What do casting foundries do?
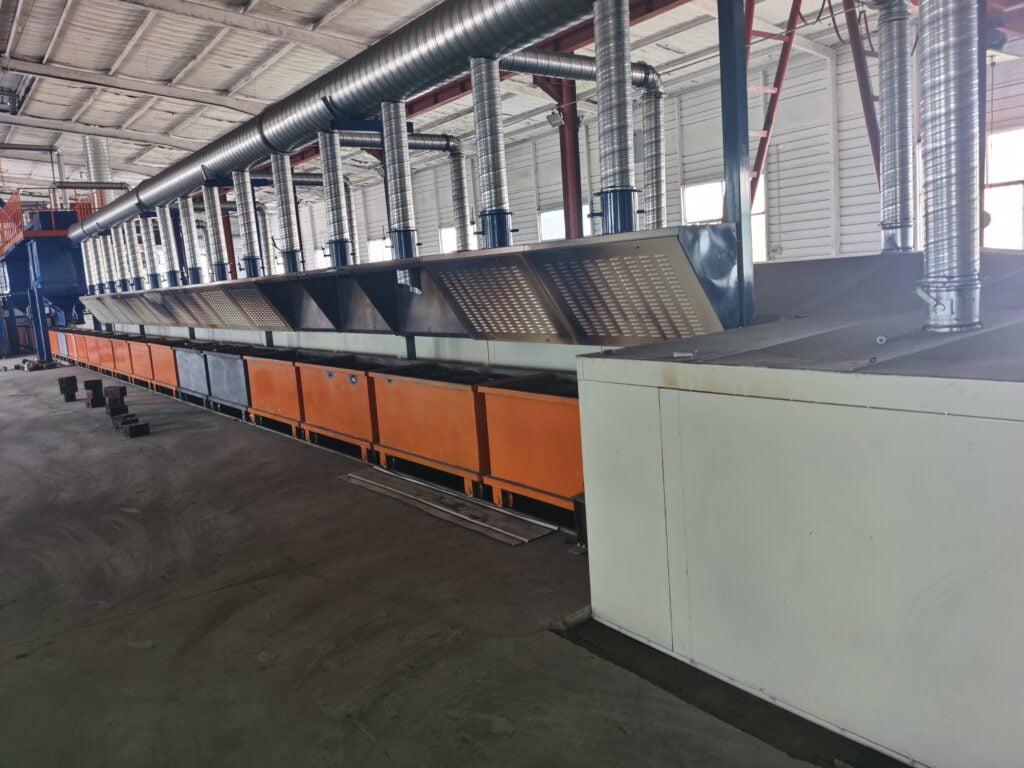
It is understand that a metal factor or foundry is a place where metals are casted into a variety of shapes with the help of melting process. This entire process is used to create functional, as well as, ornamental objects which are manufactured by using metal.
A variety of parts are manufactured in the foundries, and this casting process deal with so many tasks such as melting metal, making of patterns, creation of mold, etc. Once the metal is poured into a mold, the workers have to wait for it get solid. When poured metal is in solid shape, then foundry workers remove it from the mold, and then a final product is shaped and manufactured as per requirements.
It is vital to mention here that molds are made with different materials and foundries tend to use steel, plaster, silica sand, as well as, ceramic shell. The great thing about casting at foundries is that a range of products and materials such as waffle irons, utensils, skillets, machine parts, cabinet hardware, and doors, etc. A steel door fixed at your house is the result of casting at a foundry.
There is so much done by the casting foundries, and if they stop working, the world would be in trouble because these casting foundries do produce so many critical products for the people. The other beauty of casting foundry is its importance in the process of recycling materials, and then rebuilding the recycled material to manufacture strong materials.
Foundry and metal casting
One has to know the fact that metal casting is one of the oldest processes used by humans with regards to fine art and manufacturing. It is even said that the process 7000 years old, which shows how solid and authentic this process has been for so many centuries, and still evolving with the passage of time. When metal casting is handled in a foundry, there are two major elements used in the process, one is metal cost object, and the other is molten motel which is actually in a crucible form, and then it is changed into a mold.
The mold and metal both go through a cooling process, then the removal of metal object is done and a finished product is made. The best part of metal casting is that foundries can use a number of approaches for casting which have been developed over the period of time.
What is the job of a foundry worker?
Foundry Workers is a group of people working in a metallurgical firm making castings from mold. These professionals are responsible for creating molds and castings, monitoring temperature accuracy, and maintenance of machinery and equipment used in the foundry. The work of the foundry demands the use of strength.
Workers have to lift heavier objects for prolonged periods of time. Physical coordination is crucial for safety of workers. The removal of solidified casting requires manual dexterity in addition to knowledge of electrical equipment. Foundry staff can use forklifts as well, but require just certification.
In the foundry work, the workers are required proper working techniques, adequate ventilation and personal protective equipment to work safely. This equipment is helpful to provide them protection from the foundry environment and required to wear leather shoes, gloves and glasses so that it could protect them from the spatters. As the work is related to noisy environment therefore hearing protection should be used. When the workers are directly interacting with molten metals heat and flame sources jacket leggings and pants made of leather should be formed by them as the safety requirements made change according to the complication of task therefore before working in the foundry, it is necessary to analyze the high temperatures of the metals and use the precautions that are prescribed for the relevant metal.
The Casting Process
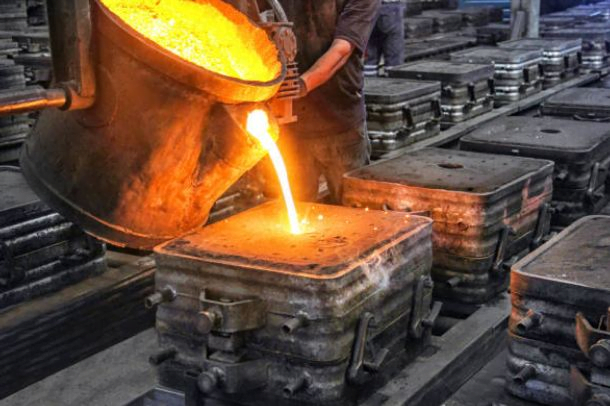
The most necessary thing to keep in mind is that the casting process is not a simple and straightforward process, rather it comes with various stages such as pattern making, molting metal, molten liquid pouring, the process of cooling, removal of metal, and at the end cleaning the products or parts. Moreover, when a part is produced after the casting process, it also goes through an inspection stage where its quality, design, and shape are inspected.
That’s why, when molds are given any kind of shape with the help of a pattern, the process is handled very carefully. The pattern consists of a replica of an object made from metal or wood. So, liquid metal is poured into given patterns to get the final shape, which is actually repaired. The creation of molds is done with several materials, and one important material is silica sand which is most commonly used in the casting process.
Sand Casting
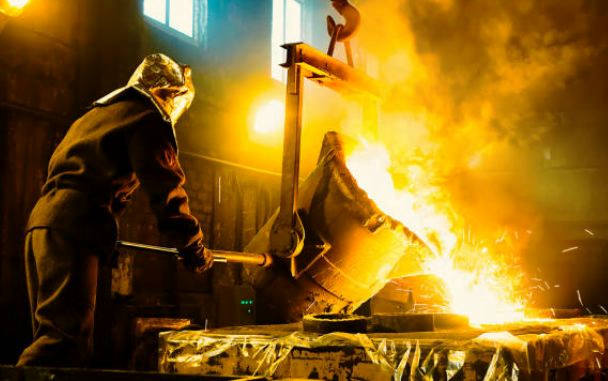
It is mentioned earlier that a range of casting processes are used, and one of them is sand casting. The mold material in this process is sand. So, whatever component is to be cast, the sand is used to make a pattern, which is going to imitate the shape of the product to be cast in the end.
The best thing about sand casting is that it is not as expensive as many other casting processes can be. Especially, if the casting volume is low, then production costs can be saved a lot by using sand casting. Another benefit of sand casting is that both ferrous and non-ferrous materials, both can be cast. The fabrication of large components is also easier to manage with sand casting.
However, there are a few issues with the sand casting as well, which one should keep in mind. The biggest disadvantage of sand casting is that when it is yielded, the accuracy can be lower when compared with other casting methods. The surface finish with sand casting is not smooth, rather it comes with a lot of roughness.
What is cast iron?
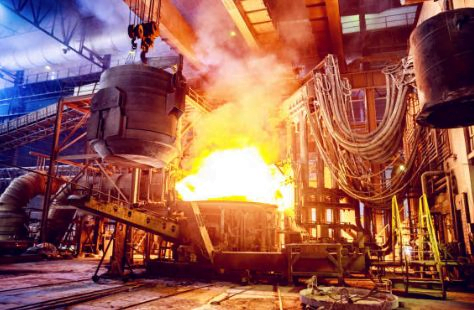
Metal alloys have a range of types in their family, and one such family is called cast iron. The name used the word “iron” so people wrongly think that cast iron means 100% iron, however, this is not the case. If cast iron is compared with carbon steel, the amount of iron is higher in carbon steel.
Cast iron has 4 major types, which need to be reviewed if the casting process will use cast iron. The four types include Gray cast iron, malleable cast iron, ductile cast iron, as well as, white cast iron.
The manufacturing process of cast iron?
Cast iron manufacturing should be handled carefully as it is not an easy task to handle. When the purpose is to make cast iron, the first step is heating the iron ore in a furnace. This process of heating continues till the time iron ore is molted. Then the next step starts to cast the molten metal, where it is taken out so that it can get into a hard shape.
Again, the cast iron ingots go through the melting process to get the final mold. When the remelting process is carried out, a variety of modifications can be made at this stage to the cast iron. The above four types come into play at this particular stage.
Disadvantages and advantages of cast iron?
It is important for the stakeholders to know that cast iron has various advantages, but there are a few disadvantages as well.
Advantages
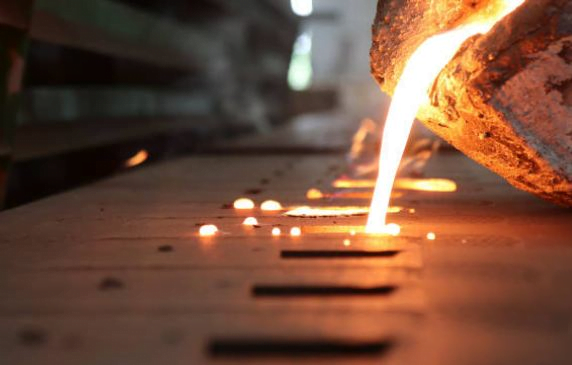
When it comes to reviewing some of the advantages of cast iron, the biggest advantage is its quality casting properties. Moreover, the easy and mass-scale availability and production of cast iron is another benefit enjoyed by the industry players. The iron cast requires the kind of tools, which are easily available, and they are inexpensive and cheap too.
The costly machining process is not needed for cast iron, and it can easily be molded into different complex sizes and shapes. When its compression strength is compared with steel, cast iron is 5 times stronger than steel in this regard. The notch sensitivity of cast iron is low, whereas overall sensibility is good. It is not only resistant to deformation, but also an extremely durable material.
Disadvantages
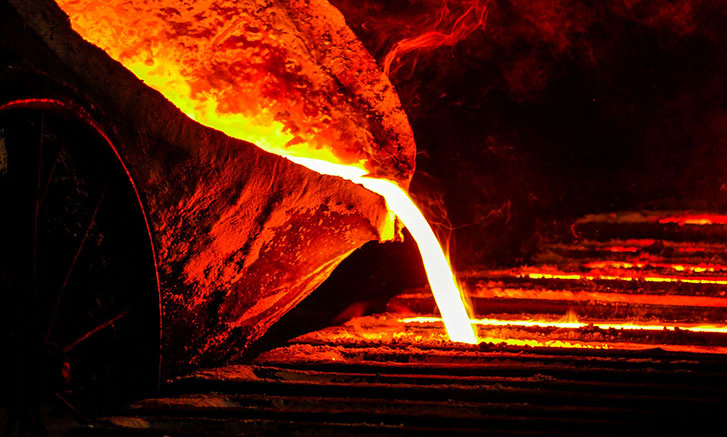
There are several disadvantages of cast iron, and the biggest one is that it is very much prone to rusting so your product made from cast iron can quickly get rusted when compared with other materials. The tensile strength of cast iron is also very poor. There is no yield point to its parts, rather they can suddenly fail to work.
In addition, the impact resistance of cast iron is also very poor, whereas brittleness is on the higher side. It is mentioned earlier that strength is low, but weight as per this ratio is also on the higher side. When it is compared with steel in terms of machinability, the performance shown by cast iron is again very poor.
Conclusion
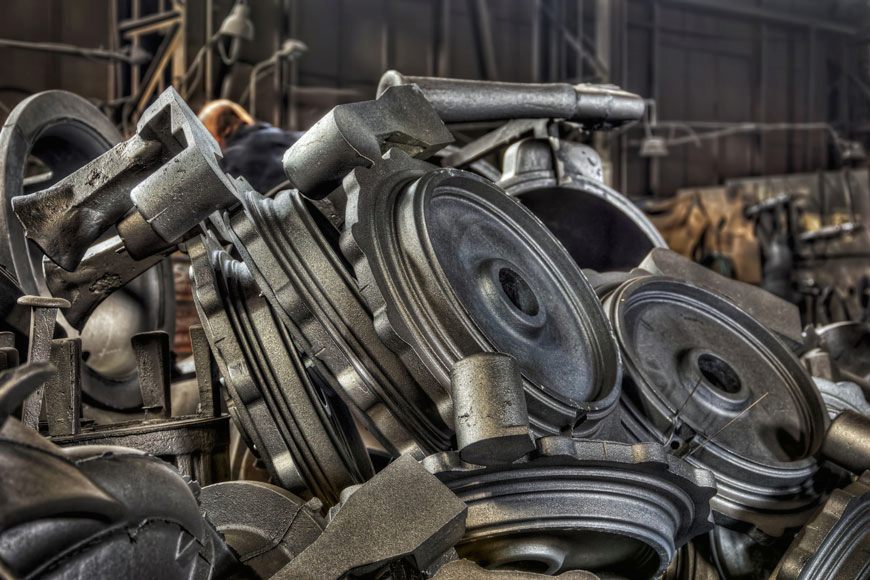
The metal casting process is managed and handled in the casting boundary. There are so many things and processes attached to the casting process. The wood or metal replica is often sued for the casting process, where sand casting or any other type of casting is done to move forward with the manufacturing of products. However, this one article is not enough to cover everything about casting foundries, however, relevant basic concepts have been explained such as molten metal, casting process, sand casting, advantages, disadvantages, etc.