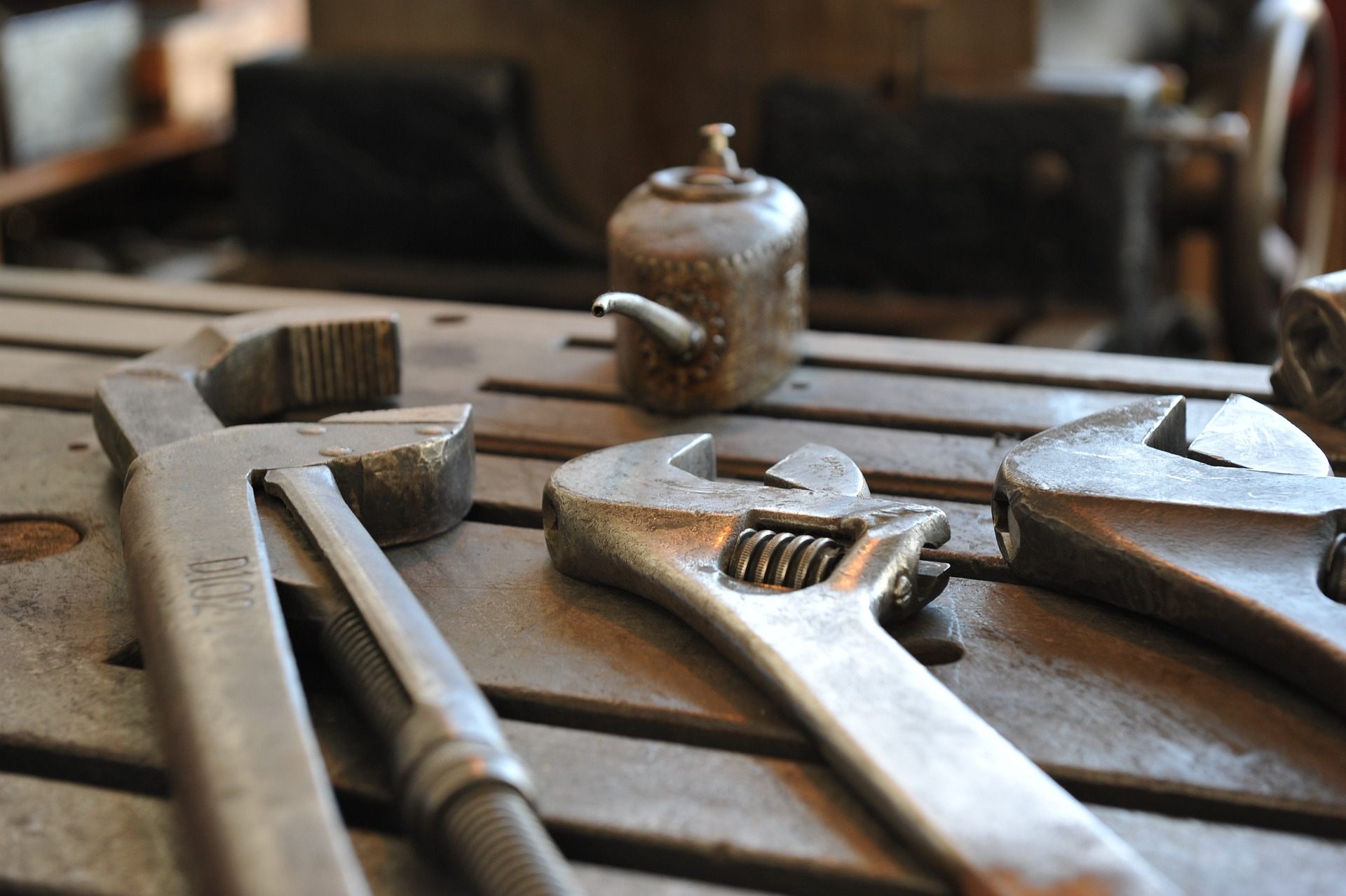
Tools
Malleable cast iron is often used to create tools, such as hand tools, screwdrivers, wrenches, and other types of tooling. This is due to its malleability, as it can be formed into various shapes and sizes without losing strength or durability.
It is also relatively lightweight, making it easy to handle and transport. Malleable cast iron is also very easy to work with, as it can be machined, formed, drilled, and tapped. This makes it ideal for the production of complex tool designs. Additionally, it is relatively easy to weld and can be painted or coated for added protection.
Rear Axle Housing Castings
Rear axle housing castings can be made from malleable cast iron for various reasons. First, it is well-suited for applications that require excellent strength and wear resistance. This is because malleable cast iron is a tough material with a hardness of around 500 Brinell.
It is ideal for applications that require strength and durability, such as those found in heavy-duty vehicles, farm equipment, and construction equipment.
Pipe Fittings
Malleable cast iron is ideal for producing pipe fittings exposed to water and other corrosive materials. It is commonly used to produce pipe fittings for water, gas, and other plumbing systems.
It is preferred for pipe fittings because it is strong, durable, and corrosion-resistant. It is also relatively easy to cast and machine, making it a cost-effective choice.