Carbon steel casting has become an essential technology in various industries, including railroad construction, power generation, and heavy trucks. Its remarkable mechanical properties, weldability, and ability to maintain the mechanical properties of wrought steel in a more flexible form make it an ideal material for many applications. At KT-Foundry, we leverage the design versatility and unique properties of carbon steel castings to optimize part design for improved mechanical performance.
Introduction
As a trusted partner in custom carbon steel casting, we at KT-Foundry work collaboratively with our clients to ensure a harmonized understanding of design specifications and tolerances, helping to optimize the casting design process and material selection for specific applications.
Key Takeaways
- Carbon steel casting offers unique properties and versatility for diverse industrial applications.
- Effective casting design can enhance performance and reduce costs for carbon steel castings.
- KT-Foundry specializes in custom carbon steel casting solutions tailored to client requirements.
- Understanding the relationship between alloying elements, carbon content and casting performance is crucial for successful carbon steel casting projects.
- Heat treatment techniques play a pivotal role in refining the mechanical properties of carbon steel castings.
Introduction to Carbon Steel Casting
In the casting context, carbon steel is an iron-carbon alloy with varying carbon content from 0.0218% to 2.11%, which determines its ultimate strength and hardness. The addition of alloying elements such as silicon, manganese, sulfur, and phosphorus in small amounts further affects its properties. Material selection plays a crucial role in optimizing the mechanical properties for diverse industrial applications.
Carbon steel casting is the process of forming metal shapes by pouring molten carbon steel into pre-formed molds, allowing the steel to cool and solidify into the desired form. This versatile and cost-effective method allows for the creation of custom components without the need for machining or complex assembly processes.
Defining Carbon Steel in the Context of Casting
Carbon steel can be classified into three main categories based on its carbon content:
- Low carbon steel (0.0218% to 0.3% carbon)
- Medium carbon steel (0.3% to 0.6% carbon)
- High carbon steel (0.6% to 2.11% carbon)
The carbon content influences the mechanical properties of the steel, such as its tensile strength, ductility, and shock resistance. Other key properties derive from additional elements in the alloy:
Alloying Element | Effect on Properties |
---|---|
Silicon | Enhances strength and corrosion resistance |
Manganese | Improves strength, hardness, and wear resistance |
Sulfur | Facilitates machinability |
Phosphorus | Improves strength and wear resistance |
KT-Foundry’s Expertise in Carbon Steel Casting
At KT-Foundry, we bring expertise in casting a wide range of carbon steels, including low, medium, and high grades, enhancing specific attributes such as tensile strength, hardness, elasticity, and elongation based on custom requirements. Our precision engineering techniques enable us to manufacture parts with exacting specifications and tolerances.
With our expert foundry services, we collaborate closely with clients to provide tailored advice on material selection, design optimization, and post-processing modifications, ensuring the final product meets their stringent expectations. Our innovative solutions have garnered unique applications among diverse industries such as aerospace, automotive, construction, and heavy machinery.
Choose KT-Foundry for your custom carbon steel casting needs and benefit from our extensive expertise and commitment to quality.
Design Flexibility and Mechanical Proficiency
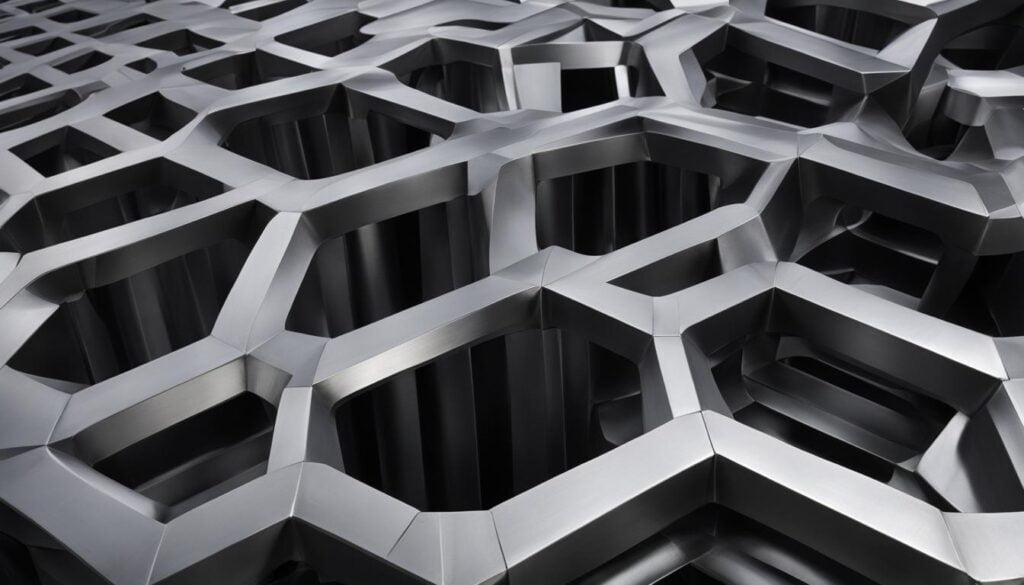
Casting geometry is a critical factor affecting the mechanical performance of carbon steel castings. At KT-Foundry, we understand that the distribution of mass and smooth geometry transitions in a casting part is crucial to ensure optimum performance and cost-effectiveness. Through strategic design adjustments, we can strengthen areas of higher stress and reduce weight without compromising on structural integrity, enabling the creation of castings that effectively meet predefined mechanical and stress requirements.
The Role of Casting Geometry on Performance
Optimizing casting part design requires a thorough understanding of casting geometry, as it has a significant impact on the overall mechanical proficiency. A well-designed casting geometry can enhance performance optimization and enable the creation of components that are both durable and cost-effective. By ensuring a balanced distribution of mass, accurate tolerance specifications, and effective stress concentrations, we can create casting designs that considerably improve the end-use application’s performance and reliability.
Optimizing Design with KT-Foundry’s Engineering Team
KT-Foundry Engineering plays a crucial role in designing castings that surpass industry standards. Our experienced engineers work collaboratively with clients to develop custom engineering solutions that cater to each project’s unique requirements. Their expertise in casting geometry, mechanical proficiency, and design flexibility enables performance enhancement, cost reduction, and the creation of casting parts tailored specifically for their intended application, whether it be automotive components or complex machinery.
Our engineering team at KT-Foundry collaborates closely with clients to ensure the best geometric design for castings, taking into consideration factors such as stress levels, weight optimization, tolerance specifications, and post-processing requirements. This partnership results in castings that not only meet the desired mechanical properties but are also cost-effective and tailored to the end-use application, from automotive components to complex machinery.
Key Factors | Benefits |
---|---|
Optimized Casting Geometry | Improved Mechanical Proficiency |
Design Flexibility | Suitable for a Range of Applications |
Custom Engineering Solutions | Cost-effective & High-performance Castings |
By collaborating with KT-Foundry, clients benefit not only from our optimizing casting design capabilities but also from the ongoing support provided by our engineering team. With a strong emphasis on performance enhancement and cost reduction, we are committed to delivering the highest level of service and support, ensuring that our customers can rely on us for all of their carbon steel casting needs.
Variability in Carbon Content and Alloying Elements
The variability in carbon content and the presence of different alloying elements significantly influence the properties of carbon steel, such as strength, toughness, and weldability. These variables include the type and amount of key alloying elements, including manganese, nickel, chromium, and molybdenum. Understanding the relationship between carbon content, alloying elements, and steel properties is essential for determining the optimal casting composition that meets specific industrial applications.
At KT-Foundry, we collaborate with our clients to navigate this complexity by providing customized recommendations based on their unique project requirements. We help clients identify optimal carbon and alloy levels, ensuring the right combination to achieve the necessary hardenability and mechanical properties for their casting applications.
By controlling the interplay between carbon content and alloying elements, we ensure a balance between performance and cost for KT-Foundry clients.
Let’s delve into the key alloying elements and their effects on steel properties:
- Manganese: An essential alloying element, manganese increases strength, hardenability, and wear resistance, particularly advantageous in reducing deformation.
- Nickel: Often added to improve toughness and impact resistance, nickel enhances the steel’s ability to withstand dynamic loads without cracking or failing.
- Chromium: Chromium increases hardenability and corrosion resistance, making it an essential element in applications that require added durability and longevity.
- Molybdenum: This element further increases steel’s hardenability and adds heat resistance properties, valuable when high-temperature performance is crucial.
Our team of experts at KT-Foundry carefully evaluates these factors and advises on the ideal combination of carbon content and alloying elements to ensure the desired steel properties are met. In doing so, we deliver precise, application-specific solutions that balance performance and cost.
Alloying Element | Primary Effect on Steel Properties | Common Applications |
---|---|---|
Manganese | Strength, hardenability, wear resistance | High-stress components, wear-resistant parts |
Nickel | Toughness, impact resistance | High-impact components, machinery subject to dynamic loads |
Chromium | Hardening, corrosion resistance | Components in corrosive environments, cutting tools, and bearings |
Molybdenum | Heat resistance, hardenability | High-temperature components, aerospace applications |
Ultimately, our commitment to precision engineering and in-depth knowledge of the complex relationships between carbon content variability and alloying elements enable KT-Foundry to deliver high-quality, customized steel casting solutions for our clients.
Heat Treatment’s Effect on Carbon Steel Casting
Heat treatment plays a pivotal role in determining the final microstructure and mechanical properties of carbon steel castings. By controlling the heating and cooling rates, KT-Foundry manipulates the steel’s microstructure to improve properties such as strength, ductility, and toughness.
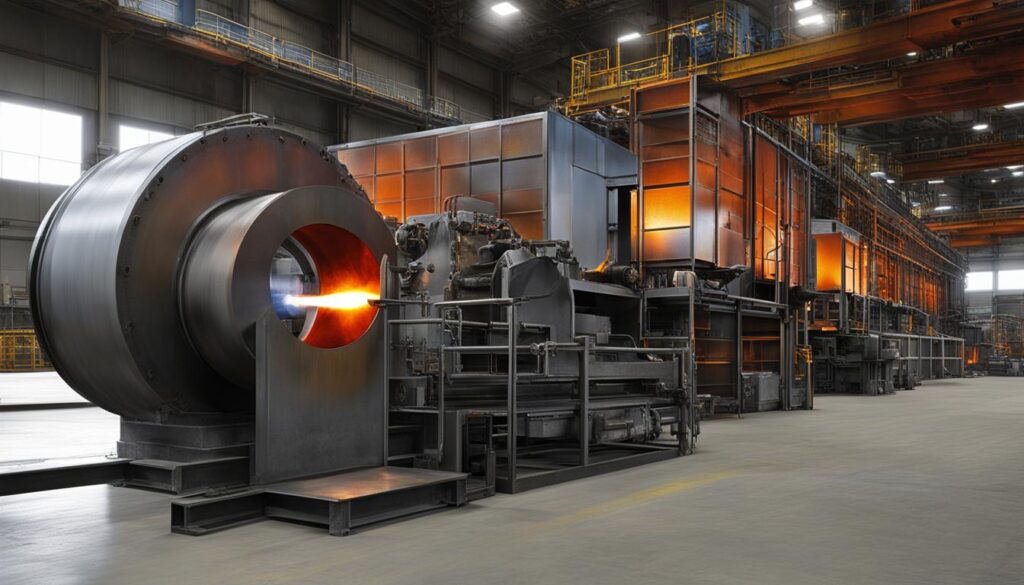
Understanding Hardenability and Microstructure Adjustments
Hardenability is the ability of carbon steel to be hardened during heat treatment. In carbon steel casting, hardenability is enhanced by adding particular alloying elements and manipulating the steel’s microstructure. The microstructure adjustments are achieved through various heat treatment techniques like annealing, normalizing, and quenching and tempering, resulting in uniform hardness, even for thicker sections.At KT-Foundry, we optimize the heat treatment processes to enhance hardenability and mechanical property enhancement in carbon steel castings.
Balancing Mechanical Properties through Heat Treatment Techniques
Carbon steel castings require a balance of mechanical properties to meet specific service conditions, such as fatigue, wear, and impact resistance. KT-Foundry masters the art of balancing these properties through sophisticated heat treatment techniques:
- QT Processes: The Quenching and Tempering (QT) processes involve rapid cooling of steel followed by heating at a lower temperature. These techniques result in desired levels of tensile strength, elongation, and reduction of area.
- Annealing: This heat treatment technique softens the steel and enhances its ductility by heating the material to a particular temperature and then slowly cooling it.
- Normalizing: This process involves heating steel to a temperature above its critical point and then air cooling it. The result is a refinement of the grain structure, leading to improved strength and toughness.
We meticulously adjust the temperature and duration of heat treatments to refine properties and achieve the specific mechanical property enhancement required by our clients. With KT-Foundry’s process control expertise, our clients are guaranteed custom-engineered carbon steel castings that outperform industry standards.
Heat Treatment Technique | Primary Objective | Typical Applications |
---|---|---|
QT Processes | Improve tensile strength, elongation, and reduction of area | Automotive, railways, construction, mining equipment |
Annealing | Soften steel and enhance ductility | Industrial machinery, automotive components, aerospace |
Normalizing | Refine grain structure to achieve improved strength and toughness | Heavy-duty machinery, shipbuilding, oil-and-gas equipment |
Carbon Steel Casting Applications and Material Selection
Carbon steel castings provide necessary mechanical properties for a wide range of applications across diverse industries, from industrial machinery with demanding strength and wear requirements to aerospace components requiring precision and reliability. The application diversity of carbon steel castings is a testament to their versatility and performance capabilities.
From Industrial Machinery to Aerospace: Application Diversity
With KT-Foundry expertise in material selection and precision castings, carbon steel finds its use in various applications, such as:
- Industrial Machinery
- Aerospace Components
- Automotive Parts
- Heavy-duty Truck Components
- Power Generation Equipment
- Construction and Infrastructure Components
KT-Foundry offers a breadth of expertise in selecting the right carbon steel grade, balancing factors such as ductility, weldability, and strength requirements with the application-specific demands to ensure optimal performance.
Material Guidance and Selection with KT-Foundry
At KT-Foundry, we specialize in guiding clients through the material selection process for carbon steel castings, considering the application, machinability, weldability, and the component’s strength. Whether it’s choosing between low, medium, or high carbon steel or considering additional alloys for enhanced properties, our expertise in investment casting and heat treatment techniques ensures that our clients receive castings optimized for their unique requirements.
Carbon Steel Type | Carbon Content | Typical Applications |
---|---|---|
Low Carbon Steel | 0.15%-0.30% | Automotive parts, construction components, machinery frames |
Medium Carbon Steel | 0.30%-0.60% | Gears, shafts, rail wheels, aerospace components |
High Carbon Steel | 0.60%-0.99% | High-strength applications, wear-resistant components, springs |
In conclusion, carbon steel castings are a versatile and reliable material choice for a wide range of industrial applications. With the guidance and expertise of KT-Foundry, clients can navigate the complexities of material selection and obtain precisely engineered castings tailored to their unique needs.
Conclusion
In conclusion, the field of carbon steel casting is an exciting space where the versatility and mechanical prowess of carbon steel meet the ingenuity and precision engineering of KT-Foundry. Our comprehensive understanding of carbon steel and its properties ensures that we deliver superior casting solutions that push the boundaries of industrial applications, providing customized casting solutions and paving the way for the future of steel castings.
From the initial design to the final heat treatment, our unwavering commitment to KT-Foundry innovation is evident in our ability to optimize the performance, reliability, and cost-efficiency of our carbon steel castings. This allows us to meet the specific needs and demands of clientele from a wide range of industries.
As the world of carbon steel casting continues to evolve, so too will our capabilities at KT-Foundry. We remain steadfast in our dedication to embracing groundbreaking technologies and refining our expertise, ultimately ensuring our carbon steel casting solutions remain at the forefront of innovation for years to come.
FAQ
What is carbon steel in the context of casting?
In the casting context, carbon steel is an iron-carbon alloy with varying carbon content from 0.0218% to 2.11%, which determines its ultimate strength and hardness. The addition of silicon, manganese, sulfur, and phosphorus in small amounts further affects its properties.
How does casting geometry affect the performance of carbon steel castings?
Casting geometry is a critical factor affecting the mechanical performance of carbon steel castings. The distribution of mass and smooth geometry transitions in a casting part is crucial to ensure optimum performance and cost-effectiveness. Through strategic design adjustments, areas of higher stress can be strengthened, and weight can be reduced without compromising structural integrity.
How does heat treatment affect the properties of carbon steel castings?
Heat treatment plays a pivotal role in determining the final microstructure and mechanical properties of carbon steel castings. By controlling the heating and cooling rates, the steel’s microstructure can be manipulated to improve properties such as strength, ductility, and toughness. Heat treatment processes like annealing, normalizing, and quenching and tempering can also be optimized to enhance hardenability and achieve uniform hardness, especially in thicker sections.
How does KT-Foundry optimize material selection for carbon steel castings?
KT-Foundry specializes in guiding clients through the material selection process, considering the application, machinability, weldability, and the component’s strength. Whether it’s choosing between low, medium, or high carbon steel or considering additional alloys for enhanced properties, our expertise in investment casting and heat treatment techniques ensures that our clients receive castings optimized for their unique requirements.
What industries and applications can benefit from carbon steel castings?
Carbon steel castings provide necessary mechanical properties for a wide range of applications across industries, from industrial machinery with demanding strength and wear requirements to aerospace components requiring precision and reliability. KT-Foundry offers expertise in selecting the right carbon steel grade, balancing factors such as ductility, weldability, and strength requirements with the application-specific demands to ensure optimal performance.