As professional copywriting journalists, we understand the importance of electric motor housing in providing quality protection for your motors. Electric motor housing is a crucial component that plays a significant role in the service life and overall performance of electric motors. The main components of an electric motor are susceptible to damage from adverse external factors such as moisture, dust, and debris. Without adequate protection, these components can fail prematurely, leading to costly repairs and maintenance.
In this article, we will discuss the different types of electric motor housing and their characteristics, the manufacturing process, the benefits of cooling channels, the importance of mounting holes and integration, and the role electric motor housing plays in electric vehicles. By the end of this article, you will understand why quality electric motor housing is essential and how it can enhance the performance and longevity of your motors.
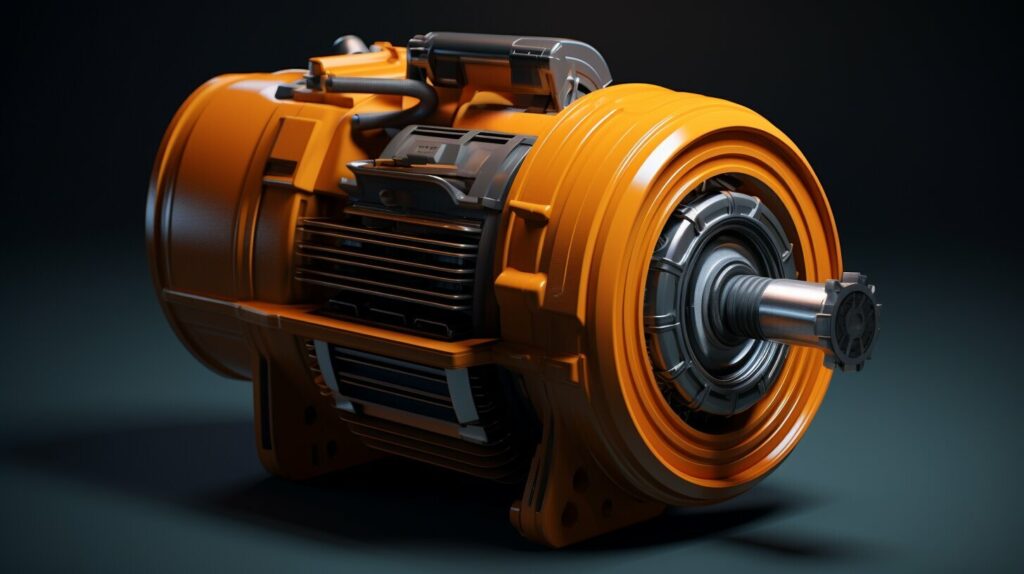
Key Takeaways:
- Electric motor housing is essential in providing quality protection for your motors.
- The main components of an electric motor are susceptible to damage from external factors, without adequate protection.
- This article will explore the different types of electric motor housing, manufacturing processes, and their benefits.
- We will also discuss the significance of cooling channels, mounting holes and integration, and the role of electric motor housing in electric vehicles.
Types of Electric Motor Housing
There are various types of electric motor housing available, each with its unique characteristics and benefits. The type of housing used will depend on the specific motor’s requirements and application.
Aluminum Alloy Electric Motor Housing
Aluminum alloy electric motor housing is a popular choice due to its lightweight and corrosion-resistant properties. This type of housing is created using an aluminum extrusion process, which involves heating and shaping the material to form a desired shape. The resulting housing is durable, can withstand high temperatures, and is easy to machine if necessary.
The use of aluminum alloy motor housing is common in industries such as aerospace, automotive, and marine, where weight reduction is important for improved efficiency and performance.
Cast Iron Electric Motor Housing
Cast iron electric motor housing is another popular choice due to its strength and durability. This type of housing is created using a die casting process, which involves pouring molten metal into a mold. The process results in a housing that can withstand high loads, vibrations, and extreme temperatures.
Cast iron motor housing is commonly used in heavy-duty applications such as industrial machinery, pumps, and compressors.
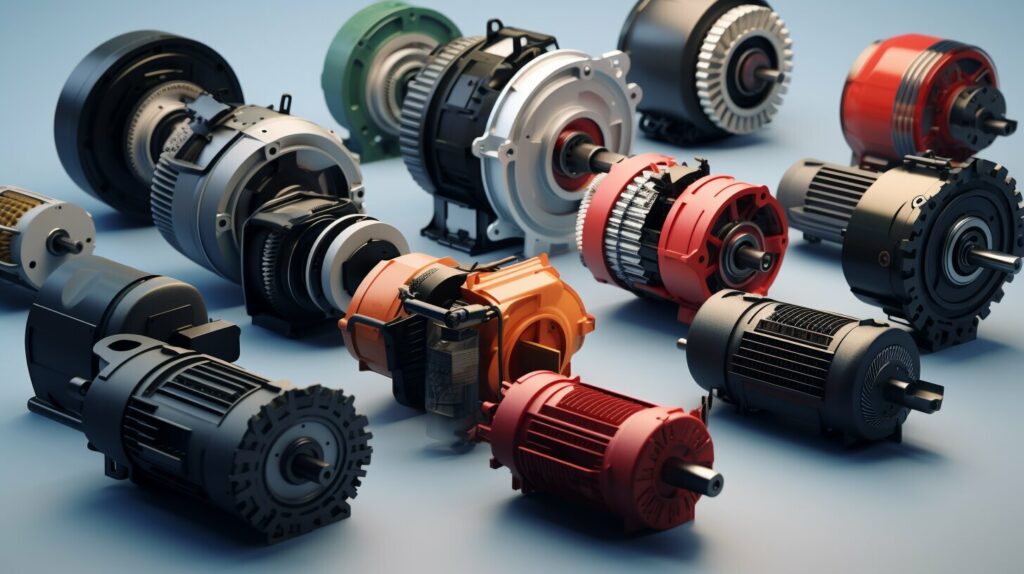
“The type of electric motor housing used will depend on the specific motor’s requirements and application.”
Both aluminum alloy and cast iron motor housing have their advantages and are suitable for different applications. It’s important to choose the correct type of housing to ensure the motor’s longevity and optimal performance.
The Electric Motor Housing Manufacturing Process
Manufacturing high-quality electric motor housing is crucial for protecting components and ensuring longevity. At our company, we use state-of-the-art methods for producing top-grade housing.
One common method we utilize is aluminum extrusion, which involves heating and pushing aluminum through a mold to create the desired shape. This method is ideal for producing complex shapes and designs with high precision and consistency.
Another technique we use is die casting, where molten metal is injected into a mold under high pressure. This method is particularly suitable for creating housing with intricate details and complex geometries.
Both techniques result in durable and efficient housing that provides optimal protection and performance for electric motors.
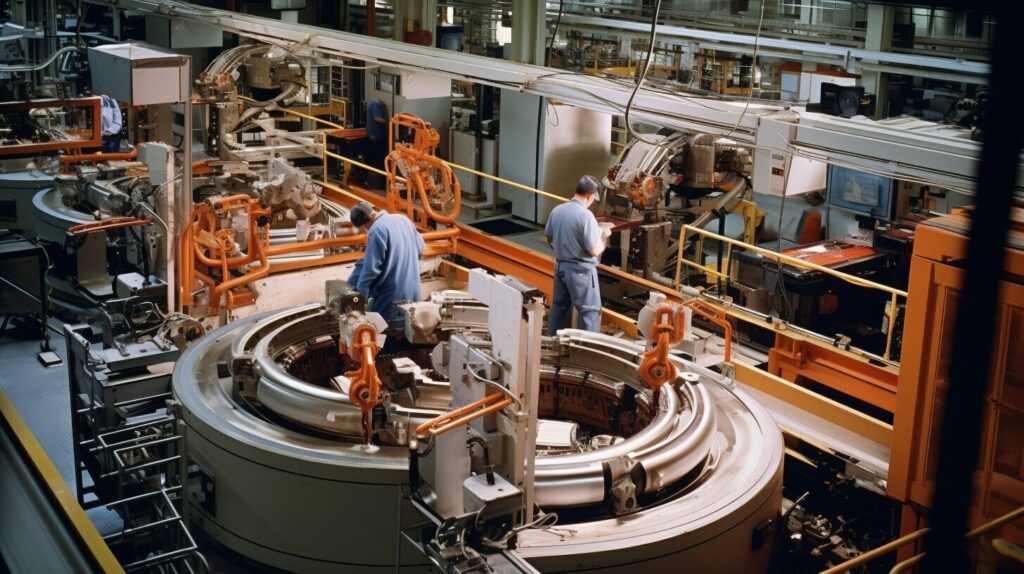
We use state-of-the-art manufacturing techniques such as aluminum extrusion and die casting to ensure our electric motor housing is of the highest quality.
Cooling Channels for Enhanced Performance
One of the critical components of electric motor housing is the cooling channels. These channels play a vital role in maintaining the temperature of the motor and ensuring its optimal performance.
Direct cooling is an effective way of regulating the temperature in the housing. This process involves circulating the coolant directly through the cooling channels, which are designed to optimize heat transfer, reducing thermal resistance, and improving efficiency.
The temperature control provided by the cooling channels helps to prolong the service life of the motor. Without adequate cooling, the motor may overheat, leading to damage to the components, and ultimately reducing the lifespan of the motor.
Advantages of Direct Cooling: | |
---|---|
Improved heat transfer | |
Reduced thermal resistance | |
Optimized efficiency |
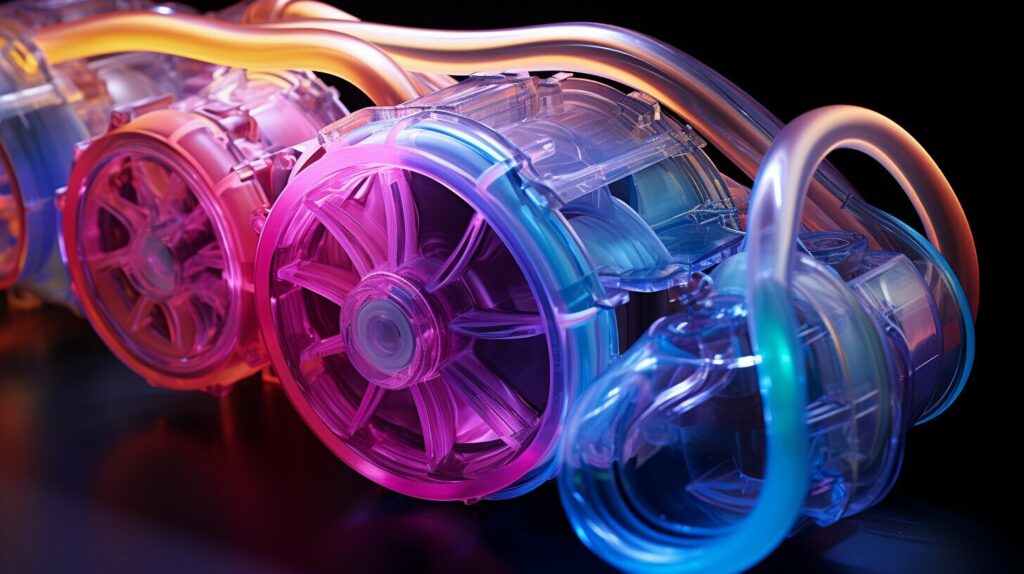
In addition to direct cooling, there are other cooling methods used in electric motor housing, such as indirect cooling. However, direct cooling is the most effective way of cooling the motor, providing a better temperature control system.
Thus, it is essential to design the cooling channels in electric motor housing carefully. The size and shape of the channels, as well as their placement, must be optimized to ensure efficient heat transfer and optimal cooling.
Overall, the cooling channels are a critical component of electric motor housing, ensuring optimal performance and prolonging the service life of the motor.
Mounting Holes and Integration
Mounting holes play a crucial role in electric motor housing, allowing for easy installation and support. For example, our electric traction motors utilize four mounting holes for secure integration into the vehicle’s system.
These holes are strategically placed to distribute weight evenly, reducing stress on the motor and increasing its service life. In addition, proper integration ensures efficient and effective operation of the motor, contributing to the overall performance of the vehicle.
Mounting holes in electric motor housing contribute to increased service life and efficient operation.
The Role of Electric Motor Housing in Electric Vehicles
In electric vehicles, the role of electric motor housing is crucial to ensuring optimal motor performance and longevity. This is because electric motors in these vehicles operate in demanding conditions, with high operating temperatures and frequent starts and stops.
One way electric motor housing contributes to the efficiency of electric vehicles is through the use of ultrasonic methods during the manufacturing process. This non-destructive testing method ensures the housing is free from defects that could compromise performance. It also allows for the use of thinner materials, reducing the weight of the housing and improving fuel efficiency.
Another important factor in electric motor housing for electric vehicles is the increase in surface area. This allows for better heat dissipation, which is crucial in these high-performance motors. The design of the housing incorporates cooling channels to ensure the motor operates within a desirable temperature range, further contributing to improved performance and longevity.
Overall, electric motor housing plays a critical role in electric vehicles. By using ultrasonic methods and increasing surface area, the motor housing provides the necessary protection and cooling to enhance motor performance and efficiency. With the continuing growth of the electric vehicle market, the role of electric motor housing will only become more important in the future.
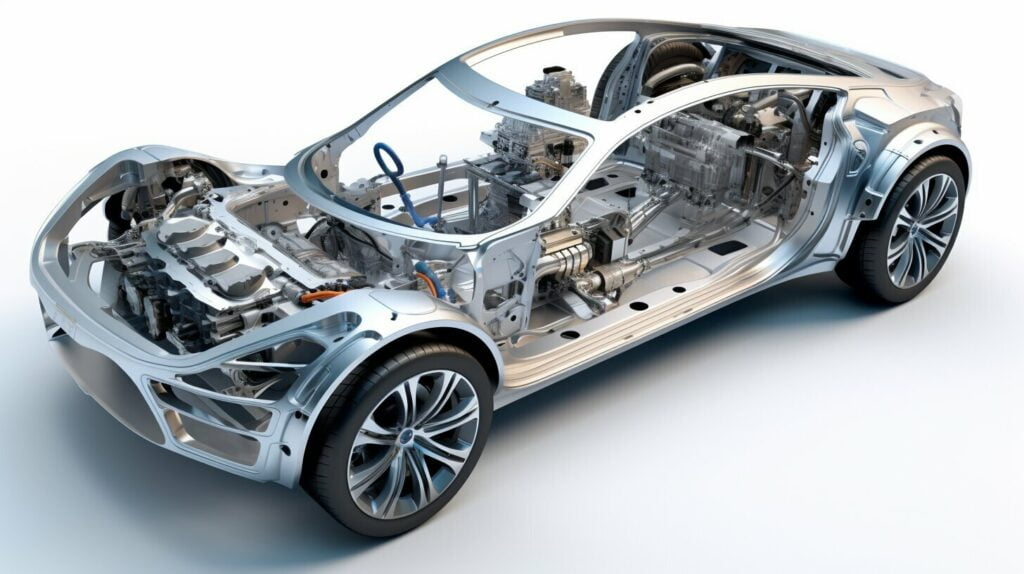
Conclusion
In conclusion, we have explored the importance of electric motor housing in providing quality protection for motors. We have discussed the different types of housing, including those made from aluminum alloy and cast iron, and the manufacturing process through aluminum extrusion and die casting. Additionally, we highlighted the significance of cooling channels, mounting holes, and integration, particularly for electric traction motors.
We have also emphasized the crucial role of electric motor housing in electric vehicles, where ultrasonic methods and increased surface area contribute to the efficiency and performance of electric motors. Quality protection of the main components is essential for optimal operation, and electric motor housing is a key component in enhancing the longevity and service life of motors.
KT-Foundry’s ability to meet and exceed customer needs by delivering top-quality electric motor housings with promptness and precision has solidified its position as a preferred supplier in the industry.
FAQ
Q: What is electric motor housing and why is it important?
A: Electric motor housing refers to the protective covering or enclosure for electric motors. It is essential in providing quality protection for motors by safeguarding the main components from external damage and environmental factors. This protection is crucial for ensuring the service life and optimal performance of electric motors.
Q: What are the different types of electric motor housing?
A: There are two common types of electric motor housing: aluminum alloy and cast iron. Aluminum alloy housing offers lightweight and corrosion-resistant characteristics, while cast iron housing provides durability and improved heat dissipation capabilities.
Q: How is electric motor housing manufactured?
A: Electric motor housing is manufactured using various methods, including aluminum extrusion and die casting. Aluminum extrusion involves shaping the housing by forcing molten aluminum through a die, while die casting involves pouring molten metal into a mold to create the housing shape.
Q: What is the role of cooling channels in electric motor housing?
A: Cooling channels in electric motor housing play a crucial role in enhancing performance. They allow for efficient heat dissipation, helping to regulate the temperature of the motor and prevent overheating. Direct cooling is particularly beneficial in improving the overall performance and service life of the motor.
Q: Why are mounting holes important in electric motor housing?
A: Mounting holes in electric motor housing are vital for easy installation and support. They allow for secure mounting of the motor in various applications and provide stability during operation. Electric traction motors, in particular, benefit from the integration of mounting holes for seamless integration into electric vehicles.
Q: How does electric motor housing contribute to electric vehicles?
A: Electric motor housing plays a significant role in electric vehicles. The use of ultrasonic methods and increased surface area in the housing design improves the efficiency and performance of electric motors. It enables better heat dissipation and protects the motor’s main components, ensuring optimal operation in electric vehicles.