Metal casting is a 7,000-year-old process used in manufacturing and fine art. It involves transferring molten metal into a mold to create a positive metal cast object. Metal casting has been used throughout history to create sculptures, jewelry, transportation, weapons, and tools. There are various metal casting processes, including investment casting, sand casting, shell molding, centrifugal casting, and continuous casting.
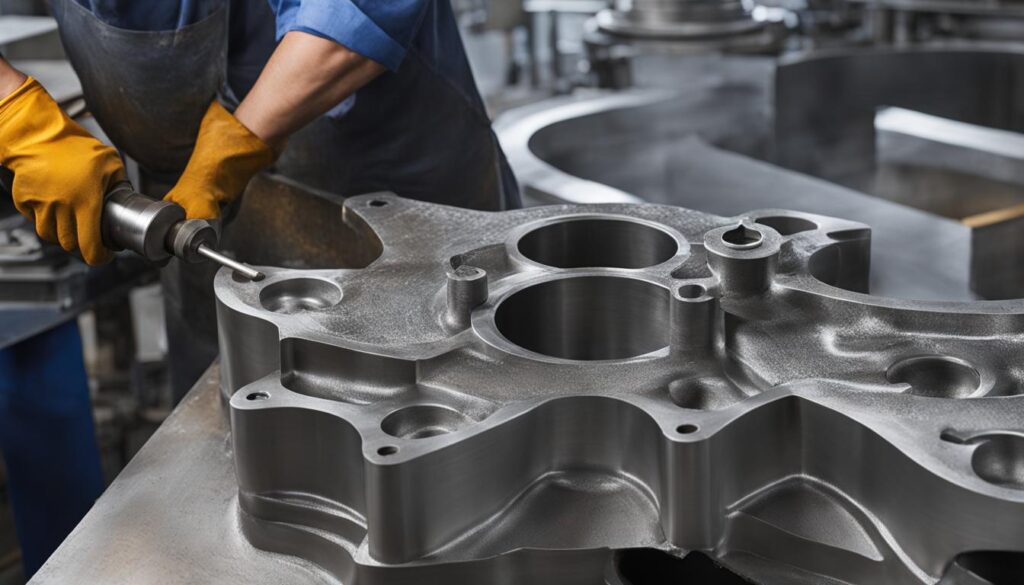
Key Takeaways:
- Investment casting, sand casting, shell molding, centrifugal casting, and continuous casting are different steel casting processes.
- Metal casting is a ancient process used in both manufacturing and fine art.
- Metal casting is used to create a wide range of objects, from sculptures to transportation vehicles.
- Each steel casting process has its advantages and is suited for different casting needs.
- Choosing the right steel casting process depends on factors such as component complexity, quantity, budget, and desired properties.
What is Metal Casting?
Metal casting is an ancient process that has been used for thousands of years in both manufacturing and fine art. It involves transferring molten metal into a mold to create a positive metal cast object. This versatile technique has been employed to produce a wide range of items, including sculptures, jewelry, transportation vehicles, weapons, and tools.
Traditional metal casting techniques encompass lost-wax casting, plaster mold casting, die casting, and sand casting. Lost-wax casting, also known as investment casting, is a method that yields precise and detailed components. Plaster mold casting involves creating a mold from plaster and pouring molten metal into it. Die casting utilizes reusable molds, allowing for the fast production of consistent components. Finally, sand casting is a cost-effective process that can be used for both small and large-scale production, providing flexibility in terms of sizes, shapes, and materials.
Overall, metal casting is a fundamental process that has played a significant role in shaping our history and continues to be an essential technique in both manufacturing and artistic endeavors. The ability to mold molten metal into specific forms has allowed for the creation of intricate and durable objects that serve various purposes.
Metal casting is an ancient process that allows us to transform molten metal into positive metal cast objects. It has been used for thousands of years in manufacturing and fine art. With techniques like investment casting, plaster mold casting, die casting, and sand casting, we can create precise components, produce consistent parts rapidly, and work with a wide range of materials. Metal casting is a vital process that has shaped our world and will continue to be a cornerstone of manufacturing and creativity.
Different Types of Metal Casting
When it comes to metal casting, there are various methods and techniques that can be employed. The choice of casting process depends on factors such as the complexity of the component, the desired quantity, budget constraints, and the specific properties required. Here are some of the different types of metal casting:
Process | Description |
---|---|
Investment Casting | A process that uses a wax pattern and ceramic mold to create highly detailed and intricate components. |
Plaster Mold Casting | A process that involves creating a mold from plaster and pouring molten metal into it. |
Die Casting | A process that uses reusable molds, known as dies, to rapidly produce consistent components. |
Sand Casting | A cost-effective process that utilizes sand molds to cast a wide range of shapes and sizes. |
Uses of Metal Casting
Metal casting has been a valuable process throughout history, serving a wide range of purposes in various industries. This versatile technique has been used to create tools, weapons, and religious objects, among other things. It offers a cost-effective solution for manufacturing complex shapes and can easily produce multiple copies of the same object.
One of the key advantages of metal casting is its ability to create intricate designs and detailed components. This makes it suitable for producing tools and weapons with specific functionalities. Additionally, metal casting allows for the creation of religious objects that have symbolic significance, often requiring complex and unique shapes.
Furthermore, metal casting plays a vital role in the manufacturing industry, catering to a diverse range of needs. It is commonly used in the production of household appliances, construction equipment, electrical components, farming equipment, and defense weapons. The versatility of metal casting enables manufacturers to create objects with different shapes, sizes, and structures to meet specific requirements.
In conclusion, metal casting has widespread applications, ranging from creating tools and weapons to manufacturing complex and unique objects. Its cost-effectiveness, ease of replication, and ability to produce intricate designs make it an invaluable process in various industries.
Different Types of Metal Casting
When it comes to metal casting, there are two main types of processes: those with expendable molds and those with non-expendable molds. Expendable mold casting involves the use of single-use molds made from materials like sand, ceramic shell, or plaster. These molds are destroyed after each casting, hence the name “expendable.” On the other hand, non-expendable mold casting utilizes reusable molds made from metals like steel or cast iron.
Expendable mold casting processes, such as sand casting and shell molding, are commonly used for producing large and complex parts. They offer flexibility in terms of shape and design and are often favored for their cost-effectiveness. However, the surface finish achieved with these processes may not be as smooth as with non-expendable mold casting.
Non-expendable mold casting processes, such as investment casting and die casting, are known for their ability to produce highly detailed and precise components. These processes are typically used for smaller parts that require intricate designs and tight tolerances. Non-expendable mold casting provides a smoother surface finish and allows for better control over the final product.
Expendable Mold Casting | Non-Expendable Mold Casting |
---|---|
Sand casting | Investment casting |
Shell molding | Die casting |
Centrifugal casting | |
Continuous casting |
Each type of metal casting process has its own advantages and is suited for different casting needs. The choice between expendable and non-expendable mold casting depends on factors such as the size, complexity, and quantity of the desired components, as well as the budget and desired properties of the final product. Consulting with casting experts can help determine the most suitable method for a specific project, ensuring optimal results.
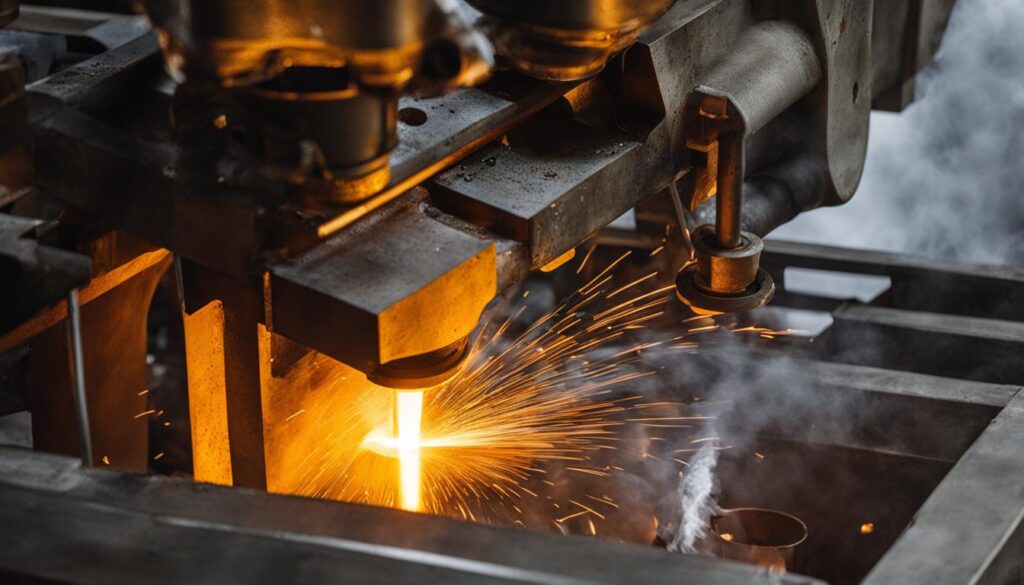
The Basic Metal Casting Process
Metal casting is a fascinating process that involves several steps to transform molten metal into a solid casting. Understanding the basic metal casting process is essential to appreciate the intricacies involved in creating a wide range of metal objects, from industrial components to intricate artwork.
To create a pattern: The first step in the metal casting process is to create a pattern of the desired shape. This pattern serves as a template or model for the final casting. Patterns can be made from various materials, including wood, plastic, or metal, depending on the complexity and size of the object.
To make the mold: Once the pattern is ready, a mold is created around it. The mold can be made from materials like sand, plaster, or ceramic, depending on the type of casting process being used. The mold must be designed to allow the molten metal to flow into it and form the desired shape.
To choose the metallic alloy: The next step is to select the appropriate metallic alloy for the casting. Different alloys have varying properties, such as strength, hardness, and corrosion resistance. The choice of alloy depends on the specific requirements of the object being cast.
To melt the alloy and pour into the mold: Once the mold is prepared and the alloy is chosen, the metallic alloy is melted in a furnace at high temperatures. Once in a molten state, the alloy is poured into the mold, filling the space previously occupied by the pattern. It is crucial to ensure a smooth and controlled pour to avoid defects in the final casting.
To remove the casting and finishing: After the molten metal has cooled and solidified inside the mold, the casting is removed. The mold is typically broken or removed to reveal the solid metal object. The casting may require further finishing processes, such as cleaning, polishing, or machining, to achieve the desired final appearance and dimensions.
The basic metal casting process involves several intricate steps that require precision and expertise. Each stage plays a crucial role in ensuring the quality and integrity of the final casting. From creating the pattern to pouring the molten metal into the mold and finishing the casting, each step contributes to the creation of unique and functional metal objects.
Advantages of Investment Casting
Investment casting, also known as lost-wax casting, offers several advantages for manufacturing precise components with complex shapes and a smooth surface finish. This casting process is highly versatile and has been used for centuries to create intricate and detailed metal objects.
Advantage 1: Precise Components
Investment casting allows for the creation of highly precise components with intricate details and tight tolerances. This process can capture fine features that may be challenging to achieve with other casting methods. The use of a wax pattern allows for the production of complex shapes, including internal cavities and thin walls.
Advantage 2: Complex Shapes
Investment casting is well-suited for manufacturing parts with complex shapes, such as turbine blades, jewelry, and dental implants. The process allows for the production of intricate designs that are difficult to achieve through other fabrication techniques. It offers design flexibility and the ability to create near-net shape components, reducing the need for extensive machining.
Advantage 3: Smooth Surface Finish
Investment casting produces castings with a smooth surface finish, minimizing the need for additional machining or finishing operations. The use of a ceramic shell mold results in a high-quality surface that requires minimal post-casting processing. This advantage saves time, cost, and labor, making investment casting an efficient choice for producing components with superior aesthetics.

Advantages of Investment Casting |
---|
Allows for the production of highly precise components |
Enables the creation of complex shapes |
Produces castings with a smooth surface finish |
Advantages of Sand Casting
Sand casting is a widely used metal casting process that offers several advantages in terms of cost-effectiveness, flexibility, and compatibility with both ferrous and non-ferrous metals. This technique involves creating a mold using a mixture of sand and a binder. The mold is then used to produce a wide range of components with varying sizes and shapes.
Sand casting is particularly cost-effective, making it a preferred choice for both small-scale and large-scale production. The materials required for sand casting, such as sand and the binder, are readily available and affordable. Additionally, the process does not require complex machinery or equipment, further reducing production costs.
One of the key advantages of sand casting is its flexibility. It allows for the production of components with complex geometries and intricate details. This makes sand casting suitable for a wide range of applications in various industries, including automotive, aerospace, and construction.
Furthermore, sand casting accommodates both ferrous and non-ferrous metals, providing versatility in material selection. Castings made through this process can be produced using materials such as steel, iron, aluminum, brass, and bronze, among others. This flexibility allows manufacturers to choose the most appropriate material based on the desired properties of the final product.
Advantages of Sand Casting
- Cost-effective: Sand casting is an affordable casting process, making it suitable for both small-scale and large-scale production.
- Flexibility: Sand casting allows for the production of components with complex shapes and intricate details.
- Compatibility with ferrous and non-ferrous metals: Sand casting can be used with a wide range of materials, including steel, iron, aluminum, brass, and bronze.
“Sand casting is a cost-effective solution for both small and large-scale production. It offers flexibility in terms of component sizes and shapes and can work with both ferrous and non-ferrous metals, including steel.”
– Casting Expert
Advantages of Sand Casting | Description |
---|---|
Cost-effective | Sand casting is a cost-effective casting process, making it suitable for various production scales. |
Flexibility | Sand casting allows for the production of components with complex shapes and intricate details. |
Compatibility with ferrous and non-ferrous metals | Sand casting can be used with a wide range of materials, including steel, iron, aluminum, brass, and bronze. |
Advantages of Die Casting
Die casting is a highly efficient process that offers numerous advantages in the production of metal castings. Its precision and fast production rates make it a preferred choice for various industries. With die casting, manufacturers can achieve precise and consistent components, ensuring high-quality castings.
The smooth surface finish achieved through die casting eliminates the need for additional polishing or machining, saving time and resources. The castings produced through this process are known for their strength and durability, making them suitable for applications that require robust components.
Die casting is particularly well-suited for large-scale manufacturing due to its fast production rates. This process enables the creation of complex shapes and intricate details, allowing manufacturers to meet the demands of their customers efficiently.
With die casting, manufacturers can achieve precise and consistent components, ensuring high-quality castings. The smooth surface finish achieved through die casting eliminates the need for additional polishing or machining, saving time and resources. The castings produced through this process are known for their strength and durability, making them suitable for applications that require robust components.
In summary, die casting offers the following advantages:
- Precision: Die casting ensures precise and consistent components.
- Fast production rates: This process enables efficient large-scale manufacturing.
- Smooth surface finish: Die casting eliminates the need for additional polishing or machining.
- Strong and durable castings: The castings produced through die casting are known for their strength and durability.
Die casting is a highly efficient process that offers numerous advantages, including precision, fast production rates, smooth surface finish, and strong and durable castings. It is a preferred choice for industries that require high-quality metal castings with intricate details and complex shapes.
Table: Die Casting Advantages
Advantage | Description |
---|---|
Precision | Die casting ensures precise and consistent components. |
Fast Production Rates | This process enables efficient large-scale manufacturing. |
Smooth Surface Finish | Die casting eliminates the need for additional polishing or machining. |
Strong and Durable Castings | The castings produced through die casting are known for their strength and durability. |
Choosing the Right Steel Casting Process
When it comes to steel casting, selecting the right process is crucial to ensure optimal results. Factors such as component complexity, quantity, budget, and desired properties must be taken into consideration. Let’s explore the different factors to help you make an informed decision.
Component Complexity
The complexity of the component you need to cast plays a significant role in selecting the appropriate steel casting process. Investment casting, also known as lost-wax casting, is well-suited for intricate and detailed components. Its ability to create complex shapes with thin walls and a smooth surface finish makes it a preferred choice for high-precision parts.
On the other hand, sand casting offers cost-effectiveness and flexibility when dealing with components that are less complex. It allows for the production of larger parts and can accommodate a wide range of shapes and sizes.
Quantity
The quantity of castings needed is another crucial factor to consider. If you require a high volume of components, die casting is an excellent option. Die casting utilizes reusable molds and enables fast production rates, making it ideal for large-scale manufacturing.
For smaller quantities, investment casting and sand casting can be more suitable. Investment casting can produce detailed components in smaller quantities, while sand casting offers flexibility and cost-effectiveness for small to medium production runs.
Budget and Desired Properties
Your budget and desired properties of the final castings are vital considerations. Investment casting, although capable of producing high-quality components, tends to be more expensive due to the intricate process involved.
For cost-effective casting solutions, sand casting and die casting are often preferred. Sand casting offers a lower cost per unit compared to investment casting, making it an attractive option for budget-conscious projects. Die casting, while more expensive than sand casting, provides strong and durable castings with minimal post-casting machining required.
Ultimately, the choice of steel casting process depends on the specific requirements of your project. Consulting with experts in the field can provide valuable insights and help you select the most suitable method to achieve your desired outcomes.
Other Steel Casting Processes
In addition to investment casting, sand casting, and die casting, there are other steel casting processes that offer unique advantages and applications.
Continuous Casting
Continuous casting is a process that involves transforming molten metal into solid forms with a continuous feed of material. It is commonly used to produce large, semi-finished castings such as blooms, billets, and slabs. Continuous casting offers several benefits, including improved productivity, better control over the casting process, and the ability to produce castings with consistent dimensions and properties. This process is widely used in the steel industry to create high-quality castings for various applications.
Centrifugal Casting
Centrifugal casting is a method that utilizes the high-speed rotation of a mold to shape liquid metal into seamless castings. This process allows for the production of hollow castings with enhanced mechanical properties, such as improved strength and uniformity. Centrifugal casting is commonly used to manufacture pipes, cylinders, and other symmetrical components where high strength and reliable performance are essential.
Slush Casting
Slush casting is a technique that creates hollow castings by coating the inside of a mold with metal, allowing the excess material to drain out, leaving a thin, shell-like structure. This process is commonly used to manufacture decorative and artistic objects that require intricate details and unique shapes. Slush casting offers the ability to create lightweight and visually appealing castings with smooth finishes, making it suitable for applications in the automotive industry, consumer products, and art.
Steel Casting Process | Advantages |
---|---|
Continuous Casting | Improved productivity, consistent dimensions, and properties |
Centrifugal Casting | Hollow castings, enhanced mechanical properties |
Slush Casting | Intricate details, lightweight, smooth finishes |
Each of these steel casting processes offers unique advantages and is suitable for different applications. The choice of process depends on factors such as the desired casting specifications, material properties, and production requirements. Consulting with casting experts can help ensure the selection of the most suitable steel casting process for specific projects, maximizing efficiency, and achieving high-quality results.
Conclusion
In conclusion, understanding the various steel casting processes is essential for successful manufacturing applications. These processes, including investment casting, sand casting, die casting, continuous casting, centrifugal casting, and slush casting, offer a range of benefits for different needs.
Steel casting processes provide cost-effectiveness, recyclability, high-quality components, and efficient production rates. Whether you require detailed components, cost-effective solutions, or high-volume production, there is a suitable steel casting process for your specific requirements.
Consulting with experts in casting can greatly assist in selecting the most appropriate method for your manufacturing applications. With their expertise, you can ensure that you choose the right steel casting process to achieve the desired results in terms of quality, efficiency, and cost-effectiveness.
FAQ
What is metal casting?
Metal casting is a 7,000-year-old process used in manufacturing and fine art, where molten metal is transferred into a mold to create a positive metal cast object.
What are the uses of metal casting?
Metal casting has been used throughout history to create tools, weapons, religious objects, and various products in manufacturing industries, including household appliances, construction equipment, electrical components, farming equipment, defense weapons, transportation vehicles, and artistic objects.
What are the different types of metal casting?
Metal casting can be categorized into two main types: processes with expendable molds, such as sand casting and shell molding, and processes with non-expendable molds, such as investment casting and die casting.
What is the basic metal casting process?
The basic metal casting process involves creating a pattern of the desired shape, making a mold, choosing the appropriate alloy, melting the alloy, pouring it into the mold, removing the casting once it has cooled and solidified, and finishing the final cast object through cleaning and polishing.
What are the advantages of investment casting?
Investment casting, also known as lost-wax casting, provides precise and detailed components, can create complex shapes with thin walls, and produces a smooth surface finish, reducing the need for additional machining.
What are the advantages of sand casting?
Sand casting is a cost-effective solution for both small and large-scale production, offers flexibility in terms of component sizes and shapes, works with both ferrous and non-ferrous metals, and provides good heat resistance and reliable mechanical properties.
What are the advantages of die casting?
Die casting is a highly efficient process that ensures precise and consistent components, enables fast production rates for large-scale manufacturing, produces castings with a smooth surface finish, and creates strong and durable castings, minimizing the need for post-casting machining.
How do I choose the right steel casting process?
When choosing a steel casting process, factors like component complexity, quantity, budget, and desired properties need to be considered. Investment casting is suitable for detailed components, sand casting offers cost-effectiveness and flexibility, and die casting excels in high-volume production. Consulting with casting experts can help determine the most suitable method for a specific project.
Are there other steel casting processes worth mentioning?
Yes, continuous casting involves transforming molten metal into solid forms, centrifugal casting utilizes high-speed rotation to shape liquid metal into seamless castings, and slush casting creates hollow castings by coating the inside of a mold with metal.
What are the advantages of steel casting processes?
Steel casting processes offer numerous benefits, including cost-effectiveness, recyclability, quality, and speed. Understanding the different methods, such as investment casting, sand casting, die casting, continuous casting, centrifugal casting, and slush casting, can help make informed decisions for various manufacturing needs.
What are the steel casting process applications?
Steel casting processes find applications in manufacturing various products, including household appliances, construction equipment, electrical components, farming equipment, defense weapons, transportation vehicles, and artistic objects.