When it comes to tough and durable materials, white cast iron is a top contender. This versatile material has the ability to handle heavy loads and high stress, making it a popular choice in a variety of industries.
White cast iron is produced through a unique manufacturing process that results in a material with a high carbon content. This makes it much stronger and harder than other Various types of cast iron exist, including grey cast iron.These properties make it highly resistant to wear and tear, giving it a long lifespan.
Whether you’re looking for a material that can withstand high temperatures, survive harsh environments, or handle heavy loads, white cast iron is a reliable and effective choice. Keep reading to learn more about this unique material and its many applications.
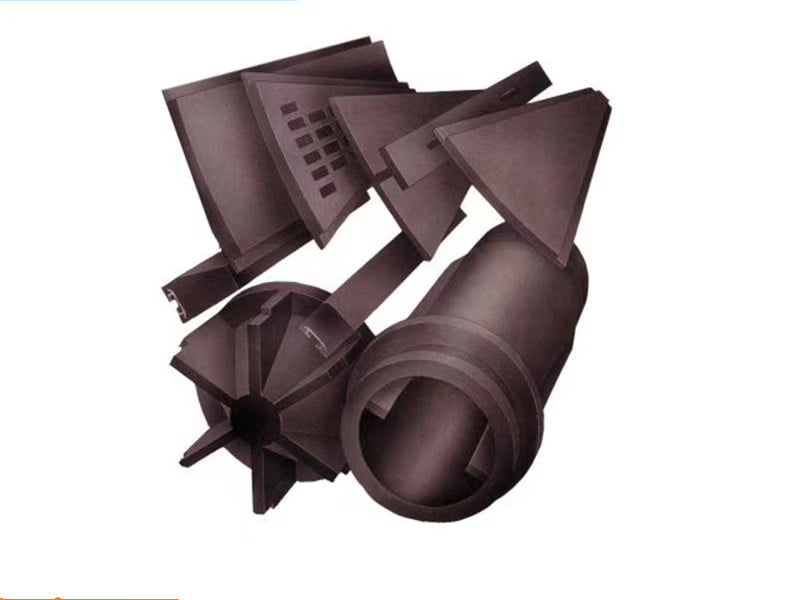
Understanding White Cast Iron and Its Composition
White cast iron is a variety of cast iron renowned for its exceptional strength and hardness. It is different from other types of cast iron, such as grey cast iron and malleable cast iron. The composition of white cast iron consists of iron carbide, which gives it its unique properties.
Iron carbide is a compound that forms when iron and carbon combine. In white cast iron, the carbon content is higher than in other types of cast iron, leading to the formation of hard, brittle iron carbide.
White cast iron also contains white cast iron precipitates, which are small, needle-like structures that form during the cooling process.
Type of Cast Iron | Carbon Content | Properties |
---|---|---|
White Cast Iron | 1.8% – 3.6% | Hard, brittle, wear-resistant |
Grey Cast Iron | 2.5% – 4.0% | Good machinability, excellent damping capacity |
Malleable Cast Iron | 2.2% – 2.8% | Ductile, low melting point, high ductility |
Grey cast iron and malleable cast iron have lower carbon content than white cast iron, which gives them different properties. Grey cast iron is known for its excellent damping capacity, while malleable cast iron is more ductile and has a lower melting point.
Fun Fact: White cast iron is called “white” because, unlike grey cast iron, it does not contain graphite flakes that give grey cast iron its distinct color.
Properties and Advantages of White Cast Iron
White cast iron is renowned for its remarkable strength and durability, which has led to its widespread use in a diverse range of industrial applications.. One of the key properties of white cast iron is its high wear resistance, which is achieved through the presence of hard, brittle iron carbide. This makes white cast iron particularly useful for components that are subject to high levels of wear and tear, such as those used in mining equipment, crushers, and ball mills.
White cast iron can be produced in a range of cast iron types, including unalloyed cast iron, as well as alloyed cast iron with increased impact resistance, abrasion resistance, and corrosion resistance. This versatility allows for a wide range of potential applications.
Another advantage of white cast iron is its ability to maintain its structural integrity under high stress and extreme temperatures. This makes it an ideal choice for use in components that must withstand significant amounts of pressure, such as valves, fittings, and piping.
Due to its exceptional strength and durability, white cast iron is also a popular choice for use in the production of cast iron cookware. The high wear resistance of white cast iron ensures that such products will not be easily damaged or worn down with regular use, making them a valuable investment for the kitchen.
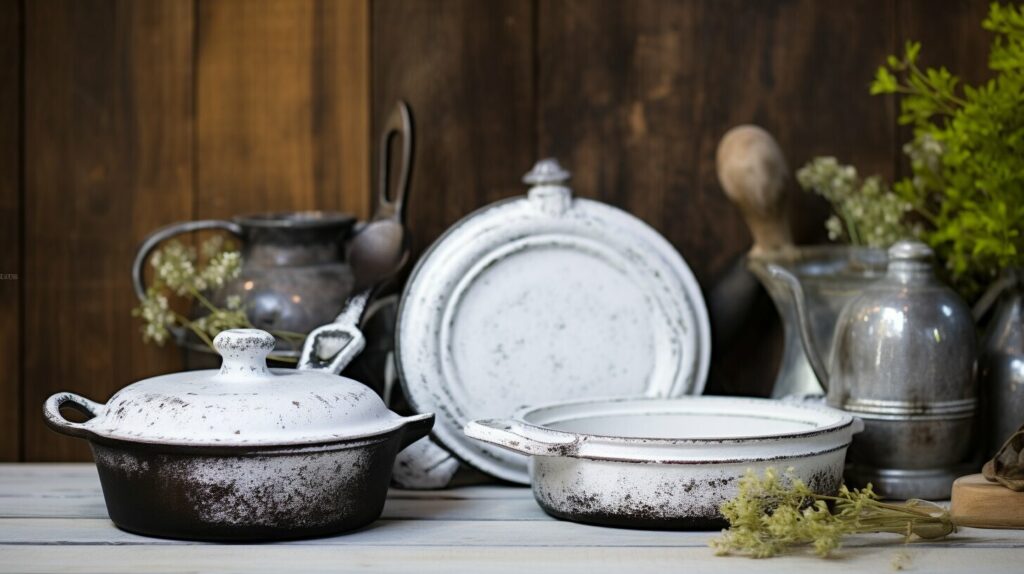
Overall, the unique properties and advantages of white cast iron make it a valuable material for a wide range of industrial and consumer applications. Its high wear resistance, versatility, and ability to withstand extreme pressure and temperature make it a popular choice in industries ranging from manufacturing to construction to transportation.
Applications of White Cast Iron
White cast iron’s exceptional hardness and abrasion resistance make it useful in a variety of industrial applications.
One of the most common uses of white cast iron is in the production of cast iron cookware. The high carbon content and excellent heat retention of white cast iron make it ideal for cooking at high temperatures.
White cast iron is also used in the production of malleable iron. By heat treating white cast iron, it can be converted into malleable iron with lower brittleness and higher ductility.
Thanks to its superior abrasion resistance, white cast iron is also used in the production of wear-resistant components such as pump parts, grinding balls, and crushing equipment. It is particularly useful in applications where impact and high-velocity friction are present.
Additionally, unalloyed white cast iron is often used in industries such as mining, construction, and oil and gas for its ability to withstand harsh environments and heavy loads.
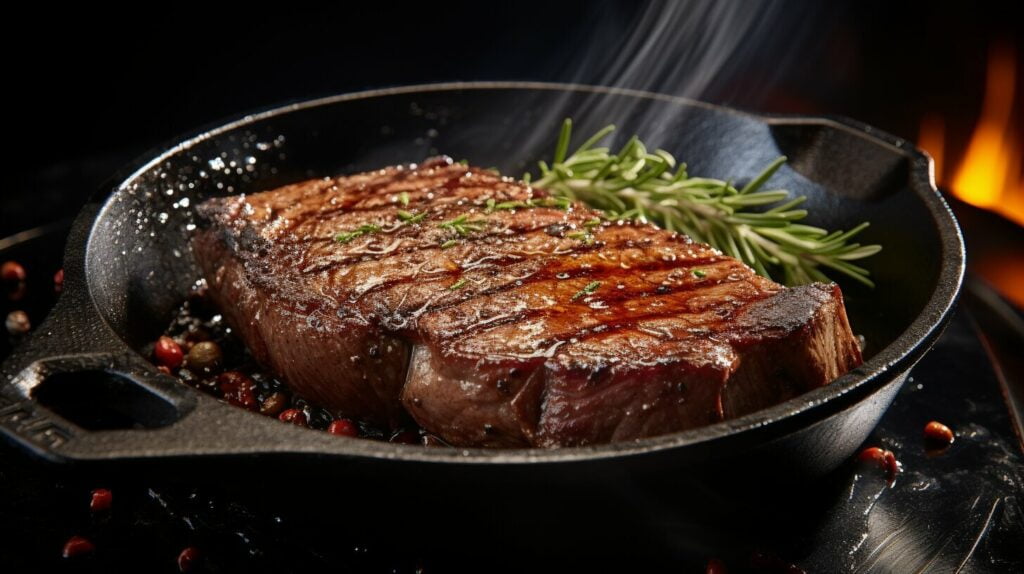
Cast iron cookware is just one example of the wide range of applications for white cast iron.
Production and Heat Treatment of White Cast Iron
White cast iron is produced through the same process as other types of cast iron, with adjustments made to the composition of the alloy. To create white cast iron, the iron must have a high carbon content, typically between 2.0% and 4.0%. The high carbon content causes the iron to solidify quickly and form the hard, brittle iron carbide that characterizes white cast iron.
Heat treatment is an important process in the production of white cast iron. In particular, quenching and tempering are commonly used heat treatment methods to improve the mechanical properties of the iron. Quenching involves rapidly cooling the iron after it has been heated. This process causes the iron to become harder but also more brittle. To counteract the brittleness, tempering is used to slightly reduce the hardness while increasing the toughness and ductility of the iron.
It is also possible to create ductile cast iron from white iron through a process known as austempering. Austempering involves heating the iron to a specific temperature and holding it for a set amount of time before rapidly cooling it. This process causes the white iron to transform into a more ductile form, making it more suitable for certain applications.
Overall, the production and heat treatment of white cast iron requires careful control of the alloy composition and precise heat treatment methods to achieve desirable mechanical properties.
At KT-foundry, we take immense pride in our expertise in white iron casting, providing top-quality solutions for various industries. One of our flagship products is the high-performance brake drums used in trains.
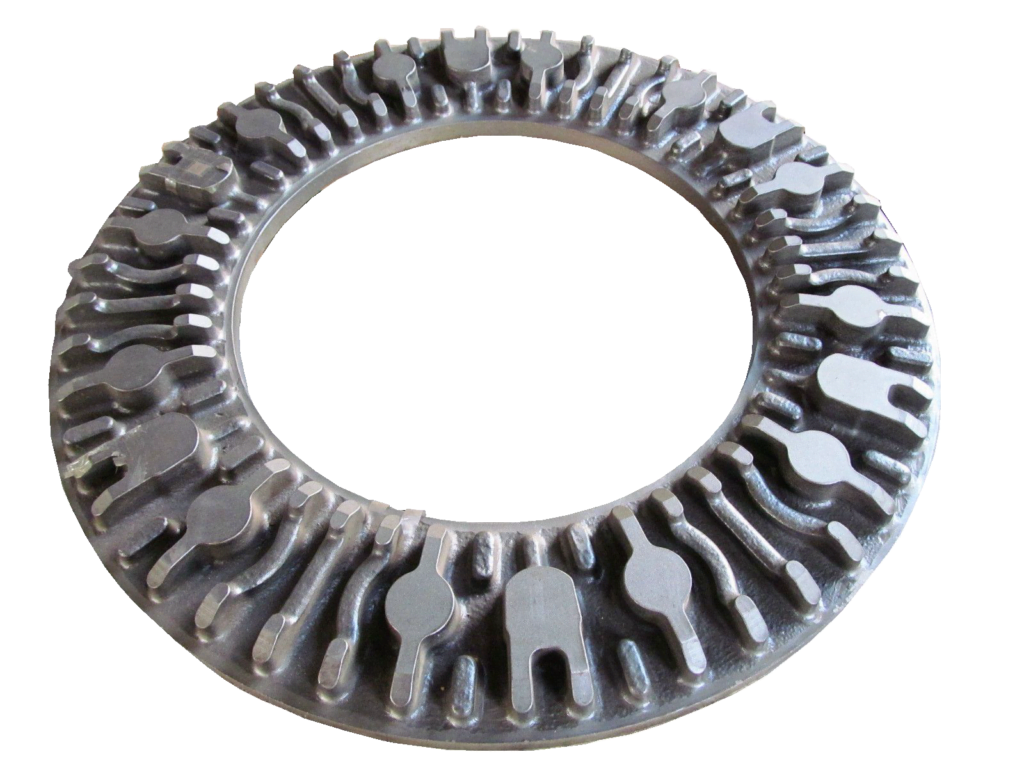
Table 1: Common Heat Treatment Methods for White Cast Iron
Heat Treatment Method | Description |
---|---|
Quenching | Rapid cooling of iron to increase hardness |
Tempering | Reduces hardness and increases toughness and ductility |
Austempering | Heating and cooling process that transforms white iron into a more ductile form |
Structure and Microscopy of White Cast Iron
White cast iron gets its name from its characteristic white surface colour. It is a brittle material with high hardness due to the presence of iron carbide and graphite flakes. The presence of these elements gives white cast iron a unique microstructure, which can be examined using microscopy.
When viewed under a microscope, white cast iron exhibits a white, crystalline structure with visible graphite flakes. These flakes interrupt the iron carbide network, creating voids and reducing the ductility of the material. The flakes also give the material its characteristic appearance and contribute to its hardness.
The formation of iron carbide in white cast iron can also be observed under a microscope. Iron carbide forms in the eutectic mixture within the material, where it exists in the form of plates or needles. These iron carbide precipitates interfere with crack propagation, contributing to the material’s high strength and wear resistance.
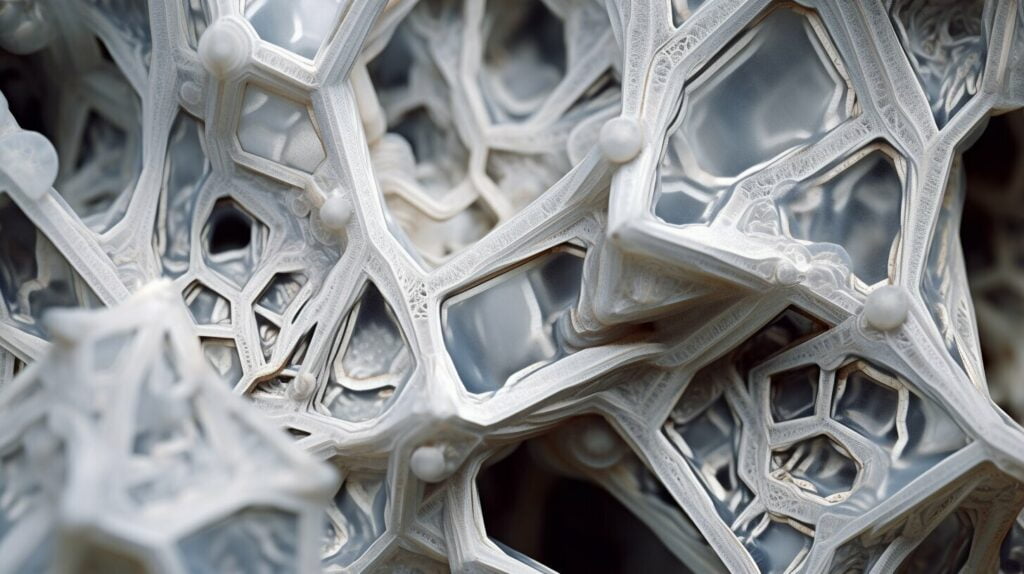
Microscopy is an essential tool for examining the properties and structure of white cast iron, providing valuable insight into its unique characteristics. By understanding the microstructure of white cast iron, engineers and metallurgists can design and optimize the material for specific industrial applications.
Strength and Durability of White Cast Iron in Industrial Applications
White cast iron is renowned for its exceptional strength and durability, making it a popular choice for a wide range of industrial applications. From structural components to molten iron, white cast iron consistently demonstrates its durability and resistance to wear.
One of the key advantages of white cast iron is its bulk hardness, which allows it to withstand high levels of wear and tear without deformation or damage. This makes it an ideal material for use in industrial applications where strength and durability are crucial.
White cast iron is commonly utilized in the production of structural components, It can be used in applications such as the worn surfaces of slurry pumps (impels and volutes), housing linings and lifting rods in ball mills and autogenous mills, balls and rings in coal mills, and teeth of backhoe diggers (although carbon martensitic steel is more common in casting).Its high strength-to-weight ratio enables it to withstand heavy loads and mechanical stress without compromising performance or structural integrity.
Additionally, the hardness properties of molten white cast iron make it a popular choice for use in foundries and other manufacturing processes. Its resistance to wear and deformation make it well-suited for use in high-temperature environments where other materials may not be able to withstand the stress.
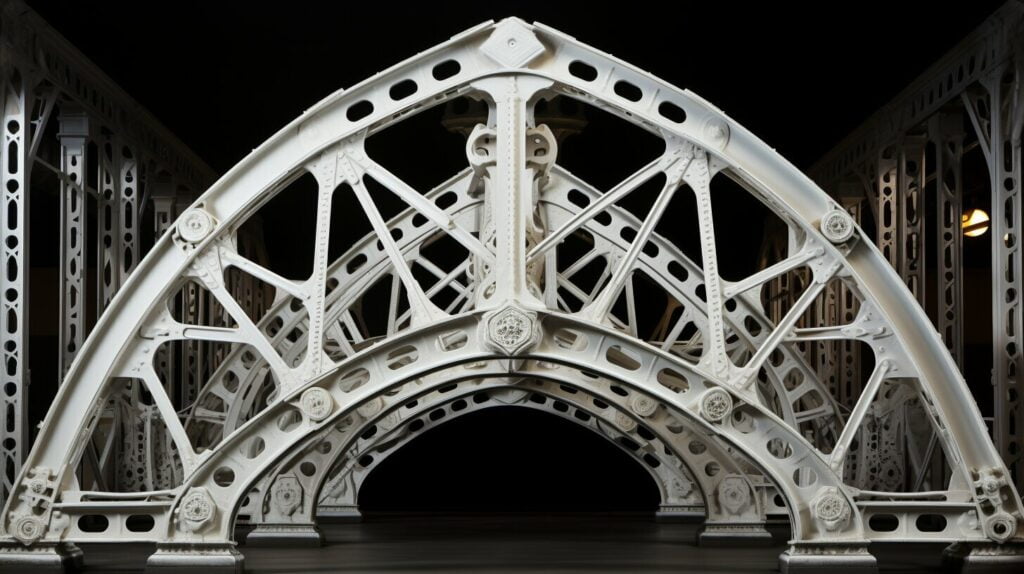
Overall, the strength and durability of white cast iron make it an excellent choice for a variety of industrial applications. Its ability to withstand high levels of wear and maintain its structural integrity over time make it an essential material for industries ranging from manufacturing to construction.
Frequently Asked Questions about White Cast Iron
As white cast iron is a highly specialized material, it’s normal to have questions about its composition, properties, and applications. Below are some of the most commonly asked questions about white cast iron, answered by our experts.
What is white cast iron?
White cast iron is a type of cast iron that contains high levels of carbon, typically between 2.0% to 3.5%. It is named after its white, shiny appearance, which is the result of the presence of iron carbide in the alloy.
What are the advantages of using white cast iron?
White cast iron offers numerous advantages, including excellent wear resistance, high hardness, and low melting point. It’s also versatile in terms of the types of cast iron it can be produced in and is often used in applications where abrasion resistance is critical.
Is white cast iron brittle?
Yes, white cast iron is brittle due to the hardness of the iron carbide within the alloy. However, this brittleness can be minimized through careful heat treatment processes.
What industries commonly use white cast iron?
White cast iron has a wide range of applications across several industries, including automotive, mining, and oil and gas. It is also frequently used in the production of malleable iron and cast iron cookware.
Can white cast iron be welded?
Due to its high carbon content, welding white cast iron can be difficult. However, it is possible to weld white cast iron with specialized techniques and equipment.
How is white cast iron produced?
White cast iron is typically produced by casting molten iron into a mold. The cooling process must be carefully controlled to avoid the formation of graphite flakes, which would result in the production of grey cast iron instead.
What is the difference between white cast iron and grey cast iron?
The primary difference is their carbon content and corresponding microstructures. Grey cast iron has a lower carbon content and contains graphite flakes, while white cast iron has higher carbon content and contains iron carbide precipitates. Grey cast iron is often used for applications that require high thermal conductivity, while white cast iron is used for applications that require high wear resistance.
We hope these answers have provided a helpful overview of white cast iron. If you have any additional questions, feel free to reach out to our team of experts.