The automotive industry is undergoing a significant transformation with the increasing adoption of electric vehicles. This shift has created new opportunities for innovation in manufacturing processes and materials. One such innovation is aluminum die casting, which has gained popularity in the automotive sector due to its lightweight properties and the ability to replace multiple traditional components with a single die-cast piece.
Aluminum die casting offers numerous advantages, including simplifying production methods, reducing costs, and enabling the use of larger components. By utilizing thin-walled aluminum castings, manufacturers can achieve improved fuel efficiency, better acceleration, braking, and handling for both hybrid and electric vehicles. Furthermore, the integration of aluminum die casting in automotive manufacturing can lead to a reduction in assembly processes, robot usage, and factory footprint.
Key Takeaways:
- Aluminum die casting is a popular choice in the automotive industry due to its lightweight properties and the ability to replace multiple components with a single die-cast piece.
- The integration of aluminum die casting can lead to improved fuel efficiency and better performance in hybrid and electric vehicles.
- By utilizing thin-walled aluminum castings, manufacturers can achieve weight reduction and enhance vehicle handling.
- Aluminum die casting offers opportunities for simplifying production methods, reducing costs, and minimizing assembly processes.
- The automotive industry’s interest in die casting solutions indicates a promising future for the sector.
Innovating Together: Aluminum Die Casting and the Automotive Industry
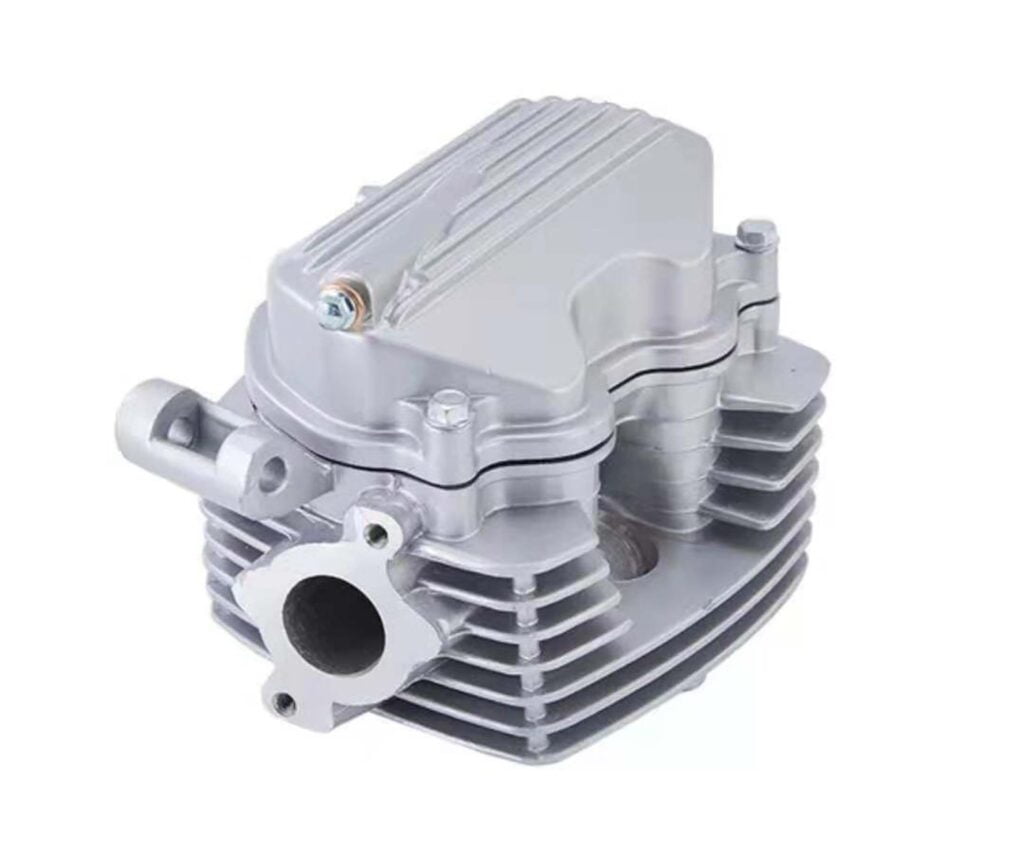
As the automotive industry shifts towards electric vehicles, the need for innovation in production methods and materials becomes more crucial than ever. Aluminum die casting has emerged as a leading solution, offering lightweight properties and the ability to replace multiple traditional components with a single die-cast piece. This not only simplifies production processes but also reduces costs and improves overall efficiency.
One of the key areas where aluminum die casting is driving innovation is in body concepts. The ability to produce larger die-cast pieces that replace multiple traditional components opens up new possibilities for integrated islands in automotive designs. To achieve this, collaboration between the die casting industry and automotive manufacturers is essential. From the production process to part handling, complete solutions are required, necessitating bigger and more precise machines and global support. Digitization plays a critical role in enhancing the efficiency and sustainability of aluminum die casting in the automotive sector. By harnessing digital technologies, manufacturers aim to achieve zero waste, reduce cycle time, and enable round-the-clock operation.
Supporting the Future: Training and Digitization
Support and training are vital components of the relationship between the aluminum die casting industry and the automotive sector. Manufacturers need access to comprehensive training programs that cover the latest developments in die casting technology, process optimization, and quality control. This helps ensure that automotive manufacturers can fully leverage the benefits of aluminum die casting in their designs.
Digital tools and technologies are also transforming the landscape of aluminum die casting. Manufacturers are adopting advanced simulation software to optimize the die casting process, improve design efficiency, and reduce lead times. Automation is becoming increasingly prevalent, allowing for faster production and improved precision. Additionally, the use of digitization enables real-time data monitoring and analysis, leading to more effective decision-making and process optimization.
Sustainability is another crucial aspect of the collaboration between aluminum die casting and the automotive industry. Manufacturers are actively seeking ways to reduce their environmental impact by using recycled or primary aluminum extracted with renewable energy sources. This commitment to sustainability aligns with the growing global focus on reducing carbon emissions and creating a more sustainable future.
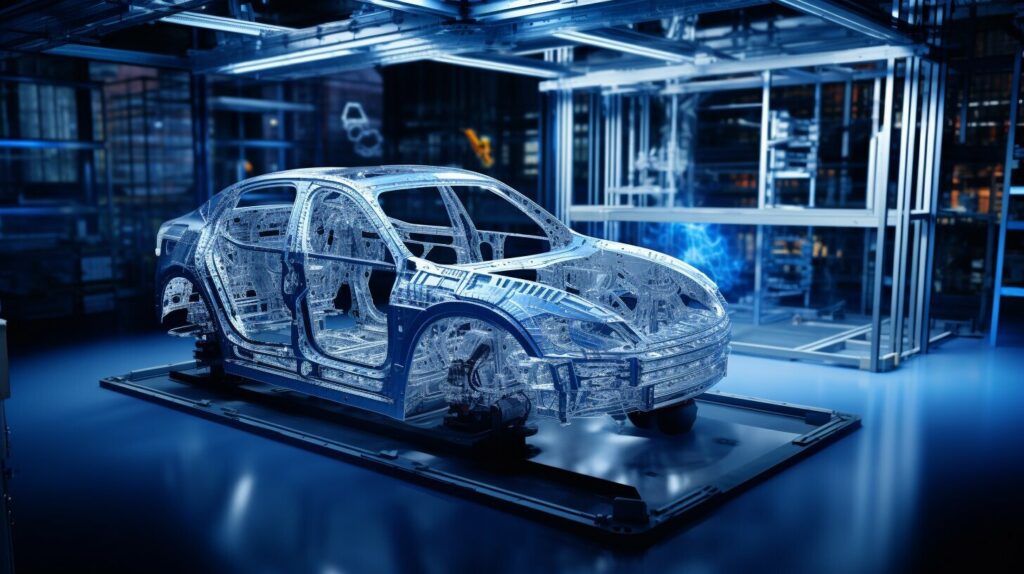
In summary, the partnership between aluminum die casting and the automotive industry is driving innovation and shaping the future of automotive manufacturing. By working together, they can create integrated solutions that optimize production processes, improve efficiency, and reduce costs. Through training, digitization, and a commitment to sustainability, the industry is poised to meet the evolving demands of the automotive sector and contribute to the development of cutting-edge vehicles.
Aluminum Die Casting for Lightweighting and Efficiency
Weight reduction is a crucial factor in automotive and electric vehicle design, and aluminum die casting offers several advantages in this regard. The use of aluminum alloys in die casting provides strength, low weight, corrosion resistance, and excellent heat dissipation properties, making it an ideal choice for automotive applications. By utilizing thin-walled aluminum castings, manufacturers can achieve improved fuel efficiency, better acceleration, braking, and handling for both hybrid and electric vehicles. In contrast, zinc is gaining popularity in areas where weight is not a significant factor. Zinc’s greater fluidity allows for the production of thinner and more intricate castings, eliminating the need for secondary operations often required for aluminum and magnesium alloys. Additionally, zinc offers extended die life and cost-effectiveness for high-volume, complex components.
Die casting plays a vital role in manufacturing thin-walled housings and components for electronic sensors used in advanced automotive technologies. The incorporation of electronic features in vehicles requires lightweight yet durable components, and aluminum die casting meets these requirements effectively. The ability to produce intricate designs and complex geometries in a single die casting process makes it an attractive choice for manufacturing electronic sensor housings. This eliminates the need for additional assembly processes and reduces the overall weight and size of the components. With the growing demand for advanced automotive technologies, including autonomous driving and connectivity, aluminum die casting will continue to play a crucial role in meeting the lightweighting and efficiency needs of the automotive industry.
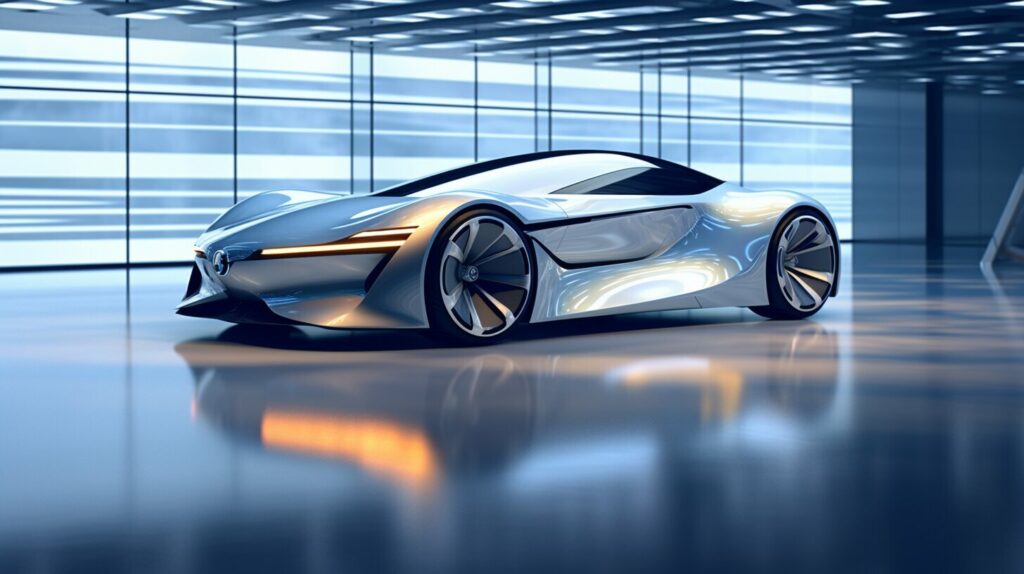
Table: Advantages of Aluminum Die Casting
Advantages | Description |
---|---|
Lightweight | Offers weight reduction for improved fuel efficiency and performance |
Strength | Provides structural integrity and durability |
Corrosion resistance | Ensures long-lasting performance in harsh environments |
Heat dissipation | Helps in managing heat generated by electronic components |
With continuous advancements in aluminum alloys, casting processes, and design optimization techniques, aluminum die casting is poised to play an even greater role in lightweighting and improving the efficiency of automotive components. Innovations in alloy development allow the production of high-strength aluminum castings that can replace heavier materials without compromising performance and safety. Furthermore, ongoing research and development efforts aim to enhance the die casting process, improve the surface finish and dimensional accuracy of castings, and minimize material waste. This continuous evolution and innovation in aluminum die casting will contribute to the ongoing success of the automotive industry in achieving its weight reduction and efficiency goals.
The Future of Die Casting in the Automotive Industry
As the automotive industry continues to evolve, die casting plays a crucial role in shaping its future. The combination of customization, sustainability, and cutting-edge technologies is driving advancements in die casting that meet the industry’s evolving needs.
One of the key trends shaping the future of die casting in the automotive sector is customization. Automakers are increasingly seeking highly tailored components to fit their specific design requirements. Die casting offers the precision, cost-effectiveness, and speed necessary to produce these customized components. With the ability to create complex geometries and intricate details, die casting enables manufacturers to deliver the exact specifications demanded by the automotive industry.
Sustainability is also a major focus in the automotive industry, and die casting offers a solution. With the use of recyclable materials and minimized waste, die casting is a sustainable manufacturing process compared to alternative methods. The adoption of advanced materials and the push for carbon-neutral solutions further contribute to the sustainability of die casting in the automotive industry.
Challenges and Solutions
While the future of die casting looks promising, there are challenges that need to be addressed. One such challenge is the demand for advanced materials. As automakers strive to enhance vehicle performance and efficiency, they require new materials that can withstand extreme conditions and provide superior performance. Die casting manufacturers are rising to this challenge by developing innovative alloys and processes that meet the stringent requirements of the automotive industry.
Another challenge is keeping up with the constantly evolving technological landscape. The automotive industry is embracing cutting-edge technologies, such as artificial intelligence, automation, and data analytics. Die casting manufacturers must stay abreast of these advancements and integrate them into their processes to improve efficiency, productivity, and quality.
In conclusion, the future of die casting in the automotive industry is promising. With customization, sustainability, and the adoption of cutting-edge technologies, die casting continues to evolve and meet the changing demands of the automotive sector. By addressing challenges and providing innovative solutions, die casting manufacturers can play a crucial role in shaping the future of automotive manufacturing.
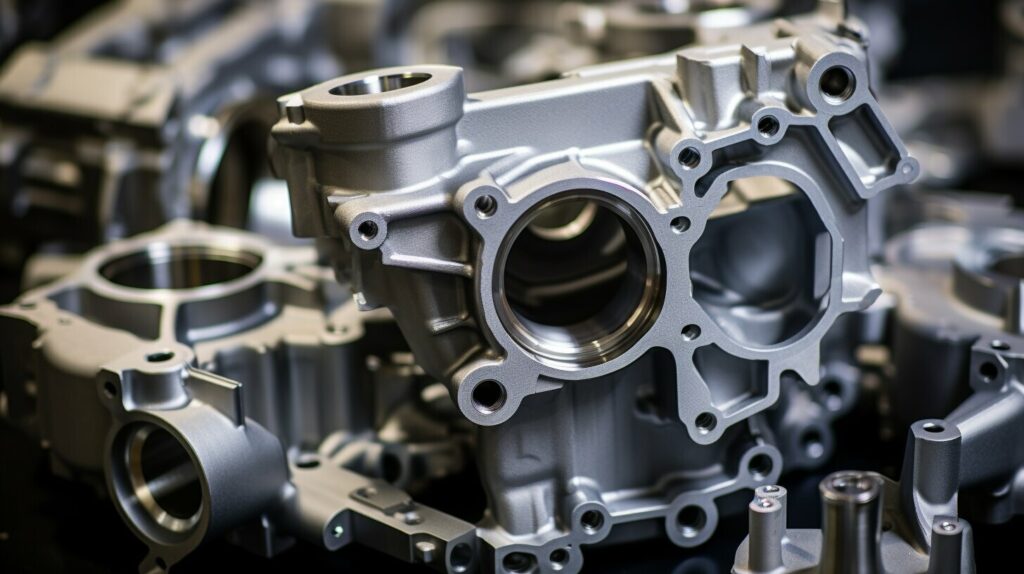
Section 5: Conclusion
As we conclude our exploration of aluminum die casting in the automotive industry, we can confidently say that die casting remains a crucial manufacturing process for producing high-quality automotive components. With advancements in technology, customization, and sustainability, die casting continues to offer numerous benefits.
Looking ahead, the future of die casting in the automotive sector appears promising. Ongoing innovations and a growing focus on electric vehicles and Industry 4.0 are shaping the direction of this industry. Despite challenges, such as the demand for sustainability and the need for advanced materials, die casting is adapting to the evolving landscape of automotive manufacturing.
Die casting’s enduring relevance in the automotive industry is rooted in its ability to deliver precision, cost-effectiveness, speed, and efficiency. The rise of electric vehicles and the adoption of cutting-edge technologies like computer simulations and automation further highlight the importance of die casting in the automotive sector.
In conclusion, die casting remains an integral part of automotive manufacturing, and its future looks bright. With ongoing advancements, a focus on customization, and a commitment to sustainability, die casting will continue to play a paramount role in the production of high-quality automotive components.
FAQ
What are the advantages of aluminum die casting in the automotive industry?
Aluminum die casting offers lightweight properties, the ability to replace multiple traditional components with a single die-cast piece, and improved fuel efficiency, acceleration, braking, and handling for hybrid and electric vehicles.
Why is digitization important in aluminum die casting for the automotive sector?
Digitization increases efficiency and sustainability by reducing waste, cycle time, and enabling 24/7 operation. It also facilitates the integration of processes across multiple plants.
What materials are commonly used in die casting for automotive applications?
Aluminum is the popular choice due to its strength, low weight, corrosion resistance, and heat dissipating properties. Zinc is also gaining popularity in areas where weight is not a significant factor due to its fluidity and cost-effectiveness.
How does die casting contribute to the manufacturing of electronic components for automotive technologies?
Die casting is vital in producing thin-walled housings and components for electronic sensors used in advanced automotive technologies.
What are some challenges faced by die casting in the automotive industry?
Some challenges include the demand for sustainability and advanced materials. However, innovative solutions are being developed to address these challenges.
What is the future of die casting in the automotive industry?
The future of die casting in the automotive industry looks promising, with ongoing innovations, a focus on electric vehicles, and the adoption of Industry 4.0 principles.