Stainless steel consists of iron, chromium, and other elements such as nickel, molybdenum, and nitrogen. In stainless steel, the chromium content serves as the passive layer of protection for better mechanical qualities of steel and corrosion resistance.
Stainless steel comes in many grades, identified by the American Iron and Steel Institute. The British Stainless Steel Association guides the appropriate specifications of each grade.
It can be used for surgical and dental instruments, food processing equipment, or construction.
Stainless Steel Production
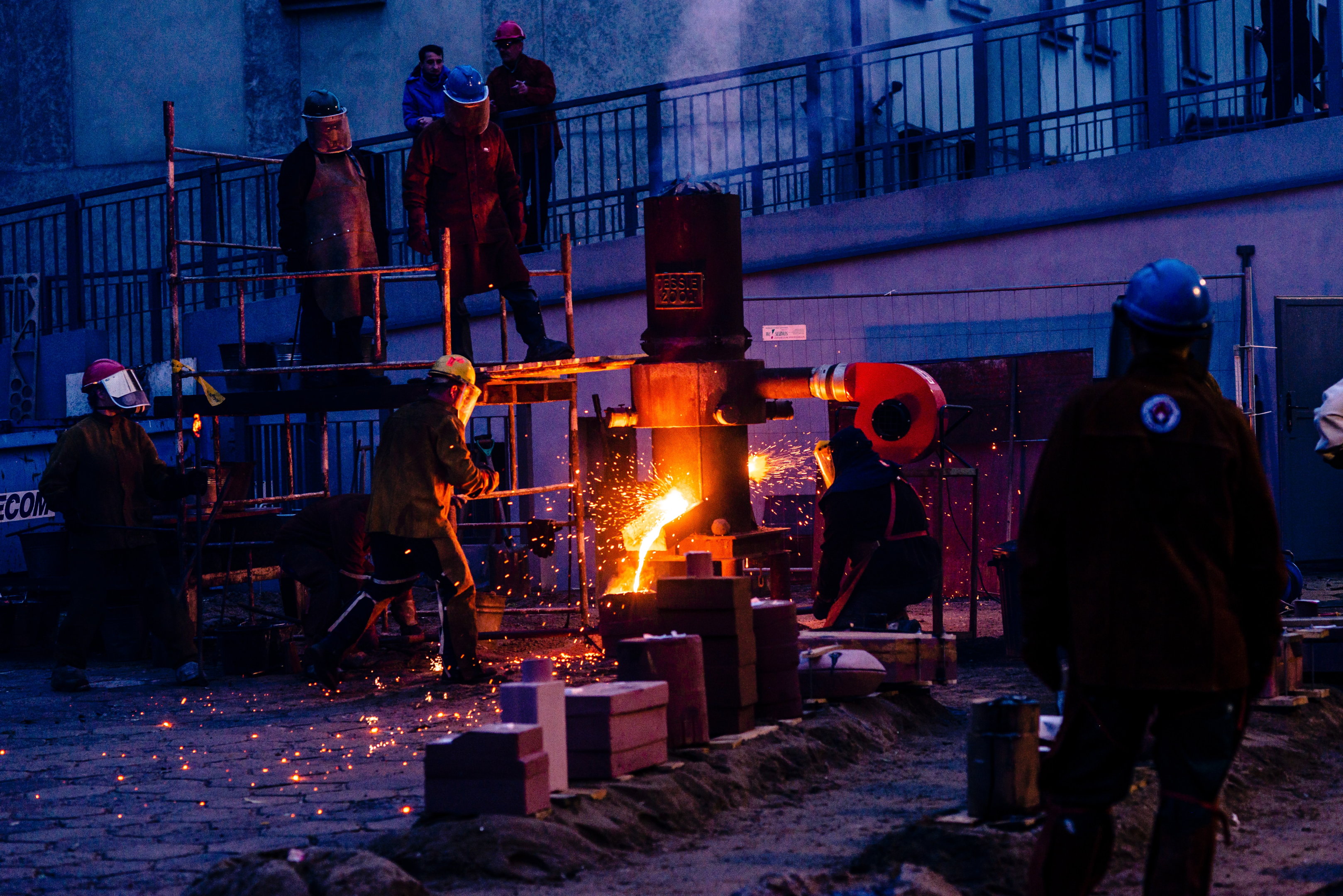
Stainless steel is produced through the “melting and casting” or “smelting” process. The raw materials are melted in an electric arc or induction furnace. The furnace is heated to a high temperature, and the raw materials are added to the furnace in the required proportions.
The melted raw materials are refined to remove impurities such as sulfur, phosphorus, and excess carbon. This process is done by adding alloying elements such as oxygen, nitrogen, and argon, which react with the impurities and remove them from the molten metal.
Once the refining process is complete, the molten steel is poured into a casting mold. The mold is typically made of sand or ceramic and is designed to create the desired shapes and sizes of stainless steel products.
It is heat treated to a specific temperature and then slowly cooling it. Stainless steels are finished by cutting, polishing, or coating. These stainless steel finishes improve its appearance or further enhance its properties.
Stainless Steel Grades
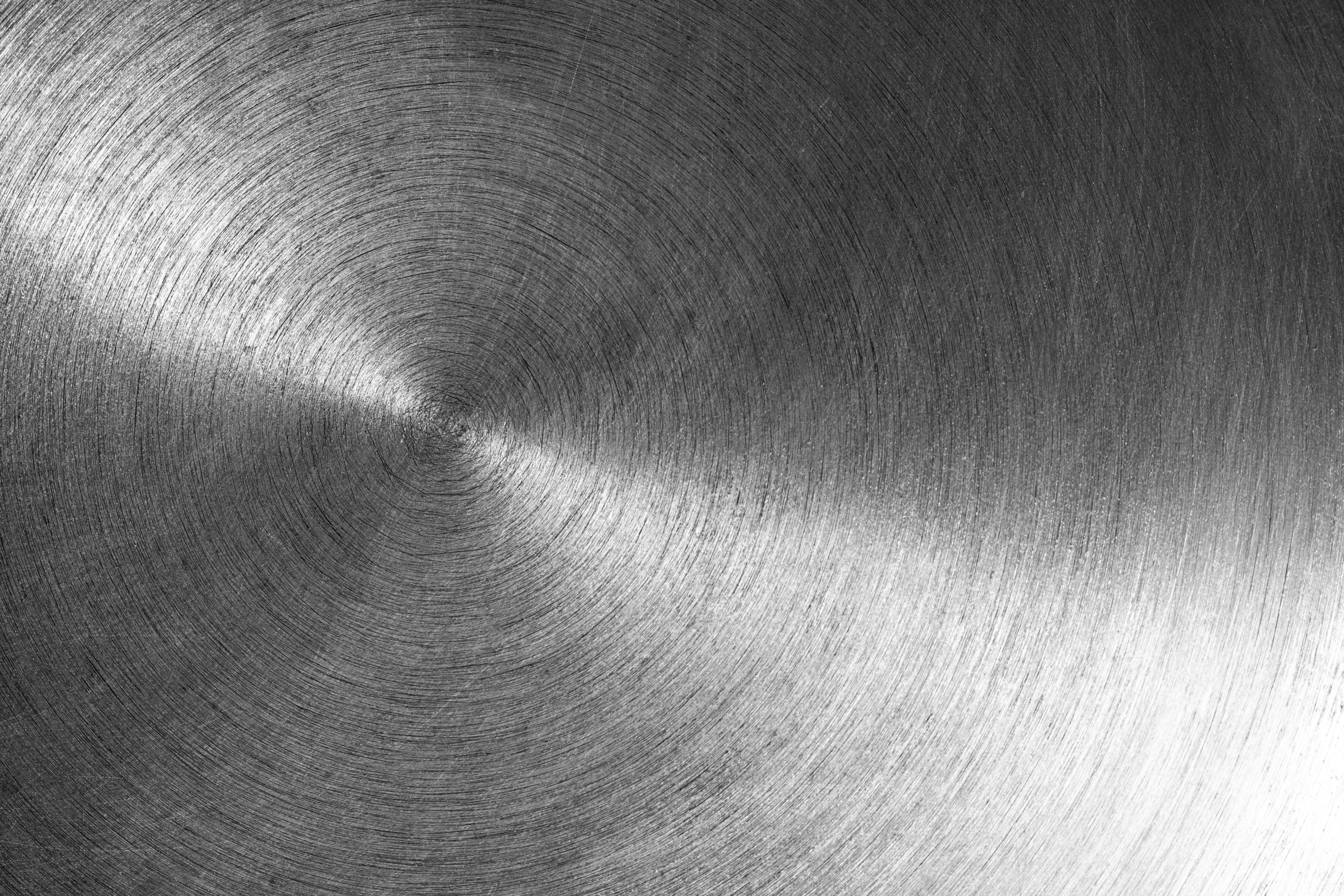
Stainless steel grade compositions are different from one another. Due to this, each grade has its own microstructure and distinct mechanical properties for its intended application.
Austenitic Stainless Steels
The chromium content in the austenitic steels creates a passive layer on the material’s surface that protects it from environmental factors, while the molybdenum improves corrosion resistance.
These steels retain their strength even at high temperatures, which makes them suitable for use in high-temperature applications such as furnace parts, heat exchangers, and exhaust systems.
Ferritic Stainless Steel
The distinctive properties of ferritic stainless steels are excellent ductility, corrosion resistance, and magnetic characteristics.
Aside from nickel, it slow carbon content of ferritic stainless steel makes them less susceptible to intergranular corrosion. This grade can resist stress corrosion cracking, especially on applications that withstand extreme temperatures.
Martensitic Stainless Steel
The high levels of carbon and chromium makes this stainless steel grade distinctive than the other grades. These elements make martensitic stainless steels attractive to consumers because it brings durability and provides excellent corrosion resistance properties.
It can also be hardened by heat treatment. Manufacturers heat the steel under elevated temperatures and then rapidly cool it for better durability.
Duplex Stainless Steel
Compared to austenitic stainless steel,duplex stainless steels has low nickel. Therefore, it less expensive to produce.
Duplex stainless steel can be difficult to fabricate due to its two-phase microstructure and high strength. Welding can be particularly challenging, as it requires carefully selecting welding parameters and filler materials to ensure a strong and corrosion-resistant joint.
The common stainless steel used under this grade is marine engineering.
Precipitation-Hardening Stainless Steels
The chromium, nickel, and small amounts of copper, aluminum, and titanium differentiates this grade to others. These elements promote the formation of precipitates, which can be further strengthened by applying heat treatment methods.
The strength and hardness of precipitation-hardening stainless steel can be adjusted by varying the heat treatment parameters, such as the temperature, time, and cooling rate. This allows for a high degree of flexibility in the design of components, as the material can be tailored to meet specific performance requirements.
Stainless Steel Properties
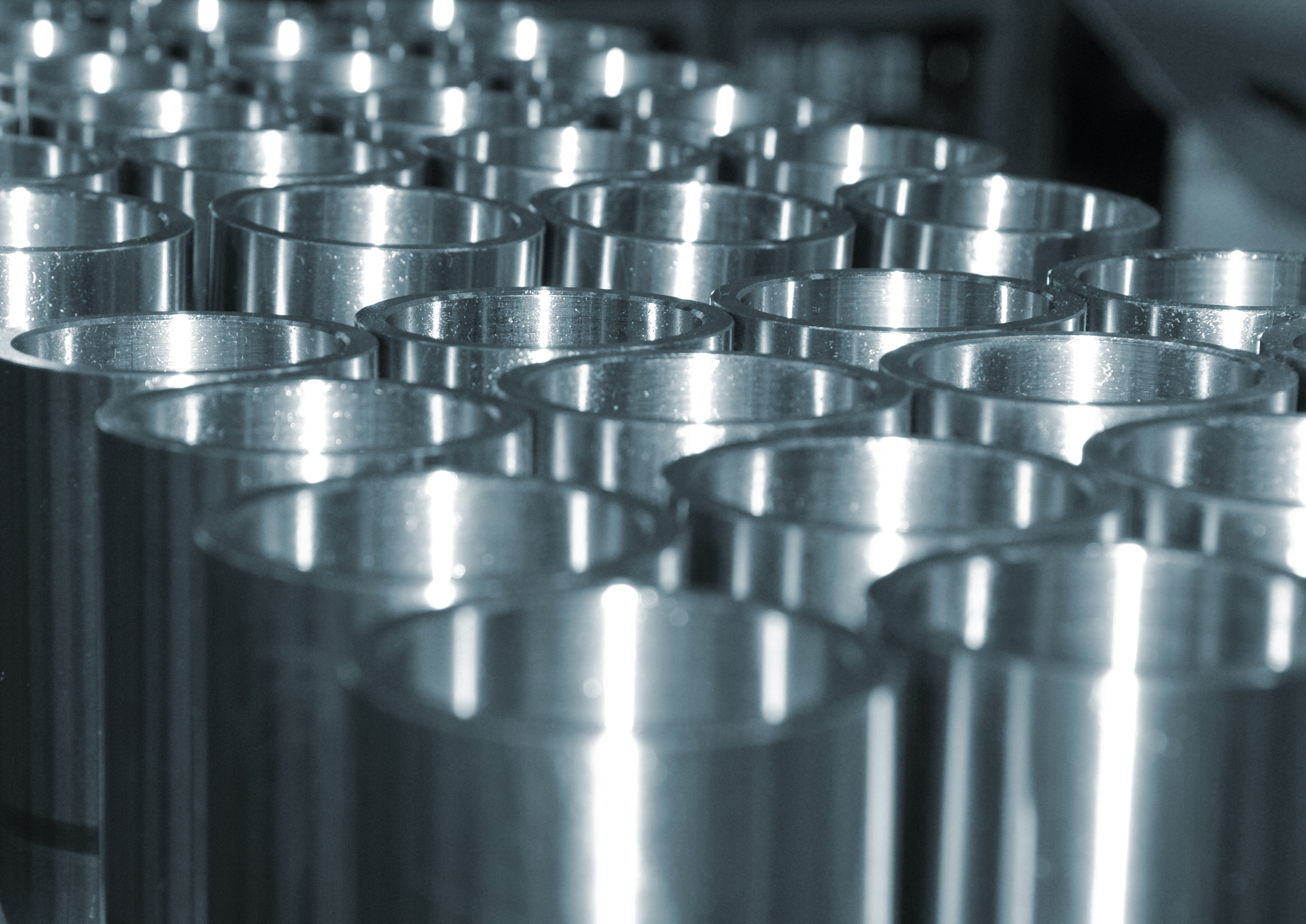
Excellent Corrosion Resistance
Corrosion resistance is the ability of a material to resist corrosion or degradation when exposed to various environmental factors such as moisture, chemicals, and atmospheric gases.
Its passive layer helps to protect the underlying stainless steel material from further corrosion.
In contrast to aluminum, which can be prone to pitting corrosion in these environments, stainless steel is more resistant due to its chemical composition which are added with other alloying elements.
Heat Resistance
Stainless steel’s ability to withstand high temperatures stems from a special equilibrium between its elements, crystal structure, and manufacturing processes. Its chromium content is self-renewing, which will reform if damaged, further enhancing the steel’s heat resistance properties.
The additional alloying elements can help stabilize the steel’s crystal structure at high temperatures and enhance its mechanical properties, such as strength and toughness.
Oxidation Resistance
The thickness and quality of the oxide layer are critical to the oxidation resistance of stainless steel. If the layer is damaged or contaminated, it can become ineffective and lead to corrosion. However, the oxide layer is self-renewing, which means it can repair itself if damaged or removed.
Nickel, molybdenum, and nitrogen help to stabilize the oxide layer, making it more effective at protecting the underlying metal from further oxidation.
Creep Resistance
The crystal structure of stainless steel is essential for its creep resistance. Stainless steel is composed of a crystalline structure arranged in a pattern of cubic or hexagonal shapes. The crystal structure can be modified by adding alloying elements such as molybdenum, vanadium, or tungsten, stabilizing the crystal structure at high temperatures.
Stainless steel can be heat-treated to produce a fine-grained microstructure, which can improve its creep resistance by increasing its resistance to deformation.
High Wear Resistance
The surface finish of stainless steel is critical for its wear resistance. A smooth and polished surface can reduce friction and abrasion, which helps to prevent wear and damage. This is particularly important in applications where the stainless steel is exposed to sliding or rubbing against other materials.
Uses of Stainless Steel in Different Industries
Medical Equipment
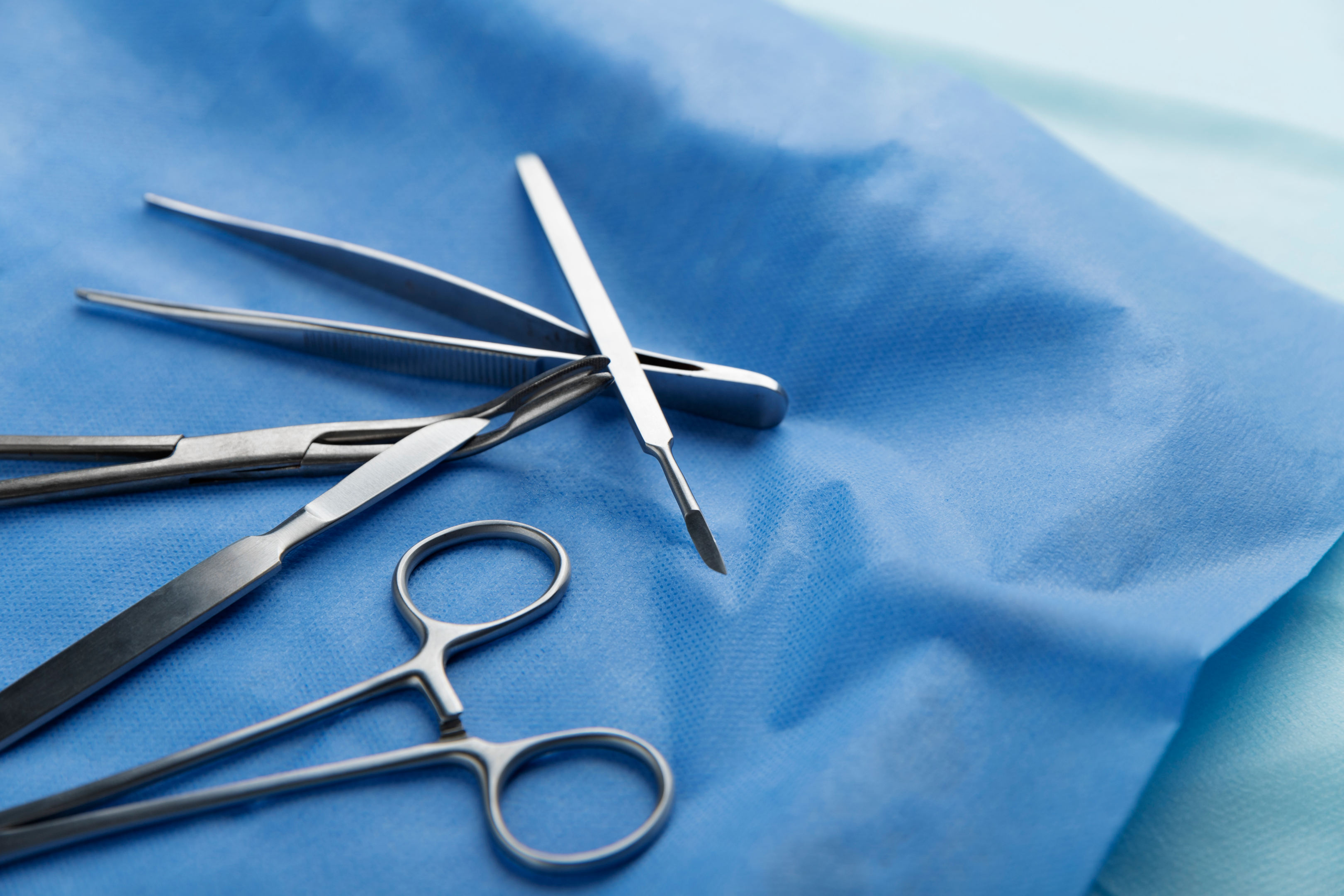
Medical technology stainless steel is biocompatible, meaning it does not cause adverse reactions in the body. It is non-toxic, non-allergenic, and can be sterilized without damaging its properties. This makes it a suitable material for medical implants, such as pacemakers, stents, and orthopedic implants.
Traditional and Marine Constructions
Stainless steel is highly corrosion resistant, making it an excellent choice for construction applications in harsh environments.
In addition, it has an appealing and contemporary appearance, which is one of the reasons why it is such a popular option for architectural and ornamental applications in conventional building construction. It can be polished, brushed, or colored to create various finishes and designs.
Structural Components
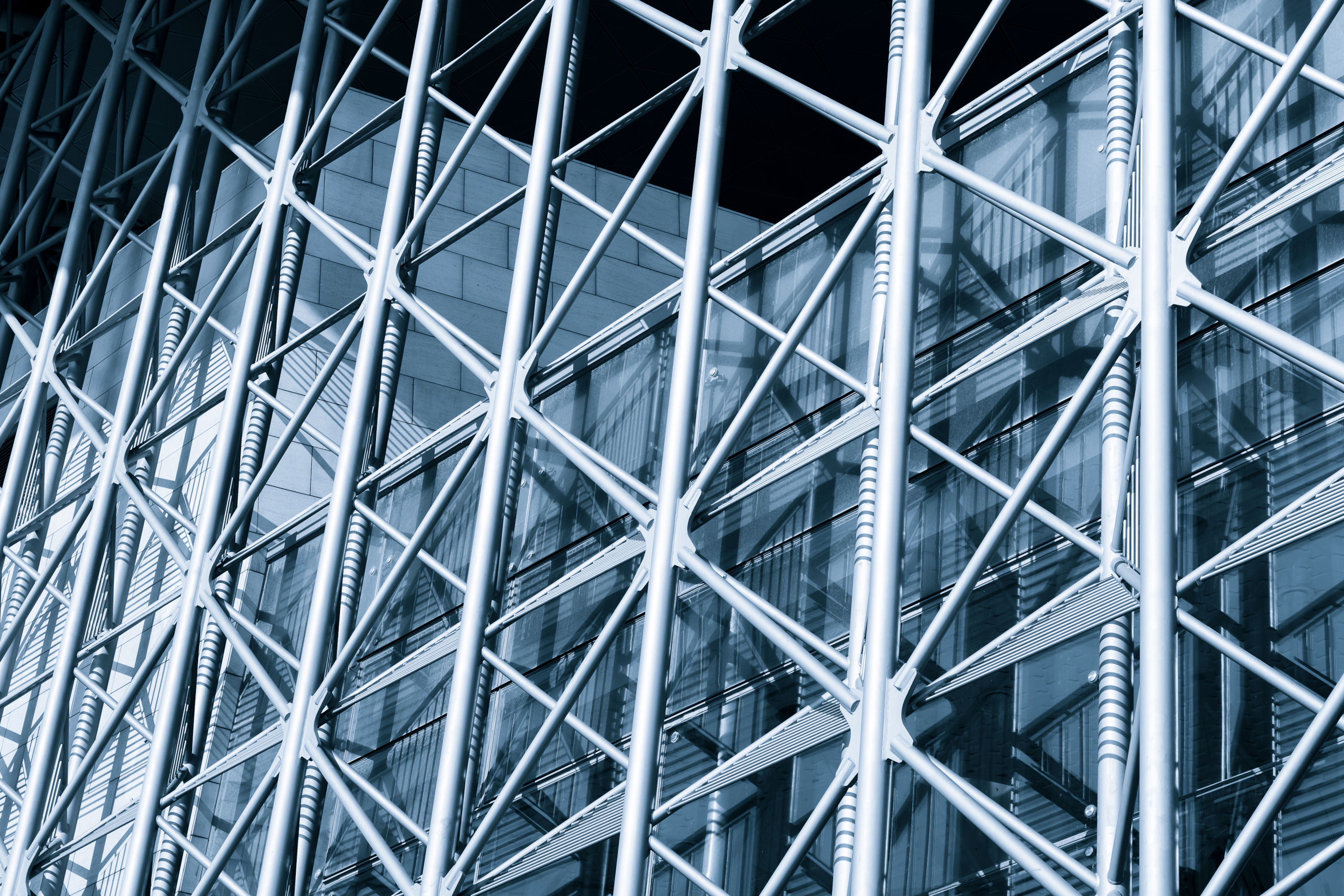
Stainless steel is a sustainable and environmentally friendly material for structural components due to its recyclability, durability, and low maintenance requirements. It is also energy-efficient, as it reflects heat and light, which reduces the need for cooling and lighting systems.
It also has excellent fire resistance properties, making it an ideal material for structural components that must withstand high temperatures and fire hazards.
Machine Parts
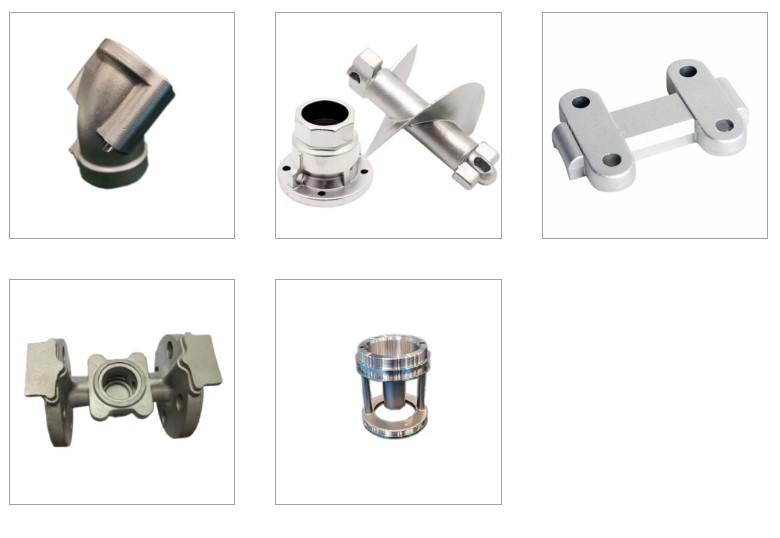
Stainless steel has excellent wear resistance properties, which makes it an ideal material for machine parts that experience high levels of friction or abrasion, such as bearings, gears, and cutting tools. Its mechanical properties also suit machine parts that withstand high loads and stresses.
Food Preparation Equipment
Stainless steels are attractive and modern, making them popular for food preparation equipment in commercial kitchens and food service environments. It is also easy to clean and sanitize, which makes it an ideal material for food preparation equipment that needs to meet strict hygiene standards.
It is also non-porous and does not harbor bacteria, making it a safe and hygienic choice for food contact surfaces.