Surface finishing is a critical step in the manufacturing process of aluminum die cast components. It plays a crucial role in improving their appearance, functionality, and durability. The choice of surface finishing method depends on factors such as functionality, aesthetics, environmental conditions, and cost. It is important to follow best practices for surface treatment, including proper cleaning, selecting the appropriate finishing method, quality control, and compliance with industry standards.
Key Takeaways:
- Surface finishing is essential for enhancing the appearance and functionality of aluminum die cast components.
- The selection of the suitable surface treatment method depends on factors like functionality, aesthetics, and cost.
- Following best practices in surface treatment, including proper cleaning and quality control, is crucial for optimal results.
- Proper surface treatment provides benefits such as improved aesthetics, corrosion resistance, and durability.
- Surface treatment plays a significant role in enhancing the performance and longevity of die cast aluminum components.
Factors to Consider in Surface Finishing Method Selection
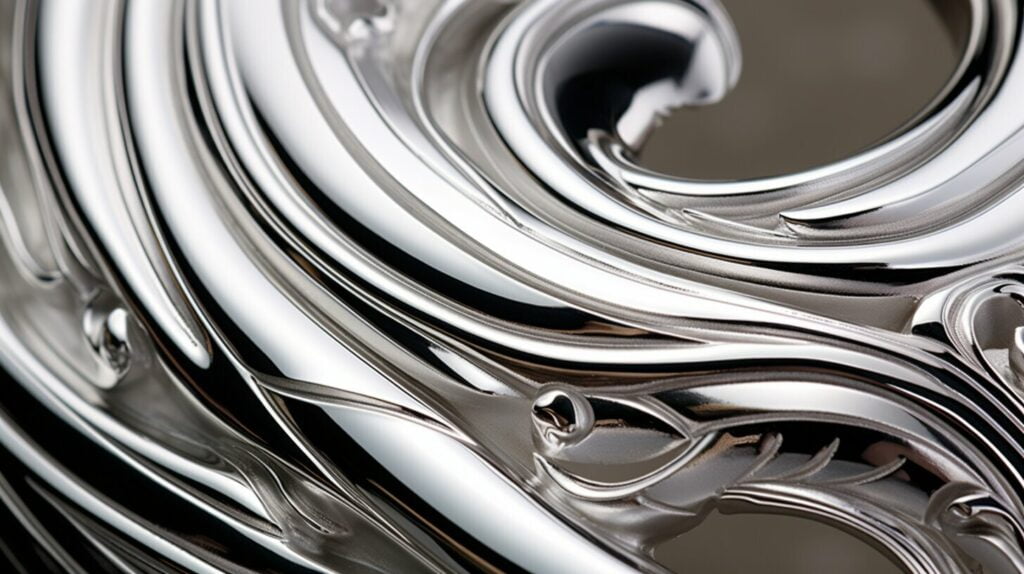
Choosing the right surface finishing method for aluminum die cast components involves careful consideration of various factors. The functionality of the component is one of the key aspects to evaluate. Different applications may require specific surface treatments to enhance performance and ensure optimal functionality. For example, a component used in a corrosive environment may benefit from a protective coating to improve its durability and resistance to degradation.
Aesthetics also play a significant role in surface finishing method selection. The desired visual effects can vary depending on the application and the customer’s preferences. Some finishes, such as polishing or plating, can give a component a sleek and luxurious appearance, while others, like textured finishes, can provide a more rugged and industrial look.
Environmental factors should not be overlooked when evaluating surface finishing methods. Components exposed to harsh conditions, such as extreme temperatures or chemical exposure, may require specialized surface treatments to ensure long-term performance and protection. It is essential to consider the impact of the environment on the component’s functionality and lifespan.
Factors to Consider in Surface Finishing Method Selection:
- Functionality: Evaluate the specific requirements of the component’s intended application.
- Aesthetics: Consider the desired visual effects and customer preferences.
- Environmental Factors: Assess the impact of the environment on the component’s performance and durability.
- Cost: Take into account the budget constraints and the overall value offered by different surface finishing methods.
Cost is another significant factor to consider. Different surface finishing methods come with varying costs, depending on factors such as material requirements, labor, and equipment. It is important to find a balance between the desired finish quality and the available budget, ensuring that the chosen method delivers the expected results without compromising the overall project cost.
By carefully evaluating these factors in the surface finishing method selection process, manufacturers can ensure that their aluminum die cast components meet the required functionality, aesthetics, environmental resilience, and cost-effectiveness.
Factors to Consider | Description |
---|---|
Functionality | Evaluate the specific requirements of the component’s intended application. |
Aesthetics | Consider the desired visual effects and customer preferences. |
Environmental Factors | Assess the impact of the environment on the component’s performance and durability. |
Cost | Take into account the budget constraints and the overall value offered by different surface finishing methods. |
Best Practices for Surface Treatment of Die Cast Aluminum Components
When it comes to surface treatment of die cast aluminum components, following best practices is essential. These practices ensure that the finished components meet the desired specifications, both in terms of functionality and aesthetics. It is a multi-step process that involves cleaning, selecting the appropriate finishing method, ensuring quality control, and compliance with industry standards.
Thorough cleaning of the surface is a critical first step in the surface treatment process. It removes any contaminants or impurities that could hinder the adhesion of the finish. This can be achieved through various methods such as solvent cleaning, alkaline cleaning, or mechanical cleaning.
Once the surface is clean, selecting the appropriate finishing method is crucial. Factors such as functionality, aesthetics, and cost should be considered. Different applications may require different surface treatments, such as anodizing, powder coating, or plating. Careful consideration of these factors ensures that the chosen finishing method enhances both the appearance and performance of the components.
Quality control and compliance with standards
Throughout the surface treatment process, quality control is of utmost importance. Regular inspection and testing help ensure that the finish meets the required specifications and standards. This includes checks for thickness, appearance, adhesion, and corrosion resistance. By implementing a comprehensive quality control system, any potential issues can be identified and addressed promptly, ensuring the highest level of quality in the finished components.
Additionally, compliance with industry and safety standards is a vital aspect of surface treatment. Adhering to these standards not only ensures the quality and durability of the components but also guarantees the safety of the end-users. It is important to stay up to date with the latest industry regulations and certifications to maintain compliance throughout the surface treatment process.
In summary, best practices for surface treatment of die cast aluminum components include thorough cleaning, appropriate finishing method selection, rigorous quality control, and compliance with industry standards. By following these practices, manufacturers can achieve optimal results in terms of functionality, aesthetics, and overall product quality.
Benefits of Proper Surface Treatment for Die Cast Aluminum Components
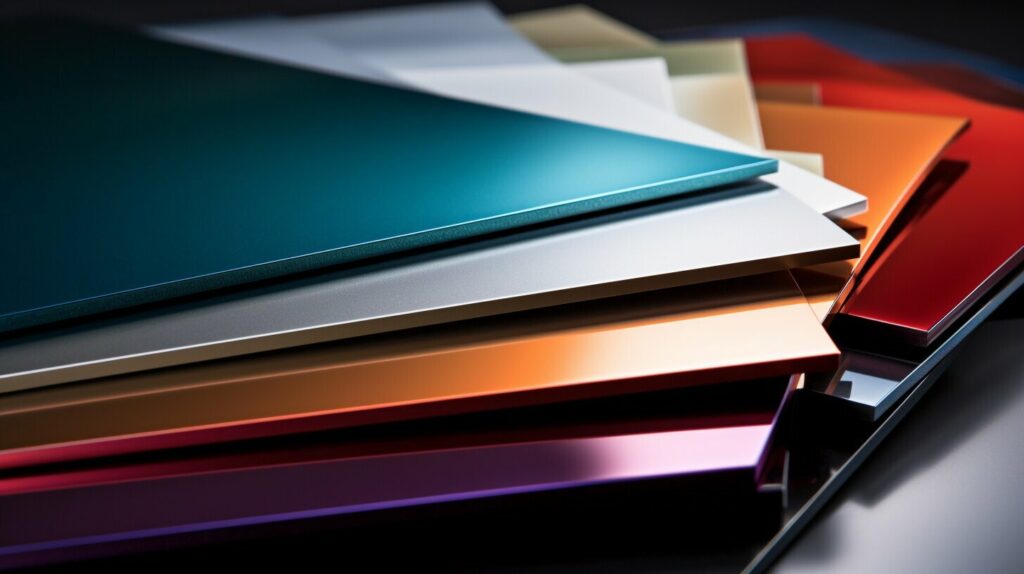
Proper surface treatment of die cast aluminum components offers a wide range of benefits that significantly enhance their overall quality and performance. One of the key advantages is improved aesthetics. By applying surface finishes such as anodizing, powder coating, and plating, the components become visually appealing to customers, creating a positive impression and increasing their market value.
Another important benefit is enhanced corrosion resistance and durability. The surface treatment methods create a protective layer that shields the components from environmental factors, preventing corrosion and extending their lifespan. This makes them suitable for various applications and environments, even those with harsh conditions.
The functionality of die cast aluminum components can also be improved through proper surface treatment. By choosing the right finishing method, manufacturers can enhance the performance and effectiveness of the components in their intended applications. The surface treatment can optimize the physical properties, ensuring the components meet the required specifications and deliver superior functionality.
Furthermore, surface treatment plays a role in reducing the need for frequent maintenance and making the components easier to clean. The protective layers created by the finishing methods make the components more resistant to dirt, grime, and other contaminants. This not only saves time and effort, but also contributes to the longevity of the components, reducing the risk of damage and wear over time.
Table: Comparison of Surface Treatment Methods
Surface Treatment Method | Aesthetics | Corrosion Resistance | Durability | Functionality | Maintenance |
---|---|---|---|---|---|
Anodizing | High | Excellent | Excellent | Good | Low |
Powder Coating | High | Good | Good | Good | Low |
Plating | High | Excellent | Excellent | Good | Low |
In summary, proper surface treatment is essential for optimizing the aesthetics, corrosion resistance, durability, functionality, and maintenance of die cast aluminum components. By following best practices and selecting the appropriate finishing methods, manufacturers can ensure that their components meet the highest standards and exceed customer expectations. Whether it’s improving the visual appeal, increasing resistance to corrosion, enhancing functionality, or reducing maintenance requirements, surface treatment plays a vital role in maximizing the overall quality and performance of die cast aluminum components.
Importance of Surface Treatment in Die Cast Aluminum Components
Proper surface treatment is of utmost importance when it comes to die cast aluminum components. It directly impacts their performance, longevity, functionality, and aesthetics. At KT-Foundry, we understand the significance of surface treatment and we employ industry-leading techniques to ensure that our components meet the highest standards.
One of the key benefits of surface treatment is enhanced performance. By applying the appropriate surface finish, we can optimize the functionality of die cast aluminum components, making them more effective in their intended applications. Whether it’s improving heat dissipation or reducing friction, surface treatment plays a vital role in maximizing the performance of these components.
“Proper surface treatment enhances the functionality and marketability of the components, making them more attractive to customers.”
In addition to performance, surface treatment also contributes to the longevity of die cast aluminum components. By protecting the surface from corrosion, wear, and environmental factors, surface finishes such as anodizing, powder coating, and plating significantly increase the durability of the components. This ensures that they can withstand harsh conditions and have an extended lifespan.
Aesthetics is another key aspect influenced by surface treatment. The right surface finish can transform the appearance of die cast aluminum components, making them visually appealing to customers. Whether it’s achieving a glossy or matte finish, surface treatment can enhance the overall look and feel of the components, making them more attractive in the market.
In conclusion, surface treatment plays a crucial role in the manufacturing of die cast aluminum components. By following best practices and employing the appropriate surface finishes, manufacturers can ensure optimal performance, longevity, functionality, and aesthetics. At KT-Foundry, we prioritize surface treatment to deliver high-quality components that meet the diverse needs of our customers.
Conclusion
In conclusion, surface treatment is an essential step in the manufacturing process of aluminum die cast components. By following best practices, manufacturers can achieve optimal performance, durability, and aesthetics in their components. Proper surface treatment enhances the functionality and marketability of the components, making them more attractive to customers.
At KT-Foundry, we understand the importance of surface treatment and employ industry-leading techniques to deliver high-quality die cast aluminum components. Our team of experts ensures that each component undergoes thorough cleaning, careful finishing method selection, and rigorous quality control to meet the highest standards.
Experience excellence in every detail with us. From the initial design to the final finish, we are committed to providing you with top-notch aluminum die cast components that not only meet your requirements but exceed your expectations. Trust KT-Foundry for all your surface treatment needs and let us bring your vision to life.
FAQ
What is the role of surface finishing in the manufacturing process of aluminum die cast components?
Surface finishing is critical in improving the appearance, functionality, and durability of aluminum die cast components.
What factors should be considered when selecting a surface finishing method for aluminum die cast components?
Factors to consider include functionality, aesthetics, environmental conditions, and cost.
What are the best practices for surface treatment of die cast aluminum components?
Best practices include thorough cleaning, selecting the appropriate finishing method, quality control, and compliance with industry standards.
What are the benefits of proper surface treatment for die cast aluminum components?
Proper surface treatment improves aesthetics, corrosion resistance, durability, and functionality, and reduces maintenance needs.
Why is surface treatment important in die cast aluminum components?
Surface treatment is important for achieving optimal performance, longevity, functionality, and aesthetics.