Aluminum die casting is a manufacturing process that offers an unparalleled strength-to-weight ratio, making it a popular choice in industries such as automotive, aerospace, and electronics. This process allows for the production of lightweight yet robust components, making it highly desirable for applications where weight reduction is crucial without compromising strength.
When it comes to material optimization, aluminum die castings outshine other manufacturing processes. This is due to their ability to enhance the strength and mechanical properties of the castings, resulting in components that can withstand demanding conditions and perform reliably.
The design flexibility of aluminum die castings is another remarkable feature. It enables the production of complex geometries, allowing for the creation of intricate parts with accuracy and precision. This ensures dimensional accuracy and consistent part production, meeting the stringent requirements of various industries.
Aluminum die castings are known for their excellent surface finish, which is achieved through the use of precision molds and fine casting grain structure. This attention to detail results in components with a smooth and flawless exterior, meeting the high aesthetic standards of industries such as consumer electronics and luxury automotive.
In addition to their strength and aesthetics, aluminum die castings also possess superior thermal conductivity. This makes them a suitable choice for applications that require efficient heat dissipation, such as heat sinks and electronic enclosures. The ability to rapidly transfer heat away from critical components ensures optimal performance and longevity.
Key Takeaways:
- Aluminum die casting offers an unparalleled strength-to-weight ratio.
- Material optimization enhances the strength and mechanical properties of aluminum die castings.
- The design flexibility enables the production of complex geometries with dimensional accuracy.
- Precision molds and fine casting grain structure contribute to excellent surface finishes in aluminum die castings.
- Aluminum die castings exhibit superior thermal conductivity, making them ideal for applications requiring efficient heat dissipation.
Material Optimization and Enhanced Mechanical Properties
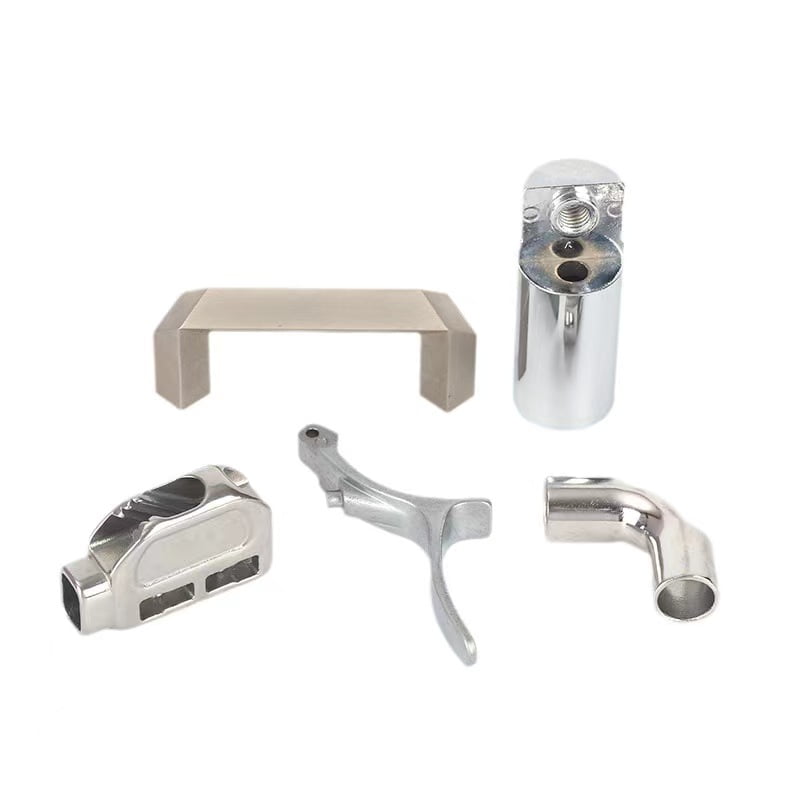
The process of aluminum die casting allows for material optimization, resulting in castings that possess superior strength and mechanical properties. By carefully selecting the alloy composition and adjusting the casting parameters, we can achieve the desired mechanical characteristics of the final product. Aluminum die castings have excellent tensile strength, fatigue resistance, and impact resistance, making them suitable for demanding applications in various industries.
Through material optimization, we can also enhance other properties of the castings, such as corrosion resistance and thermal stability. By adding specific alloying elements and controlling the cooling rate during solidification, we can create aluminum castings that can withstand harsh environments and ensure long-lasting performance.
Moreover, the material optimization process allows us to tailor the mechanical properties of the castings to meet specific requirements. Whether it’s high strength, ductility, or stiffness, we can fine-tune the composition and structure of the aluminum alloys to achieve the desired performance characteristics. This flexibility is particularly beneficial in industries where lightweight yet strong components are crucial, such as automotive, aerospace, and electronics.
With material optimization, aluminum die castings offer a unique combination of strength and performance, making them a preferred choice for manufacturers seeking lightweight, durable, and high-quality components.
Advantages of Material Optimization in Aluminum Die Castings |
---|
Superior strength and mechanical properties |
Enhanced corrosion resistance and thermal stability |
Customizable properties to meet specific requirements |
Lightweight yet robust components |
Design Flexibility for Complex Geometries and Dimensional Accuracy
Aluminum die casting offers design flexibility that allows for the production of components with intricate and complex geometries, while still maintaining dimensional accuracy. The versatility of this process empowers manufacturers to create intricate shapes and structures that would be challenging to achieve with other casting methods.
Advantages of Design Flexibility: | Examples: |
---|---|
Ability to incorporate multiple features into a single component | Complex engine parts with integrated cooling channels and mounting brackets |
Precision in replicating intricate details | Decorative or ornamental elements with fine textures and patterns |
Flexibility to adapt to various production requirements | Customized parts for different industries, including automotive, aerospace, and electronics |
Moreover, unlike other manufacturing methods, aluminum die casting ensures consistent part production. The use of permanent molds allows for the replication of complex shapes and intricate details with high accuracy. This consistency is essential for industries that demand precise specifications and reliable performance.
Dimensional Accuracy is Key
Dimensional accuracy is crucial in industries where tight tolerances and precise fitting are required. By using aluminum die casting, manufacturers can achieve the desired dimensional accuracy consistently. This precision is achieved through intricate tooling design and the casting process itself, which minimizes shrinkage and distortion.
The combination of design flexibility and dimensional accuracy makes aluminum die casting an ideal choice for industries that demand intricate geometries, precise fitting, and high-performance components. Whether it is creating complex engine parts, customized components for electronics, or decorative elements, aluminum die casting offers the versatility and precision required to meet the diverse needs of various industries.
Key Points: |
---|
Aluminum die casting offers design flexibility for complex geometries |
The process maintains dimensional accuracy |
Consistent part production and precise specifications are achieved |
Achieving Excellent Surface Finish through Precision Molds
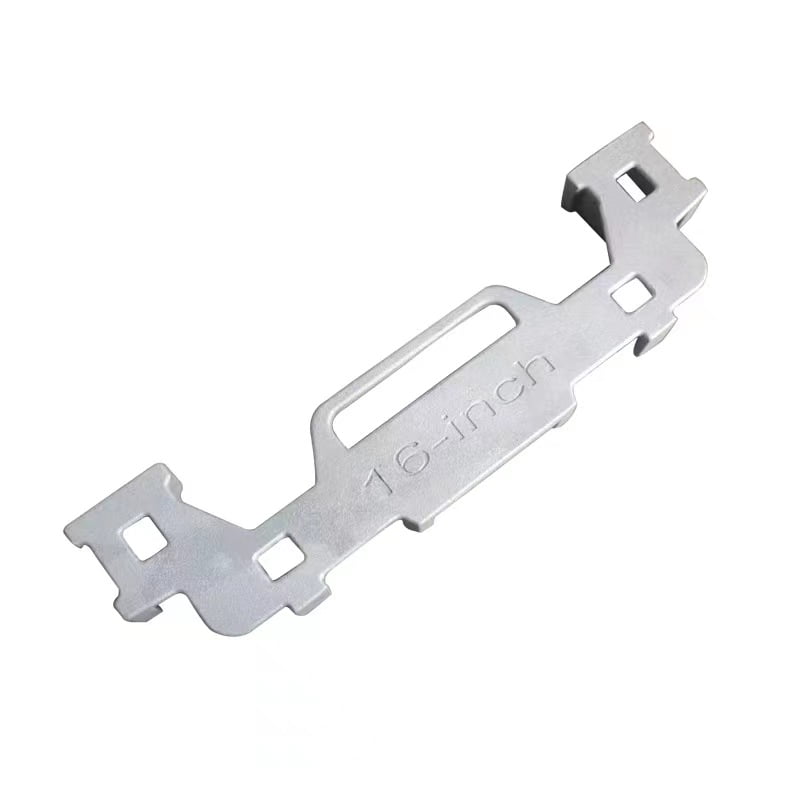
Precision molds and a fine casting grain structure play a crucial role in achieving an excellent surface finish in aluminum die castings, ensuring a visually appealing final product. The use of specially designed molds allows for intricate details and smooth surfaces to be replicated with accuracy. These molds are created with precision, ensuring that every aspect of the casting is captured flawlessly.
Additionally, the casting grain structure is carefully controlled to further enhance the surface finish. By optimizing the cooling process during casting, the grain structure of the aluminum is refined, resulting in a uniform and fine surface texture. This fine grain structure contributes to the overall quality and aesthetic appeal of the finished part.
Furthermore, the use of precision molds and fine casting grain structure also helps minimize defects such as porosity and surface blemishes. The molds ensure that the molten aluminum flows evenly and smoothly, reducing the chances of air pockets or imperfections forming. The refined grain structure, on the other hand, reduces the likelihood of surface irregularities, resulting in a high-quality surface finish that meets the desired specifications.
In summary, precision molds and a fine casting grain structure are essential elements in achieving an excellent surface finish in aluminum die castings. These factors not only enhance the visual appeal of the final product but also contribute to its overall quality and functionality. By investing in the design and production of precision molds and optimizing the casting process to control the grain structure, manufacturers can consistently produce aluminum die castings with superior surface finishes that meet the demands of various industries.
Advantages of Precision Molds and Fine Casting Grain Structure |
---|
Replication of intricate details |
Smooth and uniform surface texture |
Minimization of defects such as porosity and blemishes |
Consistent production of high-quality surface finishes |
Superior Thermal Conductivity for Efficient Heat Dissipation
Aluminum die castings exhibit superior thermal conductivity, making them the preferred choice for applications that require efficient heat dissipation and thermal management. This exceptional property of aluminum die castings is a result of the inherent characteristics of aluminum as a metal.
With a thermal conductivity of approximately 236 W/m·K, aluminum has one of the highest thermal conductivities among commonly used metals. This means that heat generated within the component can be quickly and efficiently transferred to the surrounding environment, preventing the build-up of excessive heat that can lead to component failure or reduced performance.
Furthermore, the high thermal diffusivity of aluminum ensures that heat is evenly distributed throughout the casting, minimizing the risk of localized hotspots. This is particularly important in applications where consistent temperature distribution is critical for maintaining the performance and longevity of the component.
Additionally, the superior thermal conductivity of aluminum die castings allows for effective thermal management, enabling engineers to design and optimize heat dissipation structures. By efficiently channeling heat away from sensitive components, aluminum die castings help improve the overall performance, reliability, and lifespan of various products and systems.
Advantages of Aluminum Die Castings for Heat Dissipation: |
---|
Superior thermal conductivity |
Efficient heat dissipation |
Fast and even heat distribution |
Optimized thermal management |
KT-Foundry’s advantages in die casting aluminum casting
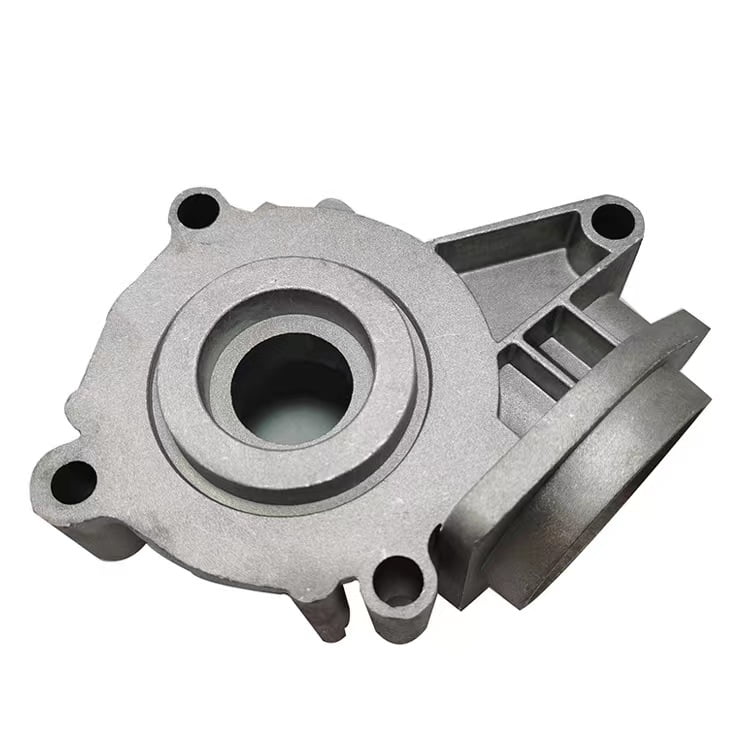
KT-Foundry is a leading aluminum die casting company with over 30 years of experience. We offer a variety of services including die casting, CNC machining, and more. We pride ourselves on our quality products and customer service.
Die casting is a process where molten aluminum is injected into a mold under high pressure. The aluminum cools and takes the shape of the mold. Die casting is a versatile process that can be used to create a variety of shapes and sizes.
One of the advantages of die casting is that it is very versatile. With die casting, you can create products in a variety of shapes and sizes. You are not limited by the size or shape of the mold.
Another advantage of die casting is that it is a very efficient process. The aluminum is injected into the mold under high pressure, which helps to speed up the process. Die casting is also a very repeatable process, so you can be sure that each product will be identical.
KT-Foundry has a team of experienced professionals who are experts in die casting. We can help you to create the perfect product for your needs. Contact us today to learn more about our services.
Conclusion
In conclusion, aluminum die casting offers a wide range of advantages, from its exceptional strength-to-weight ratio and design flexibility to its superior surface finish and thermal conductivity. It is no wonder that aluminum die castings are widely used in various industries for their lightweight yet robust components.
With its remarkable strength-to-weight ratio, aluminum die casting is the ideal choice for producing lightweight components that do not compromise on durability. This makes it highly sought after in industries such as automotive, aerospace, and electronics, where weight reduction is critical.
Furthermore, aluminum die castings can be optimized to enhance their mechanical properties, making them even stronger and more resilient. This ensures that the components can withstand the demands of their intended applications, offering long-lasting performance and reliability.
The design flexibility of aluminum die castings is another key advantage. This process allows for the production of complex geometries, enabling the creation of intricate parts with precision and accuracy. The dimensional consistency achieved through aluminum die casting ensures that every part produced meets the required specifications, resulting in high-quality components that fit perfectly into the overall assembly.
In addition, the use of precision molds and fine casting grain structure contributes to the excellent surface finish of aluminum die castings. This makes them visually appealing and suitable for applications where aesthetics matter. The smooth and flawless surface finishes not only enhance the overall appearance but also provide added protection against corrosion and wear.
Lastly, the superior thermal conductivity of aluminum die castings makes them highly efficient in dissipating heat. This property is particularly valuable in industries such as electrical and electronic, where heat management is crucial for optimal performance and reliability. Aluminum die castings ensure that heat is effectively transferred away from sensitive components, preventing overheating and potential damage.
In summary, aluminum die casting offers a winning combination of lightweight strength, design flexibility, rapid production, enhanced surface finish, and excellent thermal conductivity. These advantages make it a preferred choice in various industries that prioritize high-performance components. Whether it’s for automotive parts, aerospace components, or electronics enclosures, aluminum die castings deliver outstanding results that meet the demands of modern applications.
FAQ
What is aluminum die casting?
Aluminum die casting is a manufacturing process that involves injecting molten aluminum into a steel mold under high pressure. The molten aluminum solidifies into the desired shape, resulting in lightweight yet robust components.
What are the advantages of aluminum die casting?
Aluminum die casting offers numerous advantages, including its lightweight strength, precision and complexity in design, rapid production, enhanced surface finish, and excellent thermal conductivity.
What industries use aluminum die castings?
Aluminum die castings find uses in various industries such as automotive, aerospace, electronics, consumer goods, and more due to their strength-to-weight ratio and exceptional mechanical properties.
How does material optimization enhance the properties of aluminum die castings?
Material optimization in aluminum die castings enhances their strength and mechanical properties by ensuring the optimum use of the aluminum alloy, resulting in castings with improved durability and performance.
Can aluminum die castings be used to produce complex geometries?
Yes, aluminum die castings offer design flexibility, allowing for the production of complex geometries with precise dimensional accuracy, making them suitable for a wide range of applications.
How is the excellent surface finish achieved in aluminum die castings?
The excellent surface finish in aluminum die castings is achieved through the use of precision molds and a fine casting grain structure, resulting in castings with smooth and aesthetically pleasing surfaces.
What makes aluminum die castings suitable for applications that require efficient heat dissipation?
Aluminum die castings exhibit superior thermal conductivity, which allows for efficient heat dissipation. This makes them an ideal choice for applications that involve heat-sensitive components and require effective heat management.