Welcome to the fascinating world of aluminum die casting, where precision and versatility combine to shape the future of manufacturing. At KT-Foundry, we have mastered the art of aluminum die casting, pushing the boundaries of what is possible and driving innovation in this intricate process.
Aluminum die casting is a versatile manufacturing technique that involves injecting molten aluminum into precise molds. This process allows for the creation of complex geometries and intricate details with exceptional accuracy. With its numerous benefits and applications, aluminum die casting plays a crucial role in various industries.
Key Takeaways:
- Precision and detail are key advantages of aluminum die casting, allowing for the creation of intricate components with exceptional accuracy.
- The process offers versatility in size and complexity, making it suitable for a wide range of applications across industries.
- Aluminum die casting is cost-efficient, particularly in high-volume production, due to reduced material waste and enhanced manufacturing efficiency.
- The strength-to-weight ratios of aluminum die cast parts make them ideal for applications where lightweight yet strong components are required.
- Aluminum die casting provides a variety of surface finish options, ensuring high-quality and aesthetically pleasing components.
As we delve deeper into the world of aluminum die casting, we will explore its applications in industries such as automotive, electronics, aerospace, and consumer goods. We will also delve into the unique advantages it offers over traditional casting methods, highlighting its superior surface finish, tighter tolerances, and dimensional stability.
Furthermore, we will discuss the vital role played by aluminum die casting manufacturers in shaping possibilities for various industries. Their precision and efficiency contribute to waste reduction, higher manufacturing efficiency, and the production of high-quality components.
As we continue our exploration, we will focus on the promising future of aluminum die casting in the ever-evolving technological landscape. The lightweight design, corrosion resistance, conductivity, and impressive weight-to-strength ratio of aluminum die cast parts make them increasingly sought after in industries that demand efficient and sustainable solutions.
In conclusion, aluminum die casting is a fascinating and intricate process that has a significant impact on the future of manufacturing. With its precision, versatility, and numerous advantages, it continues to shape the way we create complex components and push the boundaries of what is possible.
The Benefits of Aluminum Die Casting
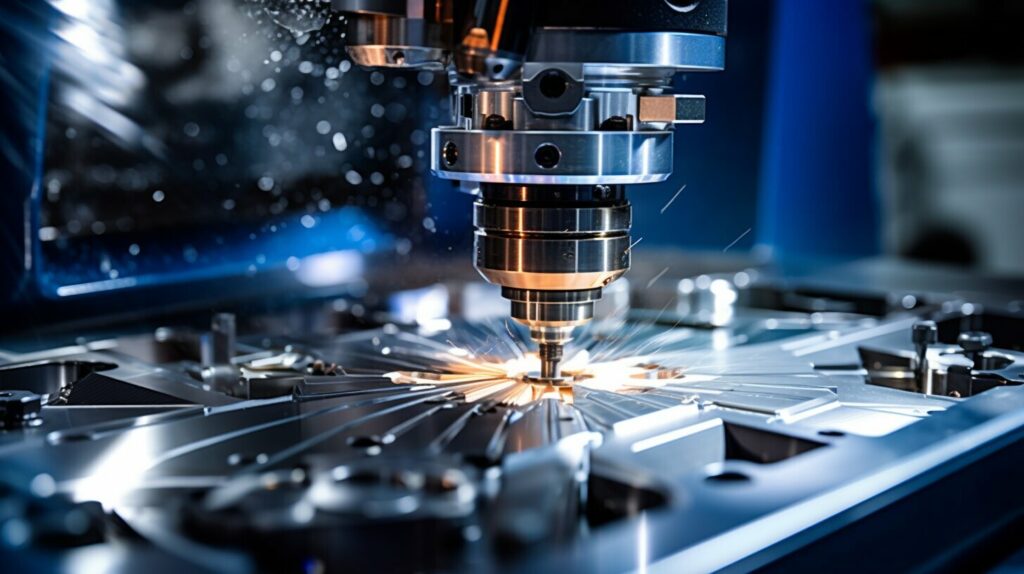
Aluminum die casting offers a multitude of benefits that make it a preferred choice in the manufacturing industry. The process allows for the creation of precision and detail in products, ensuring that every component meets the required specifications with exceptional accuracy. This level of precision is particularly important in industries where small variations can have significant consequences, such as automotive, aerospace, and electronics. By utilizing aluminum die casting, manufacturers can achieve the desired level of quality without compromising on the intricacy of the design.
In addition to precision, aluminum die casting provides cost efficiency, especially in high-volume production. The process allows for the creation of complex geometries in a single operation, reducing the need for additional machining or assembly. This not only saves time but also minimizes material waste, making it a sustainable option for large-scale manufacturing.
Another advantage of aluminum die casting is its outstanding strength-to-weight ratio. Aluminum is known for its lightweight properties, making it an ideal choice for industries where weight reduction is crucial, such as automotive and aerospace. Despite being lightweight, aluminum die cast parts maintain their structural integrity and offer excellent strength, ensuring the durability and reliability of the final products.
Furthermore, aluminum die casting provides a wide range of surface finish options. The molds used in the process can be designed to create components with varying textures and finishes, allowing manufacturers to achieve the desired aesthetic appeal. This versatility makes aluminum die casting suitable for a diverse range of applications, from consumer goods to industrial equipment.
Benefits of Aluminum Die Casting: |
---|
Precision and detail |
Cost efficiency |
Strength-to-weight ratios |
Surface finish options |
Applications of Aluminum Die Casting
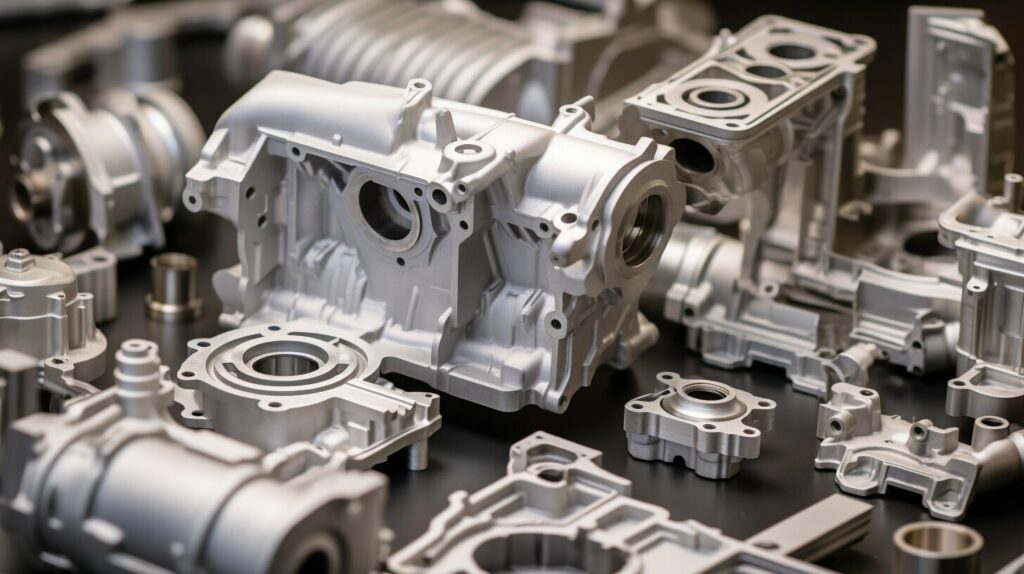
The versatility of aluminum die casting makes it indispensable in a wide range of industries, from automotive to consumer goods. The ability to create complex shapes and achieve consistent, high-quality results has led to its widespread use in various applications.
Automotive
The automotive industry heavily relies on aluminum die casting for the production of lightweight yet durable components. These include engine parts, transmission housings, and structural components. Aluminum’s excellent strength-to-weight ratio makes it ideal for enhancing fuel efficiency without compromising on performance.
Electronics
In the electronics industry, aluminum die casting is used to manufacture intricate housing and heat sinks for electronic devices. With its superior thermal conductivity and excellent electromagnetic shielding properties, aluminum is highly valued in this field. The precision and consistency achieved through die casting ensure the proper fit and functionality of electronic components.
Aerospace
Aerospace applications benefit from the lightweight nature of aluminum die cast parts, which contribute to fuel efficiency and weight reduction in aircraft. The ability to create complex geometries also allows for the production of aerodynamic components. From engine parts to structural components, aluminum die casting plays a crucial role in the aerospace industry.
Consumer Goods
Aluminum die casting finds diverse applications in the manufacturing of consumer goods. It is used to create high-quality products such as kitchen appliances, power tools, and furniture components. The versatility and durability of die-cast parts ensure longevity and performance, making them highly sought after in the consumer goods market.
In conclusion, aluminum die casting has revolutionized the manufacturing process across various industries. Its ability to produce intricate, high-quality components with exceptional accuracy, cost efficiency, and strength-to-weight ratios has made it a preferred choice for countless applications. From automotive and aerospace to electronics and consumer goods, the future of aluminum die casting looks promising as it continues to shape the world of manufacturing.
The Role of Aluminum Die Casting Manufacturers
Aluminum die casting manufacturers are at the forefront of shaping possibilities in various industries, with their commitment to precision and efficiency. As experts in the intricate world of aluminum die casting, we at KT-Foundry understand the vital role we play in delivering high-quality components that meet the diverse needs of our clients.
With a focus on precision, we strive to achieve impeccable accuracy in every aspect of the manufacturing process. Our state-of-the-art facilities and advanced technologies enable us to produce complex geometries and intricate details with exceptional consistency, ensuring that every component meets the highest standards of quality.
Efficiency is another key aspect of our operations. By utilizing advanced production techniques and optimized processes, we are able to reduce waste and minimize downtime, resulting in shorter lead times and increased cost savings for our clients. Our commitment to efficiency extends throughout all stages of manufacturing, from mold design and tooling to casting and finishing.
Collaboration is also an essential element of our approach. We work closely with our clients, understanding their unique requirements and offering tailored solutions that meet their specific needs. By leveraging our expertise and capabilities, we contribute to the success of our partners, ensuring that they can bring their innovative ideas to life.
Benefits of Aluminum Die Casting Manufacturers | Details |
---|---|
Precision | Impeccable accuracy in manufacturing complex geometries and intricate details. |
Efficiency | Optimized processes and advanced technologies reduce waste and minimize downtime. |
Collaboration | Close partnerships with clients to deliver tailored solutions that meet specific needs. |
Choosing the right aluminum die casting manufacturer is crucial for the success of any project. With our commitment to precision, efficiency, and collaboration, we strive to exceed expectations and deliver exceptional results. Partner with us at KT-Foundry and unlock the full potential of aluminum die casting for your industry.
Advantages of Aluminum Die Casting over Traditional Methods
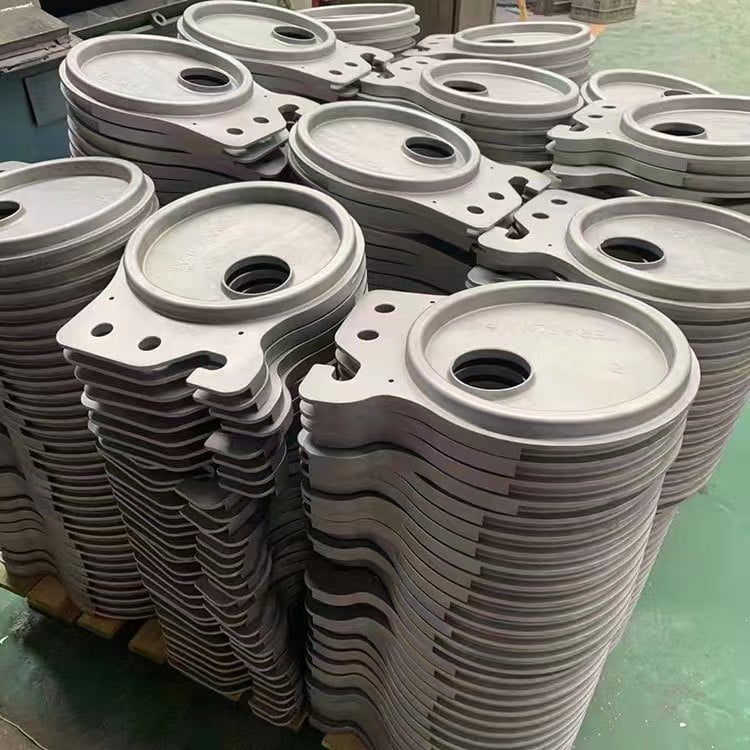
Compared to traditional casting methods, aluminum die casting offers a myriad of advantages that revolutionize the manufacturing process. With its precision and efficiency, this innovative technique has become a preferred choice for numerous industries.
One key advantage of aluminum die casting is its ability to achieve faster production cycles. The use of advanced technologies and streamlined processes allows for rapid production, reducing lead times and enhancing overall efficiency. This means that companies can meet tight deadlines and deliver products to market faster, gaining a competitive edge in the industry.
Another significant advantage is the superior surface finish provided by aluminum die casting. The process allows for the creation of smooth and flawless surfaces, eliminating the need for additional finishing processes such as polishing or grinding. This not only saves time and money but also ensures a consistent and high-quality appearance for the final product.
Aluminum die casting also offers tighter tolerances and better dimensional stability compared to traditional methods. The precise injection of molten aluminum into molds ensures accurate replication of complex geometries and intricate details. This level of precision and consistency is crucial for industries that require tight tolerances, such as aerospace and automotive, where even the smallest deviation can have significant implications for performance and safety.
Advantages of Aluminum Die Casting over Traditional Methods |
---|
Faster production cycles |
Superior surface finish |
Tighter tolerances |
Better dimensional stability |
In summary, aluminum die casting offers unparalleled advantages over traditional casting methods. Its faster production cycles, superior surface finish, tighter tolerances, and better dimensional stability make it a game-changer in the manufacturing industry. Whether it’s for automotive, aerospace, electronics, or consumer goods, the precision and efficiency of aluminum die casting continue to shape the future of manufacturing.
The Promising Future of Aluminum Die Casting
As technology continues to advance, the potential for custom aluminum die casting expands, opening up new possibilities for lightweight, efficient, and sustainable solutions. Aluminum die cast parts have gained prominence in various industries due to their exceptional properties, making them an ideal choice for critical applications.
One of the key advantages of aluminum die casting is its lightweight nature. Aluminum is renowned for its low density, allowing manufacturers to create intricate and complex geometries without compromising on strength. This lightweight design opens doors for innovative solutions in industries such as automotive and aerospace, where reducing weight is crucial for improving fuel efficiency and overall performance.
In addition to being lightweight, aluminum die cast parts offer excellent corrosion resistance, making them highly suitable for applications in harsh environments. This resistance to corrosion ensures the longevity of components, reducing maintenance costs and increasing the overall lifespan of products. Furthermore, aluminum’s high thermal conductivity makes it an ideal choice for applications where heat dissipation is critical.
The exceptional weight-to-strength ratio of aluminum die cast parts is another significant advantage. This means that despite their lightweight nature, these components exhibit remarkable strength and durability. This combination of properties allows for the creation of structurally sound and reliable parts that can withstand challenging conditions.
Advantages of Aluminum Die Casting | Properties |
---|---|
Precision and Detail | Allows for the creation of complex geometries with exceptional accuracy. |
Cost Efficiency | Enables high-volume production at a lower cost per unit. |
Superior Surface Finish | Provides a wide range of options for achieving high-quality surface finishes. |
Strength-to-Weight Ratios | Offers lightweight design without compromising on strength. |
In conclusion, the future of aluminum die casting looks promising. With advancements in technology, manufacturers can continue to push the boundaries of what is possible, creating intricate, efficient, and sustainable solutions for various industries. The versatility, lightweight nature, corrosion resistance, conductivity, and impressive weight-to-strength ratios of aluminum die cast parts make them an increasingly popular choice for designers and engineers seeking high-performance components.
Conclusion
In conclusion, aluminum die casting is a precise and innovative manufacturing process that plays a critical role in shaping the future of industries worldwide. With its ability to create complex geometries and intricate details with exceptional accuracy, aluminum die casting offers a range of benefits. These include precision and detail, versatility in size and complexity, cost efficiency in high-volume production, enhanced strength-to-weight ratios, and excellent surface finish options.
The applications of custom aluminum die casting span across various industries such as automotive, electronics, aerospace, and consumer goods. From intricate electronics housings to lightweight yet strong components for automotive and aerospace sectors, aluminum die casting enables the production of high-quality parts with exceptional precision.
Aluminum die casting manufacturers are key players in the industry, consistently producing high-quality components that meet the demands of modern manufacturing. Their expertise and capabilities contribute to waste reduction and higher efficiency in the manufacturing process, ensuring impeccable accuracy and surface finish.
Compared to traditional sand casting methods, aluminum die casting offers numerous advantages. These include faster production cycles, superior surface finish, tighter tolerances, and better dimensional stability. These advantages make it the preferred choice for large-scale manufacturing, providing efficient and precise solutions to industries across the board.
The future of custom aluminum die casting looks promising as technology continues to evolve. With its lightweight design, corrosion resistance, conductivity, and impressive weight-to-strength ratio, aluminum die casting is well-positioned to drive innovation in industries such as electronics, furniture, aerospace, transportation, construction, and healthcare. It offers endless possibilities for creating intricate, efficient, and sustainable solutions.
FAQ
What is aluminum die casting?
Aluminum die casting is a versatile manufacturing process that involves injecting molten aluminum into precise molds, allowing for the creation of complex geometries and intricate details with exceptional accuracy.
What are the benefits of aluminum die casting?
Aluminum die casting offers several benefits including precision and detail, versatility in size and complexity, cost efficiency in high-volume production, enhanced strength-to-weight ratios, and excellent surface finish options.
In which industries is aluminum die casting used?
Aluminum die casting finds diverse applications across industries such as automotive, electronics, aerospace, and consumer goods.
What role do aluminum die casting manufacturers play?
Aluminum die casting manufacturers play a vital role in shaping possibilities for various industries, capable of producing high-quality components with impeccable accuracy and surface finish.
How does aluminum die casting compare to traditional casting methods?
Aluminum die casting offers advantages such as faster production cycles, superior surface finish, tighter tolerances, and better dimensional stability compared to traditional sand casting methods.
What are the applications of aluminum die cast parts?
Aluminum die cast parts have a wide range of applications including electronics, furniture, aerospace, transportation, construction, and healthcare industries due to their lightweight, corrosion resistance, high conductivity, and improved weight-to-strength ratio.
What is the future of aluminum die casting?
The future of aluminum die casting is promising, as technology continues to evolve, pushing the boundaries of what can be achieved in terms of intricate, efficient, and sustainable solutions.