The industrial and metalworking processes rely heavily on foundry and casting. These manufacturers create castings of any type of cast iron that can be used for different applications.
They use iron as the primary metal and a variety of alloying elements. Casting aluminum and steel can also be done in foundries. This versatility is why foundries are vital to the metal production process.
Understanding The Role of Foundries
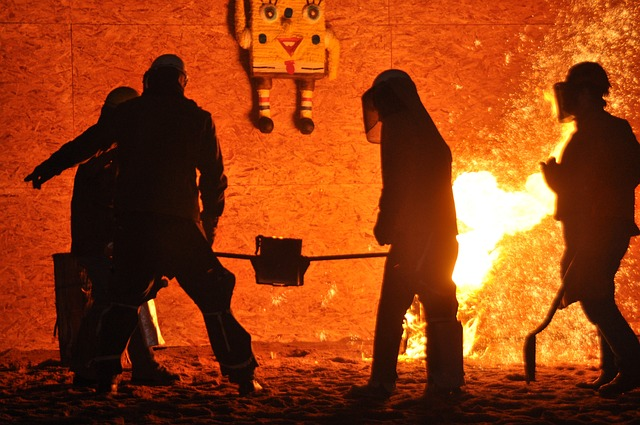
The Foundry industry is a key part of the metal manufacturing processes, providing various services that enable producing metal products. Some of its primary duties are melting metal, casting, and finishing processes for the final casting.
The role of a foundry is to ensure that the products produced are of the highest quality and meet the customer’s expectations. Foundry workers are responsible for monitoring the temperature of the furnace and the molten metal, as well as the molds and the products themselves. They must also ensure that the castings are produced safely and efficiently to avoid casting defects.
Foundries are also able to provide a variety of finishing services, such as painting and plating. As foundries have become increasingly automated, they have become more efficient and able to produce products faster and more accurately.
Casting Process for Metal Castings
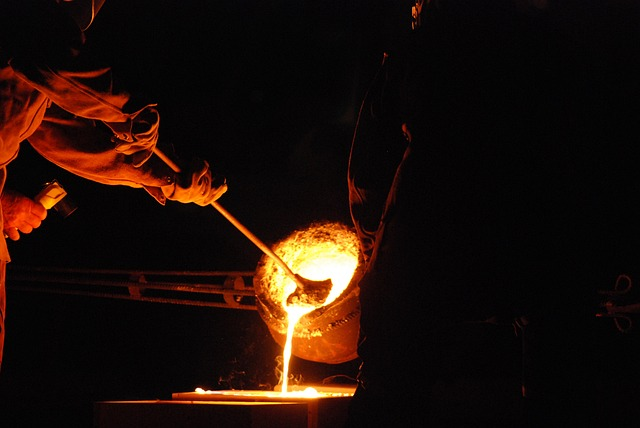
The casting method in foundries is a complex and intricate process requiring great precision, planning, and skill. It is the process of creating various metal components, such as engine parts, valves, pipe components, and other metal products. The common metals processed in foundries are iron, aluminum, and steel.
Mold Making
One of the most important foundry processes is creating mold. It is a complex process requiring various skills, tools, and special mold material.
The first step in the mold-making process is to create a pattern. This is a design of the desired shape of the finished product. Patterns are typically made of wood or metal replica of the desired casting, machined, or handcrafted. The pattern must be dimensionally accurate, so choosing suitable materials and techniques for creating the pattern is essential.
Te refractory coating helps to prevent the molten metal from sticking to the mold and also helps to ensure that the finished product has a smooth surface finish.
Melting Process and Pouring Molten Metal
This process is done using melting furnaces. Aside from pure iron ore, scrap metal and other metals can also be melted. Depending on the melted metal, this is typically done on specialised furnaces or induction heating. To pour molten metal, foundry workers usually use a ladle or special equipment.
The molten metal must be kept at a consistent temperature to maintain the desired shape.
The amount of metal poured into the mold cavity is carefully controlled. Excess material during the pouring process may require further furnishing or result in defective castings. The metal solidifies by using a cooling system such as a water bath.
Finishing Process of Metal Casting
Different finishing processes involve removing any excess material or impurities and the final polishing and finishing of the casting. This process is essential for ensuring that the metal casting is of high quality and that it meets the desired specifications.
Before beginning the finishing process, the casting must be inspected for defects or imperfections. This is done using various methods, such as visual inspection, x-ray examination, or chemical reaction testing.
Excess materials can be removed using grinding and cutting tools, such as wheels and end mills. A powder coating may also be used to create various looks for the cast metal, ranging from glossy to matte finishes. The finishing process may also improve the castings’ mechanical properties.
Types of Metal Casting Process
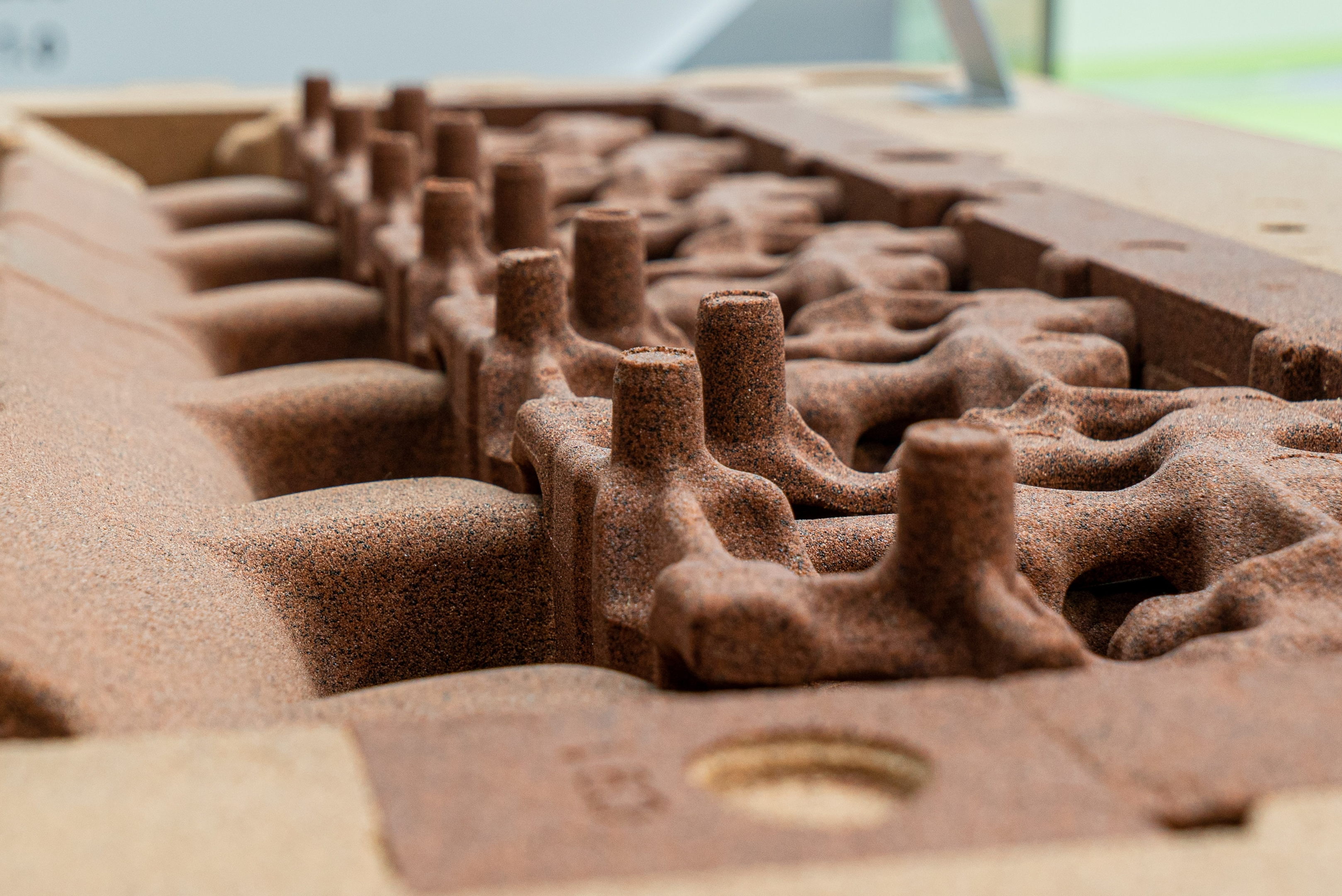
Sand Casting
Sand casting or green sand casting is the most common casting process. Sand molds are often used to produce large and complex components.
The molding sand is a mixture of silica sand and clay to form sand molds, which is the exact metal replica. The sand is packed into a form and compressed, creating a “pattern” to create the sand mold.
The curing process of the mold cavity involves heating the sand to extremely high temperatures and allowing it to cool slowly over time. This helps to ensure that the sand mold is strong enough to withstand the heat and pressure of the liquid metal.
Die Casting
The die-casting process includes melting and injecting metal into a pre-determined die. The die-casting machine consists of electric arc furnaces for melting the metal and an injection mechanism, such as a plunger.
Its mold is prepared by machining a solid steel block with the same features as the product and placed into the die-casting machine.
Investment Casting
The process of investment casting begins with a wax model of the desired part or component. Its casting molds are typically wax or plastic and filled with a ceramic slurry.
This foundry process is used to produce shapes and parts with intricate details. Additionally, investment casting molds have a long lifespan and are relatively inexpensive to produce.
Benefits of Casting Metal in a Foundry
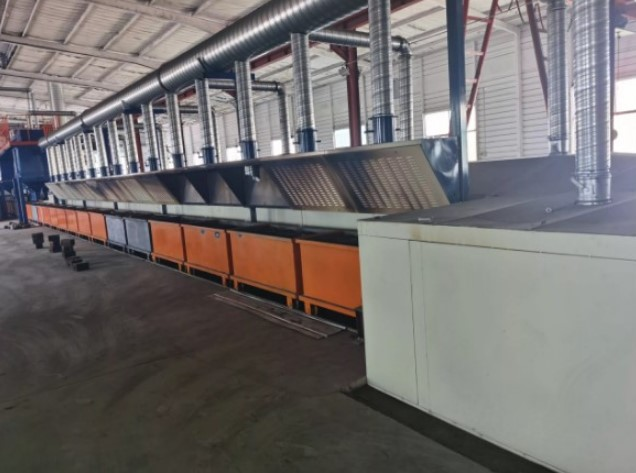
Skilled Foundry Workers
The foundry industry relies on a unique and specialized workforce to produce high-quality products. These highly skilled professionals are responsible for pouring metal into molds and creating the components and parts used in various industries. They also sand, grind, and finish castings to achieve the desired specifications.
Foundry workers have a solid understanding of working with different types of metal and the various tools used in the process. They also have a good eye for detail and can work quickly and accurately to meet production deadlines.
Availability of Modern Furnace Types
Modern furnaces can cast a wide range of alloys. Induction furnaces have improved energy efficiency and faster melting times, which can lead to significant cost savings. Electric arc furnaces can preheat and melt metals with lower heat levels than traditional furnaces.
Reverberatory and crucible furnaces are used to melt steel and aluminum. Reverberatory furnaces are used for large-scale production, while crucible furnaces are used for smaller batches. The process of melting and purifying metal is the same in both furnaces, but the choice of which type of furnace to use depends on the size and type of the metal being melted.
Produces Metal Castings in Large Quantities
The ability to produce metal castings in large quantities is one of the major advantages foundries have over other processes. They have the appropriate equipment to create large, complex parts in a relatively short time.
Ability to Produce Castings in Complex Shapes
Foundries have the ability to produce castings in intricate shapes is a significant advantage. Whether it’s a one-off prototype or a high-volume production run, foundries can create precision parts with intricate details that are otherwise impossible to make.
They can also produce parts with high accuracy and repeatability, which is essential when making complex shapes.