The quality and performance of cast alloy steel components depend heavily on their precise specifications. The most crucial factor in choosing the correct alloy is knowing the exact specifications of the steel used. This includes the exact chemical composition, the mechanical properties, and the heat treatment.
Knowing the exact alloy composition ensures the steel has the desired engineering grades for the application. If the specifications are not met, the component may not perform as expected or fail prematurely, leading to costly repairs and even danger to those using it.
What is Cast Alloy Steel Castings
Cast alloy steel is an alloy of iron and other elements, such as chromium, nickel, and molybdenum, which are added to improve specific characteristics of the steel. Carbon and alloy steels can affect the steel’s tensile strength, ductility, and hardness. This range of properties must be considered when choosing the appropriate alloy steel for a certain application.
Like wrought steel, it is strong, durable, and can resist various environmental conditions. Additionally, it is relatively easy to work with and can be used to create complex shapes and designs.
The cost of cast alloy steel is typically higher than other cast iron. This is because it is more difficult to work with and is more expensive to manufacture. Additionally, it may require special machining and additional preparation to ensure the castings meet the required specifications.
Manufacturing Processes
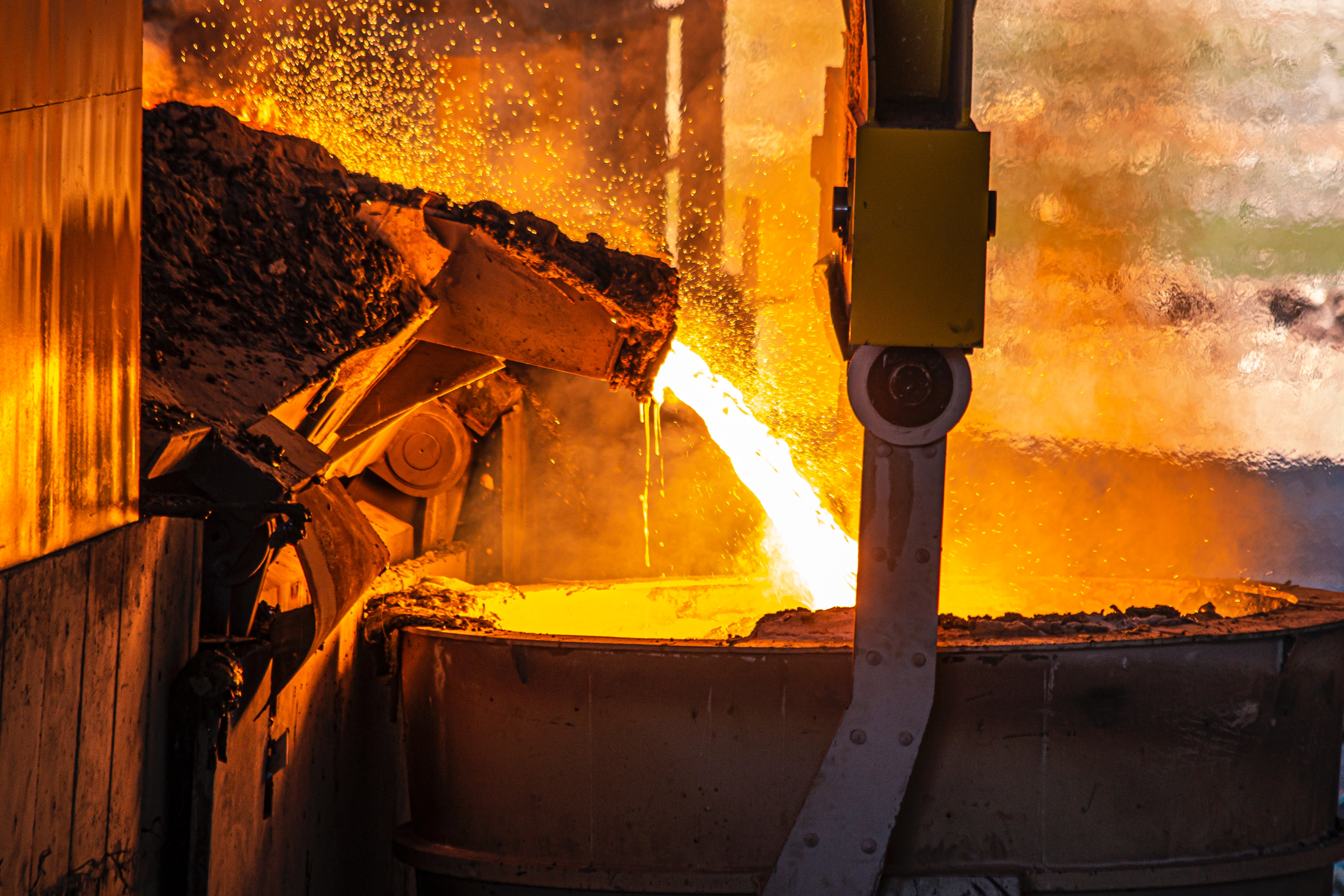
The first step in the process is the selection of iron ore and the various alloying elements that will be used to create the alloy steel. This is usually done by consulting with an experienced metallurgist or engineer who can determine the best combination of materials that will create the desired alloy. Once the raw materials are selected, they are melted in an electric arc furnace. The molten steel is mixed and cast into the desired shape.
The next step in the process is to heat treat the alloy. This is done by heating the alloy to high temperatures to harden it, improve its tensile properties, and have superior toughness. Different temperatures and times are used during the heat treatment depending on the type of alloy being produced.
Alloying Elements
Alloying elements are used to modify the characteristics of cast alloy steels. Alloying elements are added to steel to modify the properties of the metal, like strength, corrosion resistance, and heat resistance. The most commonly used alloying elements are chromium, nickel, molybdenum, and vanadium.
Chromium increases the hardness, wear resistance, and strength of the steel. It also helps to increase the corrosion resistance of the alloy. Chromium is often combined with other alloying elements, such as molybdenum and vanadium.
Nickel is also used to increase the strength and toughness of the steel. It also helps to improve the corrosion resistance of the alloy. It is usually used in combination with chromium and molybdenum.
Molybdenum is mainly used to increase the hardness and yield strength of the steel. It is also used to increase the machinability of the alloy. It is usually used in combination with chromium and nickel.
Vanadium is used to increase the wear resistance and improve the steel’s toughness. It is usually used in combination with chromium and molybdenum.
The alloying element used will depend on the desired properties of the alloy. Each alloying element has its own benefits and drawbacks, so choosing the right alloying elements for the desired cast steels is important.
Categories of Cast Alloy Steels
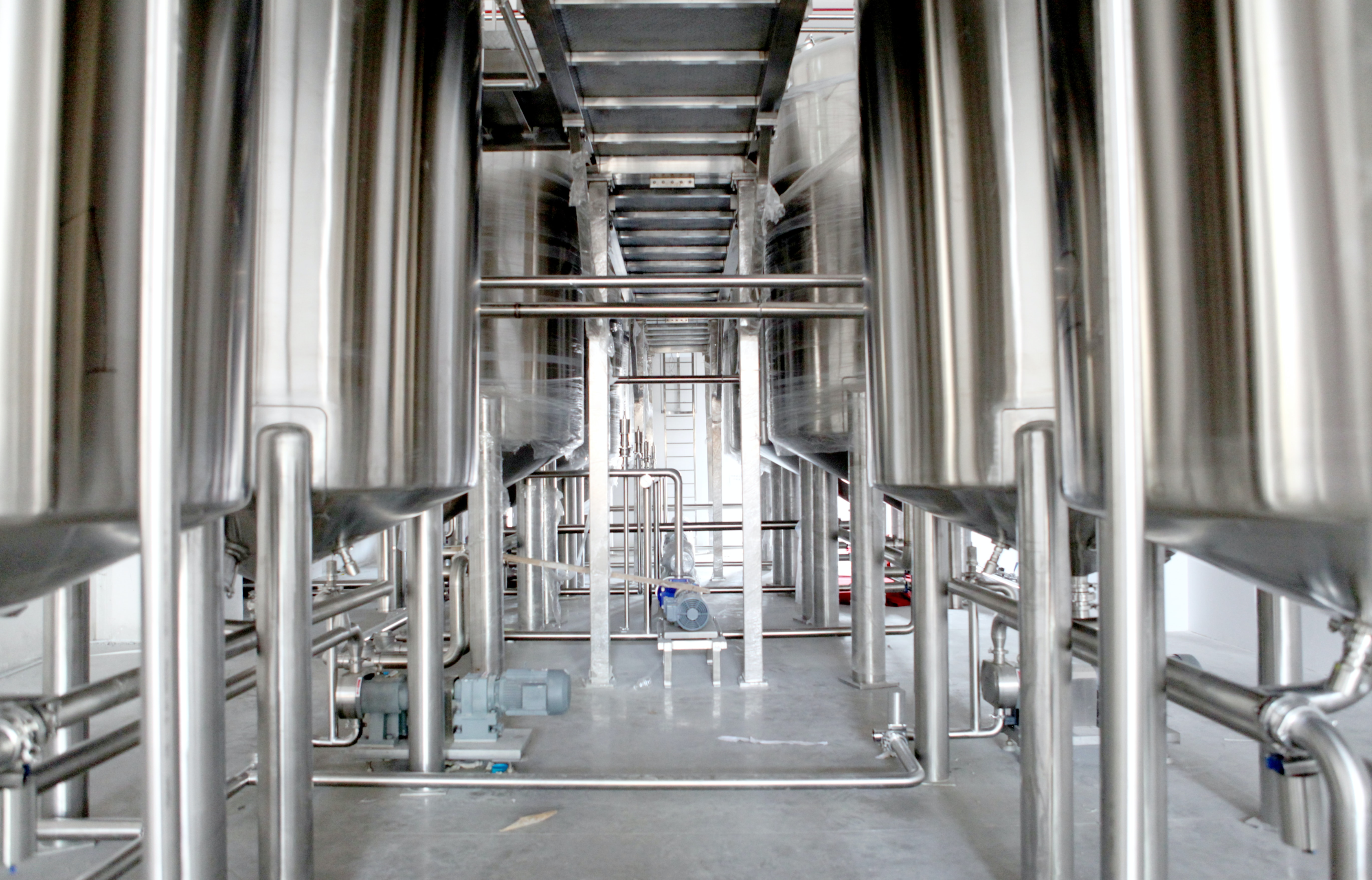
Low Alloy Steels
Low alloy steels are a type of steel alloy that contain small amounts of other elements. Low alloy steel castings offer several advantages. They are cost-effective since they require fewer alloying elements than other types of steel. They are also strong and durable, making them ideal for use in applications requiring high strength and wear resistance.
It is also easy to weld and machine. Low alloy cast steels can be heat treated to achieve different hardness levels. This category of cast steel is often used in heat-resistant steel castings.
High Alloy Steels
High-alloy steel castings are generally made from iron and steel alloys that contain high levels of chromium, molybdenum, and other metals. These castings offer excellent strength and durability compared to other metals, making them ideal for use in industries that require strength and durability.
Carbon Steels
Carbon steel is a type of alloy that contains carbon as the primary alloying element. It usually comprises iron, carbon, and small amounts of other alloying elements. The higher the carbon content, the stronger the steel will be.
Carbon steel castings with lower carbon content are softer and more pliable. However, low-carbon steel is not as strong as other types of steel, making it less suitable for applications that require high strength.
ASTM Specification for Cast Alloy Steels
The ASTM specification for steel casting outlines the requirements and guidelines for steel casting, including the types of casting techniques and the materials that can be used. It also outlines the requirements for the physical and mechanical properties of the steel castings. The chemical composition of the steel castings must meet specific requirements as well.
Chemical Composition
The ASTM Specification provides guidelines for how the chemical composition of steel castings should be reported. All chemical compositions must be reported as a percentage by weight, and any alloying elements must be reported separately. Additionally, the specification requires that any trace elements present in the steel casting be reported in the ASTM documents.
Physical Properties
ASTM has developed a specification for the physical properties of steel castings, which ensures the highest quality and performance of such products.
This includes yield strength, tensile strength, elongation, hardness, impact strength, and fatigue resistance. The specification also covers requirements for consistency and accuracy in the production of steel castings and quality control to ensure the castings meet the specified requirements.
Mechanical Properties
The general requirements for mechanical properties cover the basic mechanical properties of steel castings, including the minimum tensile strength, yield strength, elongation, and reduction of area.
ASTM also outlines the requirements for testing the mechanical properties of steel castings. These tests are used to ensure that the castings meet the specified properties.
Standard Test Methods in The Steel Casting Industry
Many organizations in the steel casting industry use the ASTM standard test methods for steel castings, including foundries, fabricators, and end users. These tests are essential for both the production and the use of steel castings, as they help to ensure that the castings meet all the requirements.
Additionally, they provide valuable data that can be used to compare different types of steel castings and identify any potential problems.
Magnetic Particle Testing
MPT is a non-destructive testing method that uses a magnetic field and magnetic particles to detect surface and subsurface discontinuities in ferrous materials. The magnetic field is created by either an electrical current or a permanent magnet. Magnetic particles are typically made of iron, steel, or other ferromagnetic materials.
These particles are applied to the surface of the material being tested, and the magnetic field causes them to be attracted to any discontinuities present in the material.
The advantages of MPT over other testing methods include its ability to detect small defects, ease of use, and relatively low cost. Additionally, the results of MPT can be quickly and accurately interpreted, which helps to reduce the time and cost associated with testing.
Maximum Hardness Testing Methods
Maximum hardness testing involves using a particular testing machine to measure the hardness of a steel sample by pressing a diamond-tipped probe into the sample’s surface. The hardness is then calculated using the Rockwell C or other hardness scales. The hardness of the steel sample is an indication of its strength and resistance to deformation and corrosion.
The results of the tests are used to assess the strength of the steel components and to determine if they are suitable for the intended application.
Chemical Analysis
The most common method used in the steel casting industry is spectrometric analysis, a form of quantitative analysis that uses x-rays or gamma rays to determine the elemental composition. This highly accurate method provides precise results for quick and effective decision-making.
Another method of chemical analysis used in the steel casting industry is the optical emission spectrometry (OES) technique. The energy of each emission is measured, and the results are used to identify the elements present in the sample.
Uses of Cast Alloy Steels in Corrosion-Resistant Steel Castings
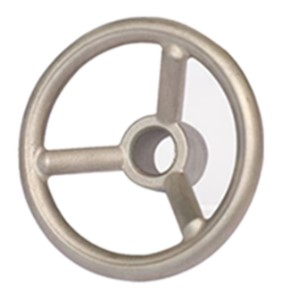
Automotive Industry
Corrosion-resistant steel castings are becoming increasingly popular in the automotive industry. They can provide superior strength and durability while being more cost-effective than other materials. This makes them ideal for automotive engineers to use in many car components, from suspension arms to brake discs.
Power Plants
Corrosion-resistant steel castings are essential components of power plants. They are used to build and maintain the critical systems and components necessary for the efficient operation of the plant. Due to the harsh environment of a power plant, steel castings are essential in providing reliable, long-lasting performance.
In particular, they are used in the boilers and condensers of power plants. The boilers are responsible for heating the water to create steam, while the condensers are responsible for cooling the steam back into liquid form.
Both systems must withstand the corrosive effects of the high temperatures and pressures in the plant, and corrosion-resistant steel castings are the ideal choice.
Chemical Processing Equipment
These steel castings are widely used in the chemical industry to manufacture tanks, valves, pumps, and other components exposed to corrosive environments. The use of steel castings prevents the corrosion of the equipment, which in turn helps to ensure that the chemical processes are carried out safely and efficiently.
This helps to reduce the risk of contamination and the release of hazardous materials.
Pumps, Valves, and Other Water-Handling Equipment
Steel castings can withstand the harsh conditions often present in water-handling systems, like high pressure, extreme temperatures, and aggressive chemicals.
In addition, the material is also very durable, so it can stand up to the wear and tear that is associated with water-handling systems. This helps to increase their lifespan, saving money in the long run.